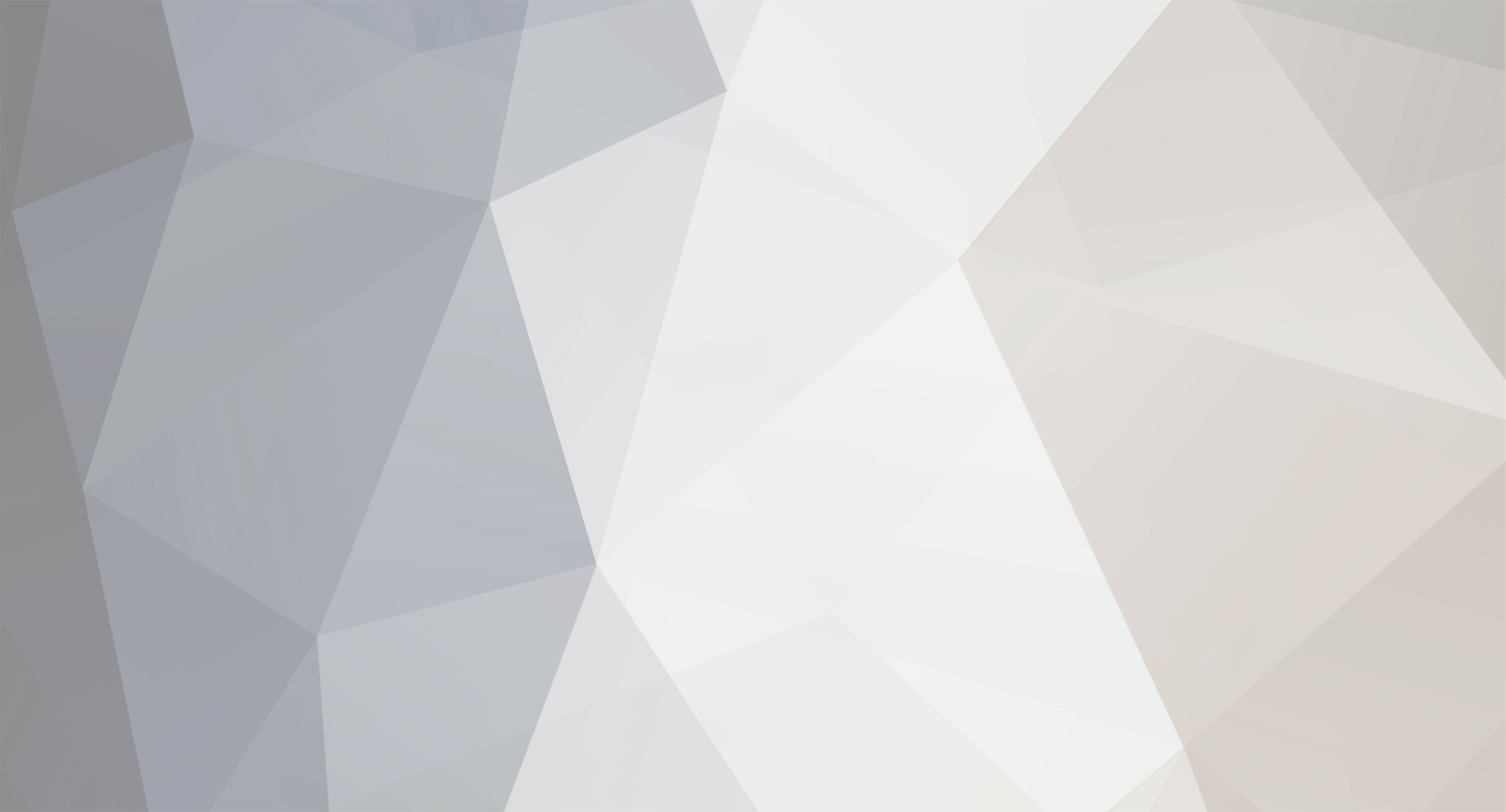
Geoff Weeks
Pedigreed Bulldog-
Posts
1,690 -
Joined
-
Last visited
-
Days Won
6
Content Type
Profiles
Forums
Gallery
Events
Blogs
BMT Wiki
Collections
Store
Everything posted by Geoff Weeks
-
Yes, I have it. May be a day or two before I get it to the post office. I am knee deep in a few projects.
-
What I got: some defects in the chrome top (bubbles but still in one piece) IHC part number but looks similar. same deal as the speedo, you pay shipping and it is yours for free.
-
I have no idea on Mack if it is normal, I was just saying it can be. In any position does the non-rod side not have air? The rod side can have air at all times in some applications, but the non rod side must be vented in one selection at least. The only way the piston will move out is when the rod side has air and the non rod side does not. The rod side has to be at a higher pressure than the non rod side to move the piston away from the trans case.
-
1st let me state, I have no experience on the Mack transmission in question, however I can answer your 1st question. Yes it can be normal to have pressure to both sides of a piston, Eaton does this on theirs. Because the rod takes up some area on the rod side, that "working" area is smaller than the other side, so when pressure to both, the piston moves to the rod side direction, when the back is vented the piston move the other way.
-
I don't know how they do it on your engine, but a lot of duel ign engines are designed to be run on both, all the time. They will run on one, but with reduced power. They are "starting the fire" at opposite sides of the cyl, and when you only burn from one side, power is lost and economy goes to hell. I have a duel ign Buda.
-
I am not a fan of "all under the cap" electronic ign. May be it was 'early days" but many had trouble with them failing. I am working on fitting a Chry reluctor to a Delco dist. If I ever get the project done (I'll post here, but don't hold your breath) then any remote control ign box could be used. For a "hobby/show"vehicle that doesn't see many hrs on the engine, points will last a long, long time.
-
several hits on the net for That Norther rad is about a grand, a few others in that price range.
-
Brake Shoe Headaches
Geoff Weeks replied to Mdmccurr's topic in Antique and Classic Mack Trucks General Discussion
I used to have some pin type shoes in 4" but when I looked in my core pile, all I could find were 15x4Q's. I much prefer the pin shoes on the narrow steer brakes. I forgot all mine were the more common 15 x 4 -
My 90 deg is square drive, so that will not be a help, my "777" ratio box is tang drive but I don't know if the parts interchange with the 90 deg, or not, I suspect not. Hippy's place or other speedo shop would likely be a better bet.
-
Mack B873sx restoration
Geoff Weeks replied to hicrop10's topic in Antique and Classic Mack Trucks General Discussion
Mack wasn't the only one to use seals and greased bearings. There are a number of ways it was done. -
Checked to see what I have. I have a 777 ratio box and a plain 90 deg but it has 5/8" threads and those look to be 7/8's
-
Another thing about "swaps" is they are never simple, yes the cut-off may not be that expensive, but then there is all the little stuff that adds up like driveshaft changes, frame splicing if not trying to bolt in. Getting replacement drums made may be the most expensive brake job you ever do, but as long as the shoes can be re-lined (shoe table not damaged) and the wheel cyl castings are not damaged, it still may work out cheaper in the long run. You are then left with something that is factory and not butchered, not only is it correct, but down the road it will make other repairs more straight forward. Take time to assess what you have now, and if drums are the only hurdle on the rear of the truck, I would advise getting them made. You may be able to "hook up" with other looking for those drums to make a "group buy" to bring the cost/unit down.
-
Just looking though Webb's catalog, I find 3 numbers that match the pilot, mounting hole and brake spec's but not surprising all are being discontinued. I found a few "hits" on those numbers, but unless you find one sitting in someones warehouse that they want to get rid of, it looks like Durabrake, is your best bet in this country. If you are having one made, then they should be able to make an exact fit. Problem with changing rear axles, is IIRC this truck is on juice brakes, so that would preclude swapping a more common and likely air braked axle. I would be looking for a minimum of 2 no matter the other one you have is still in one piece. Other than the above spec's the most important will be the hub mount to brake shoe measurement, that has to be close or be able to be machined to that spec.
-
The next video you post will be another shop putting the Cummins block back together!
-
https://www.durabrake.com/brake-drums/ In there "About us" section seam to say they make drums to order and prototypes
-
Give us the two measurements I asked for and see what can be found. we already know it is 15x 5 brake. needed are the bolt hole circle and the pilot diameter.
-
Superliner RW700 Steering axle
Geoff Weeks replied to 1961H67's topic in Antique and Classic Mack Trucks General Discussion
Paul, the dual gear starts on pg 62 https://www.rhsheppard.com/wp-content/uploads/2019/02/92-Series-Sheppard-Power-Steering-Service-Manual.pdf -
I'm getting old, that is 4k more than I paid for my last cabover (drove it home) and 3k less than I paid for my other two, which didn't need anything to go to work. Everything is more expensive today, but is why I always kept my "cores" and rebuilt when time permitted.
-
Superliner RW700 Steering axle
Geoff Weeks replied to 1961H67's topic in Antique and Classic Mack Trucks General Discussion
Yes, the tie-rod just keeps the tires in "sync" with eachother and the forces are supplied by the dual boxes. Sheppard made a "box" that looks identical to the "392" but it has no input shaft, the oil is controlled and supplied by the master box (Left in the US). Some others have used a double acting hyd cylinder, much cheaper, but when pressure is on the rod side of the cyl the forces will not be equal like they are with the whole slave gear. (Rod side has less area than the non-rod side). -
Glad I could be of help.
-
Make sure the line between the double check and trolley valve is not "crimped" anywhere along its run.
-
Yeap, that is the double check, the outlet is the pipe connection that looks like it connects to a tractor protection valve. The reason it fixed it is because without all the air line connected the flow out the exhaust was higher and that was enough to get the shuttle to move. It sound like it was "sticky". It may work for a long time or it may fail shortly, but at least you know where it is and how to fix it. Doesn't look like fun getting it out of there, however.
-
Output from the trolley. It goes to a T valve where the higher of the two inputs goes to the output (double check). Right now it is not sealing so air can come from the foot brake, back feed up the line to the trolley and since in its normal position that is open to exhaust, the air flows out the exhaust. Another way to test it is to build full air pressure, fully apply the trolley, then step of the foot pedal. It shouldn't leak until you release the trolley valve. Input to the trolley should have system air, output should be 0 psi with the valve in the normal position, and of course the line you already traced just dumps to under the hood. With the air built up, if the line you crack loose at the trolley has pressure, that is not the one you want, if you crack it loose and it doesn't have pressure, then remove it and plug it, then test the foot brake to confirm the problem has gone away. then trace that line to a valve with three lines on it.
-
There should be 3 lines to the Trolley, (2 on earlier systems where they just exhausted the air into the cab) One should be supply pressure and one should be output that will go to the double check. 3rd is the exhaust you traced. Where it would be located is up to the mfg and I have no idea on that model, where they put it. It could be located anywhere between the trolley, foot valve, and the tractor protection valve. Some are in the cab, some are down on the frame. If you are in a pinch and need to move the truck, remove and plug the output line from the trolley valve (plug the line, not the port on the trolley valve) and the leak should go away if the shuttle (double) check is the problem. You should still put the time in to fix it right.
BigMackTrucks.com
BigMackTrucks.com is a support forum for antique, classic and modern Mack Trucks! The forum is owned and maintained by Watt's Truck Center, Inc. an independent, full service Mack dealer. The forums are not affiliated with Mack Trucks, Inc.
Our Vendors and Advertisers
Thank you for your support!