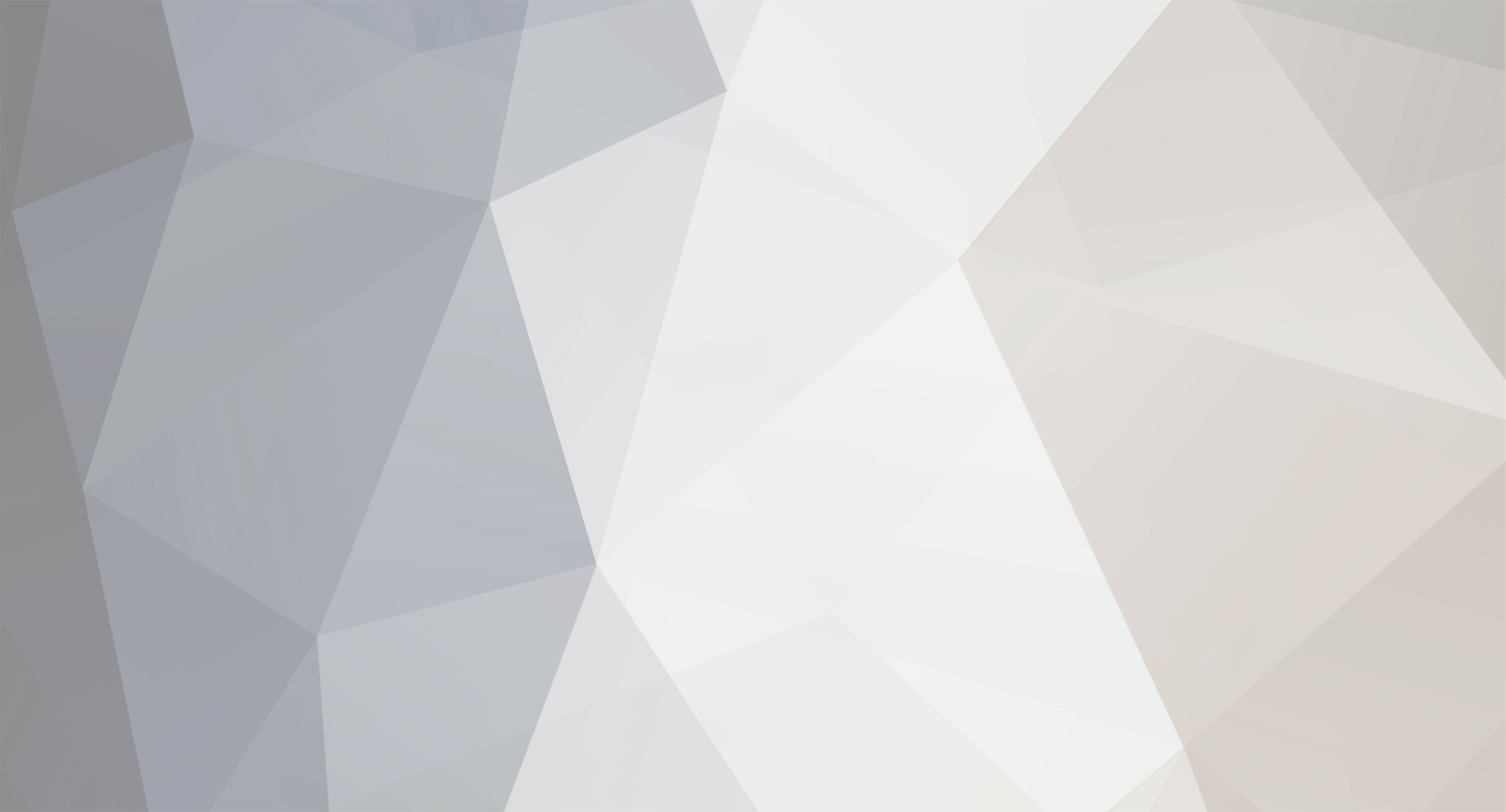
Geoff Weeks
Pedigreed Bulldog-
Posts
1,696 -
Joined
-
Last visited
-
Days Won
6
Geoff Weeks last won the day on January 19
Geoff Weeks had the most liked content!
Location
-
Location
western Iowa
Profile Fields
-
My Truck
1992 Marmon
Recent Profile Visitors
The recent visitors block is disabled and is not being shown to other users.
Geoff Weeks's Achievements
-
I saw a red fox in my yard a week ago, I left it be, as it was hunting rodents. I hear Coyotes often but rarely see them. Very afraid of humans and domesticated dog (which often bring a human with a gun). No mistaking a fox for a coyote, size and shape of the head are give-a-ways.
-
Cummins "Low flow" system, in a nutshell
Geoff Weeks replied to Geoff Weeks's topic in Other Truck Makes
By comparison, Mack's tip turbine is a more "elegant" solution to the problem, but I suspect more expensive to produce. I could be wrong about that, the last re-core I did on my Low Flow radiator cost me $2100, the out of chassie rebiuld kit cost $1500 for the engine. The need for each went away when space in front of the radiator was provided by the truck Mfg. -
Coupla people remarked about this on Freightrain thread, rather than muck it up I thought I would start anew. I had a Lowflow truck in the fleet until retirement and got to know and understand the system well. The 1st thing to understand is there are basically 2 loops in the system that run in parallel. one is the coolant that is in the block and one is the coolant that runs through the after cooler radiator and oil cooler. The all come together at the water pump and mix there. The term "low flow" is kinda misleading. The total flow is the same or higher than a normal system. The term refers to only the amount that is passing through the radiator. The radiator is a two pass core, where coolant enters at the BOTTOM goes up to the top tank and across to the other side and back to the outlet again at the bottom. There is a divider in the bottom tank to keep the sections separate. That divider must be there and seal or the engine will quickly over-heat as coolant will bypass the tubes, and just flow across the bottom tank and back to the engine. As heat moves quicker from a higher temp to a much lower temp, the side where the coolant enters and rises to the top tank is most often smaller then the side where it descends to the bottom tank and out. This allows for much of the heat to be lost when the temp difference is greatest on the "hot side" and then a larger area on the cool side to continue to bring the temp down. An engine at full load only has to loose 10 deg of coolant temp to not over heat. That is why in conventional systems, the shutter thermostat when in the lower tank is the same as the engine thermostat. So when the engine (180 deg) 'stat is full open, (190 deg) the shutters will be full open when the return temp is 180 deg. A conventional cooling system can do this if designed for the load. So a working engine, the return temp of the coolant will be 180 deg. IF you try and use this to cool the air charge from the turbo, it can never get very cool. If, however, you could reduce the returning coolant lower, say 140 deg or 160 deg, you can remove more heat from the air charge. Before low flow or air to air, often 170 deg 'stats were used to try and reduce the returning coolant temp, but this made the engine really too cool for best combustion. These early coolant based systems always took the aftercooler supply from the lowest point in the block to get the coolest water. In the Cummins system, the two loops are in parallel, that means any restriction in one loop, causes more coolant to circulate in the other. There are restrictor plates in the outlet of each head into the upper water rail. The upper water rail goes straight back to the inlet of the water pump, much like a conventional system with a weirstat, where when "closed" the coolant is returned to the water pump. This keeps the coolant flowing at all times and prevents hot spots and promotes better temp control by the thermostat as it has flow over the bulb at all times. Where the low flow system start to get complicated, is the coolant from the block to the radiator and from the radiator back to the block. The "outlet" coolant come from the oil cooler on the side of the block. It then goes to the thermostat housing where there are two thermostats, one that is full open when cool, and closes on temp rise, and one that is full closed when cool and opens on temp rise. The return flow to the block (inlet of water pump) can either be through the bypass thermostat and/or the charge cooler. When block temps are low, the bypass 'stat is fully open and the all the coolant circulates in the block, as temps start to rise, the bypass starts to close . once it reaches about 160 deg the bypass 'stat is fully closed and all returning coolant to the block must go though the aftercooler. Once the coolant from the block/oil cooler reaches 160 the main 'stat starts to open and send some of the coolant to the radiator. The return from the radiator must pass through the aftercooler before going to the waterpump, where it mixes with the hot coolant from the upper water rail, and gets sent back to the bottom of the block. Mixing of the hot upper water rail coolant and the coolant from the radiator via the after cooler reduces the temp of the returning coolant to the block enough so it can keep the engine cool. There are some "trouble points" with the system. 1st any restriction increase on one of the loops diverts more of the coolant to circulate in the other loop. So radiator tubes that a partially plugged reduce the flow in that circuit and more will stay in the block and not be cooled. 2nd the radiator tubes must be smaller (dimpled) to slow the flow through the radiator enough to loose the maximum heat before returning, but still flow enough to provide enough return coolant to lower the block coolant temps (this is where "low-flow term comes from). 3rd, the water pump must be able to move a lot of coolant without aeration. 4th the block pressure in the coolant jacket in a low flow system at 2100 rpm is 46 psi! Chew on that for a moment! The radiator never sees 46 psi because of the restrictions in the system. The 1st Big Cam 4's (low flow) look very much like the Big Cam 3's (high flow) and many didn't see the difference and mixed parts with big problems as the result. The upper water rail gaskets and water pump are different. The water pump looks the same and takes the same housing, but the pulley is smaller and the top of the housing is vented to move any air out of the system. Put a Big Cam 3 water pump on, and it will work, but not cool well and over heat when working hard. The upper water rail O rings have restrictor plates that control how much coolant returns to the inlet of the water pump. Some when seeing this, think it will cool better without the plates or with a bigger hole, when the opposite is true. Opening up the hole allow more hot coolant to return to the inlet of the waterpump and less to make it to the radiator. With the NT88, the upper water rail and water pump (as well as thermostats) changed design to where it is obvious that you can not use the Big Cam 3 and down stuff on the block. To be able to have 46 psi block pressure the water pump belt had to carry a high load and not slip, multi groove belts were used (no change from early big cam) but were less tolerant of being run while loose and would slip at higher rpm/load. Multi rib belts can not suffer slipping long before they shred. Does it all work? Yes! With a large enough radiator and a good, clean system, the charge temp is reduced, the block temp is increased and the fuel mileage is between .5-1 mpg better with the same load. Likely more than you wanted to know about Low flow, much of what I know about cooling came from Glenn Akers, the rest from hard knocks owning a low flow for 30 years and working it hard. None of it is as good as an air to air charge cooler, and when trucks were re-designed for enough room for a charge cooler in front of the radiator, the N-14 got an air to air and the low-flow era ended.
- 1 reply
-
- 1
-
-
Mine was damaged BEFORE it was boxed. No outside indication of being dropped. No way it could be dropped in a 2 ply heavy cardboard and do this much damage and not leave tell tale signs on the box
-
Back in the Mack Pack!
Geoff Weeks replied to BOBWhite's topic in Antique and Classic Mack Trucks General Discussion
Grab the hub at 12-6 and try and rock it in and out. 1st put some kind of jack stand under the axle ! you don't want it falling on you. -
Its been a coupla months now. I can't get the correct liners to fit this block, too big around, too tall but listed for this engine. I found a N.O.S. block with liners already installed, 1st arrive cracked, dropped at the factory! Inside a factory sealed box, no damage to the double wall box, but the casting was deformed and cracked. 2nd one arrived in good shape. This is one of those things where you can see the obvious failure, but not the "hidden" failures that lead up to it. The engine failed due to improper assembly, the gasket protruded into the bore, and the piston hit the gasket and shattered. What wasn't obvious until complete tear-down, was he didn't replace the front crank bushing when he installed a -.2mm reground crank, and he didn't remove the timing gear off the crank and forced it though the bushing damaging it. He also "lost" a couple of springs in the gov assemble and tried to shorten the remaining one! So even if could have got the liner in, I would still have had an engine with major problems, low oil pressure and a governor that wouldn't hold the engine speed correctly or might even overspeed. All the "hidden" problems showed when I stripped the original block and started building the replacement. I'll end up with a unit that cost me about what I could have paid for a running unit from a rental house, but I'll have essentially a "new" engine that should outlast me. A cautionary tale about buying un proved things at auction.
-
The tip turbine and Low Flow cooling were both attempts to better charge cooling without have to re design the front of the truck for enough room for an CAC cooling radiator (Air to air). once trucks were being redesigned anyway, the reasons for the tip turbine and low flow systems went away. Having the charge cooler in front of the radiator give the best cooling, and what has become the std today. At the time, Mack tip turbine was revolutionary, both Cat and Cummins were still using water cooled aftercoolers, and low thermostat temps, to walk the fine line between good block temp and enough cooling for the charge air. After Macks success, Cummins used the low flow system to run the "super cooled" multi-pass radiator coolant through the aftercooler, before sending it the engine. Cat never did and opted for the cooler in front of the radiator, which meant that their engines above 400 hp could not be fitted to many trucks. Cat engines below 400 hp still had the old water cooled aftercooler.
-
Spicer's sales pitch was "0 to top speed with only 5 stick movements". 14,16, or 20 possible selections.
-
Where you have to be careful is in the lower gears, that applies to any transmission, it the higher ranges it isn't going to damage something as easily. I would shy away from double overdrives, with the one exception of the RTLO's. 1st there is too much wasted in gearing up and back down, all that goes into heat. 2nd there is the driveshaft issue, have to do the math and make sure you are staying away from critical speed at all and 1/2 true critical at cruise. The RTLO's are really a single overdrive front box with an underdrive splitter, where one stick position down is direct, and top gear is something like .76??? in the front, and when the splitter is in 12th is something like .86. Not a true "double over" where there are two gearsets over driveing the input to a faster output. It is all in how it is plumbed in the trans that makes it seamless, kind of like when the went to the Xbar top cover on the RTO's you can't tell by the shift pattern if it is an RTO or an RT
-
In my book a 15 is a 12 anyway, and it is a transmission looking for a reason to be. I can see why fleets would spec them as it are a little more "idiot proof" than a 13 or 18. For me if I need the deep bottom end, I would choose 2 spd axles over an 18. 18 has the 15 beat any way you look at it, but in the wrong hands can get expensive quick I have a RTO 14615 in the Marmon, and the only reason it is still there is I retired before I could swap it out. Run what you came with until you have the money and time to change, but when you make the change, make it for the best possible spec's for how you are going to use it, or save your money. Just because it may be slightly better is not reason to jump from one compromise to another. The difference in cost when buying a 10 vs. a 13 or 18 on the used market is going to be a few hundred, but you still have all the costs of the bell, mounts and clutch over what you have now. I would sit tight with what I had and wait until the ideal set-up can be had. Do the Math! crunch all the numbers, startability, top speed, cruising speed RPM, jumps between gears etc.
-
Back in the Mack Pack!
Geoff Weeks replied to BOBWhite's topic in Antique and Classic Mack Trucks General Discussion
I think grain trailers can be either full trailer like you posted or pup with convertor dolly. One things for sure, you'll not be backing that out 1/4 mile at speed unless you are a whole lot better than I. I did know someone who could and did back 80' stretch trailer with pipe at 25-30 mph for a long while. Too much to go wrong quickly for me to try it. Same guy also backed a boiler and jeep into a garage in one go, I can do it, but not in one shot. -
I wouldn't have a 15 in anything if I had a say. I have one in my Marmon and hate it. If gearing for slow RPM at high road speed, steps between gears are critical to having something that works well. If using an Eaton, then look are rear gearing and transmission as a package. What you choose in the axle will effect if you want a RTO or an RTLO 13 or 18 My use was different than your, a lot more weight and wind resistance, but also a lot more displacement at power (ATA 3406). Being able to drop a gear and gain ~250 rpm vs ~400 rpm is the difference between a 13 and 15. I know right now you are thinking "I'm going up in HP I will not need to drop a gear" but there will be times you will and going to 1650-1700 is a lot better than 1900! I still say what you have will handle what you are putting through it, I wouldn't put a driver in it, but driving it yourself it would take it just fine.
-
That is only true for engine that use a rocker to work the injector. Engines with an injection pump (mech Cat and Mack) there isn't the rocker to trip the the exh valve at injection. So on those they have to use a valve on an adjacent cyl to trip and the timing isn't exactly right. It is why a mechanical Cat's Jake isn't as good as one on a Cummins. Once mfg went to electronic common rail with the cam pushing the injector and the electronics adjusting timing an duration, Jakes matched those of Cummins. 2 stroke Detroits had there own problems, keeping a Jake on those limited.
-
Yeah, my "education" was decades ago, but I still remember that today.
-
Caught me out the 1st time I ran the overhead on a Mack. Couldn't figure out what I did wrong! Once learned never forgot.
BigMackTrucks.com
BigMackTrucks.com is a support forum for antique, classic and modern Mack Trucks! The forum is owned and maintained by Watt's Truck Center, Inc. an independent, full service Mack dealer. The forums are not affiliated with Mack Trucks, Inc.
Our Vendors and Advertisers
Thank you for your support!