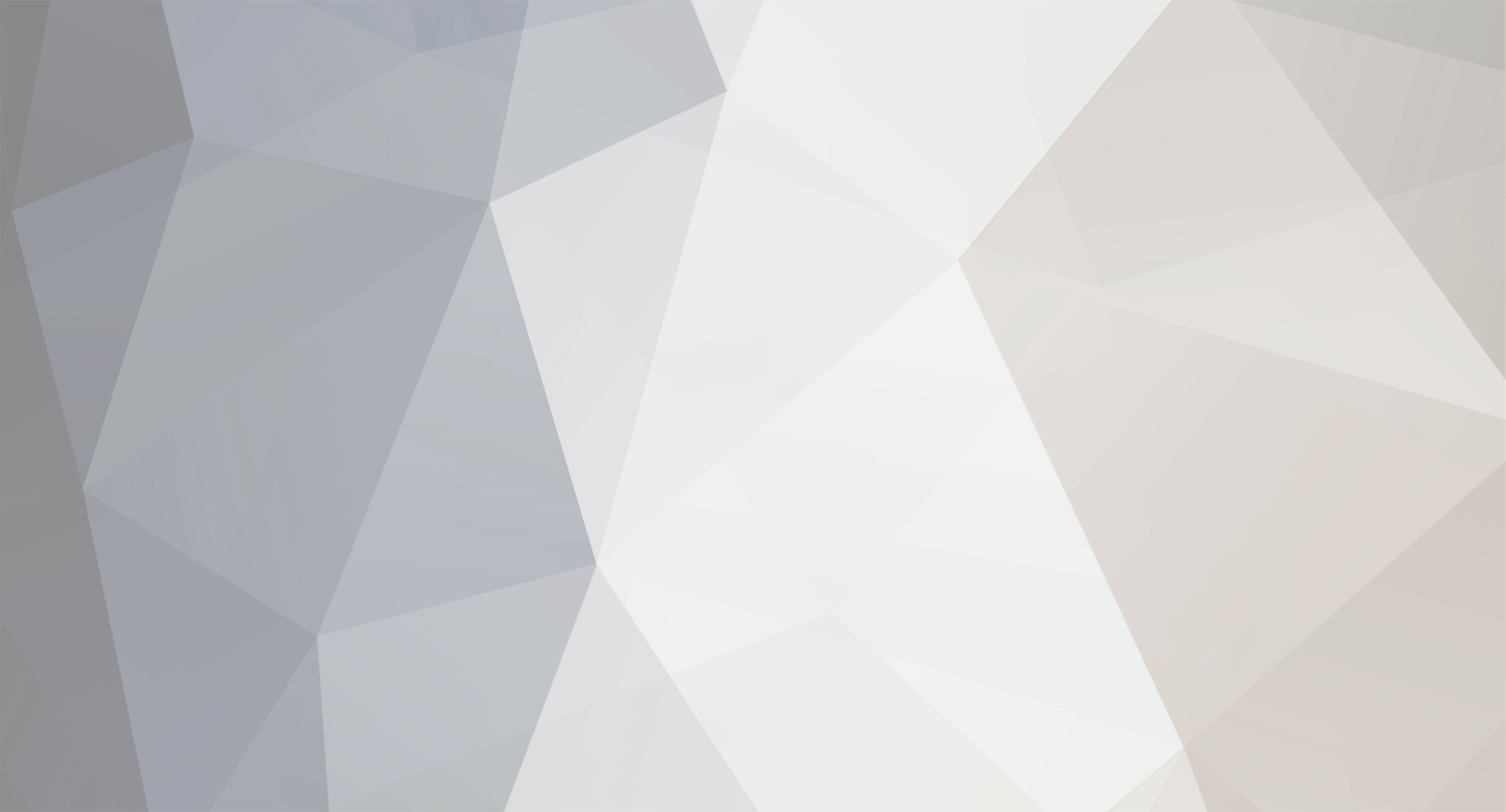
Geoff Weeks
-
Posts
1,730 -
Joined
-
Last visited
-
Days Won
6
Geoff Weeks replied to hicrop10's topic in Antique and Classic Mack Trucks General Discussion
Geoff Weeks replied to 1961H67's topic in Antique and Classic Mack Trucks General Discussion
Geoff Weeks replied to 1961H67's topic in Antique and Classic Mack Trucks General Discussion
BigMackTrucks.com is a support forum for antique, classic and modern Mack Trucks! The forum is owned and maintained by Watt's Truck Center, Inc. an independent, full service Mack dealer. The forums are not affiliated with Mack Trucks, Inc.
Thank you for your support!