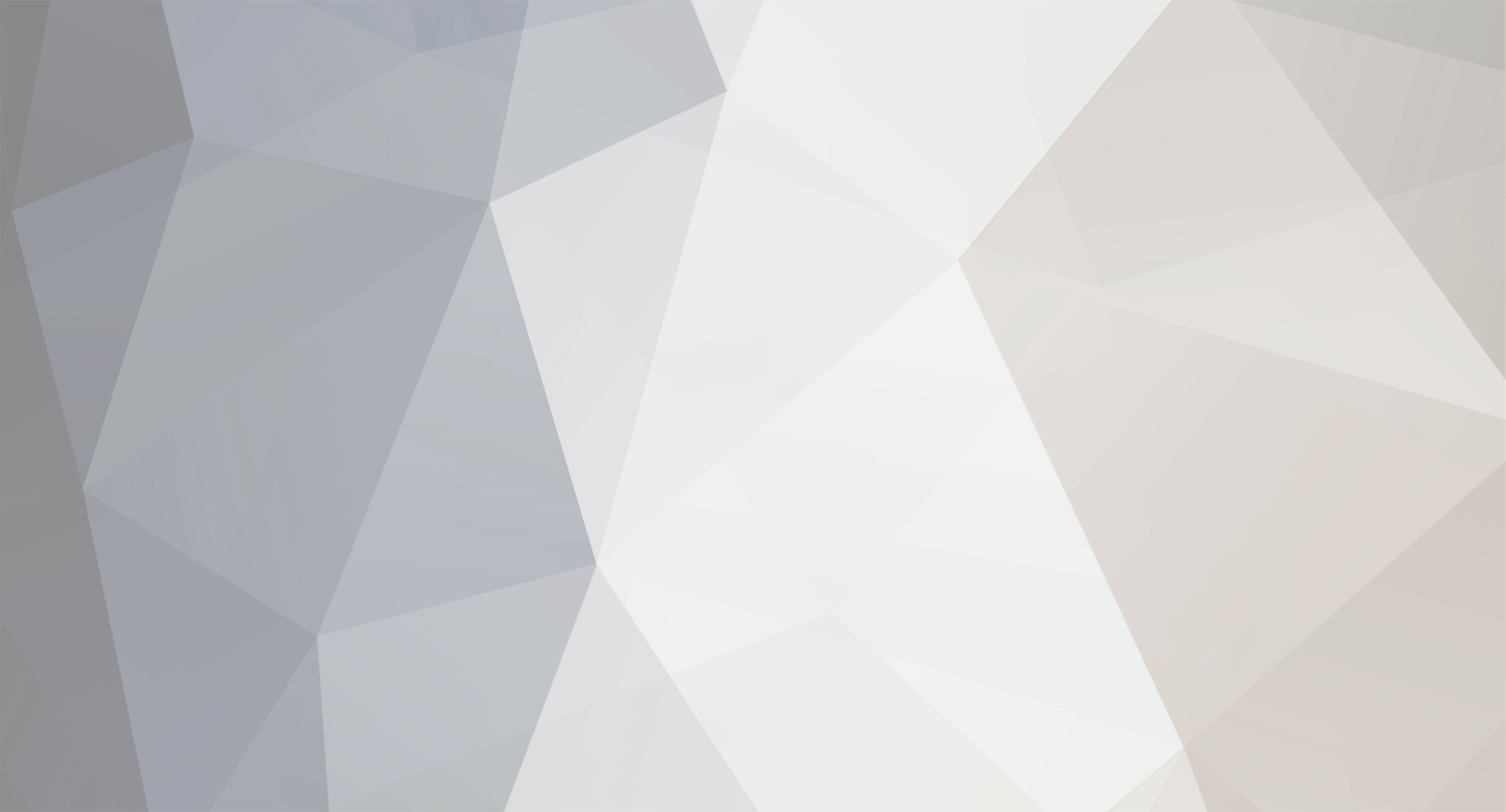
Geoff Weeks
Pedigreed Bulldog-
Posts
1,708 -
Joined
-
Last visited
-
Days Won
6
Content Type
Profiles
Forums
Gallery
Events
Blogs
BMT Wiki
Collections
Store
Everything posted by Geoff Weeks
-
Finally some DM progress
Geoff Weeks replied to mowerman's topic in Antique and Classic Mack Trucks General Discussion
ok then screw the shaft and it will bring the cover with it. It may take some torque on the shaft . CCW IIRC I was having trouble with the picture because it didn't show the box well at that angle. -
My experience it is almost always cheaper to go back with what it came with. That much movement in the Big end, means the crank is toast. You will have to assess the condition of the block and components. When I had something similar happen, I swapped in a used engine (for short term) and a re-ground crank (.010-.010) and saw many more miles out of the engine. engine swaps (for a different make/model) the devil is in the details. It will run you ragged looking for a special bracket or some other thing to get everything to play together. In some cases it make take a custom made part. If you are going to swap my vote would be Gardner 8LXB! (Since I'm spending your money not mine!).
-
SWAG, but I would look for a wire that rubbed through and make enough of a connection when wet to fowl things up, dry the resistance goes up and it works. Guy I knew with a KW had an intermittent problem, turned out a one point someone got some wires caught in the oil filter when it was tightened down. Must have pinched off some insulation and then when they were removed from the oil filter, would occasionally make contact with the block and the truck would die. Took many shops many tries to find that one!
-
Finally some DM progress
Geoff Weeks replied to mowerman's topic in Antique and Classic Mack Trucks General Discussion
turning the shaft should push the cap off the body. Likely just stuck. Nevermind, I thought I was looking at the steering box not the angle box. -
The way I'm seeing it, there is a cotter pin hole near the vertical, so I doubt is screws in, but it might be serrated on the other end of the pin.
-
Anyway you could rig up a threaded rod through the hole on the left of the picture and make a jack-screw out of it to force the pin to the right?
-
Front rear looks like an early IHC, rear rear doesn't as far as I can see.
-
Finally some DM progress
Geoff Weeks replied to mowerman's topic in Antique and Classic Mack Trucks General Discussion
Looks a little dark, better run it though again! -
Finally some DM progress
Geoff Weeks replied to mowerman's topic in Antique and Classic Mack Trucks General Discussion
Main thing to be careful of is making sure the pitman shaft is timed to the main gear. IIRC there will be some punch marks. -
New Mack Anthem
Geoff Weeks replied to james j neiweem's topic in Modern Mack Truck General Discussion
Done properly, it is a great system. Electrical equivalent of air start, lots of power for a limited time. Unlike air start, it can recharge itself even if the engine didn't start. -
New Mack Anthem
Geoff Weeks replied to james j neiweem's topic in Modern Mack Truck General Discussion
Interested in the "starting capacitor". Is it like Maxwells ESM, where all the cranking current comes from the supercapacitor and the rest of the trucks electrical is separate? I ran the Maxwell on one truck for many years and loved it. Still have it as the guy who bought the truck didn't care or know what it was. That essentially makes the trucks batteries all deep cycle service, where no high current loads are placed on them. With the Maxwell, as long as the truck batteries were over 10 volt and could supply around 18 amps at that voltage, it would charge and the truck would crank. 10volts is likely way too low for these newer "electronic" engine systems, but would start an older diesel just fine with batteries that low. Maxwell came in 2 voltages 12 and 24, but either could be charged off a 12 volt system. Then Elon Musk bought the company an suddenly the Maxwell was not long offered for sale! -
Back in the Mack Pack!
Geoff Weeks replied to BOBWhite's topic in Antique and Classic Mack Trucks General Discussion
vernier adjustable cables. Check with a tow truck supply house. Most often a large black knob with a red button in the center. Pull for rough adjustment, twist for fine. Push the red button for quick release. https://www.amazon.com/Vernier-Adjustable-VCGTX10-Locking-Control/dp/B0CNRPV957?source=ps-sl-shoppingads-lpcontext&psc=1&gQT=1 -
Replacement airbags for hendrickson suspension
Geoff Weeks replied to Gorilla's topic in Driveline and Suspension
I have had some really old (30 year?) Firestone bags. There are too many variables to know why they lasted. Like tires they are subject to UV and Ozone damage. Comfort/ride quality is determined by the design of the suspension not the air bag itself. The rolling lobe type that Hendrickson used is a good design, the "bell" shaped piston increases area as the the bag compresses. The Hendrickson splits the load between the Z spring and the bag. The bag does better are smaller high frequency bumps and the spring handles the large "swells" in the road. That is what made that design so popular. The last two question I have no knowledge to share. -
Are you just talking about the "center section" (Gears) and not the whole axle? I don't know how Mack does it, but Eaton and Meritor, you 1st ID the housing by casting number/ visual to get the basic model. To then know what rating housing it was built for you look at the diameter and spline of the side gears, and may be the diameter and spline of the input. Only difference between a 34K and a 45K diff is the side gear/axle shaft diameter. The next size up starts a 46K and goes up. 34-45 use a smaller ring gear and fit a smaller housing. Axle housings are ID'd by the bearings, brake and tube thickness. So, if trying to ID just the gear-set look to the axle shaft diameter and spline in the side gear of the differential. I guess what I'm trying to say, is the housing determines the capacity not the gearset.
-
With at least part of the hyd running over relief, it would let you know soon enough. A lot of heat is produced when that happens for a long enough time. It would happen on some manlifts (a valve would stick) and it wouldn't take long before it melted the hyd tank!
-
Yes, if the rack is physically stuck, it would not turn off, and it would not be governed (run a way) so it is not the rack is stuck, but either the signal to the actuator is not right. The fact that it would "de-rate" says the actuator is responding to inputs, both to de rate and to shut down.
-
You are asking for data not normally in any "spec" sheet when these vehicle were produced! I have a Dart and the spec sheet for it, and most of what you are looking for is not contained on it! In heavy trucks there are many engine and other options that can vary from truck to truck that are of the same model. My Dart oil field could have 3-4 engines running gasoline, butane or diesel! You can look up the spec's for the engine from the engine producer, but "number of gears" and "what it is used for" can vary widely. Fuel consumption depends on how it is used, and is never listed by truck! dimensions vary by how the truck was spec'd. Within the same model tire size alone can effect width, height etc. Once delivered to the 1st user, the trucks are often modified for their needs, adding beds, winches etc. In short, you are asking for something that doesn't exist on paper, and if it did would apply to one truck of that model only, not all trucks of that model!
-
Mack Transmission stuck in third gear
Geoff Weeks replied to Mack Snow Fighter's topic in Engine and Transmission
Plenty, but without being able to see and feel, not much help. twisted shaft, bent or damaged fork, interlock fail, shift tower problems, bearing failure, the list goes on. Your going to have to investigate more. -
New Mack Anthem
Geoff Weeks replied to james j neiweem's topic in Modern Mack Truck General Discussion
What hasn't changed a bit from the early days, is the number of axles to haul the weight and therefore the number of brakes to slow the load. 140K, 170K at 70MPH with the same brakes that were used when the speed was 1/2 that is not an improvement. More power will help get the load up the grade, but takes a good hand to get it back down the other side. I once pulled Butte, MT westbound and was one gear up from bottom, I could have used more power! only had a 315 HP at 1800 RPM gov limit, if that. Now we have big power, but still the same 7-8 axles and brakes under the same load. More power and the temptation to grab more gears and speed when pulling a grade instead of selecting a gear and riding it to the top, Much easier to do damage shifting under that kind of load on a grade, then taking more time and pulling to the top a bit slower. -
New Mack Anthem
Geoff Weeks replied to james j neiweem's topic in Modern Mack Truck General Discussion
Only thing that has changed, is the tolerance for slow moving large loads. -
New Mack Anthem
Geoff Weeks replied to james j neiweem's topic in Modern Mack Truck General Discussion
My DART oil field 150 has a 6-71 2 valve, they were rated at 200 hp! When they went to 4 valve they jumped to 238. -
New Mack Anthem
Geoff Weeks replied to james j neiweem's topic in Modern Mack Truck General Discussion
I showed up at a train de-rail, with a 6-71 (238 hp) Fleetstar, and was getting razzed, the old semi retired driver for the H-H company said "we used to move super loads with that power'. I used my Fleetstar because I knew I would have to go down an access road to retrieve the rail car. I took all the trailers down, turned them around and stretched them out for the other "large car's", on the understanding I would get the 1st load out! They ribbed me I could have the 1st load but would be last to be unloaded. The old gray hair said under his breath "don't you bet on it! You could here that 6-71 for miles, and I was the 1st to unload! -
New Mack Anthem
Geoff Weeks replied to james j neiweem's topic in Modern Mack Truck General Discussion
Pulling the same stuff we moved with 350-400hp! I moved the same stuff the oldtimers (at that time) moved with 200 hp! -
Not up on the newer stuff, but I know Meritor (Rockwell) made some double reduction units. There are two different capacities you need to consider, one is the housing and brake capacity and the other is the torque/reduction needed to move that. The double reduction were built like a standard front of a tandem with a high input and a bull gear on the pinion, but differed in that the drive ratio wasn't 1:1 from the input to the bullgear on the pinon. housing and brakes were higher capacity, allowing to carry more weight.
-
The switch allows you to quickly test that both are working, You should see an RPM drop when firing on only one, often around 50 rpm. Start on both, flip to one, then the other, to check and then back to both.
BigMackTrucks.com
BigMackTrucks.com is a support forum for antique, classic and modern Mack Trucks! The forum is owned and maintained by Watt's Truck Center, Inc. an independent, full service Mack dealer. The forums are not affiliated with Mack Trucks, Inc.
Our Vendors and Advertisers
Thank you for your support!