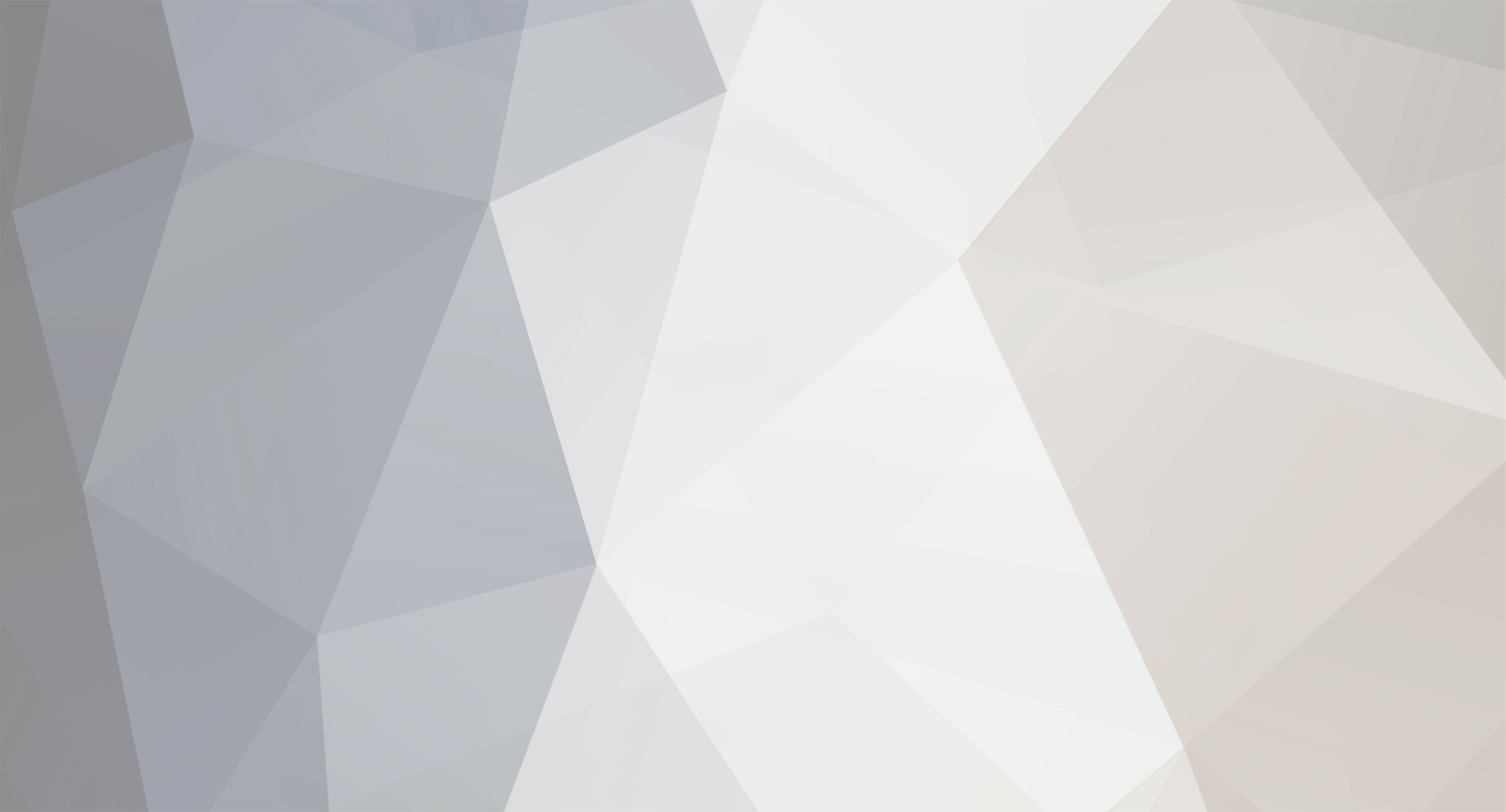
oldspwr
-
Posts
151 -
Joined
-
Last visited
-
Days Won
7
oldspwr last won the day on October 6 2021
oldspwr had the most liked content!
oldspwr replied to Goldsburg's topic in Brockway Trucks
oldspwr replied to mattb73lt's topic in Antique and Classic Mack Trucks General Discussion
oldspwr replied to R Steele's topic in Antique and Classic Mack Trucks General Discussion
oldspwr replied to R Steele's topic in Antique and Classic Mack Trucks General Discussion
BigMackTrucks.com is a support forum for antique, classic and modern Mack Trucks! The forum is owned and maintained by Watt's Truck Center, Inc. an independent, full service Mack dealer. The forums are not affiliated with Mack Trucks, Inc.
Thank you for your support!