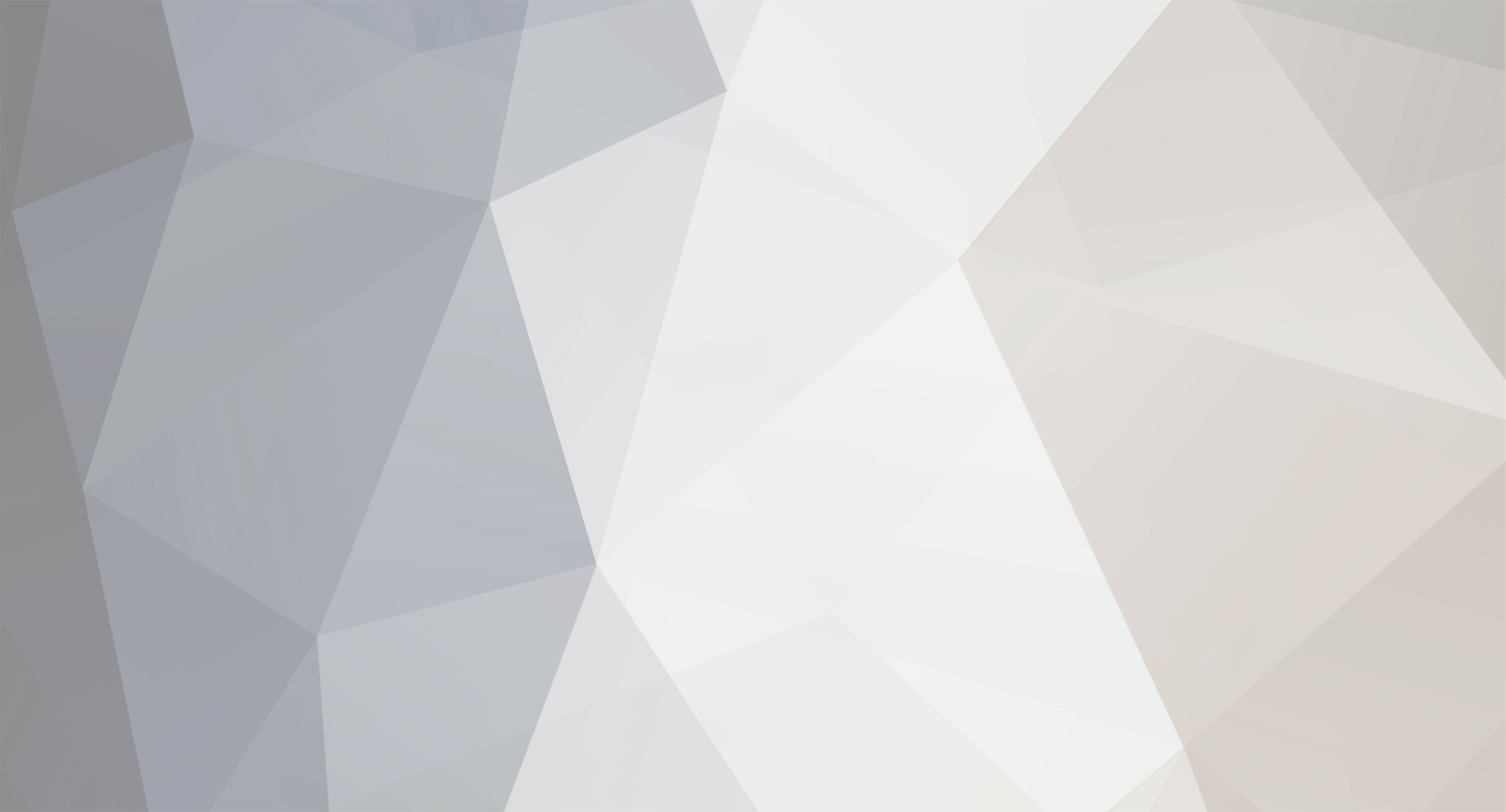
Geoff Weeks
Pedigreed Bulldog-
Posts
1,503 -
Joined
-
Last visited
-
Days Won
6
Content Type
Profiles
Forums
Gallery
Events
Blogs
BMT Wiki
Collections
Store
Everything posted by Geoff Weeks
-
My air ride truck and trailer would go 45 min running down the hiway between compressor cycles. I am not stranger to eliminating air leaks. Anything less then 15 mins while running down the hiway between cycles and I was looking for leaks. few trucks I have been around can meet or beat that, and mine had air fan clutches, just saying.
-
"thing is i have four 920ah batteries" That I got to see! I had 4 155 amp/hr batteries for a total of 620 amp/hrs and they all are bigger than the std gp 31 truck batteries. Deep cycle gp 31's are 135 amp/hrs, cranking gp31's would likely be a bit less. I think you are confusing CCA with amp/hrs, they are not the same thing. When an electrical load is placed on the truck, the alternator will take up that load up to the capacity of the alternator, then the batteries start depleting. Converting from rotational belt to electrical and back to rotational is not an efficient process. Fixed RPM means that load is fixed. It also means it can't reduce draw at lower loads and can't increase when needed, like pulling a hill. So when a fan is needed to pull air across the condenser, you'll have only one choice, with an electric fan, where as an engine driven fan can turn slowly at idle,using very little power. A/C compressor use "face seals" to hold in a fix amount of refrigerant at pressures exceeding those of the trucks air system. The older Hortons anyway, not sure on the new stuff, also use face seals for the air. They also use O rings for the piston seals. I find moisture in the air causes most problems, be it with the fan clutch or elsewhere. No mfg of a truck or bus engine relies on an electric fan, that should tell you something right there. On motor coaches where direct belt drive for the fan is not practical, hyd drive is used. Your money, your choice, but wouldn't be mine.
-
Nothing is free, that electric also loads the engine. It turns at a single speed, and can't be mechanically locked to be drive all the time like most engine driven clutches can. When the electric fails, it is done and you have no fan. Your choice, but I would never use an electric in that application. I have had two electric fan clutches, both worked well. One Facet and one OEM (on a car) Both had ways to "lock" them mechanically . The old Bendix spring applied, air released clutch is my #1 with the old Horton air applied #2 Had more air leaks on the Horton than the Bendix.
-
Good eyes, Vlad! Yes it is the Neway ARDAB (piece of C$%p) suspension and the reason the Marmon was parked. It needs new bushings, the plan was to replace with a Hendrickson Air clone (IHC air ride) I had. Health issues meant it never got done, and I suspect whoever ends up with my Marmon when I sell will want to put another suspension of their choosing under it. Other than the bushings, the truck is ready to roll. With the bushings out the rear suspension alignment is out, and it is hard on tires. I did a lot of work on the Neway before I gave up on it. Neway has NO support for this suspension and once took 18 months to get a needed bracket. The stamped steel air spring seats rot out, and Neway's answer is to replace the whole beam! I made new spring seats from structural steel and solved that problem, but it really has nothing going for it, and with the lack of support, a suspension swap just makes sense.
-
Back in the Mack Pack!
Geoff Weeks replied to BOBWhite's topic in Antique and Classic Mack Trucks General Discussion
CTS 2301 It covers the Fleetstar line. Volume 2 covers cooling systems. -
Back in the Mack Pack!
Geoff Weeks replied to BOBWhite's topic in Antique and Classic Mack Trucks General Discussion
Should look something like this: shutters.pdf -
Back in the Mack Pack!
Geoff Weeks replied to BOBWhite's topic in Antique and Classic Mack Trucks General Discussion
Yeah, I don't know if parts are even available anymore for them. I would disconnect the linkage and see that everything moves freely. Other then that, the only real test would be to remove the engine fan and let the radiator heat up, until engine temp is close to 200 and see if they move. You'll not likely see them move much when running the truck, as they close when the temp in the bottom tank is below (engine) thermostat setting. -
Back in the Mack Pack!
Geoff Weeks replied to BOBWhite's topic in Antique and Classic Mack Trucks General Discussion
Yeah, I found the instructions for them. If the engine has a 180 deg stat, the shutters should open when the bottom tank is at 180 deg, engine should be at 190 at the top outlet hose. Shutters don't open to full 90 deg on the shutter "blades" only go to about 45 deg open. Fully mechanical so any rusted linkage will jam the operation. I can see two nylon bushing in your linkage cross shaft. Just make sure it is free to move but don't force the actuator. If you need more I can try and scan the pages, but yours looks functional. -
Back in the Mack Pack!
Geoff Weeks replied to BOBWhite's topic in Antique and Classic Mack Trucks General Discussion
I could be wrong, but I believe that is the type of shutter that is fully mechanical. It uses a "wax pill" to operate the shutter. No air involved at all. The temp setting should be the same as the thermostat, as the sensing unit is in the bottom tank. Somewhere I have the info on them, as I have that type on one of my Fleetstars. One of the things I remember it saying is "DO NOT FORCE" the shutter or you can damage the "pill". On mine, all I had to do to get it working is to take apart the linkage and paint with graphite paint. -
I do know this style wheel was made in several sizes and at least 2 shaft sizes. It does seam to be used on trucks made for the military production during the war years. Later and earlier civilian production didn't use this wheel. Hopefully I'll get the correct wheel later in the week. then I have to find the correct horn button assembly for it.
-
91 superliner electronic tach
Geoff Weeks replied to 70GMC's topic in Electrical, Electronics and Lighting
The common electronic tachs I am familiar with use a mag pick-up on the flywheel that reacts to the ring gear teeth. They are not "powered" pick up. There are some that run off an ac tap on the alternator. If your engine doesn't have a cable drive, it should have a 3/4" x 16 tpi hole tapped into the bellhousing for a mag pick-up.- 1 reply
-
- 1
-
-
Back in the Mack Pack!
Geoff Weeks replied to BOBWhite's topic in Antique and Classic Mack Trucks General Discussion
In case I wasn't clear, I wasn't saying elements were not made anymore, just the filter housing. Elements should be available from any filter mfg. Baldwin, A/C etc -
The guy I bought this one from got back to me and thinks he has one with the correct shaft opening, waiting to work out an exchange. One of my K-7's has one and after 80 some odd years is near perfect condition. The other was post war and has the OEM wheel, which is all deteriorated as most do.
-
Back in the Mack Pack!
Geoff Weeks replied to BOBWhite's topic in Antique and Classic Mack Trucks General Discussion
Filter should look like this on the inside, It appears the Farr of old has been acquired by someone else and is no longer made. -
Back in the Mack Pack!
Geoff Weeks replied to BOBWhite's topic in Antique and Classic Mack Trucks General Discussion
If I am not mistaken, that is a Farr aircleaner. open and count the tubes across and down and get that size element. They were more of a "construction" equipment air filter and often were tied with an "aspirator" on the exhaust to "knock" the bigger dust particle off and blow them out with the exhaust flow. -
Looking for a "military" style steering wheel in the 18-20" range and a 1inch 36 spline. I bought this one, but it was miss labeled as a 1" and is a 1 1/8" shaft.
-
If you want to try and diagnose the present system, start at the regulator. With the battery disconnect switch in the "on" position and ignition switch off, you should have power at the left terminal of the regulator when measured between it and ground AND measured between it and the case. Next turn the ignition switch on engine off. You should see power at the ignition terminal of the regulator (the one by itself on the other side from all the other terminals), as well as power on both the generator (center terminal) and some on the field terminal. So all three terminals should have some power at least with the engine not running and the ignition on. Start the engine and look for AC voltage between any two of the three big output terminals on the alternator. If you don't have ac voltage, check the two small terminals on the back of the alternator (they are slightly staggered) one should be seeing power and the other should be going to the ground side of either the engine block or the rectifier. If you see power on one and none on the other, it is ok, if you see power on both, you have have a broken ground side wire, If you don't see power on either, you have a broken wire between the regulator field terminal and the alternator. With the engine running, the voltage at these small terminals (field voltage) will be less than the full 12 volts, but should be a readable voltage. The part most likely to fail is the rectifier. It can fail open (no power gets through) or shorted (allows power from the battery to drain through the stator windings. You can replace the rectifier with a set of diode blocks out of a modern alternator, you'd need to mount them on an insulated board and somewhere where they would get good airflow to cool them
-
If your regulator is EXACTLY like the one in my picture (there were several different regulators used), with the side with the single terminal pointing away from you and the three facing you, the three are far left: output to batteries and/or ammeter center: output from rectifier/ alternator far right: field the single terminal facing away from you is ignition feed. Note the regulator is mounted in rubber bushings and need the case grounded to function. On most there is a tab on one of the bushing that grounds from the bolt to the case of the regulator. If you are going to replace with a modern one wire alternator, you need to extend the wire from the left terminal on the regulator to the output stud on the alternator, and remove the regulator from the truck. You also remove the rectifier and assorted wires along with the L/N alternator. Note: you can identify the main current carrying terminals on the regulator as they have 2 screws holding the wire terminals on the regulator, the field and ignition feed only have one. They are also stamped with letters (G or generator) F for field, ign for ignition etc.
-
If you are going to go with a modern alternator, you'll need a pulley (most modern stuff uses a 7/8" shaft, the early L/N uses a smaller shaft) but most importantly, you'll need to make a new mount. The early L/N was designed to replace the normal generators of the day, and so came with a mount that would fit the same as a generator. Modern alternators come in either pad mount (not what you need) or SAE j180 swing mount. The SAE mount takes a 1/2" bolt and has a spool on the engine 1/2 of the mount, the two ears on the alternator fit over the spool and a 1/2" bolt passes through all. The generator mount used 3/8" bolts and a much wider spacing between "ears". To make the mount, you'll need some 5/16" or 3/8" plate and some cored bar or xx pipe (schedule 180) for the spool. It has a 1" or so OD and 1/2" ID. The mount will have to be fabricated carefully as it aligns the alternator (and therefore pulley) to the engines belts. Alternatively, you could buy a mount for a Cat or Cummins (or other engine) and adapt it to your block. Alternator will need to be either positive ground or case neutral.
-
Ok, then it is a Leece Neville alternator set up. A Delco 40DN looks some what similar but doesn't narrow down at the rear like the L/N does. Note: both have 3 AC taps on the top. Next question is do you want to fix the original or replace with something modern that is easier to get parts for? replacing makes it easier for someone not familiar with these old systems to work on it, fixing keeps the truck "period correct".
-
Sounds like the brake treadle valve is leaking. Check for air leaking out the bottom of the valve (floor mounted) or back of valve (firewall mounted). Kits are available for both types, but most just buy a reman and slap it on.
-
Likely a Leece Neville, but could also be a Delco 40DN or 30DN with something else wired to it. For the 4th time, does it look like the picture I posted? I can't help if all you do is repeat what very little info you started this post with. Tag pictures with the info and numbers would clinch the ID, Alternator, regulator and "rectifier", then we can address what the options are.
-
Not exactly like, but a version of our piston type spring brake chambers. I guess in Europe, they know enough not to remove the bolts holding the chamber together with out caging it in some way, so don't need our idiot-proof non serviceable chambers that are required here,. I have similar MGM piston chambers with the big snap ring on the rear cover/lid on my Marmon. https://mgmbrakes.com/files/4815/8153/4411/MGMBRAKES_PISTON_BRAKES_FINAL.pdf
-
did the stud back out (hopefully) or did it snap off below the spoke surface? They can be a pain if the stud snapped off. If near the surface weld a nut onto the top of the stud, gives something to wrench on and heat from the arc weld often breaks the rust bond.
BigMackTrucks.com
BigMackTrucks.com is a support forum for antique, classic and modern Mack Trucks! The forum is owned and maintained by Watt's Truck Center, Inc. an independent, full service Mack dealer. The forums are not affiliated with Mack Trucks, Inc.
Our Vendors and Advertisers
Thank you for your support!