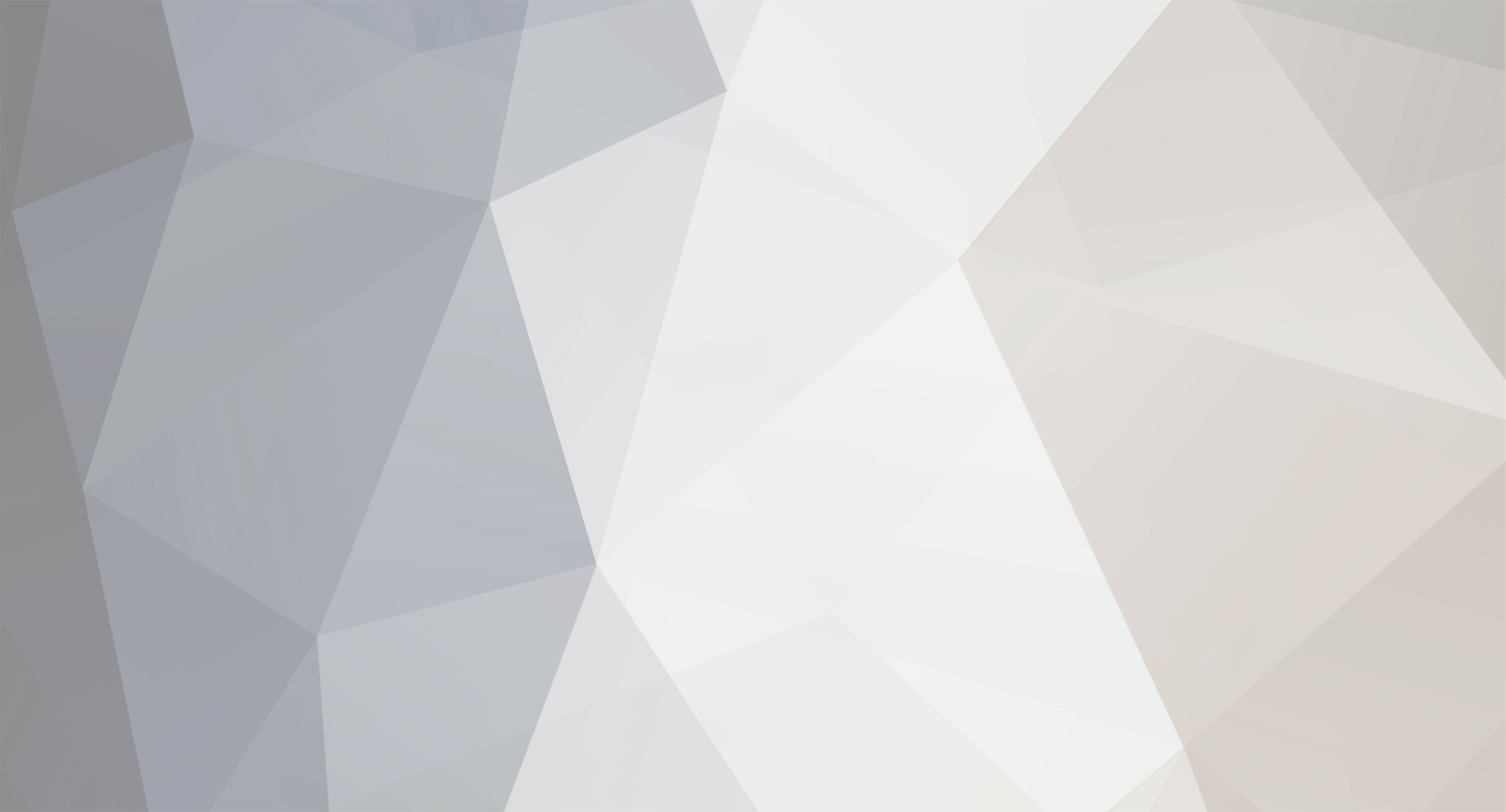
Mackpro
BMT VIP-
Posts
3,016 -
Joined
-
Last visited
-
Days Won
10
Content Type
Profiles
Forums
Gallery
Events
Blogs
BMT Wiki
Collections
Store
Everything posted by Mackpro
-
https://www.bigmacktrucks.com/topic/34802-04-vision-coolant-push/ Also this old thread has some more bulletins for this issue.
-
Amazon has the 180 and 185 thermostat kit from PAI . Mack found that when both thermostats opened at the same time it could cause a coolant push problem. So they recommended the staggered opening temps
-
http://www.engineprofessional.com/TB/TB011816-1.pdf One one cause of ASET AC EGR cooler failures is this screen getting clogged and blocking coolant to EGR cooler causing it to overheat and crack
-
https://f01.justanswer.com/HeavyEquipmentTech/6bc71206-6fd3-4357-bdfd-e51101cf15ec_Mack+cooling+system+revisions+SB215025.pdf Thermostat housing update
-
https://f01.justanswer.com/HeavyEquipmentTech/9c63171c-1162-4f60-93c3-75b9bbaba99c_Mack+surge+tank+update+sb232026.pdf one piece surge tank bulletin
-
The radiator pressure cap should be a 16 pound cap. Some people put a 10 pound cap on them and cause them to open to soon and push coolant. The ASET AC engine you have uses the 16 pound. The ASET AI and all other Mack engines ( gray engine) use a 10 pound cap. Lots and lots of bulletins on coolant push with your ASET AC engine out there . I was a Tech and Warranty Administrator at a dealership, we averaged about 250 warranty claims a year , in 2004 when the ASET engines came out our warranty claims jumped to almost 700 a year. Lots of updates came out and by mid 2006 and 2007 the failures dropped as updates were installed at the factory and existing truck were updated. Updates included new thermostats ( one opens at 180 the other at 185), new thermostat housing and piping. One piece aluminum expansion tank and better service procedures to test and correct on going issues
-
Injector cup issues
Mackpro replied to james j neiweem's topic in Modern Mack Truck General Discussion
I guess I should not have praised the common rail injectors on Thursday. Had a #.2 pumping injector go down . At least it wasn’t a cup issue. If you ever get multiple injector faults check for DEF in the fuel . Lucky it was just a faulty injector this time . But we have had drivers talking on the phone/ distracted while fueling up and put DEF in the fuel tanks and eat the injectors up -
https://volvotrucks.vg-emedia.com/FileImageDisplay.aspx?FileId=6030&DisplayType=attachment The tool number is 88800031 but no ones seem to make it other than Mack/Volvo . However I found on the Volvo side , it list the measurements from the tone wheel tooth to outer edge of the upper timing gear cover. Just line the tone wheel teeth up to the middle of the hole use a depth mic to get a reading and choose the number of shims you need . I don’t remember the Mack bulletins showing the actual measurements, only to use the tool .
-
2005 CV713 Maxitorque T310M/MLR Synchro Help
Mackpro replied to Detailed0707's question in Mack Truck Q & A
I always hated working on mack manual transmissions but as Joey said the in chassis repair can be done with the special tools but it’s still no fun . There are 3 things we have found that cause synchro failures in the Mack manuals trans . Number one thing is the set screw for the high/low range fork backing out. This is a common problem. The 107 series and early 200 series transmissions had a set screw that was drilled for safety wire. I remember the old guys rebuilding them in the 80’s using the safety wire, wish they still used it . Second thing is the stupid rear yoke bolt and washer set up . This has been a pain for years . A lot of the time we find the yoke bolt and washer missing and the only thing holding the yoke on is the pressure from the driveshaft/carrier bearing . These two things greatly affect the high low synchro. The third thing is driver error. Upshifting not so much but when downshifting and flipping the hi/low range to low at to high a speed seem to make cause a lot of bad noises. I only range shift from high to the low side when I’m almost to a full stop. -
If the ports are getting clogged on the Venturi pipe where the EGR differential pressure sits it tell the engine ECM that the EGR flow is below the target flow rate. Even though the actual flow rate probably within specs , the engine ECM will command the EGR valve to open more to meet the target flow rate . So now you got more than needed EGR flow( dirty exhaust) going back through the engine. This produces more than usual soot to clog the DPF filter. I have had this happen on the MP8 even with the newest EGR diff sensor/Venturi pipe set up. Below is a picture of the newest sensor/ pipe for the MP8. I usually pull them off and clean them on the inside.
-
Like the MP8 engine turning tool. Part number 88800014 , $268 at Mack . Amazon is $20 . This fits all MP8’s . Unsure on MP10. All the MP7’s I’ve seen use a different turning tool.
-
Yes I agree 100%
-
Anyone with a 2008 or newer Mack or Volvo who does any work on their truck needs a coolant drain hose tool. It makes draining coolant super easy since there are no petcock drains on them anymore. Part number 9996049 , they are not available from Mack anymore and cost is $136. Type that part number into Amazon and $40. I bought mine through Mack many years ago. My buddy was needing one and called Mack and found out the price and no availability. I got him the part number and Amazon to the rescue.
-
Injector cup issues
Mackpro replied to james j neiweem's topic in Modern Mack Truck General Discussion
We have not had any cup issues with any of our common rail engines. A few injector issues but none cup related. Still same injector cup but only 3 injectors are driven off the camshaft, which is why they fail. The camshaft/rocker arm rocks the injector back and forth eventually causing it to leak. That part is still the same but now you only have a 3 injectors to worry about leaking instead of 6. Still a crappy set up. -
2006 Mack vision cxn boost/ low power issues
Mackpro replied to griffvision's topic in Engine and Transmission
Do you have any Qualcomm or data logger plugged into the 9 pin Diagnostic connector?? -
I’ll see what I can do . I forgot I was signed in under Customer Portal .
-
the pattern is still the same I think they might have upped the torque valve a little. Same thing with the injectors . I believe they upped the torque 3-4 pounds
-
https://macktrucksdealer.vg-emedia.com/InformationListing.aspx?GroupId=536 Click on the underlined SB***** of the topic you want then click on Print/Save file to view the bulletin/info. I’m shocked Mack still has this on there .
-
I did not know that about the IPhone ( I have one) Mack still has some information on the MH on their E-media website. I’ll se if I can post a link. Also if anyone needs a digital copy of this book message me your email and I’ll see if I can scan it for you .
-
I started when the E7 had just been introduced. The old guys were bitching because they had finally gotten used to the E6 4 valve head engines. Had a really good old guy teach me lots . He was from Long Island and he used to restore Duesenburg cars when he was younger. I remember him rattling off torque specs of those engines. I wish I’d have listened to him more but I was just a 18 year older kid back then . I miss him greatly.
-
Last September I did 9 sets of injectors/cups in a little more than 2 weeks so that’s burned into my brain. Plus all the years at the dealership where i amassed two 5 gallon buckets of just copper cups when we were doing the change over to stainless cups., never bothered to save the stainless ones .
-
Mack updated the torque specs for the rocker arm shaft a while back. Some of the older books might have have the old data in them . This is only for the rocker arm shaft on the MP8. Tighten all hold down bolts to 44 ft pounds. Then one at a time, loosen and retighten to 30 foot pounds except the large single bolt in the rear , it stays at 44 for now. Then tighten all 120 degrees ( including big single bolt ) . This is 2 flats on the bolt head .
-
https://static.nhtsa.gov/odi/tsbs/2013/SB-10082932-6903.pdf Scroll down to the pics of the injector sealing areas. If any of the injectors looked “ unusable “ then the cup and injector needs to be replaced. This is a old bulletin but useful information. Mack now says don’t do the thread tap and pull on the stainless cups as the thread shavings were wiping out turbos left and right. Mack now has a expanding puller that grabs the sides/walls of the cup and pulls it out super fast. On copper cups you still have to use the thread and pull tool method.
-
Did you have install tool to form the end of the cup to the head ?
BigMackTrucks.com
BigMackTrucks.com is a support forum for antique, classic and modern Mack Trucks! The forum is owned and maintained by Watt's Truck Center, Inc. an independent, full service Mack dealer. The forums are not affiliated with Mack Trucks, Inc.
Our Vendors and Advertisers
Thank you for your support!