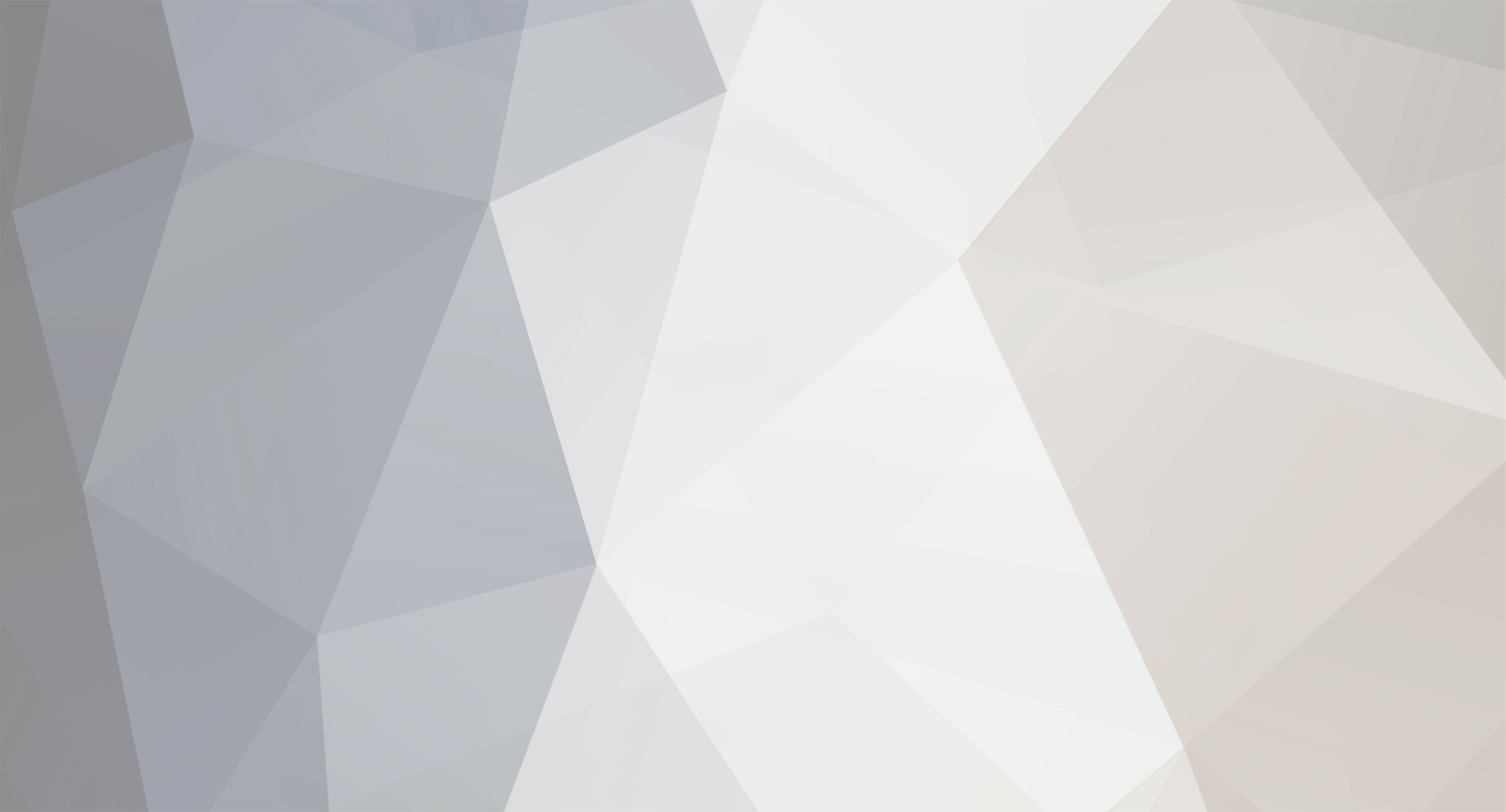
JoeH
-
Posts
2,714 -
Joined
-
Last visited
-
Days Won
18
JoeH replied to SpreadingLime's topic in Driveline and Suspension
JoeH replied to Salpolit's topic in Engine and Transmission
BigMackTrucks.com is a support forum for antique, classic and modern Mack Trucks! The forum is owned and maintained by Watt's Truck Center, Inc. an independent, full service Mack dealer. The forums are not affiliated with Mack Trucks, Inc.
Thank you for your support!