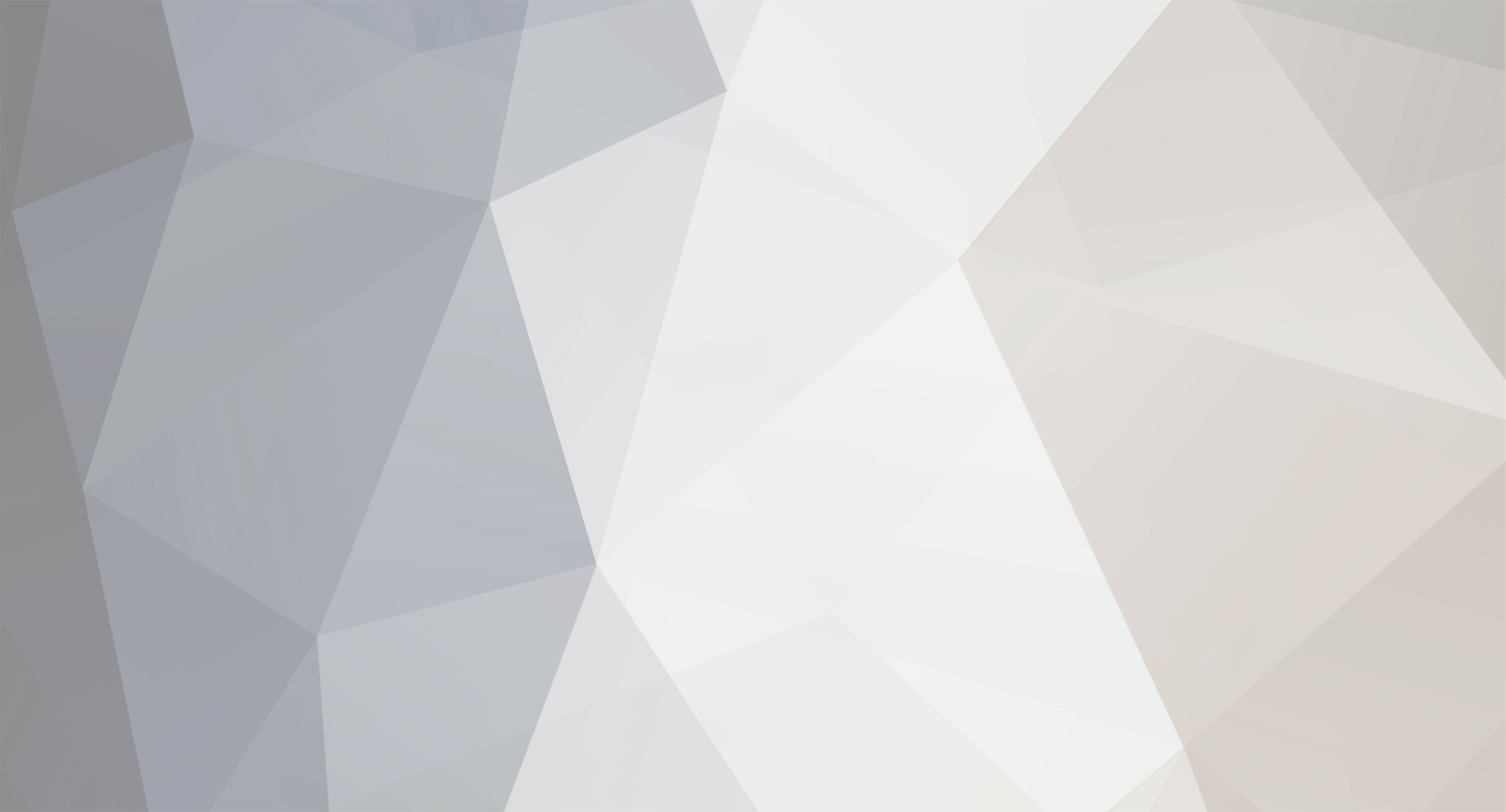
kt_Engineer
-
Posts
87 -
Joined
-
Last visited
kt_Engineer replied to BottleHauler84's topic in Driveline and Suspension
kt_Engineer replied to Outlawfleet's topic in Driveline and Suspension
kt_Engineer replied to JoeH's topic in Driveline and Suspension
kt_Engineer replied to fjh's topic in Driveline and Suspension
BigMackTrucks.com is a support forum for antique, classic and modern Mack Trucks! The forum is owned and maintained by Watt's Truck Center, Inc. an independent, full service Mack dealer. The forums are not affiliated with Mack Trucks, Inc.
Thank you for your support!