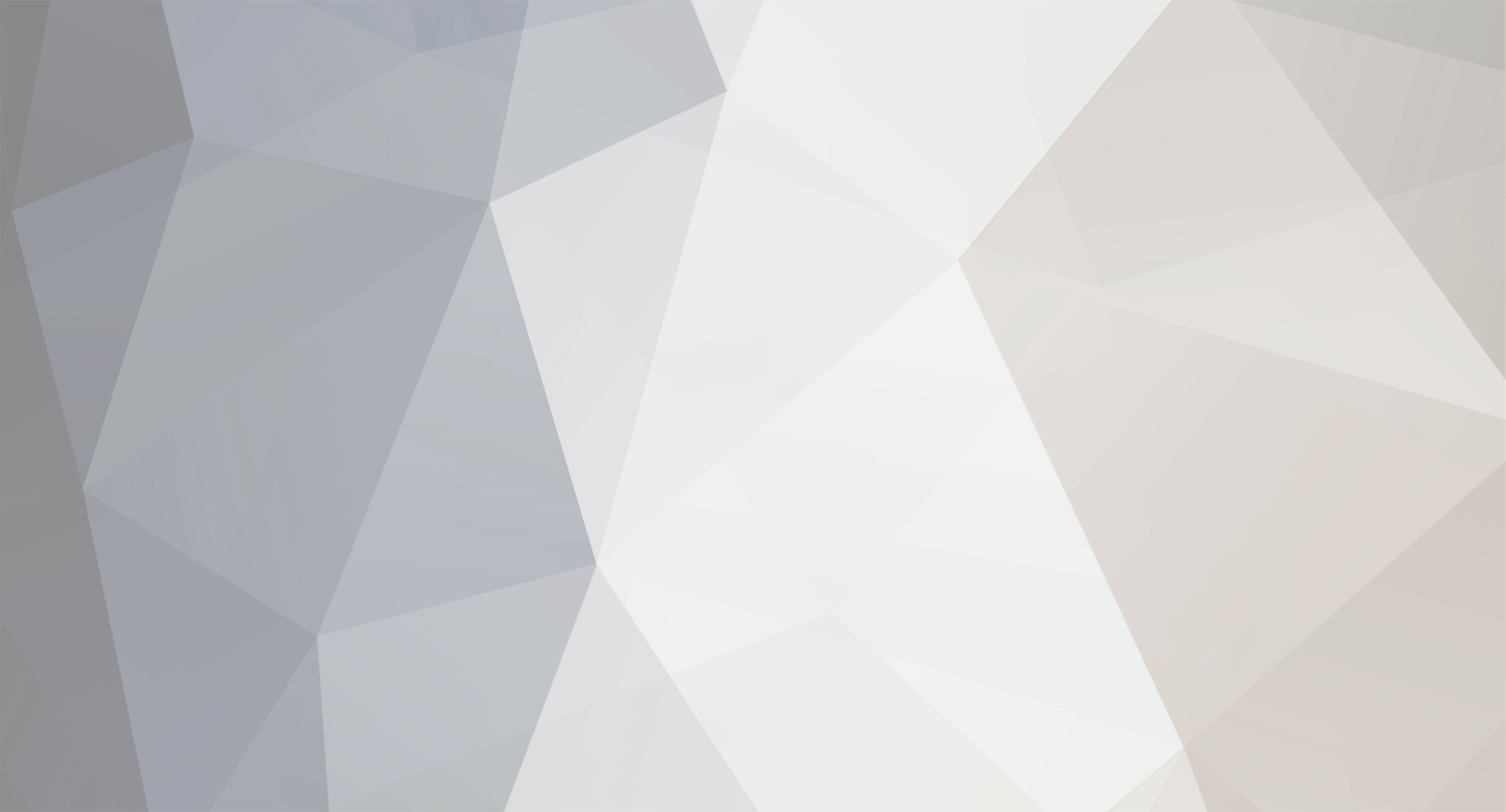
kscarbel2
Moderator-
Posts
18,686 -
Joined
-
Days Won
112
Content Type
Profiles
Forums
Gallery
Events
Blogs
BMT Wiki
Collections
Store
Everything posted by kscarbel2
-
My email to Kim Davis (that KY county clerk in the news)
kscarbel2 replied to RowdyRebel's topic in Odds and Ends
Friend, just when do you think the masses ever held the real power in our country? -
Trump says he'd deport illegal immigrants as U.S. president
kscarbel2 replied to kscarbel2's topic in Odds and Ends
Interesting to hear one of our politicians, Republican presidential candidate Carly Fiorina, acknowledge our government's decades long incompetence at the border, AND hear her point out that (as we all here still realize) the one and only language of the United States of America is English. http://us.cnn.com/videos/us/2015/09/03/carly-fiorina-trump-bush-immigration-english-pledge-sot-newday.cnn -
"People should and do trust me" - Hillary Clinton
kscarbel2 replied to kscarbel2's topic in Odds and Ends
The State Department employee who helped Hillary Clinton set up her controversial private email server will dodge giving testimony to Congress. Brian Pagliano, who worked at the Department when Clinton decided to install the insecure, homebrew technology, has been asked to appear before the Benghazi committee. But, according to the Washington Post, he will plead the Fifth Amendment to avoid giving any testimony. -
"People should and do trust me" - Hillary Clinton
kscarbel2 replied to kscarbel2's topic in Odds and Ends
It sounds as though Hillary was working for herself............rather than the American people via the United States government. http://news.yahoo.com/another-57-clinton-email-threads-contain-foreign-governments-205309673.html "Here's my personal email," Hillary Clinton wrote to U.S. special envoy George Mitchell on a summer Sunday in 2010 as he telephoned one European official after another in an effort to keep peace talks between the Israelis and the Palestinians on track. "Pls use this for reply," Clinton wrote in her email, sent from the clintonemail.com account she set up on an unsecured, private server in her New York home for her work as secretary of state. -
My email to Kim Davis (that KY county clerk in the news)
kscarbel2 replied to RowdyRebel's topic in Odds and Ends
Court records show that the defiant Kentucky clerk, Kim Davis, has been married 4 times and had twins out of wedlock. She divorced in 1994, 2006 and 2008. Davis, 49, gave birth to twins 5 months after she divorced her first husband. The twins' father was identified as her third husband, according to records obtained by the U.S. News and World Report. She has been married twice to her current husband, Ed Davis. -------------------------------------------------------------------------------- Sounds like a real piece of work to me..........not sure what faith she is following. -
DAF Press Release / September 1, 2015 DAF is to invest EUR 100 million in a completely new state-of-the-art paint shop for its cab factory in Westerlo, Belgium. Upon completion it will be the most modern truck-cab paint shop in the world. The Dutch truck manufacturer made the announcement today during a visit by Philippe Muyters, the Flemish Minister for Work, Economics, Innovation and Sport. The first cabs will leave the new 25,000 m2 large paint shop in the first half of 2017. DAF opened its Westerlo factory in 1966, where - in addition to cabs - it has also produced its own axles since the early seventies. The current workforce of 2,150 employees produces around 500 axles and 200 cabs per day for the heavy and medium duty trucks that come off the production lines in Eindhoven and in Leyland (UK). Grow capacity by 50% In the coming years DAF expects demand for trucks in Europe to grow and aims to expand its market share in the heavy-truck class to 20%. In addition, DAF also wants to expand its success outside Europe. To achieve this ambition for the coming years, DAF is creating a completely new cab paint shop at the DAF Trucks Vlaanderen site. Thanks to this investment, the production capacity of the cab plant increases with some fifty percent. Most modern paint shop of its kind in the world The new paint shop is 144 meters long, 58 meters wide and 26 meters high, and covers three floors. It is the most modern of its kind in the world, also thanks to the partners Eisenmann and Dürr, both leaders in the field of automotive paint shops. Eisenmann delivers the paint-spraying installations (spray booths, ovens and transport systems) and Dürr is responsible for the paint equipment. Amongst others, ultra-modern paint robots will be used with so-called ‘bells’. These rotate at speeds of up to 50,000 revs/min for the highest quality and maximum efficiency with reduced paint and solvent consumption. Latest innovations Next to quality and efficiency, the lowest impact on the environment has been a major focus point in the design of DAF's new cab paint shop. Many innovative solutions have been applied, including a special method to reduce and catch the inevitable ‘overspray’ when painting. Ultra-modern paint robots will very closely follow the contours of the cab, which means less paint is required. Lower energy consumption through new techniques DAF is also investing in the latest technologies to clean the air leaving the spray booths and ovens. The air is condensed so that it contains a relatively large amount of solvents, which burns automatically at a temperature of 700 to 800 degrees without the need for gas to be added and produces enough energy to heat the processing baths. The new solution not only means lower energy consumption. In addition to very limited amount of CO2 emissions, only clean water vapor is emitted. ‘Investment for the future' DAF president, Harrie Schippers: "The new cab paint shop is required for further growth both inside and outside Europe. Obviously, the investment of EUR 100 million in a new paint shop is also good news for the more than 2,000 DAF employees in Westerlo. It illustrates DAF’s confidence in the future of its plant in Belgium.” ‘Example of manufacturing-industry success in Flanders’ "DAF is a classic example of how successful the manufacturing industry in Western Europe and more specifically in Flanders can be," says Flemish minister Philippe Muyters. "That can be done by continuously investing in further increasing the quality and productivity and - just as important - in innovation. As the government, it is our duty to create an excellent climate for this and we are therefore giving this investment our full support. The new DAF cab paint shop, is a high-tech facility with numerous advanced technologies, particularly in the area of environmental protection. I am proud that Europe's most modern paint shop for truck cabs will be in Flanders*." * Flanders (Dutch: Vlaanderen), the Flemish Region of Belgium, is a Dutch-speaking area in the country's north, and one of 3 Belgian states. The national capital, Brussels, considered its own state, lies at the region's southern edge. The state also included the port of Antwerp, the former location of Mack Trucks’ European parts distribution center (PDC). .
-
Scania Press Release / September 1, 2015 Workwear with a vintage feel: that’s the theme for Truck Gear’s autumn collection, which is being launched today. Both flannel and stone-washed materials feature in the range’s jackets and hoodies, with the theme giving a nod to Scania’s history. Scania has launched its new autumn and winter collection, just in time for the beginning of autumn. This year’s vintage-workwear theme draws inspiration from the early 1950s. “The Gear Up T-shirt is based on a picture that I found in an old Scania Vabis catalogue,” explains graphic designer Lage Dahlgren. “So, It’s based to some degree on Scania’s heritage.” However, while the theme is vintage, this doesn’t mean that the whole collection is old fashioned. “We couldn’t make everything vintage, as it would have seemed like we only made old things,” says Dahlgren. “We’re living in the modern world.” Truck Gear is comprised of two distinct lines: Classic and Attitude. The Classic collection features clothes in Scania’s original colours: black, white, blue and red. The choice of colours makes the source of the clothes crystal clear: it’s immediately apparent that they are inspired by Scania. Truck Gear’s other line, Attitude, is more modern and influenced by current fashions. With the clothes based around autumn fashions rather than Scania’s colours, it was extremely important to produce a graphic identity for the prints that showed where the clothes come from. This was Lage Dahlgren’s job. “My task was to ensure that it was clearly visible that the garments come from Scania,” he says. “We’re continually trying to develop new prints. It’s something that we want and that the buyer wants.” Among the garments on offer this autumn are jackets, hoodies and beanies, with materials ranging from flannels to stonewash. Susanna B Hansson, Product Manager for Scania Truck Gear, says, “We have produced a wide range of jackets and worked with different washes, such as stonewash, for example. We’ve also used different types of prints, gum prints and glossy prints.” The clothes are available from Scania’s web shop from today. http://shop.scania.com/en/ .
-
Westport and Fuel Systems Solutions Announce Merger
kscarbel2 replied to kscarbel2's topic in Trucking News
Westport, Fuel Systems Announce Merger Transport Topics / September 1, 2015 Westport Innovations Inc. and Fuel Systems Solutions Inc., suppliers of technology for natural gas-powered trucks, agreed on a merger valued at $351 million to capitalize on opportunities when alternative fuel markets improve. The combination of Westport, based in Vancouver, British Columbia, and New York-based Fuel Systems Solutions is structured as a stock swap for two money-losing companies whose annual revenue could reach $405 million this year. The announcement comes as expected sales of natural gas-powered heavy trucks for on-highway applications are expected to fall about 6% to around 3,300 this year compared with 2014, according to ACT Research, which tied the 2015 activity in the alternative-fuel sector to a sharp drop in diesel prices. That change lengthened the payback period for natural-gas trucks, which account for barely 1% of all heavy truck sales, well below past projections when diesel was at or near record levels. “We expect that the increased scale of products and consolidation of facilities will produce both cost efficiencies and enhanced products, ultimately creating value for all our customers and our shareholders,” Westport CEO David Demers said. In the first half of this year, Westport and Fuel Systems lost a combined $43.7 million. “Westport has a publicly stated goal of reaching break even by the middle of 2016, and the merger would only strengthen the company's ability to meet this goal,” the statement said. Fuel Systems CEO Mariano Costamagna said, “Bringing together these two premier companies in alternative-fuel technology combines our technology expertise and long-standing relationships with global OEMs, our strong shared focus on improving profitability and aligns our corporate cultures, creating an ideal fit.” The transaction includes a new business unit known as Fuel Systems Automotive and Industrial Group. The statement said there are 17 brands marketed in more than 70 countries through the combined businesses. Fuel Systems holders will receive 2.129 Westport shares for each Fuel Systems share owned, worth about $7.54 per share. Westport shareholders will have a 64% stake in the company. A fourth-quarter 2015 completion is expected. The companies estimated $30 million of annual savings by 2018. Demers will head the newly formed company, and Costamagna will serve as a senior advisor while also retiring. -
Today's Trucking / September 1, 2015 Westport Innovations Inc. and Fuel Systems Solutions Inc. on Tuesday jointly announced the companies have entered into a merger agreement to create an alternative fuel vehicle and engine company. Under the terms of the agreement, Westport will acquire all of the outstanding shares of Fuel Systems common stock in a stock-for-stock transaction at a 10 percent premium. Following the closing, existing Westport shareholders will hold approximately 64 percent of the combined company and Fuel Systems shareholders 36 percent of the combined company. The move comes after the two companies combined lost US$43.7 million in the first half of 2015, according to Transport Topics newspaper. Westport has a publicly stated goal of reaching break even by the middle of 2016 and the merger would only strengthen the company's ability to meet this goal, said a news release. The transaction is subject to regulatory approvals as well as approval of both Fuel Systems and Westport's shareholders. To date, shareholders owning 34 percent of Fuel Systems and 15 percent of Westport outstanding shares have each agreed to vote in favor of the merger. The companies' respective boards of directors have unanimously approved this transaction. The companies anticipate closing the transaction in the fourth quarter of 2015. Westport and Fuel Systems will operate as separate companies until that time. Traditionally, Westport has focused the majority of its technological development and commercialization efforts in the heavy-duty and high horsepower arena, while Fuel Systems has experience and focus in the light- and medium-duty products for automotive and industrial applications. Fuel Systems brings long standing relationships with several key global OEMs, including General Motors, Ford, Nissan, Kia, Subaru and Mitsubishi, according to the companies. Westport has key relationships with complementary global OEMs, including Volvo Car Group, Volkswagen, Fiat Chrysler, Tata Motors, GAZ Group, Paccar, Daimler AG, Cummins, Ford and Volvo AB. Upon closing, the combined company will trade on both the Toronto Stock Exchange and Nasdaq under the Westport Fuel Systems name and be headquartered in Vancouver, BC, with a new business unit called Fuel Systems Automotive and Industrial Group. This new unit will represent the combination of Fuel Systems with Westport's operations unit; its automotive division will be headquartered in Cherasco, Italy, and its industrial division will be headquartered in Santa Ana, CA. The transaction will result in a combined equity value of US$351 million based on the closing trading prices for the shares of both companies on Aug. 31 and combined annual revenues ranging from US$380 to US$405 million projected for 2015, according to the companies. "The merger of these two organizations, both rich in technology innovation and with proven track records of manufacturing, production and sales, will provide greater breadth of alternative fuel systems solutions as products and development engineering to OEM partners globally," said David Demers, CEO of Westport. "We expect that the increased scale of products and consolidation of facilities will produce both cost-efficiencies and enhanced products, ultimately creating value for all our customers and our shareholders. This transaction marks a milestone in our strategic plans, whereby Westport will realize increased sales and significant cost efficiency opportunities while continuing to focus on the development, validation and launch of its proprietary Westport HPDI 2.0 and enhanced spark ignition technology." Demers and the rest of the Westport executive team will lead the combined company, while Mariano Costamagna, who is retiring as CEO of Fuel Systems, will serve in a senior advisory position of the company's new business unit with additional titles in the organization to be determined at a later date. Top talent across the combined organization will be evaluated and retained based on the organization's new structure, according to the companies.
-
Transport Topics / September 1, 2015 Element Financial Corp. announced that it has completed the purchase of GE Capital’s fleet-management business in the United States and expects to close the purchase of similar operations in Mexico, Australia and New Zealand on Sept. 30. GE is selling the fleet-management business along with other financial services, including its transportation lending business, to focus on manufacturing and industrial automation. “The fleet-management industry is a primary focus for Element as a platform for delivering strong cash flows for our business, leading-edge products and services for our customers, challenging career opportunities for our employees and attractive returns for our investors,” said Bradley Nullmeyer, president of the Toronto-based finance firm. Element also announced the appointment of Kristi Webb as president and CEO of the company’s fleet-management business. Webb currently serves as president of GE Capital Fleet Services. Jim Halliday also was named executive vice president and will oversee Element’s operations outside the United States and lead the firm’s mergers and acquisitions activities. Related reading - http://www.bigmacktrucks.com/index.php?/topic/40699-ge-sells-fleet-businesses-for-69-billion/?hl=financial
-
Daimler Cutting 1,500 Brazil Truck Jobs as Demand Plunges
kscarbel2 replied to kscarbel2's topic in Trucking News
Daimler Reverses Brazil Truck Job Cuts by Reducing Hours Instead Transport Topics / September 1, 2015 Daimler AG reversed course on the 1,500 job cuts announced last week at its Brazilian truck-making division, saying it will scale back hours by 20% instead as demand shows no sign of improving. The agreement with local unions guarantees jobs until August 2016, and the Brazilian state will compensate employees for about half their lost pay, the Stuttgart, Germany-based company said in a statement Aug. 31. Workers at Daimler’s factory in Sao Bernardo do Campo went on strike in response to the cuts originally proposed, which would have cost about 13% of the company’s Brazilian workforce their jobs. “The agreement shows that we can find fair solutions even in difficult times,” Wolfgang Bernhard, head of Daimler’s commercial vehicle unit, said in the statement. Daimler says demand for trucks and buses in Brazil, South America’s largest economy, plunged 44% in the first half of the year. Brazil’s economic contraction is forecast to continue until at least 2016. Daimler already has shrunk its Brazilian workforce by about 3,000 jobs under a two-year reorganization, primarily through voluntary severance agreements. The company operates two truck- and bus-building plants in Brazil and is setting up a factory to start making passenger cars in the country next year. It employed about 12,000 people in the Latin American country at the end of 2014. -
Your employees in Washington support the sale of U.S. company TRW to Germany’s ZF, on the condition that they sell TRW’s North American and European commercial truck linkage and suspension business to Japan’s THK Co. Ltd. You make the call. American-owned industry?...............Hmm, do we still have any? ----------------------------------------------------------------------------------------------- FTC Approves Sale, ZF-TRW Merger Moves Ahead Transport Topics / August 1, 2015 The United States Federal Trade Commission (FTC) approved an application from ZF Friedrichshafen AG and TRW Automotive Holdings Corp. to sell TRW’s North American and European linkage and suspension business for heavy and light vehicles to the Tokyo-based global machine component manufacturer THK Co. Ltd. The FTC said it required the divestiture as part of its June 2015 final order that settled charges that combining two of the world’s largest automotive parts manufacturers — a merger valued at $12.4 billion — would likely harm competition in the North American market for heavy vehicle tie rods. In May, the commission said ZF and TRW are two of only three North American suppliers of those tie rods. A tie rod is a rigid connector that links a vehicle’s wheels with the steering control mechanism. Because the tie rods are heavy, it's not economical to ship them over long distances, and as a result customers in North America predominantly buy from suppliers that have production facilities in the United States, Canada and Mexico and do not consider suppliers outside of North America as viable options. The complaint alleged that the merger would eliminate direct competition between ZF and TRW and that reducing the number of competitors from three to two would increase the likelihood of coordinated interaction between a combined ZF/TRW and its only other competitor for the tie rods in North America. The parties’ divestiture of assets, the FTC added, also addresses competition concerns raised by the European Commission. The linkage and suspension business to be divested includes five manufacturing plants in Michigan, Canada, the Czech Republic and Germany and a research and development lab in Germany. The FTC vote to approve the divestiture was 4-1, with Commissioner Joshua Wright voting no. Wright wrote, in part, in his dissent, “The market for heavy vehicle tie rods is not particularly vulnerable to coordination. First, while the product might be fairly homogeneous, there are significant switching costs, including the time and cost involved with validation testing of the new supplier’s tie rods.” Wright said Urresko SA, a Mexican parts manufacturer, is a relatively recent entrant in the tie-rod market and has become the largest supplier in the market.
-
Many knew the 1/2 ton J-10 and 3/4 ton J-20, but are unaware there was a one-ton dual rear tire J330 (later designated J3800). .
-
GMC doesn't care if it's Mt. McKinley or Denali The Detroit Free Press / August 31, 2015 As far as GMC is concerned, people are making a molehill out of a mountain. "It had no impact or change on our strategy," says GMC spokeswoman Kelly Wysocki. The brand name for the Denali may get a little more notice from President Barack Obama's plan change the name of North America's tallest peak -- back to its original moniker. Alaska's Mt. McKinley will be known again as Denali, though to auto enthusiasts, it's better known as GMC's sub-brand of luxury vehicles. Nor does she expect having the new "old" mountain name in news to impact sales. General Motors first introduced Denali as an upscale trim level on the 1999 GMC Yukon full-size SUV in 1999, but now is a sub-brand of eight individual models, according to the company. To date, more than 800,000 have been sold. More than half of all GMC Yukons sold currently are Denalis, while nearly half of all Sierra HDs and 30% of Acadias last year were Denalis, too. "The name itself means 'the high one.' For us, it’s the ultimate expression of our professional grade. That’s our motto at GMC," Wysocki said. "It reflects back to Denali. It did have to do with Mt. McKinley." The 20,237-foot mountain's original name stems from the Koyukon Athabaskan language of Alaska natives, but was re-christened Mt. McKinley in 1896 to honor of Ohio Republican William McKinley, who then was running for president and would become the 25th person to hold the office. (He was assassinated by Michigan native Leon Czolgosz in 1901.) "It’s a great thing for the Alaskans that’s it will be named what it should've been named originally," said Kristyn King, a 39-year-old nurse from Eastpointe, who drives a black 2006 GMC Envoy Denali, but didn't know the origin of the sub-brand's name. "I think more people will know now. They'll recognize the name as being the 'higher point.'" Some branding experts think the Detroit automaker should jump on the back-to-Denali designation before all the chatter melts away faster than some snow on Mt. McKinley, er, Denali. "It's the kind of publicity GM really couldn’t pay for, because you have the leader of the free world now talking about the product and talking about the actual name," said Hajj Flemings of Birmingham-based Brand Camp University. "That alone gives more credence and more visibility to GM and they could ride on that. If I were GM, I would look for ways to take that moment and develop some momentum around it. There’s a life cycle to it. In a month from now, we won’t be talking about it. What the brand needs to do is leverage that." The White House announced the name change on Sunday, though U.S. Department of Interior Secretary Sally Jewell signed the secretarial order on Friday. The then-governor of Alaska first made the mountain name-change request in 1975. The name of the national park where the mountain is situated was changed back to Denali in 1980.
-
Jeep Wrangler to stay in Toledo, Cherokee leaving, Wrangler-based pickup coming Automotive News / September 1, 2015 Fiat Chrysler has decided to keep making the Jeep Wrangler in Toledo, Ohio, move production of the Jeep Cherokee to a nearby state and build a Jeep pickup. The news comes after 11 months of uncertainty about the fate of Wrangler production in its historic home. Details about the Wrangler and Cherokee were shared with Toledo plant management this morning in response to inquiries from Automotive News, based on an exclusive interview with CEO Sergio Marchionne on Aug. 21. Automotive News has learned independently that Jeep will make a Wrangler-based pickup in Toledo, a move that will soften the blow of a transferred Cherokee -- Jeep’s best-selling vehicle. Marchionne said that the automaker has “found a solution” to how best expand production of the Wrangler -- in Toledo. Details of the plan will be announced after FCA’s contract talks with the UAW conclude; the contract expires Sept. 14. Separately, Automotive News has confirmed that the plan includes building a long-sought Wrangler-based pickup, likely in 2017 or 2018. That vehicle is under development. In the interview, Marchionne provided some details of the emerging plan: “We found a solution that accommodates a variety of other interests to us because of the way in which we can move some product around,” the CEO said. “It doesn’t take a rocket scientist [to know] that the only way I can move around the Wrangler is to move it into the other Toledo plant.” An FCA spokeswoman said the company would not comment and that the CEO’s quotes stood for themselves. Marchionne has said since January that he preferred to keep Wrangler production in Toledo. FCA’s Toledo Assembly Complex is composed of two plants: one smaller body-on-frame plant that builds the Wrangler and another nearly new unibody plant that builds the Cherokee. The two lines share some common parts staging, but otherwise operate independently. The plan would require the unibody plant, locally known as Toledo North, to be converted to body-on-frame assembly. The redesigned Wrangler would launch there. Loss of the Cherokee is a blow to Toledo, which had sought to keep the vehicle and expand Wrangler production. Through August, the Cherokee is Jeep’s top-selling vehicle in the U.S., averaging 17,611 sales per month. However, that wound may be salved if new vehicles to be added prove as popular. FCA’s plan would ensure that Wrangler production would continue while the plant is retooled for the redesigned 2018 Wrangler. The off-roader is one of the automaker’s most popular and profitable vehicles. Production of the redesigned Wrangler and pickup is planned to reach 350,000 per year, according to suppliers briefed on the plan. The Cherokee would move, likely to Sterling Heights Assembly in Michigan, or possibly Belvidere Assembly in Illinois. Both plants are capable of building the Cherokee with little or no retooling, as the Cherokee shares a platform with the Chrysler 200 built in Sterling Heights and the Dodge Dart built in Belvidere. Converting Toledo Assembly to all body-on-frame construction would solve another problem for FCA, Marchionne hinted. It would allow FCA to retool Warren Assembly in Michigan, where it makes the hot-selling Ram 1500 pickup. Marchionne said that, like the Wrangler, he can’t afford to lose production of the Ram 1500 in order to retool. “We still have Warren that’s not fixed from a manufacturing standpoint,” the CEO said. Marchionne said his two constraints are “that I can’t take down a day of Wranglers, and I can’t take down a day of trucks. So I need to move them around.” A Wrangler-based pickup has been on Jeep enthusiasts’ wish list since the brand showed the Jeep Gladiator concept in 2005. The Gladiator was built on a Ram 1500 frame and shared Wrangler styling. It is unknown whether the Wrangler-based pickup would be Gladiator-sized or smaller, to compete with the redesigned Chevrolet Colorado and GMC Canyon, as well as a potential Ford Ranger pickup. Either way, the Jeep badge and underpinnings should allow it to sell at a premium above those offerings. Unknown for now is what will happen to land the city of Toledo assembled for a possible Jeep expansion. Toledo economic development officials have sought ways to close the cost gap and keep Wrangler in its historic home. For years, Toledo had been quietly buying industrial land adjacent to FCA’s sprawling Toledo Assembly Complex in case expansion was needed. To date, more than 100 acres are available nearby. That land could be made available for suppliers, or it could be saved for future expansion of the current Wrangler line. .
-
Long before freight company Consolidated Freightways decided to form Freightways Manufacturing in 1939 for the in-house design and production of trucks for their own use (badged as Freightliners from 1942), the United States Army became an American truckmaker in 1928. Following the end of World War One in 1919, the U.S. military was demobilized. With numerous states requesting surplus military trucks for road work, Congress sold over 90,000 trucks at bargain prices, leaving the U.S. Army with less than 30,000 trucks by 1921. The U.S. Army was facing a serious problem. The trucks that Congress allowed them to retain were wearing out quickly, and no funding was being authorized to purchase new units. And importantly in the Army’s mind, most of their remaining trucks were essentially 4x2 MILCOTS (military commercial off-the-shelf), trucks that had no tactical cross-country capability. An effort had been made to update World War One Standard B “Liberty” trucks to a more modern “3rd series” specification, but they remained obsolete in design and the conversion rate was too low. In 1920, the U.S. Army Quartermaster Depot at Fort Holabird, Maryland began assembling cross-country vehicles and evaluating their performance. For the most part, components from existing vehicles were used. At Fort Holabird, Army Captain and Chief Engineer Arthur W. Herrington realized that his people could develop and produce purpose-designed high performing cross-country trucks at substantially lower costs than what the automakers were charging the Army for their commercial trucks. Though the automakers were anxious to profit from Army truck sales, few were building a suitable modern truck with all-wheel drive, particularly in the Army’s high volume one to three ton range. In 1928, U.S. Army automotive engineers at Fort Holabird began work on prototypes that would lead to a range of trucks from a 1-1/4 ton 4x4 to a 12 ton 6x6. The design team created five families of vehicles, Group I thru Group V, related to weight class. Incorporating the latest components available at the time, the prototypes were extensively tested and far exceeded the Army’s expectations. The result was the U.S. Army’s new “Standard Fleet”, one of the most impressive groups of purpose-built military tactical trucks ever built. Introduced to the public in 1932, the Standard Fleet was breathtaking. Standing tall with chrome radiator shells and headlamps, they incorporated mechanical components from the industry’s leading suppliers. Featuring Continental, Duesenberg, Franklin, Hercules, Lycoming and Sterling engines, Brown-Lipe, Spicer and Warner transmissions, Wisconsin transfer cases, Rockwell, Timken and Wisconsin axles, Lockheed hydraulic brakes and Westinghouse air brakes, and Ross steering, the Army purchased quality and reliability. Appropriately so, the trucks were badged with "USA" emblems atop the radiator grilles. Tested in Maryland at both Fort Holabird and Aberdeen Proving Ground, the trucks were universally praised by all who used them. Heat-treated frames, completely enclosed cabs, abundant power, high speed and modern drivetrains made the Standard Fleet far superior to the commercial models. A total of 60 units were built, at a cost ranging from two-thirds to four-fifths of the costs of a commercial truck, if indeed there was an equivalent available. Fire trucks and armored cars were also built on Standard Fleet chassis. The U.S. automakers were alarmed by the U.S. Army Quartermaster Corps’ efforts to build trucks in-house, and immediately lobbied Congress to put an end to further development and production. The power and money of the U.S. automakers prevailed, and Congress forced the Army to largely abandon truck production (with the exception of fire trucks based on 3rd series Standard B truck chassis). The most notable result stemming from the Standard Fleet undertaking was that the U.S. automakers finally began offering a wide range of all-wheel drive trucks to meet the Army’s needs. While FWD and Oshkosh had offered rugged all-wheel drive trucks, they were too expensive to purchase in large quantities. All-wheel drive heavy trucks were made available by Biederman, Clydesdale, Corbitt, Hug and Indiana in 1933, followed later by Chevrolet, Diamond T, Dodge, Federal, Ford, GMC, International, Mack Trucks, Reo and Studebaker. A newcomer in the truck business was Marmon-Herrington, created by combining the Indianapolis-based Marmon with Arthur W. Herrington’s truck designing expertise. Aggressive and innovative, Marmon-Herrington produced thousands of light, medium and heavy trucks for the U.S. Army. To no one’s surprise, the final Standard Fleet models bore a strong resemblance to the 3 to 7-1/2 ton trucks later built by Marmon-Herrington. Further reading - http://forums.aths.org/PrintTopic101639.aspx http://www.amazon.com/Military-Wheeled-Vehicles-Crestline-Automotive/dp/0912612215/ref=tmm_hrd_swatch_0?_encoding=UTF8&qid=&sr= .
-
I agree. Let's recap. In 1867, U.S. Secretary of State William H. Seward signed a treaty with Russia for the purchase of Alaska for $7.2 million. The purchase was dubbed "Seward's Folly" by skeptics (that was a lot of money back then), UNTIL gold was discovered in 1896. We bought the location, which gave us the right to issue new names. But I lean towards using the native name (Denali), which was used long before us, and likely will be long after we're gone. America has a long history of using native American names for land and water. The state's name, Alaska, is itself an Aleut name (https://en.wikipedia.org/wiki/Aleut_language). But there are repercussions.........Obama will have to spend millions of taxpayer dollars annually to use the Denali name, a registered trademark of General Motors for its GMC brand.
-
-
Scania Press Release / August 31, 2015 The latest addition to Scania’s engine range for marine applications incorporates proven XPI (extra-high pressure injection) common rail fuel injection technology, allowing for unrivaled fuel efficiency. The new V8 engine is also the most powerful engine in the range, boasting up to 1,150 hp. Scania’s new, more powerful marine engine range now features the company’s 2500 bar XPI fuel injection system, long used in Scania’s engines for trucks and industrial applications. Boosting power Svante Lejon is a senior technical adviser within Scania’s Research and Development division and his responsibilities include developing technical performance concepts for industrial and marine engines. “The XPI system introduces more fuel into the cylinders in a shorter time, providing more power,” he says. “However, this also places higher demands on both the filtration system and the cleanliness of the fuel, as the system is more sensitive to particles.” Lejon says the challenges involved have meant that Scania has not previously used common-rail technology in its marine solutions. “The fuel quality required for marine applications is different to that for trucks and industrial applications,” he says. “However, filter technology has now reached a level that allows for performance and up-time to be maintained at the high level that Scania expects.” Smaller footprint The V-8 version of Scania’s marine engine is based on the company’s tried-and-tested 16.4-litre V-8 for trucks. The engine is the most powerful in the marine range and is capable of producing up to 1,150 horsepower for use in working boats. While this represents an increase in power on the previous generation, the physical size of the complete installation has actually decreased making it easy to upgrade an existing V-8 installation to the new engine platform. Scania’s modular system in combination with the company’s Engine Management System (EMS) allows for the same platform to be used in different applications. An engine solution can thus be tailored for completely different operating profiles without compromise. “It’s thanks in part to Scania’s Engine Management System that we’re able to optimise our engine platform for such a wide range of areas,” says Lejon. “Otherwise, we would be forced to make an engine that wasn’t as good for each area.” Related photographs - http://newsroom.scania.com/en-group/2015/08/31/scanias-proven-fuel-injection-technology-arrives-in-the-marine-sector-2/
-
MAN Press Release / August 31, 2015 Completely new, redesigned engineOutstanding in its output classExtended range of applications for yachts of over 100 feetFrom 8 to 13 September 2015, MAN Engines will showcase their most powerful high-speed four-stroke diesel engine to date at the Yachting Festival in Cannes. The 24.2-liter twelve-cylinder model V12-1900 engine is rated at 1,900 horsepower and was specifically designed for use in luxury yachts of over 100 feet. The complete redesign of the injection, power train and cooling system has allowed MAN to achieve an increase in output of 100 horsepower over the current V12-1800. With installation dimensions of 2,139 mm x 1,153 mm x 1,265 mm (length x width x height), the V12-1900 comes in the MAN Engines customary compact size. At 2,365 kg (dry weight) and with an output of 1,900 horsepower, MAN Truck & Bus’s most powerful series engine has an outstanding power to weight ratio with a high power density and compact installation dimensions, giving boat builders significant room to maneuver in terms of design. A maximum torque of 6,220 Nm, at 1,200 to 2,100 rpm, makes the V12-1900 the most powerful engine to date in the MAN Engines portfolio. The high-performance unit generates its power from 24.2 litre displacement ensuring high power development even at the lower end and right across a broad speed range. The even and constant acceleration delivers a pleasant and comfortable ride right through to the upper end of the speed range. The special design ensures very smooth running and thus provides a relaxed ride, adding to the comfort on board. “Our V12-1900 sets the benchmark in this output class in terms of dry weight, specific output and power to weight ratio” proudly commented Claus Benzler, head of Marine at MAN Engines. At its optimum, the specific fuel consumption of the V12-1900 is at the same low level of 190 g/kWh as its heavier sister model, the V12-1800. The V12-1900 is MAN's response to the issue of increased performance for both planning and displacement hulls. At the same time and as a result of the increase in horsepower, the Bavarian-based engine manufacturer now has access to further types of ship with higher output requirements. MAN thus provides boatyards with a perfectly balanced range for all output requirements in leisure boating. The product range offers in-line 6-cylinder as well as V8 and V12 engines and covers the full range of performance from 537 to 1,397 kW (730 to 1,900 hp). All engines are also available in compliance with the strict EPA Tier 3 emissions standard. For those customers seeking something extra, optional gilded or chrome-plated cylinder head covers as well as a design cover are available. The engine can be ordered and delivered from now on. The V12-1900 can be seen from 8 to 13 September 2015 at the Yachting Festival in Cannes on stand Jetee 138. Related photograph - http://www.corporate.man.eu/en/press-and-media/presscenter/King-of-the-Lions_-MAN-12-cylinder-yacht-engine-now-with-1_397-kW-_1_900-hp_--220096.html
-
Fleet Owner / August 31, 2015 Truck and engine manufacturer Navistar said it plans to begin offering over-the-air (OTA) re-programming of engine control modules (ECMs) for its N9, N10 and N13 proprietary engines in early 2016 – a service that’s been the longtime goal of many OEMs within the commercial vehicle industry. “Over-the-air reprogramming will revolutionize the way our customers’ trucks are serviced and maintained,” noted Bill Kozek, president of Navistar Truck and Parts, in a statement. “This … is paving the way for future advancements that will drive improvements in vehicle uptime and real-world, bottom-line results for our customers.” Dr. Steve Charlton, the now-retired VP and chief technology officer for the engine business at Cummins, noted two years ago that such “on the fly” reprogramming should at some point become no more difficult than downloading digital music files. “There’s already a broadcast of public information from today’s engine control modules of public data such as throttle and torque,” he explained during a presentation at the Mid American Trucking Show back in 2013. “But then there’s private data we can extract that enriches that public data and turns it into information.” That detailed information can then be crafted into precise engine calibrations truck owners can tap into to improve whatever operating characteristics of their vehicles they desire, Charlton said at the time, be it for better fuel economy or better performance. “We expect users will be able to download and apply calibrations just like the way you download and use songs from iTunes,” he noted. “We see this as a huge enabler going forward." Navistar expects similar benefits from its “OTA” offering, which will allow customers to reprogram their ECMs via a secure Wi-Fi connection. Mike Cerilli, GM for Navistar’s connected vehicle business division, noted that Navistar has wrapped up its initial OTA testing and next is planning customer fleet tests this fall, with the system expected to be available for 2017 model International-branded trucks equipped with N9, N10, and N13 engines early next year. “OTA lays the groundwork for a pipeline of connected vehicle services such as partner engine and component calibration updates, body control module updates and future cellular capabilities,” Cerilli said in a statement. “These and future advancements will provide improved customer uptime, fuel efficiency and other benefits that will drive added value for customers.” Cummins OTA video - http://fleetowner.com/technology/navistar-plans-offer-over-air-engine-updates
-
Allison Cites Fuel Savings Using TC10 Transmission
kscarbel2 replied to kscarbel2's topic in Trucking News
Related reading: http://www.amazon.com/Vees-For-Victory-Aircraft-1929-1948/dp/0764305611 http://www.aviation-history.com/engines/allison.htm -
Transport Topics / August 31, 2015 Allison Transmission, which makes the only fully automatic transmission for heavy-duty trucks in the United States, said that fleets using its TC10 automatic gearbox report a 5% improvement in fuel economy over manual transmissions or automated manuals. Chairman and CEO Larry Dewey said during media day at headquarters here that the fully automatic transmission shifts more efficiently than either manual or automated manual gearboxes. Dewey, also Allison’s president, said that fuel is wasted when the power is interrupted during gear shifts with manuals or AMTs. “With the TC10, power goes to the wheels continuously,” he said. This increases fuel efficiency, particularly when there is more start-and-stop driving. When a manual or AMT shifts gears, the engine slows and has to come back up to driving speed. Dewey also said that automatic transmissions increase productivity and make driver recruitment and retention easier. Trucks with automatic transmissions accelerate more quickly from a stationary position, so they can move more quickly in urban traffic and merge into traffic more quickly. Dewey said that means that, over the course of a day, trucks arrive at their destinations sooner, so productivity goes up. Automatic transmissions help fleets expand the pool of drivers that can be hired by making driving easier. “The training period is significantly reduced,” Dewey said. “Drivers have to learn how to handle the big truck, but they don’t have to learn how to shift.” Allison, which celebrates its centennial this year, began production of its TC10 automatic in 2013. The company said its units are being used by about 140 fleets but would not disclose how many it has sold. Revenue totaled $2.127 billion in 2014. Transmissions used in over-the-road tractors account for 7% to 10% of Allison’s entire business, Dewey said. The company also makes transmissions that are used in buses, refuse trucks, delivery trucks, motor homes and a variety of vehicles for applications including agriculture and mining. The company was founded by James Allison, who also was one of the founders of Indianapolis Motor Speedway. In 1915, he started the Indianapolis Speedway Team Co., and four years later his team won the Indy 500. Today, Allison Transmission is the world’s largest manufacturer of fully automatic transmissions for medium- and heavy-duty commercial vehicles. In addition to its main plant in Indianapolis, Allison has manufacturing facilities in Hungary and India and regional headquarters in the Netherlands, China and Brazil. Besides truck and coach transmissions, the company has made aircraft engines, automatic transmissions for military tanks and hybrid propulsion systems.
-
Truck News / August 31, 2015 Every time I have the opportunity to drive Kenworth’s T880, the truck has evolved in some way, usually with the addition of new features and options that add to its versatility. The T880 was launched in 2013 as an alternative to the T800, a truck that generated an extraordinary amount of fanfare over its 25-plus-year run as the workhorse in the Kenworth stable. The truck maker continues to offer both models, but has already converted over most of its customers, with the T880 now representing 65-70% of the T800/T880 combined build. On a recent visit to Kenworth’s home base in Kirkland, Wash., I had the chance to drive a T880 up to the Paccar Technical Center in Mount Vernon, Wash., to see what it is about the T880 that’s winning over customers. The truck I drove had the newest available sleeper cab – a 76-inch mid-roof sleeper that will go into production in September on both the T680 and the T880. Ideal for tanker, flatdeck and lowboy applications, the new sleeper is 22 inches shorter and about 100 lbs lighter than a high-roof sleeper cab. Inside, it is both functional and roomy. If you don’t require an upper bunk, Kenworth provides ample storage along the back wall. Popular features such as the swivel passenger seat are retained to offer a highly livable space. There’s still plenty of headroom, allowing a driver up to 6’8” to stand upright. The longer sleeper cab offers more opportunities for customization. Beacon lights can be placed in several positions on the roof and you can also install roof-mounted horns. A side-of-cab exhaust option is available for those wanting to chrome up the truck. I was pulling a traditional van trailer loaded up to nearly 80,000 lbs, but you’d normally want to hook this truck up to a lower profile trailer for better fuel economy. My T880 had the Paccar MX-13 engine under the hood rated at its maximum 500 hp and 1,850 lb.-ft. or torque. It was sufficiently powered for any of the hills encountered on the drive to Mount Vernon and I was comfortably and safely able to pull out and pass slower trucks that were struggling on the hills. The transmission was Eaton’s MXP (Multipurpose Extreme Performance) UltraShift Plus, designed for vocational applications. The T880 has a more modern exterior design than the T800, but it has retained a bold, heavy-duty appearance. It is said at Kenworth that ‘Every great truck starts with a great grille.’ The T880’s wire aluminum mesh grille with stainless steel surround is distinctive and durable. It has an integrated bug screen and provides ample protection for the cooling module. A new box bumper – both chrome and painted – will soon be available, which is a popular option in Canada, according to Kyle Kimball, vocational marketing manager with Kenworth. Quarter-inch and 3/8” inch versions will be offered. The headlights on the T880 were built for vocational environments. The halogen bulbs are easy to replace without tools and can be found at pretty much any automotive retailer, including department stores. A thick polycarbonate lens provides extra protection from rock chips. The forward lighting system was designed to give good performance down field, but also produces 50% better lighting at the immediate front of the truck to improve safety while working at dark job sites. The front end was designed with reparability in mind. The five-piece Metton hood can be easily repaired and the fender can be removed by pulling 15 bolts in about an hour. Exterior air cleaners aren’t available on the T880, because its wider 2.1-metre cab won’t allow it. However, you can spec’ optional pre-cleaners that reject dirt and debris out the intake before they enter the air cleaner, extending air cleaner life in dusty environments. The hood can be lifted with just 35 lbs of effort, Kimball said, and it opens to 85 degrees for easy access. All the under-hood items that must be examined as part of the pre-trip inspection have been clustered together on the driver’s side to simplify inspections. Inside the cab, there’s a pre-trip inspection switch that cycles through all the lights, allowing the driver to check them with one lap around the truck. Inside, the T880 offers excellent forward visibility through a one-piece windshield that’s 50% larger than on the T8. Kimball explained Kenworth also lowered the crown of the hood by three inches, which can provide up to five feet of extra visibility immediately in front of the truck. Mirrors on the T880 are cowl-mounted, a key differentiator from sister company Peterbilt’s answer to this truck, the Model 567, which has door-mounted mirrors. Kimball said Kenworth prefers cowl-mounted mirrors because they’re more structurally stable, noting they can support 350 lbs without any risk of flexing the door or straining its hinges. The mirrors also stay in position better when the doors are frequently opened and closed, he added. Kenworth gives drivers options for getting in and out of the truck, with two handles on the inside of the door and optional handles available on the exhaust or side of the cab. They’ve even reinforced the map pocket to support 350 lbs, knowing some drivers grab it when climbing into or out of the cab. A new feature in the T880 is an electric-over-air system, in which all switches on the dash are electric, their communications funneled through the cab electronic control unit (ECU). “By going through the cab ECU, it looks at what the rest of the truck is doing and will allow or not allow switches to happen,” Kimball explained. For example, it won’t allow the operator to raise a dump body when the truck’s travelling down the highway. When the T880 hit the market, Kenworth realized it would take time to add all the options currently available on the T800, but in just two years, it now has about 95% of T8 options available, Kimball said. Some highly specialized options are all that’s currently lacking on the T880 and eventually, those will be available as well. There are still some T8 faithful who are reticent to make the switch to the more modern T880 but Kimball said once drivers get behind the wheel, they quickly see the benefits. There are no imminent plans to discontinue the T800. “Right now, the plan is to continue (offering both models),” Kimball said. “We’re definitely trying to convert people over to the T880 because of the features, the extra cab room and cab functionality, but we’re still offering the T800. We have a good success rate of converting people over once they get a chance to drive it.” I have nothing disparaging to say about the T800, but in terms of drivability and amenities, the T880 is an upgrade. Interestingly, one of the T880’s greatest attributes, its versatility, is landing the truck in some unexpected applications and even eating into the on-highway model T680’s turf. The vocational truck has found a following among on-highway customers who prefer the T880’s heavier-duty look. “Some lighter-weight stuff, 12,000- and 13,000-lb front axles are a good portion of T880 sales,” Kimball said. “A lot of people are still spec’ing it for on-highway applications. They want that heavy-duty truck. It still fits well, but to get the most bang for your buck, the T680 is the aerodynamic leader, so we’re trying to push people towards the T680 for on-highway. But a lot of customers want that heavy-duty look and feel to it as well.” Of course, for Kimball, having some unexpected demand from outside the T880’s anticipated market segments is a problem I’m sure he can deal with. Related photographs - http://www.trucknews.com/equipment/driving-kenworths-ever-evolving-t880/1003067485/
BigMackTrucks.com
BigMackTrucks.com is a support forum for antique, classic and modern Mack Trucks! The forum is owned and maintained by Watt's Truck Center, Inc. an independent, full service Mack dealer. The forums are not affiliated with Mack Trucks, Inc.
Our Vendors and Advertisers
Thank you for your support!