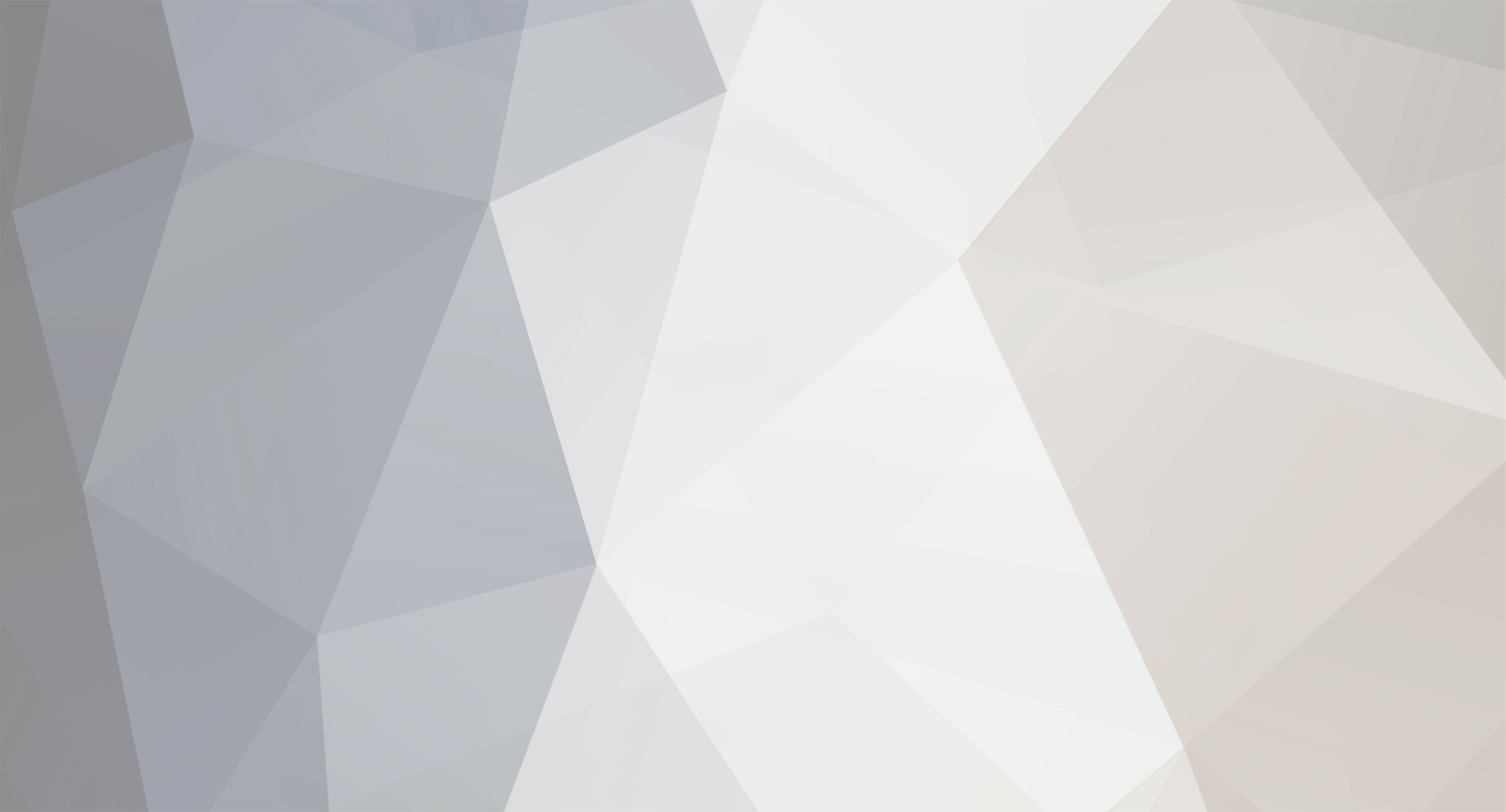
kscarbel2
Moderator-
Posts
18,734 -
Joined
-
Days Won
114
Content Type
Profiles
Forums
Gallery
Events
Blogs
BMT Wiki
Collections
Store
Everything posted by kscarbel2
-
Father stabs three sons to death Reuters / September 9, 2015 A father repeatedly stabbed his three young sons to death with a knife in the back seat of their car outside a South Los Angeles elementary school Wednesday before turning the blade on himself, police say. The father, in his 30s, was found in his car bleeding from stab wounds to the chest, his dead sons in the back and a knife in the passenger seat. The boys, ages 8 to 12, were pronounced dead at the scene. The father is the only suspect in the killings, police said. He was taken to a hospital in critical condition and will be arrested if he survives his wounds, Los Angeles Police Officer Matthew Ludwig said. "These are horrific incidents," police Chief Charlie Beck said. "These are incidents that have scarred not only a community but the first responders that have to handle them. It is a sad day in LA." John Sorrentino, whose furniture store is next to the crime scene, said he was the one who first spotted the bloody scene and called 911. "I saw this man behind the steering wheel covered in blood," he said. "I got a little bit closer, and I saw a young child in the back seat and his eyes were half open and he was covered in blood. Sorrentino said he then saw another motionless boy bent over a seat, and in the back, a leg of the third boy lying upright. That's when he ran inside his store and called 911. Beck said the boys' mother is deceased and that their stepmother was safe and being interviewed by detectives. It was unclear whether the boys lived with their father. The deaths come as homicides are on the rise in Los Angeles. In August, 39 killings drove a year-to-date uptick in murders in the nation's second-largest city. The 39 killings in August are compared with 22 the previous month and 19 last August. .
-
Four former EPA administrators appointed by Republican presidents who testified in favor of the agency’s proposed power plant regulations at a Senate subcommittee hearing last week did not respond when asked if they agreed with President Obama that global warming was accelerating. Sen. Jeff Sessions (R-AL) asked former EPA heads William Ruckelshaus, Christine Todd Whitman, William Reilly and Lee Thomas whether they agreed with Obama’s previous statements that the Earth is warming faster than previous predictions. “The president, on Nov. 14, 2012, said, ‘The temperature around the globe is increasing faster than was predicted even 10 years ago’,” Sessions said at a hearing of the Senate Environment and Public Works Subcommittee’s “Climate Change: The Need to Act Now” hearing held on Capitol Hill last Wednesday. “And then on May 29th last year, he said, ‘We also know that the climate is warming faster than anybody anticipated five or ten years ago’,” Sessions said. “So I would ask each of our former administrators if any of you agree that that’s an accurate statement on the climate. So if you do, raise your hand.” None of the former EPA heads did so. “Well, thank you,” Sessions said. “The record will reflect no one raised their hands.” Video - http://www.cnsnews.com/news/article/barbara-hollingsworth/former-epa-heads-mum-when-asked-if-global-warming-accelerating
-
Administrator Start End Gina McCarthy 07/19/13 present Bob Perciasepe (Acting) 02/15/13 07/18/13 Lisa P. Jackson 01/26/09 02/14/13 Stephen L. Johnson 05/02/05 01/25/09 Stephen L. Johnson (Acting) 01/26/05 05/01/05 Michael O. Leavitt 11/06/03 01/25/05 Marianne L. Horinko (Acting) 07/12/03 11/05/03 Linda J. Fisher (Acting) 06/28/03 07/11/03 Christine Todd Whitman 01/31/01 06/27/03 W. Michael McCabe (Acting) 01/20/01 01/30/01 Carol M. Browner 01/22/93 01/19/01 William K. Reilly 02/06/89 01/20/93 John Moore (Acting) 01/21/89 02/05/89 Lee M. Thomas 02/08/85 01/20/89 Lee M. Thomas (Acting) 01/04/85 02/07/85 William D. Ruckelshaus 05/18/83 01/04/85 Lee Verstandig (Acting) 03/10/83 05/17/83 Anne M. Gorsuch [burford] 05/20/81 03/09/83 Walter Barber, Jr. (Acting) 01/26/81 05/19/81 Steve Jellinek (Acting) 01/21/81 01/25/81 Douglas M. Costle 03/07/77 01/20/81 John Quarles, Jr. (Acting) 01/21/77 03/06/77 Russell E. Train 09/13/73 01/20/77 Robert Fri (Acting) 04/30/73 09/12/73 William D. Ruckelshaus 12/04/70 04/30/73 If one takes the time to review the appointed heads of the EPA over the years, and management of this agency, any ordinarily prudent individual should be shocked. The previous head for example, Lisa Jackson, was just was unqualified as McCarthy. As in any professionally run business, becoming head of the EPA should be based on qualifications and experience. However, it is in fact a political circus...........and the negative results clearly reflect that. The rapid tightening of commercial truck exhaust emissions regulations over the 2000 thru 2010 period was reckless and irresponsible, forcing the truck manufacturing industry to produce vehicles so unreliable that they were little more than advanced science experiments in mass production. During this time frame, truck operators of all types and size lost millions of dollars because the EPA demanded tighter emissions before viable, reliable technology existed for its smooth implementation. Another point, if the EPA had qualified leadership, it would have moved for the United States to adopt the Euro emissions regulations from year 2000, putting the US on the same page as the rest of the world, and saving vehicle manufacturers millions of dollars by no longer forcing them to design and produce two separate engine line-ups.
-
The removal of the incompetent and ignorant EPA head Gina McCarthy would be in the best interest of America............and therefore I assume it won't happen.
-
Fleet Owner / September 9, 2015 When master photographer Roger Snider gets together with Carl Carstens of Rockwood Products to put together their annual show truck calendar dubbed Chrome & Elegance, the results are often stunning – and their impending 2016 edition looks to be just as eye-popping as their previous three efforts. Snider gave Fleet Owner a behind-the-scenes look at some of the rigs and location shoots displayed in the 2016 Chrome & Elegance calendar, the theme of which is "California Dreaming." Photo gallery - http://fleetowner.com/equipment/chrome-elegance-2016#slide-0-field_images-170811
-
- 1
-
-
Today's Trucking / September 9, 2015 The linking of tractor and trailer doesn't get a lot of attention, and maybe that's no surprise. It's a simple operation, after all, and the mechanical bits are themselves something less than complex. Fifth-wheel makers have refined the technology over the years and development is more or less continuous, but most truck buyers don't think too much about it. They don't really have to. And I'd guess they think not at all about the other key part of this equation: the kingpin. What's to improve? Well, if you ask a small but successful company in Quebec, you'll find out that there really is a better mousetrap. Rotavan is that company and its product is the new RG-3 swiveling coupling system, which replaces a standard kingpin affair. As the name suggests, this is a third-generation product, with different configurations for specific applications. And how does it work? Its key feature is a rotating swivel base or turntable, unique in the trucking world, which greatly reduces friction between parts, thereby improving control of the vehicle. It sports a patented, internally lubricated system that allows for smooth rotation. By all accounts drivers love it for the way it improves handling and delivers both more flexibility and better control, not to mention a new precision. Company chief Jacques Marquis, one of the nicest guys you'll meet anywhere, says the swiveling system provides "unmatched maneuverabilty" and "unprecedented driving control". And that translates into improved safety, he adds, because friction between a conventional fifth-wheel-and-kingpin setup can cause a loss of control, skids, and accidents. The Rotavan RG-3 swivel-based system eliminates friction almost entirely and can prevent jackknifing. It also eliminates lateral wear on steer tires, says Marquis, and extends the life of coupling and steering parts. Steer-tire expenses can be cut in half over a 6-year period, he says. Video - http://rotavan.com/en/produits/fonctionnement.html
-
Fleet Owner / September 9, 2015 John Hart knows hotels. A former Marriot executive, Hart left the hotel business in 2012 to develop an online hotel booking platform called StaySmarter. And over the past year, he has taken his expertise in hotels to the trucking community. StaySmarter for Truckers allows truck drivers to find hotels that are pet friendly and have parking for their trucks, to search all hotel brands, and take advantage of special rates, such as AAA and AARP. When Hart created StaySmarter, his initial focus was predominantly on frequent travelers, not necessarily truckers, he told Fleet Owner. But over time, he said he began to recognize truckers as frequent travelers and realized they needed a designated hotel-booking tool. “We thought, ‘Wow, this is a big market,’” Hart explained. “And when we looked at existing services out there for truckers, we thought, ‘This is embarrassing.’ We felt truckers were ignored. Clearly they’re not getting the attention they need for the role they play in the economy.” According to StaySmarter’s data, about 10,000 hotels in the U.S. and Canada have trucker-friendly parking. Hart mentioned that his platform for truckers shows all hotel chains that accommodate drivers and their trucks. He also explained that rates, available discounts, and any other information truck drivers would need to know about booking a room are all on the one interface. The key benefits for truckers, according to Hart, are: Cost. Hart says the StaySmarter platform is free and ad free, offers the same prices as the hotels, allows truckers to pay after their stay, and earn points every hotel rewards program – something he says no one else offers. Efficiency. Hart points out the app works on every device (PC, laptop, tablet, smartphone) on every operating system (Windows, Android, Apple). Booking is done directly through the site, and allows user to comparison shop, he added. It’s ‘smarter.’ Hart noted that users can get a hotel confirmation number, cancel with one click (no phone call or email required), and call the hotel or StaySmarter directly if needed. “We’re hotel experts, not truck experts,” Hart told Fleet Owner. “We were surprised by how bad the experience was for truckers to book hotels. We looked at all of the websites and tools. Many don’t provide access to hotel data, and if they do, it’s simply location data. When booking services exist, they are slow, cost money, offer questionable deals, and lack features, data, and even clear user interfaces. It is a mess. Yet truckers are an important segment of travelers. They need to book hotel rooms fast.” For Hart, the overall impetus behind StaySmarter is that he believes companies like Priceline and Expedia are hurting hotels and the consumer. And, as a hotel expert, he thought he could do better. In the future, Hart said, the folks at StaySmarter expect to add data sets for truck stops and rest stops to the trucking platform. As developments to the platform pick up, Hart encourages feedback from the industry. The company, he added, is also in the process of setting up incentives for fleet owners and independent owner-operators.
-
"People should and do trust me" - Hillary Clinton
kscarbel2 replied to kscarbel2's topic in Odds and Ends
Update: It turns out that Hillary isn't sorry after all for throwing U.S. State Dept. policy to the curb and keeping classfied information on her personal server at home. She's only sorry for creating "confusion". Yesterday she elaborated "I am sorry for all the confusion that has ensued". http://abcnews.go.com/Politics/video/donald-trump-hillary-clinton-emails-33641286 -
CAT Trucks Shine in Western Australia’s Southwest
kscarbel2 replied to kscarbel2's topic in Trucking News
The Australian truck operating requirement is unforgiving, nothing at all like the US. And furthermore, we're talking Australian long-haul versus US market vocational. If you've never been, you owe it to yourself to get down to Oz and NZ for a time. http://www.cattrucks.com.au/ http://www.cat.com/en_US/products/new/by-industry/on-highway-truck.html -
CAT Trucks Shine in Western Australia’s Southwest
kscarbel2 replied to kscarbel2's topic in Trucking News
Please realize that the CAT long-haul trucks product sold in Australia are night and day different from the US market CAT vocational trucks. -
With the passing of both time and people, our trucking history can very easily disappear. Like you, I have a natural passion for America's truck industry. It's an indescribable pleasure for me to revive some of the history, before it's lost, and present it once more in the present. I'm confident there are younger generations of people with interest, and older generations who take pleasure in refreshing their memory.
-
MAN Press Release / September 8, 2015 MAN Truck & Bus has begun the construction of a € 80 million (US$89.3 million) new cab paint shop at its main truck assembly location in Munich, Germany. A new modern and efficient base coat line will be built adjacent to the current paint building with a total floor area of approximately 18,000 m² over five main levels. The new base coat line will begin operations at the end of 2017. The investment is part of the future programme of MAN Truck & Bus AG. The highly efficient painting process in the new facility consists of pretreatment, cathodic dip coating by rotation, seam sealing and filler application. The rotation process in the dip painting enables a significant reduction in the use of consumables and chemicals through the application of the latest systems engineering. In addition, very effective cleaning means that the level of particulates in the exhaust air is reduced by 90 percent and water consumption is cut by 80 percent. Furthermore, the use of innovative and resource-saving technologies enables MAN to reduce emissions in the processes concerned by half, to lower paint use by 15 percent and to cut energy consumption by 25 percent. “The investment in the new paint shop represents a key milestone for the Munich site. The new facility will allow us to significantly increase efficiency in the cab paint shop and also achieve further improvements in paint quality. The new systems are equipped with the latest environmental technologies and are thus another significant contribution towards our strategic objective of a “Green Factory”. Overall, the new system allows us to create an essential and sustainable basis from which we can create innovative processes and attain low environmental impact and maximum efficiency for both current and future premium truck generations”, Dr. Carsten Intra, Executive Board Member for Production & Logistics at MAN Truck & Bus AG pointed out. Saki Stimoniaris, Chairman of the works council, also highlighted the importance for the future of the Munich site: “The investment in the paint shop plays an integral part in our securing of both the site and employment. This means we are securing jobs in our cab production of which the paint shop is a part, and much more besides.” .
-
Scania Press Release / September 8, 2015 Alone at night, a Scania distribution trucks makes deliveries to downtown Stockholm restaurants and hotels. In a pilot project, the City of Stockholm wishes to determine the advantages of night time deliveries, avoiding peak hour traffic, queues and delays. The project, which is part financed by VINNOVA, Sweden’s innovation agency, will examine the feasibility of lifting the ban on inner-city truck traffic presently in force between 22.00 and 06.00. The project will particularly focus on noise levels and the working environment for drivers.
-
Al Qaeda-linked ISIS executes three truckers (ISIS produced this propaganda fear video in 2013) This video shows the execution style murder of three Syrian truck drivers who did nothing more than belong to a minority faith the local Al Qaeda affiliate does not like. In the video, a small band of Islamist radicals with the Al Qaeda-linked ISIS (Islamic State in Iraq and Syria) group is seen waving the tractor trailers off the side of an Iraqi road and then proceeds to interrogate the unsuspecting drivers about their prayer habits, trying to discover if they are Sunnis or members of the Alawite minority in Syria. The men first claim to be Sunni Muslims, and the gunman asks them various questions relating to Sunni religious practice. They are unable to answer the questions and in the end admit that they are Alawites. Having failed the Sunni jihadis’ questioning, the truck drivers are seated in a line in the median of the road and shot in the back of their heads firing squad style by the self-appointed law enforcers, jury, judge and executioner. The three truck drivers are shot in the back repeatedly, as chants of Allahu Akbar (Allah is the greatest) are audible in the background. More than a dozen shots are fired into the men’s bodies, even after it appears they are already dead. The incident likely took place near Ramadi in Iraq’s Anbar Province. The perpetrators wear military-type uniforms and black scarves over their heads, holding machine guns, while at least one is fully masked with a large ammunition belt hanging around his neck. The incident may have been pre-planned for public relations purposes, as the scene shown in the YouTube video was filmed from two separate angles. ISIS has emerged as a scourge in rebel controlled areas, carrying out kidnappings and sectarian killings. While Christians are at risk daily in countries like Egypt, Syria and Iraq, the video outlines the dangers facing other other religious minorities in the crosshairs of Sunni radicals, including practitioners of the Alawite faith, an offshoot of Shi’ite Islam of which Syrian President Bashar Assad is a member and protector. The jihadi uses the insulting term ‘nusayri’ to describe the Alawites. The jihadis are referred to as the ‘lions of Anbar’ and the incident appears to be taking place in Anbar province, Iraq, probably close to the border with Syria. The men are referred to as ‘nusayri (alawi) spies’ in the title.. At the end of the video, one of the ISIS members is seen throwing a burning object at one of the trucks, which begins to burn and smoke. Video - http://www.dailymail.co.uk/video/news/video-1099961/Abu-Wahib-sentences-three-truck-drivers-death-2013.html
-
AL-Monitor / September 4, 2015 Syrian truck drivers are the only ones who maintain good relations with commanders of the regime, the Free Syrian Army (FSA), Islamic State (IS) and Democratic Union Party (PYD) forces, all while constantly monitoring the clashes. In the four-year Syrian civil war, 250,000 people have been killed and 4 million of them have become refugees in neighboring countries. Millions of them are struggling to survive in a country divided four ways between the Bashar al-Assad regime, the opposition, ISIS and the PYD. Wherever they live, these Syrians meet their daily needs of flour, medicine, baby food, fuel and clothing through merchants and truck drivers who are the only ones who can cross the internal borders. It is lethal trade for the drivers. They navigate essential, fine points of survival: Without distinction, they maintain good relations with the entire gamut of factions and religiously keep track of daily clashes and events on the ground. Their biggest advantage is the constant need of all fighting parties. This is their story. Salim is one of millions of Syrians who is a victim of civil war. His family lives in Aleppo. He doesn’t have a permanent living place because he makes his living trucking through a country whose economy has collapsed. Like many of his colleagues, he has faced death many times. Salim’s story is the story of how people remaining in Syria obtain their survival needs like food, fuel and other basics and the trade relations between enemy groups. Syrians who have decided to stay obtain their flour, medicine and fuel thanks to truckers like Salim who can enter any zone, no matter who controls it. Syrian truckers are probably the only group who can cross the internal borders of different groups. Truckers are not very talkative. They don’t want to attract attention. Only Salim and a businessman who goes by MU shared the details of the “lethal commerce” on condition we don’t use their full names. Their biggest advantage is that all fighters, wherever they operate, have one thing in common: They have to take bread home. MU explained, “Trade routes are never closed fully in any area. At the end, we carry flour, pasta and oil. When we take goods to one area, families of people fighting there also benefit.” There are other fine points to keep in mind when shuttling through internal borders controlled by enemy groups. For example, truckers constantly monitor the safety of their routes through people they know. To find goods and to carry them, they have to maintain good relations with commanders in every zone. MU said, “They inform us when they seize commercial commodities. That way, they make money and we get goods to sell.” A security guard in a Mercedes escorts trucks that carry valuable goods from Esselame to the Kurdish Afrin region. This Mercedes is the ticket that allows the trucks to pass unhindered through areas controlled by various groups. When fighting groups see the Mercedes, they know that the trucks carry goods that won’t be touched and let them pass. Although production has slowed down enormously because of the civil war, it hasn’t fully come to a standstill in main cities like Aleppo and Damascus. Still, there is no electricity in most parts of the country. Small workshops produce goods, from textiles to car generators. As they can’t be exported to Turkey, Iraq or other countries, they are sold inside the country. Telephone networks are not working. Merchants and truckers learn what is produced through word of mouth from local commanders. MU said, “This is commerce with the conditions of 100 years ago.” The regime supporters, ISIS and the PYD have set up their own taxation systems in the areas they control. This tax is a kind of life insurance for merchants and truckers. For example, in the PYD area, if you are carrying tea and sugar, you pay $200 for each truck. Truckers say the system is different in the IS area: “If you are transiting through [iS] area, you pay small amounts. But if you are delivering to their area, they determine a tax based on the type of good, its value and identity of the merchant. Assad, ISIS and PYD have established systems, but not the FSA. The FSA has too many factions, and there is no established taxation system there.” When explaining how they can move in and out of all areas, MU told the latest situation in the country, in the following excerpt of the interview. Al-Monitor: Almost every corner of Syria is a war zone. The country is divided in four, everyone fighting each other, but you are moving around and cross internal borders. How is that? MU: Truckers know the safe routes. We constantly monitor where clashes are, like we follow weather reports. Coalition airplanes attack certain locations in coordination with PYD. The Assad regime informs its units of where they are going to hit. Merchants are always in touch with these parties. That is how we decide which route to take. Anyhow, whether it’s Assad, PYD or ISIS zone, there is not much interference with merchants. [The armed forces] want the trade to continue because they all benefit from it. Sometimes clashing groups declare temporary truces, say for four hours, to allow commercial vehicles to move freely. The latest was at Al Rai between Haseke and Raqqa where the PYD and IS halted clashes at certain times to allow the trade to go on. Al-Monitor: You mean they suddenly declare a cease-fire for business to go on? MU: Yes, there are severe clashes. You always see corpses all over. But when they see us, they say, ‘Let these people pass and we will resume fighting.’ They continue to kill each other after our vehicles pass through. Al-Monitor: What are favorite routes of truckers? MU: In general, we use a 400-km (249-mile) route between Idlib and Haseke. We prefer night travels. They have snipers at certain locations. Drivers know well where to turn off their headlights. If their vehicles are hit by snipers, then they have the danger of being robbed by Bedouins. Fighting groups are not the sole danger. Al-Monitor: Are any drivers killed? MU: Yes. PKK and ISIS regions are dangerous. Militants who stand at the entrance of their checkpoints are usually very unfriendly. But this is business. We take to roads knowing the dangers. For example, most of our drivers are from the FSA and they are wanted people. But they are a courageous lot. They never leave without saying their final farewells especially when they head to an Assad zone. Al-Monitor: What about money? How are payments made? MU: You don’t pay the drivers. There are money changers in every area who transfer up to $5 million a day. Some build secret compartments in their trucks and cars. Al-Monitor: A kind of hawale [bank money order] … MU: Better than hawale. No bank can transfer that much money in such a short time. Of course you have to pay 1-2% service commissions.
-
CAT Trucks Australia / Navistar Auspac Press Release / September 8, 2015 Cat CT630 stands tall in family logging company In a proud family-owned business where reputations evolve on the ability to endure the tests of time and toil among the hardwood forests of Western Australia’s southwest, Cat trucks have emerged as the modern-day truck of choice. Based at Manjimup, 300 km south of Perth, South West Haulage is a timber harvesting and haulage company which has been an integral part of the West Australian logging industry for around 60 years. For more than 50 of those years, Greg Smeathers has lived and breathed every aspect of the business. “This business, the bush, the trucks and the machinery, everything about it has been so much a part of my life since I was a kid. Even my father worked here,” says the sharp 68 year-old, born and bred in Manjimup who first joined the company as a 15 year-old apprentice mechanic in March 1962. In fact, so ingrained is South West Haulage in the life of Greg Smeathers that just three years ago, at an age when most men are contemplating retirement, Greg and sons Peter and Shawn invested everything they have to buy the company outright. “I’d had a limited financial interest in the company since 2007,” Greg explains, “and I’d been running the whole operation for years on behalf of the owners. Anyway, when the opportunity came up a few years ago to take full ownership of the company, and the boys were keen to be involved, we bit the bullet and threw everything we had into it. “At my age it wasn’t easy convincing the banks,” he smiles, “but we got there eventually. Apart from the financial aspects, the thing that got us across the line was that I’ve been totally involved in this company and this industry for well over 50 years. Plus the fact that the three of us are equal partners, and Peter and Shawn have spent most of their lives growing up around the business. “This company is now their future.” Meantime, growth has been significant since father and sons took total control. The winning of a major logging contract in early 2014 saw the size of South West Haulage almost double as annual tonnages increased to around 400,000 tonnes. A vast equipment inventory of harvesting machines, trucks, trailers and service vehicles today includes 24 prime movers with most coupled to trailer sets configured as ‘pocket’ roadtrains, operating on approved routes with overall length to 27.5 metres and gross weights up to 79 tonnes. South West Haulage operates in two divisions with Peter in charge of blue gum plantation timber and Shawn controlling the harvesting and haulage of native timbers, while Greg applies his vast experience to the overall operation. Like their father, Peter and Shawn Smeathers are highly experienced heavy equipment mechanics who know what it takes for machinery to succeed midst the constant demands of harvesting and hauling tall timber from forest to mill. “If there’s one thing for sure, I’ve certainly seen some big changes in equipment over the past 50 years,” Greg reflects. When it comes to equipment choice, father and sons take a long-term view. “We look for things to last,” says eldest son Peter. “We maintain all our own equipment and have a big workshop with mechanics and maintenance people who know how to build and rebuild things, so unlike a lot of companies we don’t have the need to replace trucks every four or five years. “The biggest thing for us is durability. The ability to just keep doing the job day in and day out. If the wheels aren’t turning, we’re not earning. It’s as simple as that.” In a business where equipment is invariably expected to deliver the full extent of its viable service life, Cat trucks are a comparatively new arrival. The first CT630 model joined the South-West fleet in 2011 when Greg was quick to recognise the advantage of a truck with a C15 engine and vitally, no AdBlue or EGR emissions controls. Since then, however, the performance and durability of Cat trucks have established the brand’s operational credentials to the point where there are now seven Cats in the fleet. In fact, all new prime movers bought since 2011 wear the Cat badge. “The business case for Cat definitely stacks up,” Peter says firmly. “There’s no question we all have a strong regard for Cat products but if the first truck didn’t stand up to the job, there would never have been a second Cat truck let alone another four or five of them. “It has become the truck of choice basically because it has done no wrong and it’s a good value-for-money proposition,” he confirms. As Peter quickly adds though, there’s more to the liking for Cat than mechanical matters. “It’s about the whole package; performance, reliability and service. We have a good relationship with the people at WesTrac, particularly Peter Calligaro (Cat Trucks manager) and when it’s all boiled down, everything revolves around the quality of the people you’re working with.” The Cats primarily operate in the blue gum operation, hauling up to 54 tonnes of sawn logs to a woodchip mill at Bunbury, 130 km from Manjimup and as far as 250 km from the furthest harvest sites. “On tare weight the Cats are at least as good as anything else we run,” Peter remarks, “but the big thing for us is that they’re showing all the signs they’ll live a long time in the job without any major issues. “The C15’s a proven engine, the gearbox and diffs are proven components, and the cabs and chassis are holding together really well. “They’re doing everything right and when it comes to equipment of any sort, that’s exactly what we’re after.” For Greg Smeathers, the Cat preference is honed on more than half a century of hard work and enduring performance. “I’ve been working with Cat gear since I was a 15 year-old apprentice, so the liking for Cat isn’t a recent thing. It’s something that has been built over many decades. The simple fact is I know it’s good gear.” On the experience with Cat trucks, a resolute Greg Smeathers concludes, “There’s no doubt that when it comes to anything with a Cat badge, we have high expectations. “The Cat trucks are certainly no different and they’re doing everything to live up to those expectations. “Better still, I can’t see any reason why they won’t keep doing it.” Photo gallery - http://www.cattrucks.com.au/cat-trucks-shine-in-was-south-west/
-
Transmec takes nine more twin-steer Iveco Stralis tractors
kscarbel2 posted a topic in Trucking News
Transport Engineer / September 9, 2015 Italian-owned logistics specialist Transmec has taken delivery of nine new Stralis Hi-Way 6x2 twin-steer tractor units to its 100% Iveco fleet in the UK. Transmec UK general manager John Simkins says the new tractor units (all AS440S48TX/P) were specified with the 11 litre Cursor 11 480bhp engine, with its HI-SCR (selective catalytic reduction) technology and no EGR (exhaust gas recirculation). They also have the Fuel Efficiency Package, designed to reduce operating costs, with technology including Iveco’s Eco-Roll. When cruise control is active, the system evaluates downhill inclines and puts the vehicle in neutral. At the end of the slope, the system selects the optimal gear and re-establishes normal vehicle operation. Other features include Iveco’s engine oil management system, claimed to reduce energy consumption by the oil pump and to enable faster engine warming. Coupled with this is an initial fill of 0W-20 low viscosity engine oil – a fully synthetic lubricant designed to release low volumes of sulphated ash at high temperatures, protecting both the engine and diesel particulate filter. The arrival of the distinctive blue and yellow-liveried vehicles comes shortly after the delivery of eight new Stralis trucks late last year (2014) via dealer Guest Truck & Van on a three year contract hire and maintenance agreement. “Our Iveco trucks have always delivered excellent performance,” comments Simkins, adding that the new vehicles are now operating from its Bradford depot. “The new vehicles have Iveco’s latest technology, in terms of performance and fuel economy, and we are looking forward to the benefits these will bring to our business.” . -
Owner/Driver / September 9, 2015 Ken Dillon has made the transition from company driver to small fleet livestock haulier. Ken Dillon has done his fair share of driving for other operators. Today, however, Ken and his wife Rhonda own a small fleet under the name of Clermont Livestock Transport. Located in central Queensland, the three trucks in the fleet are all Kenworths: a T909, a T904 and a T908. The newest, the T909, is powered by a 600hp (447kW) ISX E5 Cummins. "The 909 is definitely the best yet…It’s a real driver’s truck, I’m rapt with it," Ken says. The T909 is in stark contrast to the truck Ken started with when he was 17. "The truck was an [international] S-Line that I drove for my cousin, a tractor, doing singles and then on to road trains," he recalls. After going bush for a while, Ken came back to Clermont. He drove for McIver Transport for 18 months before spending 11 years with VJ & J Appleton. "It was hard yards back then. There was so much work and there was never any downtime. It was just go, go, go, which for a young bloke was all a big adventure and very exciting," Ken says. "You learnt a great deal, the roads weren’t what they are today and it was a case of using your initiative and solving the problems as they presented themselves." Ken entered into a business partnership with a colleague, Dan Mayes, in 2005 and purchased a new Kenworth T904 and a set of Haulmark crates. Ken subsequently bought Dan’s share of the business and now operates as Clermont Livestock Transport. Ken believes there are more cattle within the 500km radius of Clermont than the rest of Australia. "Let’s put it this way, it’s a good place to be if you want to cart cattle as it’s a very productive area," he says. While the majority of Ken’s work is in Queensland, he is happy to travel wherever the cattle need to go. "I do avoid the southern states, our gear is a bit big and heavy but we do work up into the territory and gulf," he says. Ken makes no secret he is a Kenworth man through and through. He recalls a recent encounter when he was heading into town and came across two blokes taking photos of his truck. The men were there for a photoshoot of a new Mack Super-Liner but decided to take a few shots of Ken’s truck as well. He recalls one of the photographers commenting the Kenworth looked so good coming towards them that they wanted to turn the Mack around and do the same thing. "I piped up and said: ‘you’ll never make a Mack look anything like a Kenworth’." Photo gallery – http://www.ownerdriver.com.au/industry-news/1509/living-the-livestock-game/ Kenworth T909 Info - http://www.kenworth.com.au/trucks/t909/ https://www.youtube.com/watch?v=yReyurRd_RM
-
Critics push U.S. to help Europe by taking more refugees
kscarbel2 replied to kscarbel2's topic in Odds and Ends
"this is a situation that calls for governments and their military to take the action to correct the conditions that are causing these people to flee" A key point, and yet there is no dedicated effort by the powers who can successfully accomplish such a mission to see it thru. Given the Russian connection with Assad, they must be involved in a military solution. And the fact is, they have one of the best military capabilities. ISIS is as much of a problem for Russia as it is for the US and the rest of the world. If we worked together on common goals once in a while, we could get along better the rest of the time. Note what I posted above, that MANY of the immigrants (refugees) are not from Syria. No one can blame people for seeking a better life in a higher-life-quality country, but the EU simply can't accommodate the staggering numbers we're seeing. -
Oshkosh wins $6.75 billion deal to replace U.S. Army, Marine Humvees
kscarbel2 replied to kscarbel2's topic in Trucking News
Lockheed Martin Protests JLTV Contract Award to Oshkosh Bloomberg / September 8, 2015 Lockheed Martin Corp. has filed a protest seeking to overturn the U.S. Army’s choice of Oshkosh Corp. to build a new vehicle replacing the Humvee, a program potentially valued at as much as $30 billion. Oshkosh was awarded an initial $6.75 billion contract for about 17,000 vehicles last month. The challenge pits Lockheed, the No. 1 U.S. government contractor, against Oshkosh, which ranked 99th in 2014, according to data compiled by Bloomberg. “After evaluating the data provided at our debrief, Lockheed Martin has filed a protest of the award decision,” spokesman John Kent said Tuesday in an e-mail. “We firmly believe we offered the most capable and affordable solution for the program. Lockheed Martin does not take protests lightly, but we are protesting to address our concerns regarding the evaluation” of the company’s offer. The Army plans to purchase about 55,000 of the multipurpose Joint Light Tactical Vehicle for its troops and the Marine Corps through 2040 as a better-armored replacement for the aging Humvee. AM General The announcement came the same day that AM General LLC, the other losing competitor and the maker of the Humvee, said it wouldn’t file a challenge with the Government Accountability Office that handles protests. The most famous case in the last decade of a successful protest was GAO’s 2008 decision supporting Boeing Co.’s challenge of an Air Force award to Northrop Grumman Corp. for its aerial refueling tanker. It cited “a number of significant errors that could have affected the outcome.” Boeing won the rebidding. Few Sustained Only 2.4 percent of protests over Defense Department contract awards have been sustained from fiscal 2010 through fiscal 2014, according to an analysis of GAO data by Bloomberg Government analyst Jorge Uquillas. “The government is aware of the protest” by Lockheed and “will fully cooperate in required processes,” Army spokesman Michael Clow said in an e-mail. “We remain confident that the JLTV program is well positioned to provide our soldiers and Marines a substantial capability improvement while remaining affordable for America’s taxpayers.” December Deadline The GAO has until Dec. 17 to render a decision, according to spokesman Charles Young, who confirmed that Lockheed filed a protest. If it wins the challenge, Lockheed would manufacture the vehicles at a Camden, Arkansas, facility. Oshkosh has its plant in the Wisconsin town of the same name, where it’s based. The Humvee entered service in 1985, when “improvised explosive devices (IEDs) and other anti-vehicle explosive devices were not a major factor in military planning,” according to a March 9 report by the Congressional Research Service. The Army required that its Humvee replacement be able to survive the most destructive improvised bombs, be mechanically reliable and maintainable with onboard diagnostics, all-terrain mobility, and linked into current and future tactical data networks, according to the CRS. Separately, AM General has just received a six-year, fixed-price contract valued at as much as $428 million to supply the National Guard with 654 of its new M997A3 Humvee Ambulance Chassis Vehicle designed for domestic disaster relief efforts, company spokesman Jeff Adams said in a statement. The Lockheed JLTV (with video) - http://www.lockheedmartin.com/us/products/jltv.html -
"People should and do trust me" - Hillary Clinton
kscarbel2 replied to kscarbel2's topic in Odds and Ends
The Clinton campaign has reached the end of the road. Hillary is actually grovelling. After saying for weeks that she would not apologize, refusing to admit that she was wrong, she is now saying that she's sorry and her action was a mistake. Only a last ditch effort can cause this arrogant woman to humble herself before the public. http://www.foxnews.com/politics/2015/09/07/clinton-says-no-email-apology-what-did-was-allowed/ http://www.msn.com/en-us/news/politics/clinton-says-sorry-for-using-private-email-at-us-state-dept/ar-AAe4NkW
BigMackTrucks.com
BigMackTrucks.com is a support forum for antique, classic and modern Mack Trucks! The forum is owned and maintained by Watt's Truck Center, Inc. an independent, full service Mack dealer. The forums are not affiliated with Mack Trucks, Inc.
Our Vendors and Advertisers
Thank you for your support!