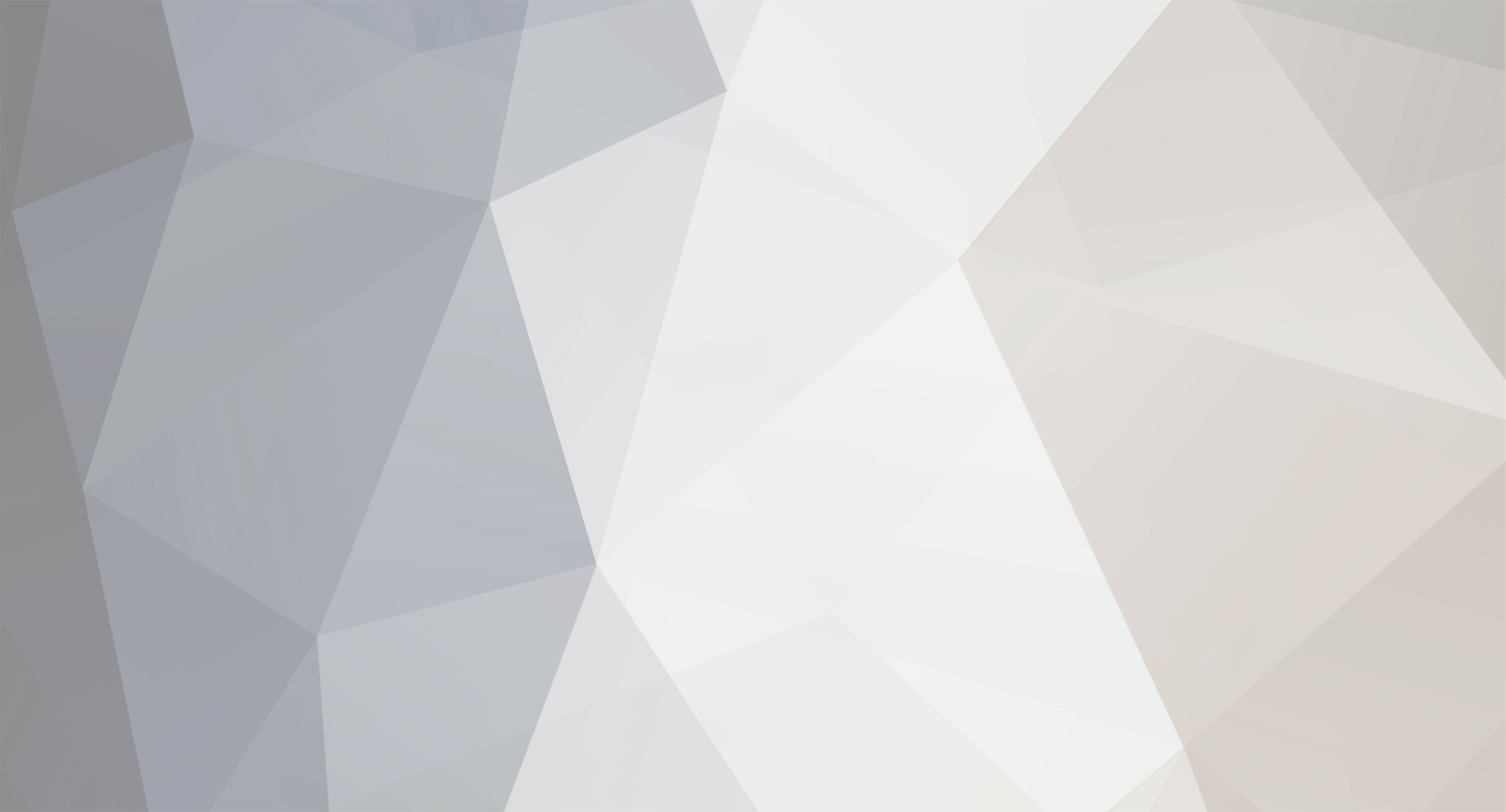
kscarbel2
Moderator-
Posts
18,750 -
Joined
-
Days Won
114
Content Type
Profiles
Forums
Gallery
Events
Blogs
BMT Wiki
Collections
Store
Everything posted by kscarbel2
-
Fleet Owner / September 15, 2015 With 2015 Class 8 truck sales in North American running a strong 10% above last year, 2016 should see similar volumes, according to Richard Howard, Sr. VP of sales and marketing for Daimler Trucks North America. Barring unforeseen global economic disruptions, “directionally we expect sales to move sideways,” he said during an event showcasing the company’s autonomous demonstration truck. The company forecasts Class 8 totals will reach 313,000 trucks this year. “We already have good order intake for 2016,” Howard said, pointing out that business confidence in the U.S. is strong and expected to stay strong. The story is the same in the medium-duty market with good demand from both small businesses and large fleet customers, according to Howard. Overall, DTNA forecasts NAFTA Class 6-8 sales will reach 435,000 this year and run at a similar rate in 2016, which is a substantial increase from 384,000 units in 2014. In the U.S. DTNA market share in Classes 6-8 is up 1.1% YTD at 39.6%, approaching the company’s high of 40.2% in 2013, Howard reported. DTNA’s push to expand component sales is also gaining traction with the new Detroit DT12 automated mechanical transmission selling 39,000 units this year and reaching 42% penetration in the Freightliner Cascadia, according to Howard. “We could have sold more if we had them,” he said. “I expect [to sell] 60,000 next year and surpass the 50% mark in Cascadias.” As part of the press event, DTNA brought the Freightliner Inspiration, the first autonomous commercial truck licensed to operate on U.S. open highways, back to Nevada where it had its debut back in May at the Hoover Dam. This time the company put journalists through the certification program required by Nevada for any CDL holder operating the advanced demonstration truck. Stressing that the Inspiration is not a prototype, Diane Hames, DTNA’s GM of marketing and strategy said it was intended as “a technology showcase of what’s possible when you combine the building blocks [of advanced safety systems] already available.” Calling the various systems integrated into the truck “bionics for the driver,” Hames said the goal is not to replace drivers, but rather “to advance and extend their capabilities.” For example, its radar and camera systems offer drivers visibility well beyond the capability of the human eye, she said, and the truck’s sensors can react to situations far faster than typical human reaction times. Integrating these building blocks will create new opportunities as trucks move beyond current passive and active safety systems to what Hames calls interactive safety. “Combining technology and big data, interactive safety will bring the next radical advances in truck safety,” she predicted. “You can expect to hear a lot more about this in the next few years.”
-
Daimler Trucks Expects Brazil Crisis to Worsen Before Revival
kscarbel2 replied to kscarbel2's topic in Trucking News
Daimler trucks boss braces for prolonged Brazil slump Reuters / September 11, 2015 German truckmaker Daimler is bracing for a prolonged slump in Brazil as shrinking growth in Latin America's largest economy and corruption probes weigh down business. "I expect no fundamental recovery in the next years," Daimler trucks chief Wolfgang Bernhard said Thursday. "The scandals are paralysing everything," he added, noting it may take as many as three years for the Brazilian trucks market to rebound. An investigation into state-run oil company Petrobras has paralysed Brazil's construction industry and derailed some oil projects, inflicting damage on the country's embattled economy. Stuttgart-based Daimler said last month it had struck a labour deal with workers at its Brazilian trucks plant in Sao Bernardo do Campo that delayed the planned layoff of 1,500 staff until August 2016. Employees at the plant have agreed to cut both their working hours and their pay by 20 percent, with the Brazilian state ready to compensate workers for half of the pay reduction. Separately, Bernhard said truck demand in China may plunge between 30 and 40 percent this year as the government there delays infrastructure projects. But solid demand in the United States and Europe, where volume will likely grow as much as 15 percent each, will help Daimler compensate for any lost business, the executive said. Daimler is planning to resume business in Iran following the country's nuclear deal with world powers, Bernhard said. The accord looks likely to be implemented after efforts by U.S. Republicans to kill the agreement collapsed on Thursday. "We will revive our activities which we let rest for many years," he said. "Iran is a great opportunity for us." -
-
-
Iveco Press Release / September 16, 2015 Even more stylish, eco-sustainable, safer, more comfortable, more efficient and more manoeuvrable. Cities love the new Eurocargo: the truck which respects people and the environment in which it works. Together with the heavy duty Stralis and light duty Daily, the new Eurocargo completes the evolution of the Iveco range. Produced at the Silver World Class Manufacturing (WCM) facility in Brescia, Italy, the new Eurocargo is set to venture out to cities around the world, as the ideal business partner. The celebration of Iveco’s 40th anniversary this year sees the launch of the new Eurocargo, the truck the city likes. Eurocargo is the ideal partner in urban missions: respectful of people and the environment, featuring all new functionality and design. It is a vehicle that offers lower fuel consumption whilst confirming its super and steady handling and versatility. Just two years after the launch of the Euro VI version, Iveco has made further improvements to a vehicle which has already been chosen by half a million customers in Europe, Africa, Middle East, Australia and Latin America. Eurocargo is the technology and market leader in Europe, and the new model offers important innovations in terms of engines, safety, comfort, cost reduction and environmental sustainability, thus completing the evolution of the Iveco range, and following closely on the success of Stralis and Daily, which won International Truck of the Year 2013, and International Van of the Year 2015, respectively. Pierre Lahutte, Iveco Brand President, said: “Our new Eurocargo is the truck that the city likes. A vehicle that has something to be appreciated by everyone: cities like it because it is sustainable, owners like it because it is efficient and has a low total cost of ownership (TCO), drivers like it because it’s a true “office on wheels”- comfortable and multi-functional, easy to handle and ergonomic to work in”. The new Eurocargo is the only Euro VI medium range vehicle in its category to adopt a single anti-emission system, the HI-SCR system with passive diesel particulate filter (DPF). The HI-SCR is the only emission control system which does not change the combustion process – because it works through fresh air intake rather than exhaust gas recirculation. Medium range vehicles are mainly used for missions such as urban distribution and municipal services: this is why Iveco has set performance improvement and fuel consumption reduction as a top priority. With a range of eight engines, the new Eurocargo adopts two Iveco Tector 5, 4-cylinder, 160 and 190 hp engines, optimised to suit the typical operating conditions of urban missions. Moreover, thanks to the development of a new turbocharger, as the compression ratio and torque output increase at speeds below 1,200 rpm, Eurocargo is able to respond more dynamically when accelerating and upon start up, which results in fuel savings of up to 8%. Lastly, thanks to the EcoSwitch system, which lengthens sixth speed engagement times and limits down-shifting into fourth, and the EcoRoll function (offered on 12-speed transmissions) which takes advantage of vehicle inertia in downhill situations, Eurocargo reduces fuel consumption when on extra-urban routes and long runs. Safety is also at the heart of Eurocargo's renewal: in addition to the steering wheel airbag and steering wheel controls, the new Eurocargo is available with all the key driving assistance systems, such as the Lane Departure Warning System (LDWS), Advanced Emergency Braking System (AEBS) and Adaptive Cruise Control (ACC). To improve safety and visibility when driving, LED Daytime Running Lights (DRL) have also been adopted as standard. Xenon headlights can be specified as an option. Eurocargo not only incorporates many new features, it is also built around an entirely new design – which reflects the style pioneered by Daily – with new air deflectors and the new front grille that traces a smile beneath the large brand name in the centre. The advertising campaign that will accompany the new Eurocargo, along with the slogan "The truck the city likes", places the vehicle as a central figure in urban settings. The vehicle can be driven with ease in the city, a city that everybody wants call home, a city that merges and becomes a perfectly integrated part of the everyday lives of the public.
-
Critics push U.S. to help Europe by taking more refugees
kscarbel2 replied to kscarbel2's topic in Odds and Ends
This revelation relates to my thought process. Ironic that we're only hearing about this now. http://www.theguardian.com/world/2015/sep/15/west-ignored-russian-offer-in-2012-to-have-syrias-assad-step-aside We're not always going to agree with or trust the Russian government. But there will be times, as in WW2, when we need to cooperate with them for the greater good. And handled properly, that cooperation can lead to a better "working relationship" at other times. With the current administration having gone with a very poorly thought out ISIS and frankly close-minded, arrogant Syria strategy, Europe is now overflowing with refugees it realistically can't support, hundreds of people including children have died senselessly in this convoluted migration, the Middle East is in a state of chaos. Well done, and I fear terrorist cells have seized the recent open door opportunity to enter Europe. -
Green Car Congress / September 14, 2015 Ford will be introducing the Euro-spec version of its Edge SUV at the IAA in Frankfurt this week. The large SUV will be offered in Europe with a choice of 180 PS (177.5 hp) 2.0-liter TDCi diesel engine with six-speed manual transmission, or 210 PS (207.1 hp) bi-turbo 2.0‑liter TDCi diesel with six-speed PowerShift automatic transmission. Ford said both powertrains will deliver up to 40.6 mpg US (5.8 l/100 km) fuel efficiency and 149g/km CO2 supported by Auto-Start-Stop technology. The upscale Edge will join the Ford Kuga (U.S. market Escape) SUV and EcoSport compact SUV to meet the demands of growing numbers of SUV customers in Europe. Ford expects to sell 200,000 SUVs in Europe in 2016—a 200% increase compared to 2013. (Earlier post.) Edge also will feature Ford’s Intelligent All-Wheel Drive (AWD) technology as standard, delivering a seamless transition between front-wheel drive and all-wheel drive performance to provide a more secure footing on the road especially in slippery conditions. Measuring how the car’s wheels are gripping the road surface every 16 milliseconds, the system can send up to 100% of engine torque to the front or rear wheels. By only delivering torque where and when it is needed, Intelligent AWD has minimal impact on fuel-efficiency and CO2 emissions compared with permanent four-wheel drive systems. Edge and the new Ford Ranger pickup, also being introduced at Frankfurt, are among eight Ford models offered with AWD or four-wheel drive, including the all-new Focus RS, Galaxy, S-MAX, Mondeo and Mondeo Vignale. All-new Edge will offer new Ford technologies, including Adaptive Steering, which automatically optimizes the steering response according to vehicle speed, making it easy to maneuver at low speeds, while remaining precise and intuitive at higher speeds; and Front Split View Camera, which makes restricted visibility junctions or parking spaces easier to negotiate. Edge will introduce segment-first Pre-Collision Assist with Pedestrian Detection; a camera- and radar-based system that operates at speeds from 5mph to over 100mph to detect vehicles and people in the road ahead. The system can automatically apply the brakes if a potential collision is detected and the driver does not respond to warnings. Ford anticipates a five-star safety rating from independent crash test authority Euro NCAP. Acoustic windscreen glass and laminated glass for the driver and front passenger door windows help minimize noise in the cabin. Underbody panels and wheel well liners further minimize road and wind noise. All Edge models (except Zetec in UK) are also equipped with Ford’s Active Noise Control technology that detects unwanted engine noise in the cabin and cancels it out with opposing sound waves that are fed through the car’s sound system. Ranger The current Ford Ranger has generated rapid sales growth in Europe since first being introduced in late 2011. Total sales of 21,600 vehicles in 2014 in Ford’s 20 traditional European markets were more than double those achieved in 2012, while 16,700 Rangers were sold in the first eight months of 2015—a further 36% increase year-over-year. Ranger won the prestigious “International Pickup Award 2013” title, and the new model will be challenging for the 2016 award at the competition next month. New Ranger offers improved fuel economy, with a more efficient powertrain range—enhanced by Auto-Start-Stop technology, new final drive ratio options and the introduction of Electric Power Assisted Steering—delivering reductions in fuel consumption of up to 17%. The improved diesel line-up features 130 PS (128.2 hp) and 160 PS (157.8 hp) variants of Ford’s latest 2.2-liter TDCi engine—delivering increased output compared to the 125 PS and 150 PS engines in the outgoing model—and the 200 PS (197.3 hp) five-cylinder 3.2-liter TDCi unit. Both six-speed manual and automatic transmissions are available, and customers can select four-wheel drive and two-wheel drive variants. Wildtrak models feature four-wheel drive as standard. All new Ranger variants achieve significantly improved fuel efficiency, with the 160 PS model offering exceptional figures of 6.5 l/100 km (36.2 mpg US) and 171 g/km CO2 emissions for reduced running costs—compared with 7.8 l/100 km (30.2 mpg US) and 206 g/km CO2 in the outgoing model. An electronically controlled transfer case allows drivers in four-wheel drive models to shift on the fly from two- to four-wheel drive high-range with a knob on the center console. For low- speed torque or additional downhill braking in challenging terrain, drivers also can engage low- range four-wheel drive gearing. An electronic locking rear differential also helps to improve traction in difficult conditions. These off-road strengths are matched by towing capability of up to 3,500 kg and payload capacity. An array of driver assistance technologies deliver greater comfort and convenience, including Lane Keeping Alert and Lane Keeping Aid, Adaptive Cruise Control with Forward Alert, Front and Rear Park Assist, Rear View Camera, and a standard Electronic Stability Control system with rollover mitigation and trailer sway control. Other smart technologies include: Hill Launch Assist, which helps drivers confidently start off from a slope, whether in forward or reverse; Hill Descent Control, which uses the traction control system to help when descending steep slopes at a constant speed; Adaptive Load Control, which adjusts the Electronic Stability Control system based on vehicle load; and Emergency Brake Assistance, which provides additional pressure to the brake system to increase braking force when the driver applies the brakes quickly in an emergency situation.
-
Scania Press Release / September 14, 2015 Scania has added an updated 16.4-litre V8 engine to its marine solution’s range. The new engine boasts a maximum power output of 1,150 hp (846 kW) with an outstanding fuel economy. The engine benefits from being a part of Scania’s modular system thus providing high uptime. Scania’s latest marine engine makes use of the company’s common-rail XPI fuel-injection technology, first introduced to truck engines in 2007. Consequently, the new marine engine utilises well-proven technology and provides customers and users with high reliability and high uptime. Joel Granath is Senior Vice President, Scania Engines. “This high-power V8 stands on the same foundation as all previous engines before it,” Granath says. “It features outstanding fuel-efficiency, uptime and a top power-to-weight ratio.” Used in combination with the Scania-developed Engine Management System (EMS), the technology delivers unrivalled levels of fuel-efficiency resulting in a 5 percent decrease in fuel-consumption compared to previous versions. The power output from the new V8 engine ranges from 900 hp (662 kW) to 1,150 hp (846 kW), depending on application and rating. While the latest addition to the engine range offers more power, the physical size of the complete installation remains the same. Engines from Scania are renowned for their unrivalled power-to-weight ratio and massive torque. The new engine platform pushes these parameters further, resulting in an even higher productivity. The complete V8 common-rail edition ranging from 900 hp to 1,150 hp, is suitable for both propeller and waterjet applications. Related photograph - http://www.scania.com/media/pressreleases/P15084EN.aspx#
-
Owner/Driver / September 9, 2015 As the name suggests, trucks and trailers shared centre stage at this year’s Perth Truck and Trailer Show. Held over three days in late July at the Perth Convention and Exhibition Centre, the show attracted local manufacturers, plus local representatives of national companies and eastern states exhibitors keen on promoting their wares in the west. A welcome addition to the 2015 event was the opening day’s information seminars covering topics such as dangerous goods transportation, fatigue management, chain of responsibility (COR) and trailer brake requirements. Cat Trucks’ new triple-rated CT630 HD was displayed prominently at the show. "It’s very comfortable, great visibility, great air-conditioners, and it’s got the yellow engine inside, which is well supported by WesTrac’s footprint up and down the road," business unit manager at WesTrac Kewdale Highway Truck Centre Peter Calligaro says. He says acceptance of the Cat Trucks brand has the biggest hurdle in the west, although that is steadily changing. "Kenworth has been big over here, and Volvo are really doing a big push at the moment, but our product is being accepted now," he says. "It is a good product; I’ve not seen anything that is causing us many headaches, so I believe it’s just to keep pushing, and keep marketing, and we’ll get there in the end." Skipper Trucks had a presence at the show and opted for an outdoors display instead of shouldering arms with competitors inside. Skipper Trucks, part of the Automotive Holdings Group (AHG), has long been a familiar name in the Perth truck market, although close on four years ago it was rebranded as WA Iveco. "Skipper Trucks has been an entity for 30 odd years, and it never actually went away, it just wasn’t a sign on the wall," company representative Mike Rutherford explains. "The last three years, you talk to anyone and they’ll just say: ‘I’m just going down to Skipper’s’. People didn’t change, we were still called Skipper’s." The relaunch of Skipper Trucks has coincided with the move to new premises at Welshpool. Skipper’s showcased two of its premium trucks, an Iveco Powerstar 7800 and an Iveco Stralis 500, at the show to get the Skipper’s name back in the minds of the public. Meanwhile, trailer makers rightly occupied a fair share of space inside the Perth Convention and Exhibition Centre, with local outfits keen to highlight WA’s expertise in that sector. This included Custom Quip Engineering (CQE), which had aluminium tippers on show. Not far from the CQE stand, G & A Lombardi general manager Mike Dunbar chatted with prospective customers about the company’s Steelite end tipper range. Overall, organisers were placed with attending figures with around 8,500 visitors attending over the three days. Show director Peter Woods says while the number of attendees is lower than in previous years, he believes it is due to the industry going through hard times, both locally and across the country. "There has been a definite shift in the industry in the past year or so, and we are grateful to all our exhibitors for sticking with the show and extending their support to the industry," he says. The Perth Truck and Trailer Show is presented by the Commercial Vehicle Industry Association, a division of the Motor Trade Association (MTA). Plans are already underway for the next show, which will be held on July 28 to 30, 2017. Photo gallery - http://www.ownerdriver.com.au/events-news/1509/western-exposure-at-2015-perth-truck-and-trailer-show/
-
Commercial Carrier Journal (CCJ) / September 11, 2015 The “rules of the game” for next-gen engine oils, still set to hit the market late next year, should be fully defined in the coming months, says Chevron Delo’s Shawn Whitacre, giving oil makers like Chevron a year to finalize their products and to meet the new specifications of the so-called PC-11 oils. The new oils are scheduled to be first licensed on Dec. 1, 2016, Whitacre says, the date by which it will be available to fleets and owner-operators. PC-11 will be split into two categories. The first will replace the current CJ-4 oils on the market and will be licenced as CK-4 by the American Petroleum Institute. The second, which will be called FA-4, will be low viscosity oils — “thinner” oils designed to help increase fuel economy and lower greenhouse gas emissions. Whitacre, a senior staff engineer for Chevron, is the new chairman of the ASTM’s Heavy-Duty Engine Oil Classification Panel, replacing outgoing chairman Jim McGeehan, a longtime Chevron oil engineer and longtime chair of the classification development panel. Whitacre has been on the panel since 1996, helping develop five engine oil categories. The two PC-11 oils are the first new classifications in a decade, requested by engine makers several years ago to meet the needs of evolving, modern engines and help aid in meeting current and upcoming fuel economy and emissions regulations. The testing processes for the new categories is stringent and time consuming, Whitacre says — why oil makers like Delo will have a year to conduct the tests on the new oils, which have been in development now for about four years. Oil buyers will, once the products go to market, have more options in their oil choices, Whitacre says, in the form of new lower viscosity grades like 10W-30s or those with even lower viscosity. The CK-4 category will be completely backwards compatible with all engines on the market. But, says Whitacre, the thinner FA-4 oils may not be, and the decisions will be left to the engine manufacturers to determine whether if they can be used in older equipment.
-
Transport Topics / September 14, 2015 Austin, Texas-based FlowBelow Aero Inc. (http://www.flowbelow.com/), a manufacturer of tractor-mounted aerodynamic products, announced it has partnered with tank truck carrier Indian River Transport to equip its tractors with the company’s new fuel saving AeroKit system. No terms of the arrangement were disclosed. The AeroKit includes quick-release wheel covers and a pair of tandem fairings installed on the tractor that work together as a complete aerodynamic system to address the complex airflow around the exposed rear wheels of the tractor. "We have already begun an aggressive installation program with the assistance of FlowBelow at each of our three terminals,” said Mark Gressett, who is safety director at Indian River Transport. Indian River Transport (http://www.indianrivertransport.com/) , which is based in Winter Haven, Florida, operates 650 trucks and 800 food grade tank trailers across the United States, Mexico and Canada. The company primarily hauls fruit juice and dairy products. The patented AeroKit system reduces aerodynamic drag and improves fuel efficiency of the tractor by 2.23% based on SAE J1321 third-party testing using EPA's SmartWay guidelines, the company said. “We tested the AeroKit in our fleet for over seven months, starting in January specifically to test the product’s winter durability and performance,” Gressett said. “There are limited options for improving the aerodynamic performance of a tanker trailer, so we were very interested in the AeroKit as a tractor-mounted aerodynamic system. We were impressed with the product’s durability, ease of use, fuel-efficiency performance of over 3% and investment payback in less than one year.” “Beyond ordering the most aerodynamic and fuel-efficient tractors from the OEMs and controlling driver behavior, routes and fuel stops, there are few options to increase the overall fuel efficiency of a tanker fleet,” said Josh Butler, founder and CEO of FlowBelow. “We are pleased that our Tank Truck AeroKit can play a key role in helping these specialized fleets improve their fuel efficiency and environmental impact.”
-
New Zealand to extradite American on industrial espionage charges
kscarbel2 replied to kscarbel2's topic in Odds and Ends
Obama Administration to Block New Zealand Extradition Request ABC News / September 14, 2015 On Monday, New Zealand Prime Minister John Key announced that the U.S. government was refusing to extradite American truck driver Timothy Maikshilo, who is facing formal charges of industrial espionage. "A document arrived from the United States, rejecting the extradition of Maikshilo, a man who is in the process of causing incalculable damage to New Zealand’s food industry," announced Key, who called the U.S. position "extremely troubling and shocking." According to Wellington Police Chief Tim Barfield, authorities have determined that while Maikshilo was employed in New Zealand as a temporary help truck driver, he took a nighttime position at Sanitarium Health and Wellbeing Company’s factory and headquarters in Auckland as a forklift operator where he took inside information on the manufacture of the company’s Marmite food spread. When he became aware of company suspicion, he abruptly departed New Zealand and returned to the United States. The move by the Obama Administration to block Maikshilo’s extradition has prompted harsh criticism from White House critics who note New Zealand’s long-time support of American policy in the Pacific. U.S. Senator Ted Cruz (R-Texas) calls the decision "a classic and common case of the US exploiting pretenses of law and justice to protect criminals from the rule of law, even when faced with allegations of the most egregious wrongdoing.” Responding to criticism Monday afternoon, U.S. State Department spokesman Patrick Ventrell said "we reiterate our expressions of sympathy to Sanitarium Health and Wellbeing, and understand the potential loss of jobs there. But as a matter of longstanding policy, we don't comment on specific extradition requests, so I simply can't get into that." . -
Missouri mother keeps kids in crate underground Associated Press / September 13, 2015 A 24-year-old mother is in custody Saturday after her two young children were found barefoot, dirty and living in a wooden shipping crate in an underground cave on the eastern edge of Kansas City, Missouri. Brittany Mugrauer was charged Friday night with two counts of felony child endangerment. Jackson County detectives discovered the 4- and 6-year-old children Thursday in the 8-by-10-foot crate furnished with vehicle bench seats, two small blankets, trash and thin wires. According to the probable cause statement, the crate was missing one side and surrounded by car parts and vehicles in various states of disrepair. The investigators, who went to the cave to serve a search warrant related to a possible stolen car operation, noted that the children did not appear frightened by them or the fact that they were alone. The 4-year-old child was using hands to eat a dirty, dry cup of ramen noodles, a detective wrote. When asked why they weren't wearing any shoes, the children responded that they didn't have any. The older child told officers he should be in first grade but did not go to school. The extensive network of caves is the product of massive limestone mining in the late 1800s and early 1900s. Years after the mining operations ceased, companies started finding ways to use the millions of square feet of abandoned underground space. The caves house hundreds of businesses, many of which specialize in storage or warehousing because they are protected from extreme weather and have year-round temperatures of around 70 degrees. The officers were down there investigating a possible chop shop, where stolen vehicles are dismantled so that the parts can be sold or used to repair other stolen vehicles. Many of the caves feature paved roads, utilities and developed business space, while others, such as the one where the children were found, consist of dirt floors and uncontrolled entrances.
-
DAF Press Release / September 11, 2015 The DAF CF Silent has won the Fleet Transport Truck Innovation Award 2016. For the second year in succession, DAF Trucks was honored with this Award, following up on the same decoration last year for the class leading fuel efficient PACCAR MX-11 engine. The jury praises the effective and smart ‘Silent Mode’ solution, contributing to enhanced transport efficiency. The DAF CF Silent is part of the DAF Transport Efficiency program with the aim to further optimize return per kilometer through amongst others enhanced vehicle availability. Thanks to the smart ‘Silent Mode’, the truck enables goods to be loaded and unloaded in areas where evening, night-time or early morning noise restrictions apply. When the special 'Silent Mode' is activated – just by pressing the ‘Silent’ button on the dashboard – the engine software switches to a program that limits torque and engine speed. Gears are changed at lower engine speeds and also thanks to the encapsulation of the gearbox noise level remains even below 72 dB(A). The DAF CF Silent is powered by the Euro-6 DAF MX-11 engine, with ratings of 210 kW/290 hp to 320 kW/440 hp. “Its cleverness and ease of operation made the jury honor the DAF CF Silent with the Fleet Transport Truck Innovation Award,” commented Jarlath Sweeney, Group Editor, Fleet Transport Magazine in Ireland. “The technology makes it possible to continue transport operations during evenings and at night in areas where noise restrictions apply. This directly adds to uptime and thereby increases transport efficiency.” Related photograph - http://www.daf.com/~/media/images/daf%20global/imagebank/daf%20press%20releases/2015/q3/daf%20cf%20silent%20fleet%20transport%20award%202016.jpg
-
Volvo Group Press Release / September 11, 2015 Volvo Group Executive Team member Torbjörn Holmström has announced his intention to step down from his position as Volvo Group Chief Technology Officer and Executive Vice President Group Trucks Technology. A global search will be conducted during autumn 2015 to identify his successor. “After concluding the largest industrial project in history of the Volvo Group - the renewal of the Volvo Trucks and Renault Trucks ranges - it is time to prepare for my successor”, says Torbjörn Holmström, Volvo Group Chief Technology Officer and Executive Vice President Group Trucks Technology. “Continuity in technology leadership is an essential part of driving large product projects and now is a good time to look for a new head of technology development.” Torbjörn Holmström will continue in his current position until such time as a successor has been appointed to lead the Volvo Group´s global truck technology and product development organization. Following this, he will remain at the Volvo Group as senior advisor research and development. .
-
Whether you are working behind the wheel of a truck or a computer screen, sitting down for prolonged period of time is killing you — literally — by way of obesity, heart disease, and diabetes. All this downtime is so unhealthy that it's given birth to a new area of medical study called inactivity physiology, which explores the effects of our increasingly butt-bound, tech-driven lives, as well as a deadly new epidemic researchers have dubbed "sitting disease." "Our bodies have evolved over millions of years to do one thing: move," says James Levine, M.D., Ph.D., of the Mayo Clinic. "As human beings, we evolved to stand upright. For thousands of generations, our environment demanded nearly constant physical activity." But thanks to technological advances, that physically active environment has disappeared. When you sit for an extended period of time, your body starts to shut down at the metabolic level, says Marc Hamilton, Ph.D., associate professor of biomedical sciences at the University of Missouri. When muscles — especially the big ones meant for movement, like those in your legs — are immobile, your circulation slows and you burn fewer calories. Key flab-burning enzymes responsible for breaking down triglycerides (a type of fat) simply start switching off. Sit for a full day and those fat burners plummet by 50 percent, Levine says. In addition, the less you move, the less blood sugar your body uses. Research shows that for every two hours spent sitting down per day, your chance of contracting diabetes increases by 7 percent. Your risk for heart disease goes up, too, because enzymes that keep blood fats in check are inactive. You're also more prone to depression: With less blood flow, fewer feel-good hormones are circulating to your brain. "Sitting is the new smoking," says Anup Kanodia, a physician and researcher at the Center for Personalized Health Care at Ohio State University's Wexner Medical Center. As evidence, he cites an Australian study published in October 2012 in the British Journal of Sports Medicine that compared the two pastimes. Every hour of TV that people watch, presumably while sitting, cuts about 22 minutes from their life span, the study's authors calculated. By contrast, it's estimated that smokers shorten their lives by about 11 minutes per cigarette. How can this happen? Not only is sitting lousy at calorie burning, but it has been shown to suppress the production of an enzyme called lipoprotein lipase, which is essential for turning bad cholesterol into good. Sitting can also lead to insulin resistance and, therefore, trouble metabolizing sugar. All these strikes against it help to explain, at least in part, its association with heart disease and diabetes. Spending the day sitting down also has significant negative effects on your posture and spine health, says Douglas Lentz, a certified strength and conditioning specialist and the director of fitness and wellness for Summit Health in Chambersburg, Pa. "When you sit all day, your hip flexors and hamstrings shorten and tighten, while the muscles that support your spine become weak and stiff," he says. It's no wonder that the incidence of chronic lower-back pain among women has increased threefold since the early 1990s. And even if you exercise, you're not immune. We've become so sedentary that 30 minutes a day at the gym may not do enough to counteract the detrimental effects of eight, nine, or 10 hours of sitting, says Genevieve Healy, Ph.D., a researcher at the Cancer Prevention Research Centre of the University of Queensland in Australia. That's one big reason so many women still struggle with weight, blood sugar, and cholesterol woes despite keeping consistent workout routines. In a recent study, Healy and her colleagues found that regardless of how much moderate to vigorous exercise participants did, those who took more breaks from sitting throughout the day had slimmer waists, lower BMIs (body mass indexes), and healthier blood fat and blood sugar levels than those who sat the most. In an extensive study of 17,000 people, Canadian researchers drew an even more succinct conclusion: The longer you spend sitting each day, the more likely you are to die an early death — no matter how fit you are. So if exercise alone isn't the solution, what is? Fortunately, it's easier than you think to ward off the perils of prolonged parking. Just ramp up your daily non-exercise activity thermogenesis — or NEAT. That's the energy (i.e., calories) you burn doing everything but exercise. In his groundbreaking study on NEAT, the Mayo Clinic's Levine used motion-sensing underwear to track every single step and fidget of 20 people who weren't regular exercisers (half of them were obese; half were not). After 10 days, he found that the lean participants moved an average of 150 minutes more per day than the overweight people did — enough to burn 350 calories, or about one cheeseburger. Fidgeting, standing, and puttering may even keep you off medications and out of the doctor's office. Think of your body as a computer: As long as you're moving the mouse and tapping the keys, all systems are go. But let it idle for a few minutes, and the machine goes into power-conservation mode. Your body is meant to be active, so when you sit and do nothing for too long, it shuts down and burns less energy. Getting consistent activity throughout the day keeps your metabolism humming along in high gear. When you get out of your chair and start moving around, you turn on fat burners. Simply standing up burns three times as many calories as sitting down, according to Levine. And, he adds, "NEAT activity can improve blood flow and increase the amount of serotonin available to the brain, so that your thinking becomes sharper and you'll be less likely to feel depressed." Shake things up throughout the day by interrupting your sedentary stints as often as possible. "Stand up every half hour," says Neville Owen, Ph.D., of the University of Queensland. "If you have to sit for longer than that, take more extended and active breaks and move around for a few minutes before sitting back down." When you're reading e-mail and taking phone calls, do it standing. Walk with colleagues to brainstorm ideas. And consider trading your chair for a large stability ball. "It forces you to engage your muscles, and you're likely to stand up more because you're not melting into a chair," Lentz says. At home, it's simple: Limit TV time to two hours a day or less. Better yet, watch it from a treadmill or exercise bike. Among women, the risk for metabolic syndrome — a constellation of health woes including high blood pressure, high cholesterol, and high blood sugar — shoots up 26 percent for every hour per day they spend watching the tube. Not sure how much of a difference these mini moves will make? Swapping a more active approach for just a few of your daily activities can help stave off the one-to two-pound weight gain most women accumulate every year — and it can keep your metabolism buzzing the way nature intended it to.
-
The COMTRANS int'l commercial vehicle show is held every two years at the Crocus Expo Centre in Moscow. The show is held on the odd number years, alternating with the global IAA commercial vehicle show in Hannover, Germany.
-
House bill would increase Interstate weight limit to 91,000 pounds
kscarbel2 replied to kscarbel2's topic in Trucking News
New bill would permit 91,000-lb. rigs with extra axle Fleet Owner / September 11, 2015 Pointing to productivity and safety benefits, Rep. Reid Ribble (R-WI) announced Thursday that he will introduce legislation to allow 91,000-lb., six-axle tractor-trailers on the federal interstate highway system. The Safe, Flexible and Efficient Trucking Act (Safe Trucking Act) will be offered as an amendment to the surface transportation reauthorization, or highway bill, expected to be taken up in the House Transportation and Infrastructure Committee (T&I) next week. Speaking on a teleconference with members of the news media, Ribble explained the extra axle would distribute the weight load and actually improve braking power, compared to a 5-axle rig at 80,000 pounds. And current infrastructure standards can support 91,000-lb., six-axle loads without additional “rehab costs” to Interstate bridges, based on a “deep dive on the data” in the recently released DOT truck size and weight study. Additionally, he expects an increased weight limit on federal interstate highways would shift some truck traffic away from those state highways where higher limits are currently permitted. “For me, it’s not just about productivity, but it’s the increased safety by having fewer trucks moving more product in a safer manner,” Ribble said. “Our roads are already heavily crowded. This 13% increase in capacity is heavily significant in moving more freight with fewer vehicles. This would also result in reduced fuel costs and CO2 emissions.” He cited the immediate benefits to Wisconsin’s paper mills as an example of improved freight efficiency with heavier trucks. Indeed, the congressman’s remarks were followed by representatives from a variety of industries that contend the truck weight increase would aid global competitiveness. American Forest & Paper Assn. President and CEO Donna Harman, who noted that competitors in Canada and Mexico already benefit from higher truck weight limits, said that the number of truck trips for forest products could be reduced by approximately 1.4 million each year under Ribble’s bill. More specifically, Connie Tipton, president and CEO of the International Dairy Foods Assn., said that a 5,000-truck dairy fleet could serve its 150,000 delivery locations with 500 fewer trucks. James Sembrot, senior director of transportation at Anheuser-Busch InBev, called the Safe Trucking Act “common sense policy that everybody can support,” and explained that his company ships more than a million truckloads of beer and raw materials each year—and many of those trailers are 60% empty due to the current weight restrictions. The 91,000-lb. limit would permit Anheuser-Busch to take 100,000 trucks a year off of the highway. He also estimated the cost of adding a sixth axle would be about $7,400 per trailer. The Coalition for Transportation Productivity (CTP), a group of 200 manufacturers, shippers, carriers and allied associations whose primary aim is to support such legislation, organized the press conference. “Truck travel has grown 22 times faster than road capacity since the federal weight limit was last changed in 1982,” said John Runyan, executive director of CTP. “Recognizing that more than 70 percent of freight must be shipped by truck, we need to confront the highway capacity crunch now if our country is to remain competitive. The Safe Trucking Act safely improves the productivity of truck shipments so we can decrease the truckloads necessary to meet demand and make our entire transportation network more efficient.” That the 6-axle configuration is “bridge-formula compliant” and actually saves money on pavement restoration makes the bill “a game changer,” Runyan added. He also pointed out that the legislation would allow DOT to specify additional safety equipment for any trucks operating at the 91,000-lb. limit. “They have the ability to make this a world-class truck for the movement of heavy goods, if they so choose,” Runyan said. Ribble explained that the bill will be offered as an amendment to the highway bill, noting that T&I Chairman Rep. Bill Shuster prefers the base legislation to be as “clean” as possible to garner bipartisan support. And Ribble conceded his bill will face opposition, both from the rail industry and some highway safety groups. But, he suggested, the 91,000-lb. limit should be more acceptable than previous attempts at a 97,000-lb. limit. The Coalition Against Bigger Trucks has led the opposition on those previous attempts, but those efforts came under scrutiny earlier this year when a New York Times investigation revealed that the rail-backed group was paying law enforcement officers to lobby Washington legislators about potential dangers of longer and heavier trucks. Still, his bill shouldn’t be about trucks vs. rail, Ribble noted. “This is as old as rail is, and they’re going to continue to oppose anything that might affect competition in the marketplace,” Ribble said. “That’s to be expected, but we believe they have a strawman argument, based on how goods and services are moving about the county right now.” Ribble also emphasized that his bill shouldn’t be confused with legislation that would increase twin-trailer length from 28 feet to 33 feet. Such legislation is attached to a pending bill to fund the DOT, and the trailer provision faced vocal opposition from Democrats in both the House and the Senate (where the rider made it out of committee by a single vote). Supporters of the longer trailers have emphasized that the configuration is safe because the combination does not add any weight, while Ribble made the case the heavier trucks are safe because they are not longer, under his bill. “We don’t touch the size of the trucks at all,” Ribble said. “Different groups and different organizations, whether for or against, will make their case as it relates to vehicle size, but I deliberately didn’t address it in this bill because I didn’t want to go down that rabbit trail.” Still, the Coalition for Efficient & Responsible Trucking (CERT)—which backs longer trailers—on Thursday issued a notice to address the “misleading language” of the opposition, who are "doing everything possible to undermine proposals to make freight transportation safer and more efficient.” CERT was responding to a recent CQ Roll Call report ("Ribble Bill Would Add Trucks' Weight to Debate on Length") in which a spokesman for the Advocates for Highway and Auto Safety “conflates” the separate issues of truck length and weight, and contends there’s a “significant overlap” in the membership of CERT and CTP—and “they all want bigger and heavier trucks.” CERT rejected the claim, and said the two organizations do not share any common member companies. And, to complicate matters, a lot of truckers don’t like the idea of heavier trucks, either. The Owner-Operator Independent Drivers Assn. (OOIDA) reiterated its objection Thursday, saying the 91,000-lb. limit doesn’t overcome the problems with 97,000-lb. rigs. OOIDA Executive Vice President Todd Spencer called the proposal “a dumb idea on every level.” OOIDA contends the bill just provides an interim step to the higher limits, and that these limits are to benefit shippers and a just few large carriers. Ribble said the T&I leadership would meet Friday to finalize a schedule for introducing its highway bill, with the tentative plan calling for a Thursday, Sept. 17 date for committee mark-up. -
Bloomberg / September 11, 2015 Daimler AG said it expects demand for trucks and buses in Brazil to plunge as much as 50% this year as the crisis in South America’s largest economy gets worse. The market in Brazil, struggling to overcome a crippling recession, will need one to three years to return to growth, Wolfgang Bernhard, head of Daimler’s commercial-vehicle unit, said at the Hamburg club of business journalists late Sept. 10. “We expect to continue hibernating,” Bernhard said. Industrywide truck sales plunged 44% in the first half of the year, the Stuttgart, Germany-based company said in August. Brazil is one of several markets in which “there’s a strong, very cold headwind,” he said. Brazilian bond and equity markets tumbled Sept. 10 after Standard & Poor’s cut the country’s credit rating to junk with a negative outlook. Daimler already has shrunk its Brazilian workforce by about 3,000 jobs under a two-year reorganization and in August announced reduced working hours at its local truck-making division. The company will invest in new products in Brazil despite the downturn because it sees long-term potential in the country, Bernhard said. Daimler has been able to restore market share despite the crisis, becoming the country’s biggest seller of trucks again, he said. “This may not be a sign of spring, but it shows that our team managed to cope with that difficult environment,” Bernhard said. The company operates two truck- and bus-building plants in Brazil and is setting up a factory to start making passenger cars there next year. It employed about 12,000 people in the Latin American country at the end of 2014.
-
New Zealand Herald / September 13, 2015 In a swiftly moving case, Wellington police are investigating an allegation of industrial espionage within the country’s food industry. The New Zealand Herald understands the case involves allegations that a recent temporary help American truck driver working at night part-time at Sanitarium Health and Wellbeing Company’s factory and headquarters in Auckland as a forklift operator took inside information on the manufacture of the company’s Marmite food spread just before abruptly returning to the United States. Wellington Police Chief Tim Barfield said inquiries began several weeks ago after police were approached by a Sanitarium representative. "Police can confirm that there is an investigation under way but it is in its early stages," he said. “Exercising treaty laws between New Zealand and the United States, we are moving forward to extradite the suspect back to New Zealand for questioning.” American counsel for the man under investigation, Timothy Maikshilo, refused to make any comment to the New Zealand Herald. Marketing Manager Mark Roper of Sanitarium’s New Zealand operation stated "We have a witness who will testify that Maikshilo plans to replicate and produce our Marmite product for retail distribution in the United States.” Roper would not say how long Maikshilo had been with the company or what information he was alleged to have taken. "There's an ongoing police investigation and I'm afraid that I can't comment on it at all other than to agree with the police that there is an investigation ongoing and that's all I can say right now," Roper said. .
-
Man murders three brothers, kills self ABC News / September 13, 2015 Three brothers were shot to death by a man who then killed himself in a rural area of Louisiana outside Baton Rouge early Sunday. The East Baton Rouge Parish Sheriff's Office said the men were found dead in a driveway after an argument broke out at about 12:30 a.m. Sheriff's office spokeswoman Casey Rayborn Hicks said the men were watching football and listening to music at a neighbor's house when they got into an argument over the music. The shooter was identified as Rodney Chemin, 60, and the three brothers as Joseph Allen, 57; Perry Allen, 55 and Mark Allen, 51. The four men were found dead outside Chemin's house.
-
Father murders wife and children, kills self Associated Press / September 12, 2015 A Minnesota father used a shotgun to kill his wife and three children before turning the gun on himself. Brian Short killed his wife, Karen, and their three teenage children in their Greenwood home late Monday or early Tuesday. "All evidence indicates Brian Short killed his family members in their bedrooms before turning the gun on himself," the department said in a news release. Officers found the dead family members Thursday during a welfare check at their home. A co-worker of Brian Short told police they hadn't been heard from in days. The children hadn't reported to school since it resumed on Tuesday. Police found Karen Short, 48, and the three children — Cole, 17, Madison, 15, and Brooklyn, 14 — dead in their bedrooms. Brian Short, 45, was found dead in the home's eight-car garage. The Hennepin County medical examiner ruled Saturday that all five died from shotgun wounds to the head and that only Brian Short's wound was self-inflicted.
BigMackTrucks.com
BigMackTrucks.com is a support forum for antique, classic and modern Mack Trucks! The forum is owned and maintained by Watt's Truck Center, Inc. an independent, full service Mack dealer. The forums are not affiliated with Mack Trucks, Inc.
Our Vendors and Advertisers
Thank you for your support!