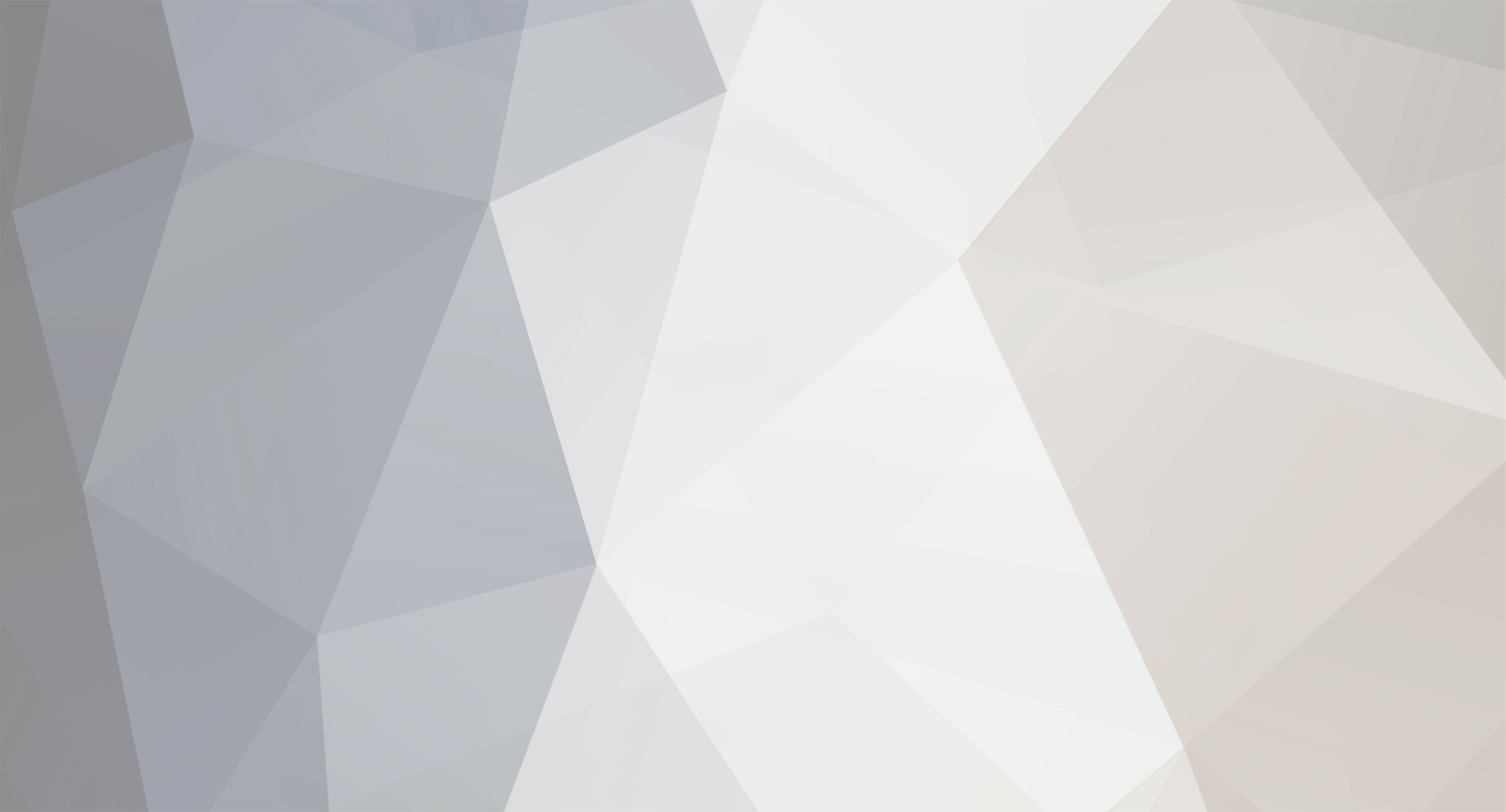
kscarbel2
Moderator-
Posts
18,767 -
Joined
-
Days Won
114
Everything posted by kscarbel2
-
When Chevrolet's Titan 90 ran like a Deere
kscarbel2 replied to kscarbel2's topic in Other Truck Makes
Detroit chips in with an overhead camshaft six Commercial Motor / March 14, 1987 Over the past decade Detroit Diesel Allison — General Motors' diesel engine and automatic transmission-manufacturing subsidiary — has seen its share of the North American Class Eight (top weight on-road truck category) engine market dwindle away almost to nothing. Of the 130,000 or so Class Eight vehicles which were sold in North America last year, only 5% had Detroit Diesel engines. Once DDA would have been disappointed if its market share had dropped below 30%. DDA's vee-eight and vee-six twostroke engines never found favour with European operators, mainly because of their poor fuel consumption. Now they have suffered a dramatic decline in popularity among American operators too, primarily because of reliability problems associated with water leaking into the lubricating oil. GM has now restructured its diesel engine division, merging it with the diesel engine business of agricultural equipment manufacturer John Deere to form a 50/50 joint venture company which is to be called Dedec (Detroit Deere Corporation). It has also introduced an all new truck engine which has taken seven years to develop and is designed to leapfrog its competitors, chiefly Cummins and Caterpillar, in technical innovation, performance and market share. Donovan Downham, Dedec's vicepresident of sales and marketing, is confident that the new engine, designated Series 60, will capture "at least 22% of the US heavy duty diesel market in the next five years." Dedec's plans for selling the Series 60 engine in Europe are less clear, but there is no doubt that it will become available here. Floor, the Dutch specialist vehicle builder, has one of two Series 60 prototypes which have been shipped to Europe. Foremost among the other European vehicle manufacturers who are at least potential customers for the Series 60 engines are ERF, Foden, Seddon Atkinson, Kassbohrer and Perlini, the Italian manufacturer of on/off-road trucks. Another surprising name on the list of possible customers for the new engine is Dal (and Leyland Oaf). The Dutch manufacturer needs an engine to take it into the 300kW-plus onroad truck sector which is becoming increasingly important in Europe, and its own 11.6 litre engine, with a maximum power rating of 270kW (360hp) would probably be unduly stretched at much higher ratings. The Series 60 engine could provide Daf with a more costeffective option than a new engine development programme. In the USA truck manufacturers who are already fitting Series 60 engines in their Class Eight models include Freightliner (owned by Daimler-Benz), Kenworth and Peterbilt (part of Paccar) and Volvo White, in addition to GM's own truck-building division, GMC. There are two displacements in the Series 60 family: 11.1 and 12.7 litres. The larger engine has a 15% longer stroke than the 11.1 litre unit, sharing its 130mm bore and all but eight of its component parts. Unlike earlier Detroit Diesel engines this one is built to metric dimensions and, unlike the 71 and 92 Series Detroit two-strokes — which will remain in production — its designation bears no relation to its swept volume in cubic inches. All Series 60 engines are in-line, six cylinder, turbocharged and air-to-air charge-cooled four-strokes. Uniquely, for an engine of this size and type, the Series 60 has a gear driven overhead camshaft, and it is the first diesel engine of any type to go into full production with a fully electronic control system for its fuel injection equipment as standard. The DDEC (Detroit Diesel Electronic Control) system became an option on vee-six and vee-eight 92 Series twostroke engines in 1985 (CM August 24). NEW STANDARDS The engineers who designed and developed this engine say their objective was to set new standards in fuel economy, reliability, durability, noise level, and exhaust emissions. It is in the first and last of these areas that the electronic control of both fuel metering and injection timing plays a crucial role. For all twelve US variants of the new engine, with maximum power ratings from 186kW (250hp) to 298kW (400hp) at speeds of 1,800 and 2,000 rpm, Dedec's performance curves show that in terms of full load minimum specific fuel consumption the Series 60 matches, or in some cases is slightly ahead of the most fuel-efficient truck engines which are currently on the market, Like some versions of the Cummins 10 litre engine, Gardner's 12.7 litre 6LXDT and the latest Perkins Eagle 12.17 litre, the Series 60's SFC dips as low as 189 g/kW-h (0.311b/hp-h). Significantly, it does so while comfortably meeting the current US Federal and even the more stringent Californian limits on diesel engine exhaust emissions. "This is a 50-state engine," says David Merrion, Dedec's vice-president of product engineering. He is also confident that by 1991, when even tougher emissions limits come into force in the USA, including a new limit on particulates emission, the Series 60 will be able to meet them without the bulky exhaust systemmounted particulate traps which all diesel engine manufacturers are currently experimenting with. Some Dedec engineers believe that without such severe exhaust emission limits the Series 60 could break the 183g/1W-h (0.30Ib/hp-h) barrier, which would certainly put it ahead of all other production truck diesel engines. As it stands, the Series 60 is claimed to give on-the-road fuel economy ranging from two to 15% better than any of its current US competitors. When development work started on the Series 60, in 1980, it was intended that it would only be made in 11.1 Litres capacity. As the demand for power outputs above 261kW (550hp) steadily increased during the early eighties, however, DDA's engineers reached the conclusion that they would need a larger capacity to satisfy this demand without compromising durability — all Series 60 engines are intended to cover 800,000km (500,000 miles) before requiring a major overhaul. Merrion says the reason for not simply derating the 12.7 litre unit for power outputs below 261kW is that the penalty in fuel consumption caused by the parasitic losses of the bigger engine would be about 3% worse than with the 11.1 litre unit. Increasing the swept volume of the 12.7 litre engine for still higher power outputs has already been considered. There is enough space between the engine's wet cylinder liners for a larger bore version to give a swept volume of around 13.7 litres, and it is this engine in which DAF has shown particular interest. http://archive.commercialmotor.com/article/14th-march-1987/24/detroit-chips-in-with-an-overhead-camshaft-six -
When Chevrolet's Titan 90 ran like a Deere
kscarbel2 replied to kscarbel2's topic in Other Truck Makes
"In the early 1980s Detroit Diesel, then still a division of General Motors had a 3.2 % market share and was hemorrhaging money. The two stroke engines they were then building which were technologically similar to the engines Deere used in the 435 and 8020 tractors were unlikely to ever meet the new emissions standards that were coming. So Detroit Diesel approached John Deere who was having its own struggles due to the 1980s farm economy, about merging engine building operations. Plans and negotiations soon began. 4000 to 5000 GM workers would be assigned to the new company along with another 2000 from Deere. Company headquarters would be in Detroit and the Redford Township engine plant and Romulus parts distribution and engineering center would also be used. All of the other Detroit Diesel operations such as those building engines and Allison transmissions for light trucks as well as locomotive engine operations would not be affected. Deere plants affected would be the engine facilities in Waterloo, Dubuque and Saran, France. Things progressed to enough of a degree that in March of 1987, a few brochures and ads were printed that included the new company’s name, Detroit Deere Corporation. However being a deal was finalized, Roger Penske who a few years earlier had purchased Hertz Truck Leasing and was Detroit Diesel’s largest customer sent a team who along with GM’s John Farmer put together a 700 million dollar deal in a matter of weeks with General Motors holding 20% of the note for 10 to 15 years. The Romulus site was sold off and Allison Transmission was kept by GM, at least for awhile. Penske’s group also hammered out a new contract with the UAW that markedly decreased absenteeism and grievances. The new Detroit Diesel then went full speed ahead with production of the Tech 80 engine developed by Arn Vanderbock. That engine was later named the 60 series and market share soon climbed from 3% to 35%." --------------------------------------------------------------------------------------------------------------------------------- Detroit series 60 was developed by Mr. Arn Vanderbock who was an engineer at Cummins. He proposed it to Cummins. They declined. He came over to Detroit Diesel. https://talk.newagtalk.com/forums/thread-view.asp?tid=685481&DisplayType=flat&setCookie=1 -
Dual-clutch gearbox complaints haunt Ford Michael Martinez, Automotive News / July 1, 2019 The Ford Focus and Fiesta are fading away in the U.S., but the headaches caused by the small cars' PowerShift dual-clutch transmissions live on. Ford Motor Co. never conquered the long-term reliability problems on the gearboxes that thousands of customers complained would shudder, jerk and hesitate. Although engineers helped solve some early glitches with software updates and redesigned parts, Ford issued more than 20 technical service bulletins related to the transmissions, which were code-named DPS6. In 2014, Ford extended the transmissions' warranty by two years and 40,000 miles. Litigation over the transmissions remains unresolved. Ford reached a settlement in 2017 for a class-action lawsuit covering 1.9 million owners, but the settlement is being challenged in a federal court in California on the grounds that not enough owners would be compensated. A separate mass-tort case involving thousands of customers is pending in Michigan. Former Ford CEO Mark Fields has been ordered to testify by July 31 in a series of cases involving customers who opted out of the class-action suit. A Florida judge last month denied Fields' motion to avoid testifying. Ford also has been forced to pay up around the world; last year it lost a class-action lawsuit in Thailand and separately was fined $10 million by a court in Australia. "They have a major PR and customer-satisfaction nightmare on their hands," Gabe Shenhar, associate director of the auto test program at Consumer Reports, told Automotive News. "It's still not well sorted out." Customer complaints Ford introduced the six-speed PowerShift transmission in 2010, playing up the gearbox's fuel-economy benefits. But customers soon began complaining about jerkiness and a lack of power, and the transmission — along with the troublesome MyFord Touch infotainment system — contributed to Ford's plunge to No. 20 in Consumer Reports' 2011 reliability survey from 10th the previous year. Many customers weren't used to the dual-clutch gearbox, incorrectly assuming it would behave like a regular hydraulic automatic transmission. The PowerShift used two dry clutch packs in place of a normal automatic torque converter, which tended to make buyers think the car wasn't properly accelerating. On the reliability front, the clutches would overheat and often showed signs of premature wear. Ford made some changes in 2012 that it believed would solve most of the problems, but complaints continued. The company also directed dealers to make fixes that often included replacing clutches and updating the transmission control module. "They made it marginally more palatable, but each update came with some loss of fuel efficiency and power," Shenhar said. "Customers weren't happy." The warranty extension Ford eventually offered was a "pretty clear conclusion" it didn't have a permanent fix, Shenhar said. Angry customers have turned to the courts, arguing that Ford knew about the defects but sold the vehicles anyway and then blamed owners for not driving them properly. Although Ford reached a settlement in 2017 that would give customers $2,325 if they opt in and meet certain qualifications, that settlement is being challenged by groups that argue the deal would let Ford off the financial hook. The automaker's lawyers argued to keep the settlement in front of three appeals judges in April. An answer is expected by December. The automaker, in a statement, said it does not comment on pending litigation but is committed to providing top-quality vehicles for its customers. "We continue to deny the allegations in this lawsuit, but rather than continuing with the litigation, Ford entered into a settlement agreement with lawyers representing these plaintiffs," the statement said. "That settlement is fair and appropriate and we look forward to final court approval." Fields testimony A number of customers opted out of the class-action lawsuit, and their suits have been combined into a federal case in California. That's where Fields comes in. The former CEO was Ford's president of the Americas when the cars with the dual-clutch transmissions were launched. "The deposition is critical to investigating and confirming that Ford's executives at the highest level knew of the problems with the transmissions and intentionally concealed that information and sold the Focus and Fiesta to the public anyway," Russell Higgins, an associate attorney at Knight Law Group, which represents a number of individuals in the case, told Automotive News. Fields, who was replaced by Jim Hackett in May 2017, is a senior adviser at TPG Capital, a global asset management firm. "Mr. Fields is sort of where the buck stopped in terms of corporate knowledge," Higgins said. "It's important to have him be able to talk about his actions and what he knew."
-
I’ve been saying for years that we need to connect with them. I’ve dealt with them......they’re no different from us.
-
When Chevrolet's Titan 90 ran like a Deere
kscarbel2 replied to kscarbel2's topic in Other Truck Makes
Well now I didn’t know that. Very interesting. -
When Chevrolet's Titan 90 ran like a Deere
kscarbel2 replied to kscarbel2's topic in Other Truck Makes
Mr. Hancock pegged it. --------------------------------------------------------------------------------------- July 21, 1986 General Motors and Deere & Company have signed a memorandum of understanding to form a joint venture to design, manufacture and distribute diesel engines worldwide, the companies announced recently. The proposed corporation would be held equally by both parent companies. The agreement is subject to final negotiations and clearance by the federal antitrust authorities. The joint venture will include the diesel engine operations of Deere & Company and the Detroit Diesel Allison Division of General Motors (DDA). F. James McDonald, president of General Motors, and Robert A. Hanson, chairman and chief executive officer, Deere & Company, issued this joint statement: "General Motors and Deere & Company believe this proposed joint venture is a very positive step for the diesel engine operations of both companies. The new organization will allow us to provide a full line of products that will benefit from combined resources in both technology and economies of scale in manufacturing. These advantages, coupled with a strong distribution network and the considerable experience of management and production personnel from both companies, give us confidence that the new company will play a leadership role in the diesel industry." Officials predict annual sales of about $1.5 billion for the new company. The new company is yet to be named and will be headquartered in the Detroit area. Senior management will be drawn from both GM and Deere. It is expected that the new firm will be in operation under its new name and management by January 1,1987. The joint venture will utilize diesel engine facilities in the Detroit area presently operated by Detroit Diesel Allison Division of General Motors. These include the Redford heavy-duty diesel engine plant, the Romulus Parts Distribution Center and the Romulus Engineering Center. Also included will be the tools and machinery used to manufacture the Detroit Diesel 8.2L medium-duty engines now being built by GM's Chevrolet-Pontiac-GM of Canada (CPC) group which recently acquired DDA's Romulus diesel engine manufacturing facility. The 8.2L engine will be a part of the new joint venture's line. The Deere & Company facilities to be utilized include the Waterloo, Iowa, diesel engine plant and a diesel engine plant in Saran, France. Engines will also be provided from the Dubuque, Iowa, factory, which will continue to be part of Deere & Company. These three facilities supply engines for John Deere agricultural and industrial equipment as well as for use by other customers in marine and industrial applications and generator sets. All other DDA operations will remain with GM, and other operations of Deere & Company will be unaffected. The combined product line gives the new company a complete range of diesel engines from 50 hp to 2,000 hp, with a wide variety of configurations to meet virtually every application need. Detroit Diesel Allison has been marketing the John Deere line of diesel engines through its worldwide sales organization for the past year, under an earlier agreement. The two companies also have been cooperating under a technical agreement for joint engineering efforts on new products. These actions have provided continuity and direction while the joint venture has been under study. -
Good on Trump. .
-
100 Years Limited Edition Mack.
kscarbel2 replied to Hayseed's topic in Modern Mack Truck General Discussion
I disagree, because I was there and know. We needed a partner. And as John Curcio accurately stated of Renault, "They came to the party in 1983 when nobody else loved us." Elios Pascual was as fine an individual as you could every know, and he cared about Mack Trucks. -
When Chevrolet's Titan 90 ran like a Deere
kscarbel2 replied to kscarbel2's topic in Other Truck Makes
The 151 cubic inch (2.5-litre) in-line four cylinder Pontiac "Iron Duke" was also the standard engine in the Jeep CJ5, CJ-7 and CJ-8 for four years over the 1980-83 period. -
Had a wonderful conversation over lunch this week with a former Chevrolet heavy truck distributor who recalled when General Motors decided to offer the Chevrolet Titan 90 (and I assume the GMC Astro) with John Deere power. The former dealer principal ordered one unit for himself, and a second unit for the local John Deere dealer who was a friend. The trucks were received and the two buyers were thrilled with their new trucks and "green" powerplants. However, after a short time, General Motors contacted the dealer owner and explained that the plan to offer Deere power had been cancelled, and as a result they had to return the two trucks.....which they reluctantly did. Has anyone else in the BMT universe heard about this moment in American truck history ?
-
The Guardian / June 28, 2019 When Gary George bought a truckload of videotapes for $218 from a US government surplus auction more than 40 years ago, he planned to sell them to television stations – to record over. Fortunately, he decided to hold on to the three tapes labelled “Apollo 11 EVA”, which have since been identified as the only surviving original recording of the first moon landing, in 1969. Now the tapes – which include Neil Armstrong’s famous words “That’s one small step for man, one giant leap for mankind” – are to go on sale in July at Sotheby’s in New York, where they are expected to fetch as much as $2m. The collection also includes footage of Buzz Aldrin walking in minimal lunar gravity, planting the US flag on the moon, collecting samples. It also shows the crew’s call with Richard Nixon. George, now 65, was astonished. “I had no idea there was anything of value on them,” the retired mechanical engineer from Las Vegas told Reuters. “I was selling them to TV stations just to record over.” George thinks he sold eight reels to television stations for $50 each. It was his father who spotted the three Nasa labelled reels. “He was really into the space program and he said, ‘I think I’d hang on to those. They might be valuable someday. So, for that very reason, I pulled them out and hauled them around the country for the next 43 years. That’s how come they survived.” In 2006, Nasa admitted that they could not find the original video recordings of the landing. It was not until two years later, when George was on holiday with a friend who worked at Nasa, that he found out they were looking for them. He did not have the equipment to watch the tapes, but after he started speaking to Nasa about handing them over he was able to see the footage for the first time in a special studio in California.
-
VW's Traton shares limp on stock market debut Reuters / June 28, 2019 FRANKFURT - Traton made a lacklustre start on its debut on Friday, as shares in Volkswagen's truck unit slipped below their initial public offering price. The stock opened at 27 euros ($30.75), the IPO price in Europe's second-largest listing of the year, before slipping to trade as much as 2.4 percent lower. Germany's benchmark DAX index was up 0.5% at 1200 GMT. Weak demand for German listings had forced VW to scale back its Traton IPO and it had already priced the offering at the low end of its target range. "At first glance, markets don't look that bad. But volumes have been low as risk averse investors hoard cash," a banker working on the deal said. The average daily turnover of Stoxx600 shares stood at 470 billion euros so far this year and the June median was 439 billion euros, compared with the 2018 daily average of almost 600 billion. Global IPO volumes are down 30% in the year so far, Refinitiv data shows, while the European figure is at its lowest level since 2012 amid concern about the global economic outlook. Volkswagen floated 11.5% of Traton's shares after initially seeking to list a stake of up to 25% in a bid to put the company's truck business on an independent footing. The deal values Traton at 7.9 and 7.0 times its 2019 and 2020 earnings before interest and taxes, respectively, roughly in line with the valuation of its peer Volvo, two people close to the matter said. The 1.55 billion euros ($1.77 billion) in proceeds from the offering will flow to parent Volkswagen which aims to use the funding to invest in mass producing electric cars. Traton, which includes the MAN, Scania and Volkswagen trucks businesses wants to create a global trucks operation. A flotation could give Traton the resources to deepen its relationship with U.S. truck maker Navistar International Corp , in which it owns a 16.85% stake. Asked whether Volkswagen planned to buy out Navistar, Chairman Hans Dieter Poetsch said: "Today's steps make many things possible. Currently there are no concrete plans." Traton Chief Executive Andreas Renschler said alliances with Navistar, Hino and Sinotruck gave Traton economies of scale. "We don't need any further participation at all, there's no need to always buy companies," he said. ($1 = 0.8780 euros)
-
100 Years Limited Edition Mack.
kscarbel2 replied to Hayseed's topic in Modern Mack Truck General Discussion
-
1990 Mack MS250 Garbage Packer
kscarbel2 replied to j hancock's topic in Antique and Classic Mack Trucks General Discussion
Absolutely fantastic. If everyone here could only know how important and successful the Mid-Liner ranger was to Mack Trucks.......the right product at the right time. We sold thousands to Penske, Ryder and countless other fleets from coast to coast. -
Ford to slash 12,000 jobs in Europe by 2020 Edward Taylor, Reuters - Bloomberg / June 27, 2019 FRANKFURT -- Ford Motor Co. said it will have cut 12,000 jobs in Europe -- about 20 percent of its overall workforce there -- by the end of next year to try to return the business to profit, part of a wave of cost reductions in an auto industry facing stagnant demand and record-level investments to build low emission cars. Ford said it has ceased production at three plants in Russia, is closing plants in France and Wales, and has cut shifts at factories in Valencia, Spain and Saarlouis, Germany. The cuts will reduce its manufacturing footprint in Europe from 24 plants down to 18. Approximately 12,000 jobs will be impacted at Ford’s wholly owned facilities and consolidated joint ventures in Europe by the end of 2020, primarily through voluntary separation programs, the automaker said in a statement released on Thursday. The challenge of investing in electric, hybrid and autonomous vehicles -- while having to overhaul combustion engines to meet new clean-air rules -- has forced Europe's carmakers to slash fixed costs and streamline their model portfolios. "We have largely concluded consultations with social partners regarding restructuring actions," Stuart Rowley, president, Ford of Europe told Reuters. Around 2,000 of the jobs to be cut are salaried positions, which are included among the 7,000 salaried positions Ford is reducing globally, the carmaker said. The rest are workers on hourly contracts or agency workers. Ford Europe has 51,000 employees in Europe or 65,000 when joint ventures are included. In January Ford announced a sweeping business review that included the prospect of plant closures and discontinuing loss-making vehicle lines to pursue a 6 percent operating margin in Europe. Falling demand Demand for cars in Europe is falling. The European automobile manufacturers' association ACEA on Thursday predicted that European passenger car registrations will shrink by 1 percent in 2019 to 15 million cars, revising its previous forecast of 1 percent growth. Car sales will stagnate or decline in the next three years, AlixPartners said in a survey of the industry published this week. Manufacturers balancing sales of electric and combustion engined cars will see margins hit particularly hard, the survey said. Ford said it intended to double the profitability of its commercial vehicle business in Europe in the next five years, supported by a restructured Ford Sollers joint venture in Russia and a strategic alliance with Volkswagen Group. Earlier this year Ford said it would seek to exit the multivan segment and focus on developing electrified versions of more profitable "crossover" and SUVs. European passenger vehicle development, including for battery electric vehicles, will be centered in Cologne, the carmaker said. Ford also said it expected to triple passenger car imports into Europe by 2024 by selling Mustang and Explorer vehicles, including a Mustang-inspired electric car in late 2020.
-
Mack Ultra-Liner Day Cab
kscarbel2 replied to j hancock's topic in Antique and Classic Mack Trucks General Discussion
You are right of course, the T2090 had a .71 overdrive........not .60 -
-
Mack Ultra-Liner Day Cab
kscarbel2 replied to j hancock's topic in Antique and Classic Mack Trucks General Discussion
Most likely a T2050 5-speed with a 0.60 overdrive top gear. As many times as I saw that truck in operation, it is painful to see it now in this state of disrepair. That MH Ultra-Liner is as modern as any truck today. -
Ford targets Power Wagen with new Super Duty Tremor package Michael Martinez, Automotive News / June 27, 2019 DETROIT — Ford Motor Co. is looking to cash in on the continued popularity of pricey pickups and stave off hard-charging Ram in the sales race with the Super Duty Tremor, an answer to Ram's off-road Power Wagon. The off-road package, unveiled Thursday, will reach dealerships in the fourth quarter along with other versions of the freshened 2020 Super Duty. It's available on XLT, Lariat, King Ranch and Platinum trims of the F-250 and F-350 with either the truck's new 7.3-liter V-8 gas or 6.7-liter diesel engine. The addition to Ford's formidable Super Duty lineup is meant to capture cash that customers would otherwise spend on aftermarket add-ons. Ford says some 70 percent of Super Duty customers accessorize their vehicles, sometimes spending tens of thousands on upgrades, and that roughly 15 percent of buyers upgrade the stock wheels and tires within six months of purchase. The Tremor package also helps shore up Super Duty's dominant market position, directly confronting a popular niche filled by second-place Ram. "Tremor balances what customers demand in terms of work with what they need in the great outdoors," Todd Eckert, Ford's truck group marketing manager, said in a statement. The trucks sit 2 inches higher in the front with a total of 10.8 inches of ground clearance to help slog through mud, water and uneven terrain. Ford says the pickups can navigate up to 33 inches of water, a best-in-class mark. The package comes with unique tires, wheels, suspension, shocks and dampers. It features trail control, also available on the F-150 Raptor and Ranger, and a unique rock crawl mode. Officials did not discuss pricing or power figures but said the Super Duty Tremor will have greater towing and payload than the Ram Power Wagon, although the figures will be slightly lower than for the standard Super Duty. The Tremor name will adorn the shocks and appear on the rear side of the pickup box. Brian Rathsburg, Ford's Super Duty marketing manager, said the package targets a different buyer than the F-150's Raptor performance variant. He said it represents "an enhanced version" of the company's FX4 off-road package that's available on the Ranger, F-150 and Super Duty. The FX4 and Tremor packages cannot be combined, and Rathsburg said Ford expects half of Super Duty customers to pick one or the other. "There's a recreation element to this," Rathsburg said. "We see it more of an evolution of the Super Duty customer as their lifestyle changes." .
-
Matt Cole, Commercial Carrier Journal (CCJ) / June 25, 2019 Daimler Trucks North America announced recently a recall of approximately 741 trucks due to the vehicles potentially having insufficient service brake air reservoir capacity, according to National Highway Traffic Safety Administration documents. DTNA says the affected trucks fail to comply with the Federal Motor Vehicle Safety Standard because to the issue. Insufficient air reservoir volume could reduce brake effectiveness, the company adds. Truck models included in the recall are: 2013-2019 Freightliner Cascadia 2005-2009 Freightliner Columbia 2014-2015 Western Star 4700 2015 Western Star 4900 2006 Western Star 6900 2013-2018 Freightliner 108SD 2014-2019 Freightliner 114SD 2014 Freightliner 122SD 2004-2005 Freightliner FL80 Business Class 2010 Freightliner FLD 2005-2017 Freightliner M2 2018-2019 Freightliner M2 Business Class 2005-2007 Sterling Acterra 2007 Sterling L7500 2006-2007 Sterling L8500 2004-2006 Sterling L9500 2007 Sterling LT7500 2007 Sterling LT8500 2005-2008 Sterling LT9500 Daimler will notify owners of affected trucks, and dealers will add reservoir capacity to the trucks. Owners can contact DTNA customer service at 1-800-547-0712 with recall number FL-815. NHTSA’s recall number is 19V-370.
-
Ford Trucks International Press Release / June 25, 2019 We are growing throughout Europe! Delighted to announce our brand-new facility in Slovakia! .
-
BigMackTrucks.com
BigMackTrucks.com is a support forum for antique, classic and modern Mack Trucks! The forum is owned and maintained by Watt's Truck Center, Inc. an independent, full service Mack dealer. The forums are not affiliated with Mack Trucks, Inc.
Our Vendors and Advertisers
Thank you for your support!