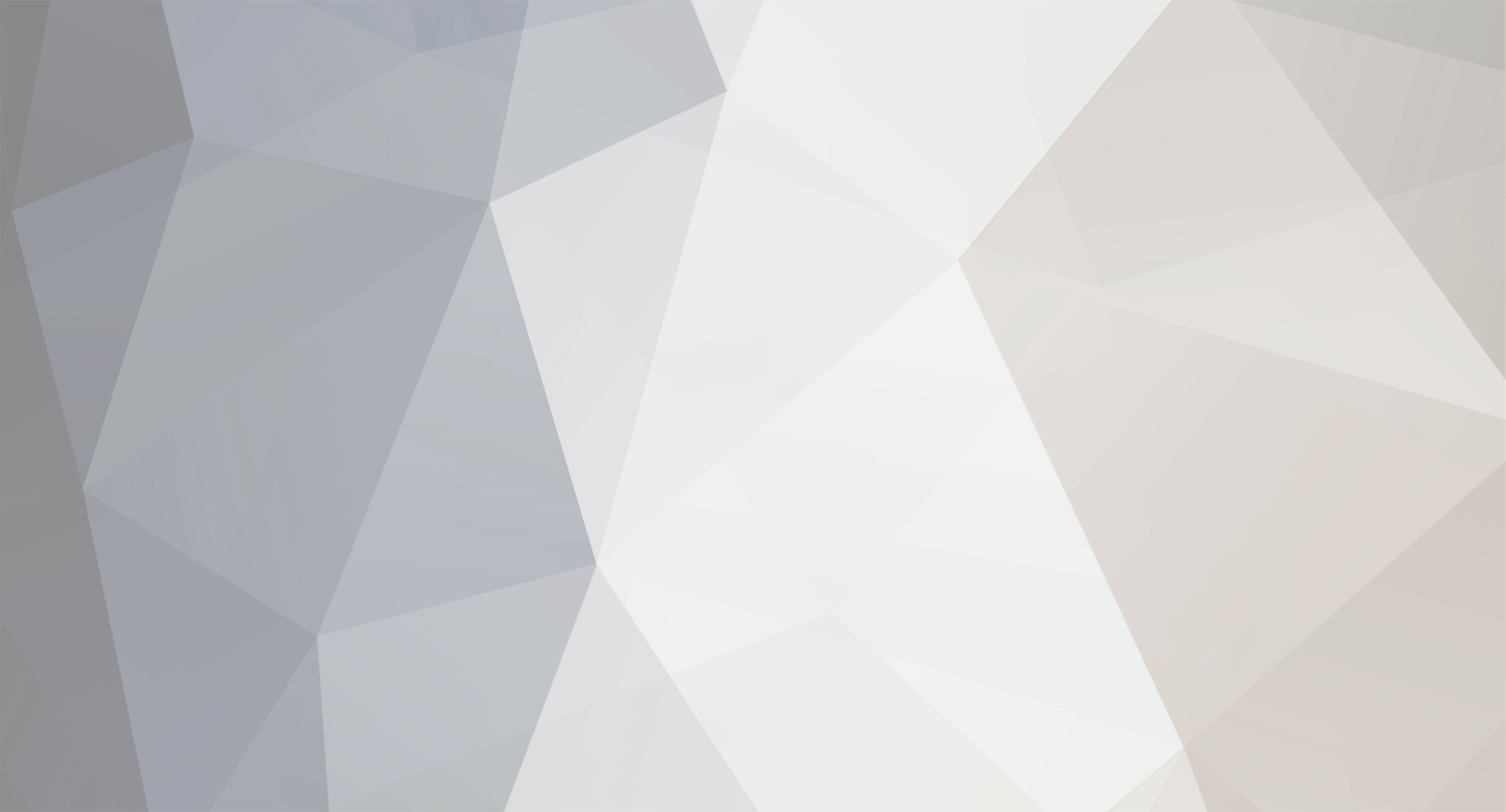
kscarbel
Pedigreed Bulldog-
Posts
1,114 -
Joined
-
Last visited
-
Days Won
8
Content Type
Profiles
Forums
Gallery
Events
Blogs
BMT Wiki
Collections
Store
Everything posted by kscarbel
-
Automotive News / December 9, 2013 DETROIT -- The U.S. Treasury today sold its last shares of General Motors stock, ending more than four years of government ownership in the nation’s largest automaker at a loss of about $10.5 billion to U.S. taxpayers. The government said in a statement that it recouped $39 billion of its original $49.5 billion investment into GM. Company executives and dealers say that the stigma of federal ownership, which earned GM the derisive nickname “Government Motors,” has hurt sales. “We will always be grateful for the second chance extended to us and we are doing our best to make the most of it,” GM CEO Dan Akerson said in a statement. “Continued investments, innovation, and job creation are just some of the 'returns' of a healthy GM and domestic auto industry. Our work continues uninterrupted, and we will keep our sights squarely on our customers and transforming the way we do business.” Talking to reporters at a press event in Detroit today, GM North America President Mark Reuss said he believes that the government’s exit could give GM a short-term sales lift and help its image in the longer term. “I think probably some people will begin to consider us right away, maybe the next day,” he said, acknowledging that truck buyers “probably” have been most turned off by GM’s government ownership. Reuss sent a Twitter message saying, “Free at last, free at last -- thanks to all of the hard work and those who gave us a chance.” Reuss said that GM has spent “four years on the fundamentals” to become a more nimble company with a stronger focus on making quality cars and trucks. Closing Chapter Treasury Secretary Jack Lew told reporters on a conference call: "This marks one of the final chapters in the administration’s efforts to protect the broader economy by providing support to the automobile industry." Lew said that the automotive industry has created more than 370,000 new automotive jobs since GM exited bankruptcy in the summer of 2009. “All three U.S. automakers are profitable, competitive, and growing,” he said. GM shares today hit their highest level since they began trading publicly three years ago, rising to $41.16 before closing at $40.90. The GM bailout was launched in late 2008 under President George W. Bush’s administration as part of the government’s broader, $421.8 billion Troubled Asset Relief Program, most of it to bail out lenders during the financial crisis. The funding was continued under President Barack Obama, which created an automotive task force to restructure GM and Chrysler. The government gave GM about $40 billion in loans in exchange or a roughly 61 percent equity stake in GM. The bulk of the money recouped by the government came through periodic stock sales, including GM’s $5.5 billion purchase of 200 million shares in December 2012. GM also made $6.7 billion repayment in 2010. The Treasury lost about $1.3 billion on its $12.5 billion investment in Chrysler when it sold its remaining shares in 2011. In a statement issued by the White House, President Obama said the bailout preserved about 1 million automotive jobs and helped to blunt the severity of the recession. "When things looked darkest for our most iconic industry, we bet on what was true: the ingenuity and resilience of the proud, hardworking men and women who make this country strong," he said. "Today, that bet has paid off. The American auto industry is back." GM has posted 15 straight quarters of profits since emerging from bankruptcy, racking up nearly $20 billion in net income.
-
Need help selecting transmission for new Granite
kscarbel replied to leegsr52's topic in Engine and Transmission
An advantage of Eaton's vocational AMTs is the ratios available to creep at various speeds by selecting any gear. Allison has so few gears, the driver has little choice and less control. -
Need help selecting transmission for new Granite
kscarbel replied to leegsr52's topic in Engine and Transmission
I actually have a great deal of experience with both the Eaton AMTs and Allison in actual use. But we won't go there. Anyone who disliked AMTs in low speed operation is probably thinking about the earlier (on-highway) UltraShift DM3 that used a centrifugal type clutch which engaged via engine speed. MUCH has changed since then. First, the latest Eaton UltraShift Plus AMTs uses an electric clutch actuator which now allows the clutch to engage at idle, which significantly improves low speed operation. The original UltraShift DM3 and the current UltraShift Plus are two different animals (I fault Eaton for not creating an altogether new name for the current product to avoid confusion). Second, Eaton now has an entire range of purpose-designed AMTs specifically for the vocational segment. http://www.eaton.com/ecm/groups/public/@pub/@eaton/@roadranger/documents/content/ct_243345.pdf You said something to the effect that if the clutch is constantly engaging and disengaging, then it is not smooth enough to stay in front of a milling machine unless you spec it with gears low enough to get the clutch fully engaged by 1 mph and keep it there, then you have no top end. For that scenario, Eaton offers the 11-speed VMS spec AMT (paving, ect.) with a 26.08 first gear. That ratio, combined with the specialized vocational software and the electric clutch actuator, results in smooth low speed operation. In reality, Eaton's vocational AMTs geared correctly will not engage and disengage the clutch. The driver selects the gear he wants and holds that gear. This disables upshifts and the clutch is engaged for slow speed curbing. Another advantage of Eaton's vocational AMTs is the ratios available to creep at various speeds by selecting any gear. Allison has such few gears, the driver has little choice. Eaton is winning vocational business from Allison every day because of the UltraShift Plus AMT's slow speed maneuverability. The Allison's "urge to move” makes it harder to control the vehicle, while the Eaton AMT has no such problem. And, having a 0.73 overdrive top gear, top end (speed) is in no way compromised. In fact, all Eaton vocational AMTs have a 0.73 or 0.74 top gear. As for clutches, the precise electronic clutch engagement of Eaton's AMT transmissions consistently results in longer clutch life, not shorter. Of course, different dump applications have varying requirements. And that's why Eaton offers 5 different vocational AMTs to ideally meet varying requirements. For example, I already mentioned the UltraShift Plus vocational 10 (VCS), 11 (VMS) and 13 speed (VHP) AMTs have 3 reverse gears, and the 18-speed (VXP) has 4 reverse gears. Compared to the Allison, the vocational UltraShift Plus AMTs are significantly cheaper, will give you a simpler installation with better chassis integration, and deliver lower maintenance costs and better fuel economy. The Allison will definitely burn more fuel while sitting in torque converter mode, unable to lock the converter. While it may not become overheated, it is still wasting energy. When I spec a municipal transit bus or residential refuse chassis, vehicles in stop-and-go operations, I spec an Allison transmission. But with school buses, the Eaton UltraShift HV medium duty AMTs come out ahead of the Allison with lower initial purchase cost, lower cost of ownership and superior fuel economy. -
Mack Trucks never produced HVAC systems. Evans (vendor 2790) produced the 3-speed R/U/DM heaters. Kysor of Byron (vendor 7979) produced an integral R/U/DM heater/air conditioner (Mini Brute) that was uniquely used in glider kit production, and was also available thru Mack dealers as a retrofit kit. Introduced in the early 1980s, Signet (vendor 3230) was the first integral heater/air conditioner for the R/U/DM. Red Dot (vendor 4379) later became the integral heater/air conditioner for the R/U/DM with a superior performing design. A Red Dot HVAC system also replaced the Signet unit in late model MH production. Red Dot was again chosen to supply HVAC for the CH/CL.
-
Are you spec'ing your heavy rescue Spartan chassis with independent front suspension? I believe the Oshkosh TAK-4 IFS is proprietary to Pierce, but the Timoney "Strider", Reyco Granning and AxleTech independent front suspensions get a lot of praise. AxleTech offers it all, coil spring, air spring or hydraulic strut. And Hendrickson offers a low cost IFS option with their DMX independent front suspension.
-
Air suspensions are designed and built by Hendrickson. I'm not sure if leaf springs now are coming from Dana, Hendrickson or both. Volvo announced on October 18 that production of the legacy Mack axles and carriers would return to the former Mack Truckss Hagerstown plant (now Volvo Powertrain). Meritor had produced the legacy Mack axles from 2004 (Dana from 1984 thru 2003). In order to get Volvo's business, ArvinMeritor (now simply known as Meritor) purchased Volvo's axle manufacturing unit in Lindesberg, Sweden in 1999 (for US$135 million). As Volvo so often does with vendors, the company promised Meritor unrealistically high volumes and in return demanded rock bottom pricing. Since that time, Meritor hasn't found the relationship particularly profitable. In the U.S., Meritor is all too glad to see Volvo take over legacy Mack axles and carrier production as they're not making much money. Volvo still depends on Meritor for axles in Sweden.
-
Replacing a camshaft in an FDM is a hassle. Front discharge has its place, and buying the struggling Savage appeared like an intriguing opportunity to Mack management at the time. But after the purchase, it quickly became apparent that Savage was not a mature company with a mature product. Parts was a nightmare. Rather than simply fit a Savage mixer with a Mack engine and transmission, Mack should have shut down Savage and had our engineers redesign the entire product resulting in a "pedigreed design" front discharge mixer worthy of the Mack name.
-
Mack Trucks purchased Savage Manufacturing Corporation in 1989, making it a Mack subsidiary, Mack Trucks of Utah (for tax reasons). The resulting Mack FDM-700 model (Front Discharge MIxer) was available in both mid-engined (behind the cab) and rear-engined versions (replacing the camshaft on a mid-engined model was a hassle). Faced with a variety of market challenges, the FDM did not become popular. Shifting gears in 1998, Mack decided to cooperate with Oshkosh and offer a Mack-powered version of the Oshkosh S Series front-discharge mixer (with a McNeilus drum - Oshkosh owns McNeilus). Oshkosh would assemble the trucks utilizing Mack powertrains. The new Oshkosh S-Series based Mack-badged truck was called the FCM (Front-discharge-Concrete- Mixer). As a result of the Mack-Oshkosh agreement, Mack discontinued production of the FDM in Utah and closed that plant, with production ending in September 1998. The Mack/Oshkosh tie-up ended when Volvo acquired Mack Trucks.
-
http://www.bigmacktrucks.com/index.php?/topic/2094-is-volvo-good-or-bad-for-mack-trucks/page-13
-
Next generation engines, axles and transmissions ???
-
The Wall Street Journal / December 2, 2013 WARREN, Mich. -- Universal Truckload Services, Inc. (NASDAQ: UACL) announced today that it will acquire the sole shareholder of Westport Axle Corporation from an international industrial group headed in Brazil by SM Brasil Participacoes S/A. Based in Louisville, Kentucky, Westport provides value-added warehousing and component distribution services to U.S. manufacturers of Class 4-8 trucks, RVs and super-duty trucks. Westport also machines and distributes steering knuckles and axle components for the automotive industry. For the year-ended December 31, 2012, Westport had operating revenues of $58.4 million, and $66.0 million for the nine months ended September 30, 2013. The cash purchase price is $123.0 million and is subject to a post-closing adjustment. To finance the acquisition, Universal anticipates increasing its senior credit facility to $300.0 million. Universal expects to receive regulatory approval for the transaction and close in late December 2013, subject to customary closing conditions. "We are very excited about the opportunities this new partnership brings to Universal," commented Scott Wolfe, Chief Executive Officer. "The acquisition of Westport strategically enhances our customer base by further penetrating industrial markets, specifically to manufacturers of medium and heavy-duty trucks. We believe that Westport's value-added services and limited capital requirements fit nicely into Universal's business model and long-term growth strategy. We look forward to working with Westport's proven management team to enhance their already-strong customer relationships as we further expand Universal's value to our customers." About Universal: Universal Truckload Services, Inc. is a leading asset-light provider of customized transportation and logistics solutions throughout the United States, Mexico and Canada. We provide our customers with supply chain solutions that can be scaled to meet their changing demands and volumes. We offer our customers a broad array of services across their entire supply chain, including transportation, value-added, and intermodal services. So now, the Brazilans have cast off their U.S. Westport subsidiary because they weren't making any money with it, and Mack brand chassis will now be assembled by a freight company. Sounds great. (Westport assembles Volvo chassis for Mack brand production in Allentown. The work was previously performed by Lancaster Preferred Partnership).
-
Westport Axle is located at Allentown's Bridgeworks Enterprise Center, in the former Mack Trucks Plant 4* in south Allentown. * Mack Plant 4, built in 1926 to assemble truck chassis and paint truck bodies, was closed in 1984. http://www.bigmacktrucks.com/index.php?/topic/26449-who-got-the-contract-to-build-mack-chassis/
-
The 865 was a high torque-rise Maxidyne spec V-8, and the 866 was set up for multi-speed transmissions. When the E9 first came out in the early 1980s (evolved from the ENDT1000/1005) at the same time Cruise-Liner production shifted from Hayward, California to Macungie, you had the EM9-400 Maxidyne V-8 governed at 2,100rpm (55% torque rise), the "Econodyne" spec EM9-400R for multi-speed transmissions governed at 1,700 rpm (23% torque rise), and the E9-440 V-8 for multi-speed transmissions governed at 1,800rpm (16% torque rise). The EM9-400R offered maximum fuel economy in a V-8, while the E9-440 was aimed at the owner-operator segment. Then in the mid-eighties, the Maxidyne spec V-8 was dropped, and the product range became the E9-400, E9-450 and E9-500 (US market) which all had a 20% torque rise. So given that you have a Maxidyne-spec EM9-400 governed at 2,100rpm with a massive 55% torque rise, as is, you should stick with a 5 or 6-speed Maxitorque tranny. A multi-speed transmission will of course bolt up, but the only unit I'd recommend is a triple-countershaft Mack TRDL1070 10-speed. But if you have your fuel pump recalibrated to "Econodyne" EM9-400R spec, that would work very well with an Eaton (multi-speed) transmission and deliver impressive fuel economy.
-
The labor dispute didn't cause the relocation to Hagerstown. The labor dispute was the result of the decision to relocate powertrain production to Hagerstown, Maryland. Many New Jersey employees understandably didn't want to relocate to Western Maryland. Their was only one PDC, in Bridgewater Township. Somerville was originally under Bridgewater Township so the two location names were interchangeably used.
-
The former Mack plants in Long Island City, New York; Plainfield and New Brunswick, New Jersey; Hayward, California; Oakville, Canada and also the master parts distribution centers in Bridgewater, New Jersey and Antwerp, Belgium are now so often forgotten.
-
Financial Times / December 1, 2013 Iveco expects truck sales in Europe to flatten out in 2014 after two years of falling demand, as the need to replace ageing heavy-duty fleets offsets worries over new regulations. Sales of commercial vehicles, from vans to heavy trucks, have fallen dramatically in Europe since the financial crisis, reflecting a slump in economic growth and industrial activity. But a small decrease this year is set to flatten out in 2014, the president of Europe’s fourth-largest truckmaker by sales said, following suggestions from rivals that the worst might be over for the industry. “I do not think that sales will go down in 2014. The heavy segment will increase,” said Lorenzo Sistino, referring to trucks able to carry more than 16 tons of freight. “The fleet needs to be refreshed. We think that sales will recover.” Sales in Europe this year will be just over 1.6m trucks, or two-thirds of the continent’s pre-crisis total. High unemployment and sluggish economic activity, particularly in southern European countries, has severely reduced demand. Volvo, Europe’s second-biggest truckmaker by sales, has said it expects sales of heavy-duty trucks to remain flat next year, while Daimler, the continent’s biggest brand, has said it is “optimistic for 2014”. The European truck market inched up 1 percent in the third quarter of this year from a year earlier, reversing a downward trend seen since the end of 2011. A new set of emission standards for trucks known as Euro 6 will come into force in the EU on December 31, with some truckmakers anxious that because of the advanced technology in the less-polluting trucks, the higher cost price may deter some buyers. Iveco, the Italian brand owned by CNH Industrial, sells almost three times as many trucks in China through joint ventures as it does in Europe, and will focus on increasing its presence in that country, Africa and in Latin America to offset slower growth in Europe. Iveco has no plans to enter the US, Mr. Sistino said, and was not interested in a return to the Indian truck market, which has seen billion dollar investments by rivals such as Daimler betting on its emerging potential, but has so far lagged behind expectations. “We have a lot of business areas where we need to grow,” said Mr. Sistino. “There is huge potential for de-contented vehicles in Africa,” he said, referring to trucks with fewer features.
-
Question: In what way did Mack Trucks and MAN share a common connection? Answer: Both the International Motor Company (the forerunner of Mack Trucks) and German truckmaker MAN produced Swiss Sauer brand trucks under license. MAN began producing Saurer trucks under license from 1915. The International Motor Company, the holding company that included the Mack Brothers Motor Car Company and Saurer Motor Company*, began producing Saurer trucks under license from 1911 at a plant in Plainfield, New Jersey which went on to become Mack Truck’s legendary Plainfield drivetrain production location. *The New York-based Saurer Motor Company had been created in March, 1911 to build Swiss Saurer trucks under license, 7 months before becoming a part of the International Motor Company in October.
-
Wall Street Journal / November 22, 2013 Federal investigators are probing a subsidiary of Caterpillar Inc. to determine whether it was dumping train parts into the ocean near the Port of Long Beach, California, as part of a possible scheme to bill railroad companies for unneeded repairs. The Peoria, Ill.-based maker of heavy equipment disclosed in a securities filing three weeks ago that it had received a federal grand jury subpoena to provide documents and information on its Progress Rail unit, which repairs locomotives and railcars. But Caterpillar hasn't provided details about the criminal investigation or how it arose. The grand jury investigation is being conducted by the U.S. Attorney for the Central District of California, based in Los Angeles. It is examining whether Progress Rail was dumping brake parts and other items as a way of concealing evidence that Progress Rail was charging owners of rail equipment for replacing parts that were still in good shape. Union Pacific Corp., a major railroad operator, was one customer believed to have been affected by the alleged Progress Rail activities. The U.S. Attorney got involved in this case because of suspicions that Progress Rail was breaking environmental laws, according to a person familiar with the situation. In its disclosure three weeks ago, Caterpillar said it was cooperating with the authorities. "We currently believe that this matter will not have a material adverse effect on the company's consolidated results of operation, financial position or liquidity," Caterpillar said at that time. Caterpillar acquired Progress Rail in 2006 for about $800 million. Progress Rail, which had its origins in the metal-scrap business, was founded by William P. "Billy" Ainsworth, an Alabama native who built up a nationwide business repairing and refurbishing rail equipment. Mr. Ainsworth has remained head of Progress Rail. He oversaw Caterpillar's diversification into production of railroad locomotives via the 2010 acquisition of Electro-Motive Diesel, or EMD, formerly owned by General Motors Co. Progress Rail is based in Albertville, Alabama, and has more than 90 branches across the U.S. It competes with small independent shops as well as large railcar manufacturers, such as Union Tank Car Co. and Greenbrier Cos., that also do repair work. Railcar owners, such as chemical producers and leasing companies, and the railroads hire Progress Rail to make repairs or replace worn brake shoes, wheels and other components. Railroad inspectors routinely pull cars out of service if they discover a problem. Industry experts say repair shops that billed for more work than necessary were once common in the industry. But better monitoring of repairs and greater emphasis on standards for replacing parts have reduced the frequency of disputes between equipment owners and repair shops. "There's more policing than there used to be," said Mike Francis, an equipment consultant from Texas who inspects repairs on behalf of railcar owners. "Twenty or 30 years ago, repair shops were like the wild, wild West." Even today, Mr. Francis said, "the opportunity to take advantage of folks is high. If you're in Chicago and your car is in Florida and somebody says you need repairs, you don't know that. You're not there." The investigation marks a possible second embarrassment in a year for Caterpillar. Last January, the company was forced to make a $580 million writedown in the value of ERA Mining Machinery Ltd., a Chinese maker of roof supports for coal mines, acquired in 2012 for about $700 million. Caterpillar blamed accounting "misconduct" by several former senior managers of the acquired company.
-
Södertälje / November 11, 2013 Scania has invested US$ 60.5 million to build the truck industry’s most advanced climate test facility. With its climatic wind tunnel, located within the company’s R&D center in Södertälje, Sweden, Scania can subject test trucks to the most demanding weather conditions, thereby speeding up development and improving performance. Scania is now less dependent on field testing and, using the wind tunnel’s controlled environment, can now shorten lead time from development to product launch. “This unique facility helps us improve fuel efficiency and reduce emissions even further,” says Harald Ludanek, Executive Vice President and head of R&D. “Because we can reduce the impact of snow, rain and dirt, drivers will benefit from a better cab environment and enhanced safety.” Arctic chill to scorching heat In the facility, temperatures between -31 and 122 degrees Fahrenheit (-35 and +50 degrees Celsius) can be simulated, as well as humidity of between 5 and 95 percent. The air channel system is equipped with a number of small snow cannons to produce various types of snow. The snow can be replaced with rain of whatever intensity desired, and even the drop size can be altered. By adding an ultraviolet (UV) visible chemical to the rainwater, and subsequently illuminating the test vehicles with UV light, it is possible to determine exactly where rainwater and dirt have stuck and how they flow off the vehicle. The test vehicle is parked on rollers – one for each set of wheels. These allow technicians to simulate speeds of up to 62 miles per hour (100 km/h), the optimal pace for testing trucks and buses. Among tests that can be carried out are how components withstand heat and chill, how rainwater flows off vehicles, driver visibility in heavy rain and snow, windscreen icing, wind noise and how dirt adheres to cab sides, rear view mirrors and door handles. “Scania’s trucks and buses are designed to offer the best performance, regardless of climate,” says Christer Ramdén, Head of Vehicle Performance Testing. “As we enter new industrial segments and markets, with increasingly challenging climatic conditions, we need to ensure that our vehicles will perform faultlessly.” Houses a 140 square foot nozzle Construction of the 82 feet (25 meter) tall building was started in 2011 and completed early in 2013, when extensive testing of the complex systems took place. The sheer size of the building is needed to accommodate trucks and buses and the huge nozzle, with a surface area of 140 square feet (13 square meters), from which air is forced past the vehicle and then fed up to a fan on the upper level of the facility. The climatic wind tunnel offer advantages such as performing tests under near-Arctic conditions in the middle of summer and, conversely, simulating scorching heat in winter. Above all, the facility offers opportunities for reliable repetitive testing. Based on actual road segments in Europe and elsewhere – which have been carefully documented and recorded – tests in the climatic wind tunnel can be programmed to precisely simulate these segments. Versatile tests for better performance In heavy rain, tests can be carried out to assess water intrusion in air intakes and its effects on wiper functions, how the climate system performs and mist removal.In snow, tests can determine snow clogging on front lids, snow intrusion in air intakes, snow clogging of filters as well as wiper and defroster functions.Sunshine can be generated with a radiation intensity of 400–1,100 W/m² on the front, roof and cab sides. Cloud and tunnel functions can also be simulated. Tests can thereby show how the climate system copes with heat.By adding 0.5% fluorescent chemical to rain water, tests will show contamination of sides and door handles, windscreen and side window visibility, and how exterior driving mirrors are soiled.Aero-acoustic tests can be carried out to measure wind noise, also with a lateral wind flow.Video: http://www.scania.com/media/calendar/2013/scania-climatic-wind-tunnel/scania-climatic-wind-tunnel.aspx?tab=5 Images: http://www.scania.com/media/calendar/2013/scania-climatic-wind-tunnel/scania-climatic-wind-tunnel.aspx?tab=1&group=0
-
- 2
-
-
Automotive News / November 15, 2013 DETROIT -- Hyundai is working on a 1.8-liter engine that works like a diesel, but burns gasoline. If the engine makes production, Hyundai officials say, it could deliver a 25 percent fuel economy gain over a comparable gasoline engine -- about the same gain as a diesel -- but it would cost less to buy and operate. Diesel fuel currently averages about 60 cents more per gallon than regular gasoline in the United States. Unlike many of today's diesels, the Hyundai engine does not require a system that injects urea into the exhaust to reduce emissions. Hyundai calls the engine a GDCI, for gasoline direct compression ignition. With compression ignition, the pressure in the cylinder ignites the fuel. Compression ignition is used in a diesel engine, whereas a spark plug burns the fuel in a gasoline engine. The Hyundai GDCI engine has no spark plugs. It uses both a supercharger and a turbocharger and has exhaust valves that open twice instead of once per cycle. The extra opening draws in heat, which along with the pressure of being compressed in the cylinder, ignites the fuel. Hyundai plans to begin vehicle testing next year in a fleet of Sonatas. "We are still really early in the development stage, but it is looking very, very promising," said Nayan Engineer, Hyundai's manager of engine design and testing. Hyundai has been working on the concept and has partnered with Delphi Corp. and the University of Wisconsin. "The technology is very promising, and we believe it will be a game-changer," said John Juriga, director of powertrain engineering at the tech center. In dynamometer testing, the GDCI engine is developing around 180 hp. The engineering work and testing is being done at Hyundai's technical center in suburban Detroit, near Ann Arbor, which is being handed a greater role in the company's powertrain development. Juriga said Hyundai has adopted a new powertrain strategy that calls for innovation. "We need to stop being the fast follower and be the leader," Juriga said. "So we're making changes in the way we think and do business." http://www.autoguide.com/gallery/gallery.php/?g2_view=largephotos.Largephotos&g2_itemId=863233 http://www.autoguide.com/gallery/gallery.php/?g2_view=largephotos.Largephotos&g2_itemId=863225 http://www.autoguide.com/gallery/gallery.php/?g2_view=largephotos.Largephotos&g2_itemId=863241 http://www.autoguide.com/gallery/gallery.php/?g2_view=largephotos.Largephotos&g2_itemId=863209
-
- 1
-
-
Fleet Owner / November 15, 2013 Landi Renzo USA announced it has received EPA approval of a dual-fuel (diesel and natural gas) engine. The remanufactured powerplant is a pre-EGR Detroit Diesel S60 12.7L engine. The dual-fuel system injects natural gas after the turbo/intercooler and a computer controls the exact balance of natural gas and diesel fuels, to achieve the maximum performance, efficiency and economy, Landi Renzo said. This engine runs on compressed natural gas, which replaces the majority of diesel fuel usage for an average fuel displacement of up to 60% and noise reduction of up to 40%. The dual-fuel engine reduces particulate matter by up to 40%, CO2 up to 14% and smoke reduction up to 50%. “As a world leader in alternative fuel systems, we are pleased to present the availability of this innovative technology. Not only does this expand our current clean fuel product offering, but also it further promotes the increased use of natural gas as a fuel and moves us further down a path of energy independence in the United States,” said Andrea Landi, president. Benefits of the engine include: Performance comparable to the original pre-EGR engine in terms of torque, horsepower, drivability, and economyMaintains and improves the emission levels of the original engineFlexibility for adaptation to different diesel enginesAbility to switch back to 100% diesel if neededRequires less CNG storage compared to a dedicated CNG vehiclesExtended range compared to original diesel systemLandi Renzo SpA is the world leader in the alternative fuel industry, serving more than 30% of the global market for LPG and CNG solutions. Established in 1954, Landi Renzo began exporting its products throughout Europe in 1963 after national sales grew rapidly. Since then, it has expanded in the Eastern European, Indian, and South American markets with new branches opening in Brazil in 2003 and China in 2005.
-
- 1
-
-
Ford does not sell the Cargo in Mexico, nor the North American market F-600/700 series. (http://www.ford.mx/camiones) You will see Brazilian-built Cargos throughout South America.
-
If you're going to buy LED headlamps, you're better off going with a name brand that can give you nationwide after-sales support (ease of warranty replacement). That would be Truck-Lite. They brought LED headlamp technology to the US market. And note the price difference, $521.50 (each) for the no-name brand versus $200 for the Truck-Lite. http://www.truck-lite.com/webapp/wcs/stores/servlet/CategoryDisplay?catalogId=10001&storeId=10001&categoryId=10326&langId=-1 http://www.amazon.com/Truck-Lite-27270C-Round-Headlamp-price/dp/B007K8AA7I http://www.amazon.com/s/ref=nb_sb_ss_i_1_14?url=search-alias%3Dautomotive&field-keywords=truck%20lite%20led%20headlight&sprefix=Truck%3DLite+LED%2Cautomotive%2C1412 http://www.bigmacktrucks.com/index.php?/topic/33498-truck-lite-introduces-led-headlamp-for-heavy-duty-markets/
-
Wall Street Journal / November 13, 2013 Manuel Hernandez is one of a vanishing breed: a professional long-haul trucker. He loves backing an 18-wheeler into a tight spot. He has been patiently training new drivers for more than eight years. Lately, though, Mr. Hernandez's patience has been worn thin by a confusing tangle of rules, efficiency directives, and electronic devices that cap his speed, log his every move, and practically try to autopilot his truck. Magnifying the stress are more federal rule changes that took effect in July and are now roiling the industry. Under the revised rule, the average workweek has been shortened to 70 hours from 82. They must take one 30-minute break during the first eight hours of driving. And the required 34-hour break between workweeks now must extend over two nights, including the hours between 1 a.m. and 5 a.m. Those changes are proving more disruptive because they are added on to existing requirements that limit drivers to driving 11 hours a day and require them to rest a consecutive 10 hours. The changes are aimed at reducing chronic fatigue and related crashes, according to the Federal Motor Carrier Safety Administration, the Department of Transportation agency responsible for highway safety. Fatalities in large truck crashes declined 26% from 5,111 to 3,757 in the decade ending in 2011, according to the FMCSA, but it considers that number still unacceptably high. "This agency is not just mandated but driven to improve the operating environment of trucks," said Anne Ferro, the agency's administrator, in an interview. The agency's analysis shows the latest changes—affecting drivers of about 2.3 million long-haul, heavy-load trucks—would prevent about approximately 1,400 crashes and 560 injuries and save 19 lives a year. Ms. Ferro recently took a 34-hour truck ride from Upper Marlboro, Md., to St. Louis. She said she gained a new appreciation for the pressures on truck drivers, but the trip didn't change her mind about the need for the new revisions. The industry says the rule is too costly and possibly even dangerous because it inadvertently puts more trucks on the roads during rush hour and forces drivers to sleep when they're wakeful and drive when they're sleepy. Two weeks ago, Schneider National Inc., a closely held trucking company, said its shipments had fallen 3% to 4% since the rule took effect. At a trucking conference sponsored by the American Trucking Associations last month, a panel of trucking executives said the rule was pushing driver turnover even higher. Last month, three members of the House Committee on Transportation and Infrastructure introduced legislation to delay the new, more tightly regimented 34-hour provision until it could be independently reviewed by the Government Accountability Office. Though the debate is raging over truck driver hours, it reflects a battle of wills and agendas in the highly fragmented $642 billion industry that hauls 69% of the nation's freight. Trucking companies are straining to boost profitability, operating on a long-standing business model that pays drivers by the mile. Safety advocates want to see that practice overhauled. Regulators, meanwhile, are grappling with how to increase safety in an industry where 97% of the 1.3 million trucking companies have fewer than 20 trucks and shippers have the upper hand. Neither long-haul truck drivers nor their trucking companies get paid for the myriad delays caused by shippers, Ms. Ferro said. Trucks drivers like 50-year-old Mr. Hernandez are caught in the middle. For Mr. Hernandez, the pressure was on as soon as he steered his shiny royal blue International ProStar out of the Mesilla Valley Transportation truck terminal in El Paso, Texas, last month and headed for Interstate 10 to California. Donning a white cowboy hat, he settled into the padded driver's seat, his "home away from home," for what was supposed to be an easy 754-mile ride to a Lowe's distribution center in Perris, Calif., to deliver 53 refrigerators that had come from an Electrolux factory in Mexico. The "drop and hook" at Lowe's the following afternoon was the easiest kind. He would trade the loaded trailer for an empty one. Then he would drive 70 miles to a Maruzen of America warehouse in Carson, Calif., to fill that trailer with auto parts and clear Los Angeles traffic. There would be no stops, except for those required by the FMCSA. "As long as the wheels are turning, I'm getting paid," Mr. Hernandez said. He had just finished his 34-hour mandatory break; he had 55 hours to drive in the coming 120 hours—and he aimed to use them to cover as many miles as possible. As he began driving, a relentless chorus of electronic beeps began to go off. An electronic log—a little black computer screen to the right of his steering wheel—began recording whether the truck's motor was on or off; whether he was on duty or off; his gas mileage. Throughout the trip, his "elog" would tell him where to get gas. If his truck stopped abruptly, it would ask for an explanation, to which he would respond via touch screen. Mr. Hernandez, who is a company driver for Las Cruces, N.M.-based Mesilla Valley Transportation, had been assigned the shortest route with stops for the cheapest gas. Mesilla's chief executive, Royal Jones, started out with one truck at age 19 and built the company into an operation that now has 1,300 trucks and 4,700 trailers on that kind of penny-pinching. But truck trips rarely go according to plan. Traffic, breakdowns and loading delays all cost him time and pay. Truckers are paid by the mile, and Mr. Hernandez's 36 cent rate is near the top of the range. Yet, "trucking is not like a lot of jobs where you can control the time frame," he said. On a recent trip from East Rutherford, N.J., to Dallas, he could only stand by helplessly and watch as it took eight hours for workers to unload mattress foam by hand from his truck. Mr. Hernandez used to be able to make up lost time by taking shortcuts, or driving a little faster to avoid traffic. Now, his "elog," the electronic monitoring system that has superseded his log book, reports even the tiniest bit of cheating on his hours or his route and a governor on his speedometer won't let him go more than 64.5 miles an hour. (Mr. Jones said he sets the governor for safety, to save wear and tear on the trucks and optimize fuel savings.) A serious trucker, Mr. Hernandez's trips are usually two to three weeks long. But he's also a dedicated family man, so his time at home is paramount. From the start of any trip, his goal is to drive as many miles and return to El Paso to spend his 34-hour break with his wife, Teresa. They'll be married 30 years this month. Often now, he can't. Five times since July 1, his 70 on-duty hours have run out before he can complete a trip and he and his truck have has been stranded. One of the times, he dropped a load in Dallas and then drove to a truck stop on I-20 to wait out his reset. "There was nothing to do," he said. "It can be a nightmare of having to sit for 48 hours, tired, when all you want to do is get home." When he finally does get home, it's for 10 hours and he's back on the road again. "Who made up these rules," he asked, shaking his head. "Did they have any experience in driving truck, and traffic and dealing with customers and your breakdowns?" The rule changes capped a decade of litigation against the FMCSA by safety advocates, drivers and plaintiff lawyers pushing for tougher driving laws, Ms. Ferro said. In a compromise, the agency agreed to review the hours of service rule, she said. Ms. Ferro began the review after she arrived in 2009. After declining, the fatalities from large truck crashes rose in 2010 and 2011—by a total of 10% from a 2009 low of 3,380, she found. Moreover, new sleep research showed that working long hours daily and weekly eventually caused chronic fatigue, slow reaction times and reduced ability to assess situations, including your own fatigue levels. "Prior to this rule, drivers could work as much as 82 hours in an eight-day period. Once in a while, perhaps you can do that," Ms. Ferro said. "Week after week, that schedule results in a state of chronic fatigue that impacts a driver's ability to be alert and respond." Not to mention other health problems, such as obesity and sleep apnea. All that may be true in theory, but most truckers say the rule makes matters worse by disrupting their sleep cycles and adding stress. Ms. Ferro's recent truck trip was an eye-opener. She said it "intensified my understanding" of why truck driving doesn't follow more sensible schedules. Many shippers don't either and they pay by the load, not by the hour. "Safety has to be built into that supply chain," she said. Now the agency will also study the safety implications of unpaid delays caused by shippers, as well as compensation. "When you're getting paid piecework by the mile and the load, you're incented to drive as much as you can," she said. "Are those the incentives we want for somebody who's driving an 80,000 pound load 60 miles an hour?" Indeed, Mr. Hernandez's ride to Perris, Calif., started out smoothly, but before he'd crossed into New Mexico, he began to worry about the "Banning scales," the California Highway Patrol's inspection station in the desert east of Banning, Calif. They're "super tough." He breezed through weigh stations in Texas, New Mexico and Arizona, postponing his 30-minute break until Eloy, Ariz., near the end of his eight-hour limit. He doesn't like to stop when he is on a roll because it might make him sleepy, he said. To stay on schedule, he still needed to drive 218 miles to reach Quartzsite, Ariz., for the night. He used to be able to alternate driving and sleeping, depending on when he got tired. Mr. Hernandez is required to take 10 consecutive hours of rest to promote a circadian rhythm sleep cycle. The problem with imposing a rule like that on a trucker's unpredictable schedule, he said, is that "sometimes when you're not tired, you have to sleep and when you're tired, you have to drive." That requirement has combined with the new rule changes to cut the number of miles he and his trainee can drive to about 6,000 a week, from 7,500. Pay for an experienced driver has fallen to about $50,000 from $65,000 a year, Mr. Hernandez said. New drivers are making about $40,000 at Mesilla. Many rookies decide it isn't worth it. Some nights, there's no place to sleep because so many budget-strapped states are closing their rest stops. Mr. Hernandez has had to park on a freeway ramp—an entrance ramp, preferably, because it's less dangerous, and with other sleeping truckers so he won't get robbed. There's no predicting the next setback. When he arrived at the Banning scales the next day, he groaned at the long line of trucks. "We're going to waste so much time," he said. It was noon. More than nine hours later, with nighttime setting in, he finally left Banning. The inspectors had detected a worn part, a pivot beam bushing. The repair, which involved removing the back wheels and axle, was complicated and it looked as if he might run out of drive time and would be stuck in the desert for the night. He had been driving less than three hours but had been on duty for 12 of his allotted 14 hours. He drove the hour to Lowe's and then made a couple of quick stops on a newly assigned route before having to quit about midnight for another 10-hour break. Because the delay will cost him nearly 390 miles and $140, the rest of his week would be extra stressful. "Sometimes I think they're trying to choke out the trucking industry," he said.
BigMackTrucks.com
BigMackTrucks.com is a support forum for antique, classic and modern Mack Trucks! The forum is owned and maintained by Watt's Truck Center, Inc. an independent, full service Mack dealer. The forums are not affiliated with Mack Trucks, Inc.
Our Vendors and Advertisers
Thank you for your support!