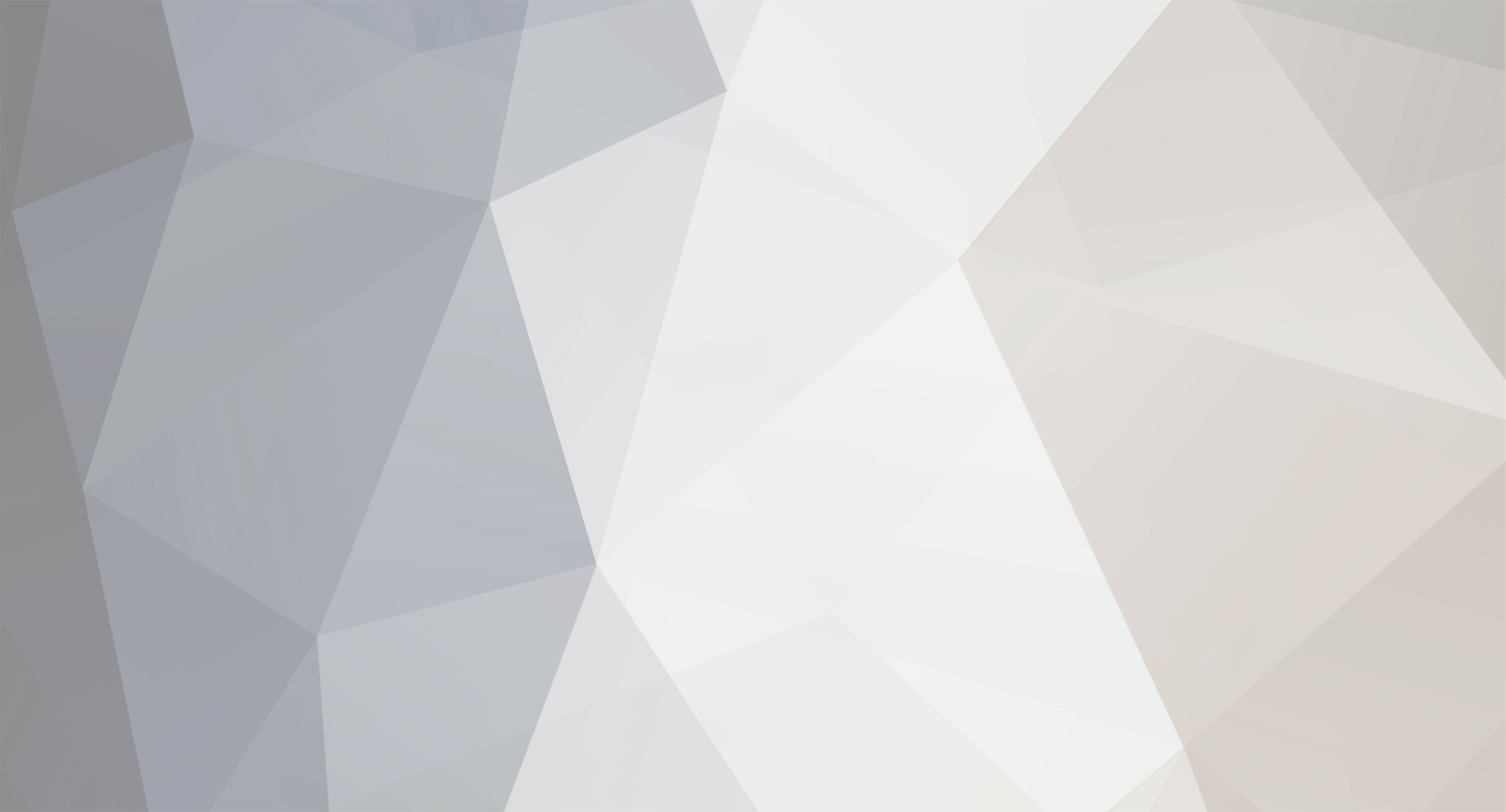
JoeH
-
Posts
2,382 -
Joined
-
Last visited
-
Days Won
16
Content Type
Profiles
Forums
Gallery
Events
Blogs
BMT Wiki
Collections
Store
Posts posted by JoeH
-
-
It says diesel on the hood, but I don't know anything about B's
-
Complain on the Volvo customer satisfaction hotline about the dealer and the work. Not that Volvo cares I suppose...
-
10 hours ago, terry said:
Should be stamped on front on that flat spot next to power divider, might have to wire brush it to see it. terry
And a chipping hammer, underside of the truck tends to get caked in concrete. Truck runs just fine for me, I like it's gearing. It'll do 70+ IIRC, though I never take it on roads with speed limits above 55. Biggest problem I have with the truck is it's about a foot longer than any other triaxle in the area. 228" wheelbase, steers a bit like the Titanic.
-
That is priceless. I'd love to be a fly on that wall.
-
Did all your fault codes clear up too? If not, I would go through and get them fixed. You won't know if a new problem arises if the light is always on.
-
All i see is a bunch of letters leading to an error code webpage.
-
- Popular Post
- Popular Post
-
Sounds unlikely, out my way above Philadelphia we go through Associated Truck Parts in Warminster, PA. Any time we have an odd brake part we need we usually take it in for them to measure. It's a bit far for you though... Nice looking rig!
-
On 3/21/2019 at 2:37 PM, 41chevy said:
Tonight is the regular monthly Village Meeting with public participation. I'm looking forward to it. Taking my M917 to the meeting to exercise it a bit and show off my new vinyl sticker on the steer diff.
Keep the updates coming, though I know that could be a while the way bureaucracy works.
-
I hope that has a V8 in it. Just to add to how ridiculous and one off it is.
-
That's exactly how fast my RD 688S goes with an 8LL. No idea what ratios in the rears, I guess it's 4.17!
-
A traditional Jake brake is my preference. Simple, tried and true. Doesn't give the most braking, but it's adequate. If it doesn't hold you around 1800 RPMs on the downgrade then you're in too high of a gear for the hill anyways.
-
Only other thing I could think of is pushing exhaust past turbo seals? Exhaust manifold should have no problem holding that pressure. I would call pacbrake and ask. Get on the phone with a tech or engineer there and ask questions.
-
If the piston generates 20psi vacuum then that's another 40# off your valve spring, leaving you with 110# spring pressure.
-
That's exhaust valve diameter? That has about 1.8-1.9 square inches of surface area, so that's about 40 pounds of pressure. At higher RPMs you need more pounds of spring tension because the valves have less time to close between cycles. 40 # of pressure on the valve leaves you 150# of spring pressure. Of course the back pressure doesn't push on the valve with that 40# until the valve is shut. At fully opened the valve spring might not have much resistance, as the pressure is vented into the cylinder. But, you also have vacuum created on the intake stroke which is acting to pull the exhaust valve open, which is takes from your remaining 150# spring pressure.
-
I got the 60 pounds of pressure because it's 20 pounds per square inch and a 2 inch valve has 3.14159 square inches of surface area. If it's a 3 inch valve the surface area jumps to 7 inches, which jumps to 140 pounds of back pressure acting on your valves, leaving only 50 pounds of spring pressure shutting the valves.
-
You have to take the 190# and convert it to psi on the surface area of the valve head. If it's a 2 inch diameter, πr^2 is 3.14159. Now take your 20 psi back pressure and you have 60+ pounds of pressure trying to open your valves, which leaves 130 pounds of spring pressure holding them shut.
-
What back pressure do they list for other brands like Cummins? You might be surprised.
-
I think the butterfly brakes are operated by an air cylinder. I assume you can put an air regulator on it to control the amount of back pressure the brake generates.
Find out what # springs the exhaust valves are, and what diameter they are. Run a little math, you'd have to generate enough force to counteract the valve springs to cause valves to float. You'll need to leave a safety factor to ensure the springs can still hold the valves with some force.
Your other choice is a traditional Jake brake that opens the exhaust valves at TDC of compression stroke to dump off the combustion energy. Doesn't generate any back pressure, and certainly doesn't take 700# off your payload.
-
Looks like it weighs a decent amount, not sure what maintenance is involved. A traditional engine brake or a butterfly style seems simpler and less maintenance. And weigh less.
-
Is it VMac II or VMac III?
With key on, engine off is the lightning bolt on?
If so, with cruise off hold down the set/decel button until light goes off. It should spit out a 2 digit code, which can be looked up to see which sensor is failing.
-
If they're double frame trucks, the best thing you can do to preserve them is split the frames apart one side at a time and sandblast/paint them. Some people even drill and tap the outer frame rail for grease fittings so they can prevent future rust jacking. Nowadays they make a "heavy single" frame, I wish they had started using them sooner.
-
1
-
-
That's a nice truck. I'd be a happy driver scooting around in that. Is the cab air ride? We just bought an '88 to put on the road, but it doesn't have an air ride cab. Makes a world of difference, I compare cab air ride to sitting on a cloud. I'm going to put air bags under this cab before I put it on the road.
-
Is it low on power steering fluid?
Vibration that 2 mechanics and Mack dealer can’t figure out
in Engine and Transmission
Posted
Did you ever just swap the motor out with a replacement? Maybe the flywheel housing or bell housing got tweaked, throwing the engine/trans alignment off. Or the crank got tweaked. Ever check the flywheel run-out with the trans off?