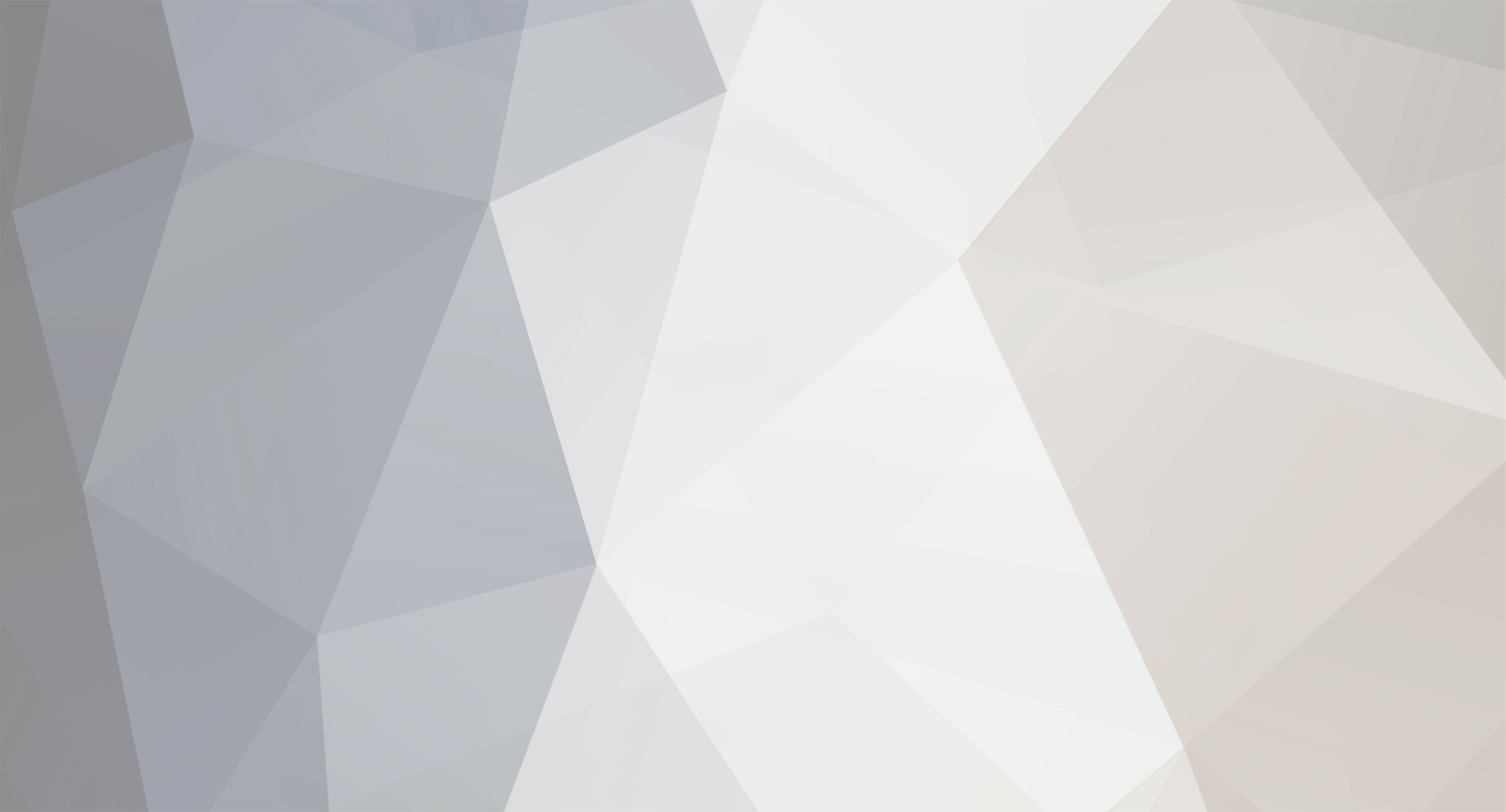
kscarbel2
Moderator-
Posts
18,717 -
Joined
-
Days Won
114
Content Type
Profiles
Forums
Gallery
Events
Blogs
BMT Wiki
Collections
Store
Everything posted by kscarbel2
-
17-year throws newborn child away into dumpster Associated Press / July 31, 2015 A newborn baby girl who was found alive in a dumpster in western Kentucky remained in a hospital Friday, and a teenager was charged with attempted murder. The McCracken County sheriff's office said the baby was in stable condition after being found by a man Thursday afternoon. "What alerted him was he heard a loud noise outside," Sgt. Darrin Frommeyer of the sheriff's office said Friday. The man said he went outside, saw a young man walking away from the dumpster, walked over to it and heard a baby crying, Frommeyer said. When he opened the dumpster, he found the baby and called authorities. A 17-year-old boy was detained later and charged with attempted murder, first-degree criminal abuse and tampering with physical evidence, Frommeyer said. The teen is the boyfriend of the baby's 15-year-old mother, who was taken to a hospital with bleeding hours after the baby was found, Frommeyer said. The boyfriend confessed to police what happened. Officials don't know whether the 17-year-old is the baby's father. The mother lives with her mother and sister in an apartment near the business where the baby was found, and the boyfriend lives with his aunt, Frommeyer said. The girl's family told authorities they didn't know she was pregnant.
-
There are two CAT truck stories going on in the world. Down in Australia where CAT long-haul trucks are being marketed, the Navistar version of the MAN D26 is available (dubbed CT13), BUT the engine they are actually promoting is the CAT C15........and that's a "road engine" as you say. I've had little interest in the North American CAT vocational truck effort because, frankly speaking, the CT660 looks like a Tonka toy (Having said that, the newer CT681 looks purpose designed, if somewhat dated in appearance), and CAT U.S. flubbed the launch. But the effort in Australia is being attempted in the right way. I can't predict the future for CAT Australia, but my hat is off to the people down there. http://www.cattrucks.com.au/trucks/ct630hd/#tab=3 http://www.cattrucks.com.au/wp-content/uploads/2013/11/P30669_Engine_Spec_Brochure_A4-Low-Res.pdf http://www.cattrucks.com.au/wp-content/uploads/2014/10/P40006_CAT_Brochure_r6.pdf http://www.cattrucks.com.au/category/testimonials/
-
2 men arrested for shooting and killing 4-year-old boy as he played with stuffed toys on lawn KTLA News / July 31, 2015 Two men were arrested in the killing of a four-year-old California boy who was shot while playing with a stuffed animal in his family's front yard. Darron Daniels, 20, and Maurice Kelley, 25, were taken into custody for investigation of murder and attempted murder after Daniel Munoz was killed, San Bernardino County sheriff's authorities said. Daniel was outside his family's house Wednesday in the inland city of Highland when shots were fired. The boy was taken to a hospital where he was pronounced dead. Investigators have not discussed a motive for the shooting. They said Friday they were looking for a four-door, 1990s white Toyota Camry with black bumpers. Sheriff's deputies declined to provide any additional information. Daniels and Kelley are expected to appear in court on Monday. Highland, a city of 54,000 people in the foothills 60 miles east of Los Angeles, has been grappling with a rise in violent crime. Last year, authorities arrested more than 100 people in a crackdown on gangs in the city, the Los Angeles Times reported. On Wednesday, Daniel was playing with a stuffed bear he called Superman while family members picked fruit and watered plants in the front yard. His mother, Yuliana Morales, had taken an elder sibling and cousins to an amusement park and promised the boy he could go next time. 'It's my fault for leaving him here,' she said. .
-
Man shoots neighbor and runs over her with lawn mower Yahoo News / July 30, 2015 A $1 million bond has been issued for a man accused of shooting his neighbor to death and then running her over with a lawn mower. According to the Huron County Sheriff’s Office, deputies were called at just after 11 p.m. and told that shots were fired at a home in the 4300 block of Kirkwood Drive Tuesday. When deputies arrived at the scene, Linda Ciotto, 62, was found with a gunshot wound to the head. She was pronounced dead at the scene. It was determined that Ciotto was using her lawn mower at the time of the incident. James Blair, 50, is accused of shooting Ciotto and then running over her left arm with the mower. Blair reportedly barricaded himself in his home after authorities arrived. The Mansfield ASORT team and the Richland County Hostage Negotiator’s Team were called to assist Willard police and fire departments. Blair stayed in his home for nearly five hours as negotiators tried to get him to surrender. Tear gas was then used in an effort to push him out of the home. He was arrested shortly after. Blair faces a charge of murder and is in Huron County Jail on $1 million bond. The case is being investigated by the Bureau of Criminal Investigation, and two search warrants were executed — one for Blair’s home and one for Ciotto’s home.
-
Out of control, Baltimore killings soar to a level unseen in 43 years Associated Press / July 31, 2015 Baltimore reached a grim milestone on Friday, three months after riots erupted in response to the death of Freddie Gray in police custody: With 45 homicides in July, the city has seen more bloodshed in a single month than it has in 43 years. Police reported three deaths — two men shot Thursday and one on Friday. The men died at local hospitals. With their deaths, this year's homicides reached 189, far outpacing the 119 killings by July's end in 2014. Nonfatal shootings have soared to 366, compared to 200 by the same date last year. July's total was the worst since the city recorded 45 killings in August 1972, according to The Baltimore Sun. Crime experts and residents of Baltimore's most dangerous neighborhoods cite a confluence of factors: mistrust of the police; generalized anger and hopelessness over a lack of opportunities for young black men; and competition among dealers of illegal drugs, bolstered by the looting of prescription pills from pharmacies during the riot. Federal drug enforcement agents said gangs targeted 32 pharmacies in the city, taking roughly 300,000 doses of opiates, as the riots caused $9 million in property damage in the city. Perched on a friend's stoop, Sherry Moore, 55, said she knew "mostly all" of the young men killed recently in West Baltimore, including an 18-year-old fatally shot a half-block away. Moore said many more pills are on the street since the riot, making people wilder than usual. "The ones doing the violence, the shootings, they're eating Percocet like candy and they're not thinking about consequences. They have no discipline, they have no respect — they think this is a game. How many can I put down on the East side? How many can I put down on the West side?" "You can't attribute every murder to narcotics, but I would think a good number" of them are, says Shawn Ellerman, Assistant Special Agent in Charge of the Baltimore division of the Drug Enforcement Administration. ----------------------------------------------------------------- Here’s a thought: Why not have our government establish an effectively “border” around our country’s perimeter, so as to turn off the flow of illegal and crime-stimulating drugs from Mexico and Latin America.
-
Parents charged with child neglect after their toddler daughters are found wandering around motel naked and hungry, and test positive for COCAINE Daily Mail / July 31, 2015 Two parents have been charged with child neglect after their lice-infested toddler daughters were found wandering around a motel in South Carolina naked, hungry and with drugs in their systems. The two girls, aged one and two, were discovered by an unnamed woman walking nude down a set of stairs at a Motel 6 in Chesnee on May 31. They reportedly told the passerby they were hungry. The woman then alerted staff members at the motel, who provided diapers, wipes and clothing for the toddlers. Workers subsequently spent 45 minutes searching, door-to-door, for their parents. The girls' mother, Cheryl Leeanne Lynn, 24, was reportedly discovered hiding in the bathroom of the family's motel room, while their father, Andrew Donovan Buff, 28, was also found in the room. The only available food was a jar of peanut butter, along with two bottles of water. The girls were taken into emergency state custody and given medical exams. While one of the sisters had pink eye, they both had lice. Shockingly, the two toddlers also both tested positive for cocaine. On Wednesday - nearly two months after the incident at the Motel 6 on Jones Road - Lynn and Buff were arrested by sheriff's deputies and each charged with two counts of child neglect. Lynn has been released from Spartanburg County Detention Center pending a court hearing. Buff, however, is being held at the facility on a $10,000 cash or surety bond, officials said. The father of two has a lengthy criminal history, including convictions for shoplifting. .
-
Broken-down motorist murders couple and wounds their daughter after they stopped to help Daily Mail / July 31, 2015 An 18-year-old Wyoming man who robbed and shot three members of a family after asking for roadside help told investigators he opened fire after one of the victims laughed at him, an FBI agent said in a court filing Thursday. Jason Shane, 51, and Tana Shane, 47, died in the Wednesday shooting in the small town of Pryor, Montana, FBI spokesman Todd Palmer said. Their daughter, 26-year-old Jorah Shane, was shot in the back when she tried to run away, and she is recovering in a Billings hospital, the woman's aunt, Ada Shane, said. The family are reportedly part of the Whistling Water tribe, the Crow Nation's largest clan. The statement by Special Agent Larry McGrail II was filed in U.S. District Court seeking a murder warrant for Jesus Deniz, also known as Jesus Deniz Mendoza, of Worland, Wyoming. Two FBI agents interviewed Deniz on Wednesday, and Deniz acknowledged shooting three people with a .22 caliber rifle and then driving away in their car, McGrail's statement said. 'Deniz told the interviewing agents that he shot the victims because he was getting tired of waiting around, and because the daughter had laughed at him,' the statement said. Deniz is being held in Park County, Wyoming, after police arrested him near Meeteetse, about 120 miles away from Pryor. A judge's signed warrant would begin the process of returning Deniz to Montana to face charges in the killing. U.S. Magistrate Judge Carolyn Ostby scheduled an initial court appearance for Deniz on Friday. Jorah Shane recounted to her relatives the events leading to the shooting. Her mother, Tana Shane, drove by a young man parked on the side of the road who told her he had run out of fuel, Ada Shane said. 'He's only 18, and he looked like an innocent boy,' Ada Shane said. 'Both my brother and sister-in-law have big hearts.' Tana Shane went by her house, picked up her husband and daughter, and they drove back to the stranded car, Ada Shane said. The man pulled a gun and held it to the temple of 51-year-old Jason Shane. He ordered the father to stop the car and told everybody to get out, Ada Shane said. He told the family to give him their money, but the family said they had only change because they recently returned from a religious revival in Window Rock, Arizona. The man told the family to start walking. Tana Shane told her daughter in their Native American language to run. Jorah Shane told her aunt that she heard a shot, started running then heard bullets whizzing by her head. She fell, heard another shot, and started running again toward a church just as a car was pulling out. She ran to the car, and the frightened driver leaped out, Ada Shane said. Jorah Shane jumped in the driver's seat and drove to her house with the shooter still firing at her, the aunt said. Jorah Shane was later hospitalized. A bullet had grazed her head and she had a gunshot wound to the back. She didn't know as of Thursday that her parents had been killed in the shooting, Ada Shane said. Related reading - http://www.bigmacktrucks.com/index.php?/topic/41155-the-us-is-bordering-a-war-zone/
-
California grants parole to kidnapper who kept 26 schoolkids hostage buried underground Daily Mail / July 31, 2015 A convicted kidnapper who kept 26 children and a school bus driver in a buried trailer has been granted his freedom - after the governor of California didn't object to parole. James Schoenfeld, 63, kidnapped the bus carrying the group then buried them alive in a chilling heist inspired by the film Dirty Harry. Schoenfeld confessed to carrying out the 1976 crime with his brother Richard and his friend Fred Woods. He was originally given a life sentence, which was commuted to allow the possibility of parole. This will now be granted to him after almost 40 years in prison. Governor Jeremy Brown could have denied the recommendation of Schoenfeld's parole board, but took no action. The passage of the deadline at midnight on Thursday means that the parole process will continue. The victims of the kidnapping had described the suffering they felt 39 years later in a heartfelt letter to the parole board. They expressed the desire for their captors to remain in jail. In 1976, the Schoenfeld brothers and Woods took the children, who were aged from five to 14, and bus driver Ed Ray from Chowchilla in the Central Valley to a quarry near Livermore. There they were held captive inside a buried, ventilated trailer stocked with mattresses, food and water. The victims eventually managed to dig their way out and escaped unhurt. Richard Schoenfeld was paroled in 2012. Woods was denied parole the same year but may have another parole hearing this fall. The kidnappers were influenced by the 1971 Clint Eastwood film Dirty Harry, in which the antagonist kidnaps a school bus of children in exchange for a ransom. The Schoenfeld brothers and Woods lured the bus driver by pretending their white van had broken down on the side of a road. The bus driver stopped to see if the occupants of the van needed help. But three masked men, later identified as brothers Richard and James Schoenfeld and Frederick Woods, stormed onto the vehicle, brandishing guns and forced Ray to the back of the bus. The children and Ray were loaded onto two vans and driven around for 11 hours, during which time the hungry, petrified youngsters soiled themselves and held each other in fear. The vans were driven to a quarry near Livermore, where the captives were forced into a buried trailer stocked with mattresses, food and water - and equipped with fans and ventilation. The kidnappers, all from wealthy Bay Area families, planned to ask for a $5million ransom for their hostages. Their plot, which they had worked on for 18 months, unraveled when they took a nap. The driver and older boys were able to stack mattresses to a hole in the top of the van. They pushed open a weighted-down metal lid and freed the children who had spent 16 hours underground. 'He was a courageous man,' victim Jodi Heffington-Medrano said of Ed Ray, the driver. 'He kept 26 scared children in line and made us feel safe.' But even when the hostages started to escape, they feared the men were waiting outside for them, she said. All three men received life sentences after pleaded guilty to kidnapping charges. Jennifer Brown Hyde, 48, who was nine years old when she was kidnapped along with her ten-year-old brother described the chilling memory and life long trauma she has endured. She asked the parole board not to grant James Schoenfeld his freedom. 'I was honestly brutal,' she said. 'I wrote that they buried me alive, they stole my childhood and caused me immense emotional pain over the years. It affected my life, my parents’ lives and my children’s lives. 'For me, it’s having to deal with hatred and anger toward other human beings, and that’s a struggle that almost 40 years later I still have to deal with. 'Until recently I slept with a night light. I have anxiety attacks when I’m in a confined space, and it’s a problem living in the South when we have tornado warnings and we have to take cover in storm shelters... They took away my ability to be free.' The kidnapping affected Hyde's ability to be a mother to two children since she did not have what she considers a normal childhood. 'You don’t go from being buried alive and thinking you’re going to die to having a normal childhood,' she said. 'I’m fortunate I’m not incarcerated or hooked on drugs, which is how some of the kids dealt with it. I’m as OK as a broken person can be.' They letting this nut go free and re-enter society??? Seriously??? .
-
When Freightliner Walked Volvo on a Leash – the US Market N10
kscarbel2 replied to kscarbel2's topic in Other Truck Makes
As I recall, 1987 was the last year the Brigadier was built solely by GM and badged as a GMC. In 1988, the last year, the fleet favorite Brigadier was still built by GM in Pontiac but was marketed by the Volvo GM Heavy Truck Corp joint venture for that one year, and badged WhiteGMC. Then it was effectively replaced by the horrible (my opinion) decontented White-based WG in 1989, which had been introduced in 1988. I personally believe that the only reason Volvo agreed to sell the Brigadier in 1988 is because there was a lot of pressure from fleets. There were a few Brigadiers titled as 1989 models, but I suspect they were produced in late 1988. The WG was cheap, in EVERY sense of the word. But when the recession hit in the early nineties, a lot of fleets that had always purchased quality (Mack) rather than cheap trucks, such as Harwood Cochrane's Overnite Transportation, decided that cheap was suddenly right for them. So after a slow start, and blessed by the recession, the clumsy WG finally took off. The N10 never competed with the Brigadier. Brigadiers ran 290 to 350 horsepower engines, while the N10 was limited in LTL on-road applications at 253hp. And the Brigadier was a bargain for what you got, a favorite with fleet accountants. The N10 never sold well, not at all, but Volvo kept on hoping until they finally gave up. The Volvo Swedes absolutely hate admitting anytime they're wrong. -
15-year-old mother smothers newborn baby to death Associated Press / July 24, 2015 A teenage girl has been charged with murder after police said she admitted to killing the baby after giving birth Wednesday. Police say the teen killed her newborn baby on Abraham Flexner Way at Jewish Hospital, while visiting her grandmother at the hospital. Police received a 911 call that a teenager had given birth and killed the baby. The teenager admitted to smothering the newborn to death, putting the baby in her purse, and getting rid of evidence. The teenager is charged with murder, tampering with evidence, and abuse of a corpse. The murder took place in a hospital and it went undetected for hours -- until a friend of the teen got a text message from her about noon Wednesday. "I'm crying so much, please don't tell anyone," the girl read from her received messages. "I was in the hospital, my granny had another stroke," the teen continued. "So I walked outside and I overheated and now I'm in the hospital and around 4 this morning I pushed out the baby in the toilet. It was crying and opening its eyes and everything. I had to kill it." The girl said she told her friend to call the police, but the teen replied, "No, what the F. It's been dead since 4 in the morning, I told you I had to kill it." The 15-year-old mother also sent pictures of the baby to her friend. She told her friend she put her child in the dresser of the hospital room and planned to take her home, find her clothes and bury her. When she asked her friend to help, the friend called 911.
-
Teen suffocates newborn child, then going shopping Associated Press / July 30, 2015 A teenage girl suffocated her just-born baby boy before putting his body in a shopping bag, then going on a trip to a Victoria's Secret store the next day, prosecutors said as she was charged with murder Thursday. Tiona Rodriguez, now 18, pleaded not guilty, with her lawyer saying it was a stillbirth, not a killing. The indictment came nearly two years after Rodriguez was arrested on a $45 shoplifting charge at the lingerie store, where a security guard found the body in a bag Rodriguez was carrying. Prosecutors said their lengthy investigation revealed a girl who became a mother at 14 and was callously determined not to let anyone know she was having another baby. "She knew she would be in big trouble if her family found out, so she made a plan — to kill this baby," Manhattan Assistant District Attorney Rachel Ferrari said. "She had derailed her life once. She was not going to do it again." To carry out that plan, the then 17-year-old Rodriguez went to a friend's house Oct. 16, 2013, delivered in a bathroom, tore the 8-pound boy's umbilical cord with her hands and asphyxiated him, Ferrari said. In a text message at some point, Rodriguez used a vulgarity to describe the baby and added she'd "dig a hole" and "put it somewhere" adding an "LOL" — online jargon for "laughing out loud" — and "then we go eat iHop," the prosecutor said. After having her now 4-year-old son — a pregnancy unknown to her family until she went into labor — Rodriguez delivered again in 2012 in her bathtub, Ferrari said. That child didn't survive. Ferrari said that the circumstances of the death are unclear, but that Rodriguez had texted her then-boyfriend about smashing or burning the body to disguise what it was. Ward said that was a miscarriage. Prosecutors said the latest baby lived at least a few minutes after being born in 2013.
-
When Freightliner Walked Volvo on a Leash – the US Market N10
kscarbel2 replied to kscarbel2's topic in Other Truck Makes
The Titan Tiptop was inspired by the US market, but far from a success, the effort never got off the ground. And back then, the Volvo drivetrain was immature. When Volvo first came over and would sign near anyone willing to take the franchise, they never sold many F86US in the US. But when Freightliner came into the picture, a trusted name, the F6 and F7 began to sell. But Volvo was always behind Mack's Mid-Liner range, which by the mid eighties had become the most popular medium truck (COE) in the U.S. market. I was thinking about you the other day when someone brought up the Seddon Atkinson 400 series......good truck in its day. . -
21-month-old toddler found decomposed in crib, father arrested Associated Press / July 30, 2015 A man who told police he put bags of garbage in his young daughter's room to mask the smell of her decomposing body was granted sole custody of the toddler during a divorce last year. Eric Warfel, 34, of Medina, a suburb south of Cleveland, was ordered held on a $1 million bond on Thursday after being charged with abuse of a corpse. He was arrested Wednesday after a cable television technician was allowed inside his apartment to upgrade the service and found the body of 21-month-old Ember Warfel in her crib. Warfel told police Ember died June 18 and he hadn't informed family members or anyone else about her death. Warfel put garbage in the dead girl's room to mask the smell and had moved into a motel with a 7-year-old daughter. Police found Warfel and the girl Wednesday at a shopping center in the Cleveland suburb of Westlake. An autopsy will be conducted to determine how Ember died. Additional charges are expected, police said. Medina police said Thursday that a substance suspected to be cocaine was found during a search of Warfel's hotel room. Warfel and his ex-wife, Malinali Galdamez, had another child who died. Five-month-old Erin Warfel died March 31, 2013, after being taken by paramedics to a hospital while in full cardiac arrest, according to an autopsy report. Her death was ruled as "sudden unexplained infant death." Warfel and Galdamez married Feb. 14, 2012. A divorce decree indicates the 7-year-old has the same last name as her mother. The girl was removed from Warfel and Galdamez's home before their divorce by the Cuyahoga County Department of Job and Family Services and moved in with Warfel's parents. Galdamez did not seek any parenting rights beyond limited visitations. There are numerous references in the divorce decree to her substance abuse problems. It was Galdamez's fifth marriage and Warfel's first. Medina Police Chief Patrick Berarducci said Galdamez lives somewhere in New York. Prosecutors asked for a high bond because they consider Warfel a flight risk. The magistrate said Warfel had previously discussed moving out of state. He told the magistrate Thursday that he last worked for an insurance company in 2012. The discovery of a young girl's decomposed body in a crib at an Ohio apartment is prompting authorities to take another look at her sister's death two years ago, the Medina County police chief said Friday. .
-
History repeatedly tells us that inaction will result in the loss of American lives. Arguably, it already has. The cartels are sending illegal drugs across our southern border with relative ease, and reaping profits in the millions of dollars. I use the term “border” loosely here because it no longer appears to be effectively controlled as a border. Definition: Border - a line separating two political or geographical areas, especially countries. Throughout our history, past presidents have acted to combat lawlessness in other countries when that country's government was failing in its inherent responsibility to maintain law and order, and America’s security was under threat. Wake-up Call The lawless, drug cartel-controlled Mexican state of Chihuahua is located in northwestern Mexico bordering a huge swath of the United States of America including the states of New Mexico and Texas. The war-like situation at hand is far beyond the designed means of our Border Patrol. They are not soldiers. I fully expect that our next president will be forced to send troops into Mexico, just as President Woodrow Wilson ordered a military expedition of 4,000 troops led by Brigadier General John J. "Black Jack" Pershing into Mexico in 1916 to capture Pancho Villa.........dead or alive.........to quell raids by Villa and his gang of lawless marauders into the United States. No ordinarily prudent American can pretend to believe that the murderous rampages in Mexico are not going to spill over into our country. Certainly, the flood of illegal immigrants has no trouble spilling over into the United States from Mexico, as our government has taken no effective and resolute action to end the crisis at our southern border. Today, harmful illegal drugs are killing Americans from coast to coast, and destroying the fabric of society. Tomorrow, Mexico’s cartels and criminals will be establishing themselves within our borders. It’s fair to say that many already have, and are operating with relative impunity. When is the United States going to stand up and take action? To the best of our knowledge, the government is doing nothing. Cooperating with Mexico’s police and military is like cooperating with Pakistan. How many more American will have their lives destroyed by drugs, or murdered by drug-related criminals, before the government finally acknowledges and confronts this problem that is tearing our beloved country apart from coast to coast? Human nature doesn’t change. Unless we play hardball, as our country did in the past with effectiveness, we will NOT be taken seriously. Frankly speaking, they are laughing at our lack of will and determination to stop them. As Theodore “Teddy” Roosevelt so aptly said, “speak softly and carry a big stick.” ----------------------------------------------------------------------------------- Eight family members decapitated in north Mexico AFP / July 29, 2015 Eight people from the same family, including two minors, were kidnapped by masked gunmen and their decapitated bodies were found days later in northern Mexico, authorities said Wednesday. The bodies were found after a ninth member of the Martinez family escaped Sunday's abduction near Casa Quemada, in the state of Chihuahua, and alerted the authorities. They were all men, with the youngest aged 15 and the oldest 42. The family was traveling in a vehicle when it was kidnapped by armed men wearing masks and dressed in military-like fatigues. The bodies of three men were found on a rural road on Wednesday. One was 18 years old and the two others were 25. A day earlier, authorities recovered five other bodies that had been dumped in different parts of Casa Quemada. Two of them were aged 15, two others 18 and the oldest 42. Some witnesses said the family had gone to the mountain region to cut wood, while others claimed that the relatives cared for drug fields. The mass murder took place in a region known as the Golden Triangle, which includes the states of Sinaloa, Chihuahua and Durango, where drug cartels grow marijuana and opium poppies. On July 18, 11 men traveling in three vehicles on a dirt road were killed in a remote area of Durango when they were apparently ambushed by armed civilians. Five other men were wounded in the attack, which took place within the Golden Triangle. US law enforcement officials suspect that Sinaloa drug cartel leader Joaquin "El Chapo" Guzman is hiding in the region following his July 11 escape from prison. The state of Chihuahua has endured much of the gruesome violence that has plagued Mexico in a drug war that has left tens of thousands of people dead nationwide since 2006, when soldiers were deployed to combat cartels. The city of Ciudad Juarez, which borders Texas and is part of Chihuahua, was once considered the murder capital of Mexico, though the homicide rate has sharply fallen in recent years. Much of the violence in Ciudad Juarez was attributed to turf wars between the Sinaloa and Juarez drug cartels.
-
Caterpillar Australia Press Release / July 29, 2015 U.S. announcement boosts Cat Trucks business An announcement by Caterpillar Inc. that it will begin independently designing and manufacturing its vocational truck range at a Caterpillar plant in Texas will have no impact on the supply of Cat branded trucks in Australia, New Zealand and Pacific markets. Caterpillar launched its first vocational truck, the CT660, in North America in 2011, built by Navistar. Caterpillar’s announcement in the US concerns Cat’s North America vocational truck range which is available in left hand-drive configuration only, and was never introduced to the Australian, New Zealand and Pacific markets. “The Cat-branded trucks supplied to Australian, New Zealand and Pacific markets are completely different models to the Cat vocational range which is a uniquely Caterpillar product,” comments Glen Sharman, Director of Sales, Marketing and Business Development for Navistar Auspac. “The Cat trucks we offer here are developed specifically for our on-highway markets. “The Cat Trucks range has evolved immensely since the Australian launch in 2010 with models like the CT630S, the CT630SC and most recently the CT630HD rated for roadtrain triples applications. “Navistar certainly wouldn’t be investing in development of these models if it saw anything other than a long and strong future for Cat-branded trucks in our markets,” says Glen Sharman. “Cat trucks are a valuable and ongoing part of Navistar Auspac’s plans for today and tomorrow and any assumptions or speculation otherwise are completely mistaken. Caterpillar truck representatives in the US further state they will continue to source Cat-branded engines such as the CT13 that Navistar builds to power Caterpillar vocational trucks and the CT610 on-highway model in the Navistar Auspac range. “The CT13 engine you see in the Caterpillar truck will continue to be available in the (vocational) truck,” says David Schmitz, Product Manager, Caterpillar Trucks. Furthermore, speculation by some competitors and commentators that Cat’s durable 15 litre engine has a limited future has been firmly refuted by Caterpillar. “Earlier this year we mentioned that we will have a 15 litre announcement later this year and it is still on track,” confirms David Schmitz. “The 15 litre engine is key to future growth.” “The way we see it, this is another highly positive development for Cat Trucks in our region. There is no question that Cat Trucks will continue to grow in the Australian, New Zealand and Pacific markets,” concludes Glen Sharman. http://www.cattrucks.com.au/trucks/
-
Volkswagen Worker Series: The “Experienced” Money Maker
kscarbel2 replied to kscarbel2's topic in Other Truck Makes
http://www.bigmacktrucks.com/index.php?/topic/35895-from-lt-to-worker-volkswagens-versatile-long-lasting-lt-cab/?hl=volkswagen . -
When Freightliner Walked Volvo on a Leash – the US Market N10
kscarbel2 replied to kscarbel2's topic in Other Truck Makes
-
When Freightliner Walked Volvo on a Leash – the US Market N10
kscarbel2 replied to kscarbel2's topic in Other Truck Makes
-
Volvo entered the U.S. market some 38 years in 1974. They signed a few dealers and introduced the F86(US). But they didn’t understand the U.S. market and their launch failed miserably. In 1978, a frustrated Volvo decided to try again. Volvo signed an agreement with Freightliner Corporation under which the American truckmaker became the exclusive importer and distributor of Volvo trucks in the U.S. market. At the same time, the N10(US) conventional was added, and the F6 and F7 replaced the obsolete F86. The N10 was introduced to the global market in 1973, and updated in 1989 resulting in the NL10. The heart of the Volvo N10 conventional was the 9.6 liter (586 cu.in.) TD100C (later renamed D10) rated at 253 horsepower and 671 lb/ft of torque. It was paired with a Volvo model R63 eight-speed direct drive transmission. U.S. sales began in the 1979 model year. American customers didn't care for the small interior cab dimensions, and the engine was considered underpowered. Freightliner's agreement to distribute Volvo trucks in the U.S. market was a savvy move by the truckmaker, providing its dealers for the first time with a complete product range from medium to heavy with which to compete in every market segment. But just as Volvo began to penetrate the U.S. market under the experienced hand of Freightliner, the arrangement ended in May 1981 when Consolidated Freightways sold its Freightliner truck manufacturing unit to Daimler, thus cancelling the Freightliner/Volvo agreement. In August 1981, Volvo purchased the assets of White Motor Company (with the exception of the Cleveland, Ohio plant due to its age and large pension fund liability) to regain a U.S. sales network (White had gone into bankruptcy in September, 1980). Volvo's new U.S. business unit was called Volvo White Truck Corporation and based in Greensboro, North Carolina. In an attempt to address N10 low power criticism, Volvo White Truck Corporation in 1984 introduced the intercooled 12.1-liter (742 cu.in.) TD120 (later renamed D12) powered N12 in the U.S. market rated at 325 horsepower, and sold it thru 1986. I believe that March 1987 was the last build date for U.S. market N10s. Still making no headway (or profit), Volvo purchased a majority stake in General Motor's heavy truck division (GMC) in 1987 to form the Volvo GM Heavy Truck Corp. joint venture and the WHITEGMC brand. GM sold its minority stake in the JV in 1997, and Volvo GM Heavy Truck evolved into Volvo Trucks North America. These acquisitions by the Germans and the Swedes marked the beginning of their battle for dominance in the North American market, and the decline of the U.S. truckmakers. Today in year 2013, as a result of a flagging desire to dominate in our own truck market, the majority of heavy trucks on America's roads today are produced by foreign companies. Related reading - http://www.bigmacktrucks.com/index.php?/topic/30397-when-freightliner-ran-volvo-in-america/ .
-
Originally launched in 1996, the “Worker” gets the job done 24/7 with, shall we say, a few years of on-the-job experience. Available with a wide range of chassis from light medium to heavy, today’s “Worker” is the distribution segment’s go-to truck for a cost-effective delivery solution. Uptime and profitability? You’re asking the right people - our first generation “Worker” wrote the book, and our 2nd gen Worker represents a new chapter in trucking efficiency. At Volkswagen Truck, we understand your needs, challenges and priorities, and give you a competitive edge in business. The “Worker” has been called brilliantly straightforward and innovative, cost-effective and attractive.............who are we to argue? See your Volkswagen Truck dealer today, and experience a new era of cost-effective transport. Volkswagen Truck – We’re right for your business
-
Equipment disparity on Ford F-150 prompts new crash test
kscarbel2 replied to kscarbel2's topic in Trucking News
New test shows disparities in Ford F-150 crash protection Automotive News / July 29, 2015 After a highly unusual follow-up crash test, the Insurance Institute for Highway Safety has concluded that Ford Motor Co. “shortchanges” some buyers of its redesigned 2015 F-150 pickups by equipping certain models with protective steel bars while leaving them off others. In separate crashes, a four-door crew cab F-150 SuperCrew aced IIHS’s tests and earned the safety agency’s coveted Top Safety Pick rating. But an extended cab SuperCab version of the F-150 received the second-lowest rating of “marginal.” Why the difference? IIHS says it comes down to four protective steel bars that Ford installed on the SuperCrew that are left off the SuperCab. The tubular bars, welded to the frame and placed in the front wheel wells, also are missing from regular cab F-150s. David Zuby, IIHS’s chief research officer, said leaving the bars off the SuperCab “shortchanges buyers who might pick the extended cab thinking it offers the same protection in this type of crash as the crew cab.” “It doesn’t,” he said. “In a small-overlap front crash like this, there’s no question you’d rather be driving the crew cab than the extended cab F-150.” In an e-mailed response to questions from Automotive News, Ford spokesman Mike Levine said Ford will add "countermeasures to the SuperCab and Regular Cab for the 2016 model year. The type of countermeasure and structure will vary by cab type." Changing course The IIHS originally tested the SuperCrew in April under its usual procedures to test only the highest-volume version of vehicle nameplates. The researchers were not planning to test any other F-150s. The institute changed course after learning from Automotive News that the SuperCab lacks the SuperCrew’s wheel blockers. The IIHS, a 55-year-old nonprofit funded by auto insurers and based in Arlington, Va., plans to release the results of the new tests Thursday. Automotive News obtained an advanced copy of the report through another source and was granted access to IIHS’s chief research officer. “Based on these two tests, those structures which extend from the outboard edges of the frame rails seem to do a good job of protecting the occupant compartment from excessive intrusion in this type of crash,” Zuby said. Wheel protectors As Automotive News first reported, SuperCrew F-150s come standard with a pair of what Ford calls “protectors” in front of and behind each front wheel. The tubular steel bars extend out from the frame, absorbing energy in a frontal impact and deflecting the wheel away from the passenger cabin. The IIHS and many engineers call the devices wheel blockers. The 2015 models without the protectors -- the SuperCab and regular cab pickups -- historically account for about 25 percent and 5 percent of total F-150 sales, respectively, according to a Ford spokesman. The IIHS already had tested the SuperCrew F-150 in April when Automotive News informed it that only the SuperCrew had the protective bars. The revelation prompted the agency to delay a planned report on F-150 crash safety and to conduct a second test, on June 11, this time on a SuperCab. In May, when Automotive News asked a Ford spokeswoman why the protectors were on the crew cab but not other versions, she said, “It’s something that we do regularly. It’s to optimize the structure. All of that is to meet regulatory requirements and achieve public domain ratings.” Asked to clarify what public domain ratings were, she replied, “crash testing.” Spokesman Levine said Ford had no plans to recall 2015 F-150s without the blockers, which the company calls Small Offset Rigid Barrier countermeasures. "We are evaluating which specific changes we will make to the SuperCab and the Regular Cab to improve performance in the IIHS small-overlap front crash test," he said. "It is important that any changes do not compromise performance on other crash tests." Levine added: “The 2015 F-150 is the safest F-150 ever. It is the only full-size, light-duty truck to earn NHTSA’s highest five-star rating for the driver and passenger for all crash test modes and cab configurations. In addition, the 2015 F-150 SuperCrew is the first large pickup in the industry to earn an IIHS Top Safety Pick in the current rating system.” Test results The small-overlap front crash test has proved particularly vexing to automakers since it was introduced in 2012. The test crashes a front corner of the vehicle against a stationary barrier at 40 mph, simulating the vehicle striking an object such as a tree. Many automakers have had difficulty passing the test. The two diverging 2015 F-150 crash test results show why. Comparing the two models, the SuperCrew received a top rating of “good” on every crash test it was subjected to by IIHS. The SuperCab, however, earned a “poor” rating on structure and “acceptable” ratings on restraints and kinematics, as well as hip and thigh and lower leg and foot dummy injury measurements. The results all together earned the SuperCab an overall safety rating of “marginal,” one mark above “poor” on IIHS’s four-grade scale. The SuperCrew’s occupant compartment remained intact, IIHS said, and the crash-test dummy had a low probability of injury thanks to the pickup’s structural and in-cabin safety equipment. However, in the SuperCab, “intruding structure seriously compromised the driver’s survival space,” IIHS said. The brake pedals and toepan were pushed back between 10 and 13 inches toward the driver, and the steering column was pushed back nearly 8 inches toward the driver’s chest. The crash-test dummy’s head “barely contacted the front airbag before sliding off to the left and hitting the instrument panel,” IIHS said. The IIHS does not plan to test the regular cab F-150, which has a very similar underlying structure to the SuperCab. Important marketing Pickup safety is big business for automakers, especially because women influence the vast majority -- about 70 percent -- of all pickup purchasing decisions. This spring, the National Highway Traffic Safety Administration subjected all three cab versions of the F-150 to its own battery of crash tests. All three earned five stars, the federal agency’s highest rating, and the achievement features prominently in Ford’s F-150 marketing. NHTSA, however, does not conduct a test similar to the IIHS’s small-overlap test. While NHTSA’s testing judged all three F-150s as equal, the IIHS’s testing showed that one configuration -- the SuperCrew -- was safer than the others, at least in the small-overlap frontal crash test. Under IIHS rules, a vehicle must get a “good” or “acceptable” rating on the small-overlap and other tests to receive the group’s Top Safety Pick designation. IIHS researcher Zuby declined to speculate on why Ford put the protectors on its SuperCrew but not on other F-150s. “I think automakers are trying to design the vehicles to offer the best protection for their customers,” he said. “But occasionally, we do see evidence that maybe they are trying to get a good rating in a test, maybe without looking for a completely holistic solution.” Ford spokesman Levine said “the F-150 program was well underway when this [small offset rigid barrier] test mode was introduced.” Zuby said IIHS is always careful to identify which vehicle variant it is crash testing, but, he said, sometimes consumers make assumptions that might not be accurate. “Which is why, when we saw this issue, we decided to do the extra test,” Zuby said, “just so that we would be providing complete information to the public.” Related photographs - http://www.autonews.com/article/20150729/OEM11/150729843/new-test-shows-disparities-in-ford-f-150-crash-protection -
GM prices diesel Colorado from $31,700; towing capacity set at 7,700 pounds Automotive News / July 28, 2015 The diesel-powered Chevrolet Colorado will be priced from about $31,700 to $38,700, including destination charge, when it debuts this fall. Chevy will only offer the 2.8-liter Duramax diesel in mid- and upper-trim LT and Z71 crew cab models, in both two-wheel-drive and four-wheel-drive configurations. The diesels will be offered at a $3,730 premium to those models equipped with a 3.6-liter V-6 engine. Chevy executives believe the diesel offering will give the Colorado an edge on the Toyota Tacoma, the top-selling midsize pickup, with 88,801 units sold in the first half of the year, more than double that of the Colorado (41,575). They also hope it's an answer to the Ram 1500 Eco Diesel, the only full-size half-ton pickup with a diesel. Chevy engineers have said they expect the diesel Colorado's fuel economy rating to surpass 30 mpg in highway driving, which would eclipse the diesel Ram's 29 mpg rating. The Colorado’s 2.8-liter diesel will generate 181 horsepower and 369 pounds-feet of torque. It will have a towing capacity of 7,700 pounds, up from 7,000 for the 3.6-liter V-6. Along with greater capability and efficiency, it expands the Colorado lineup to give customers more choices and the capability of exploring more possibilities on and off the road, Sandor Piszar, director of Chevrolet truck marketing, said in the statement. GM spokesman Otie McKinley said Chevy would consider offering the diesel engine on lower trim packages if consumer demand warrants it. The GMC Canyon will get the same engine. The price will range from about $33,200 on an SLE 4X2 crew cab with a 5-foot bed to about $41,900 for a top-trim SLT 4X4 with a 6-foot bed. The all-new 2.8-liter engine, which is made in Thailand, will be paired with a six-speed automatic transmission that features a vibration-absorbing system to dampen noise. The diesel Colorado will include an exhaust-braking system, which enhances control and prevents brake wear on steep downhill descents.
-
Magirus introduced the third generation of its legendary conventional cab series in 1971. Known as a Magirus-Deutz Eckhauber (meaning conventional truck), they featured air-cooled Deutz engines and became legendary in the vocational and specialty truck segments. So popular were the all-wheel-drive variants of this truck that Iveco produced it thru 2003 (You can more or less still buy a new Eckhauber today.....from SAMIL in South Africa - http://www.samiltrucks.co.za/). Photographs of older Magirus-Deutz trucks - http://www.hansreckweg.dk/truckerlinks/engelsk/magirus.htm .
BigMackTrucks.com
BigMackTrucks.com is a support forum for antique, classic and modern Mack Trucks! The forum is owned and maintained by Watt's Truck Center, Inc. an independent, full service Mack dealer. The forums are not affiliated with Mack Trucks, Inc.
Our Vendors and Advertisers
Thank you for your support!