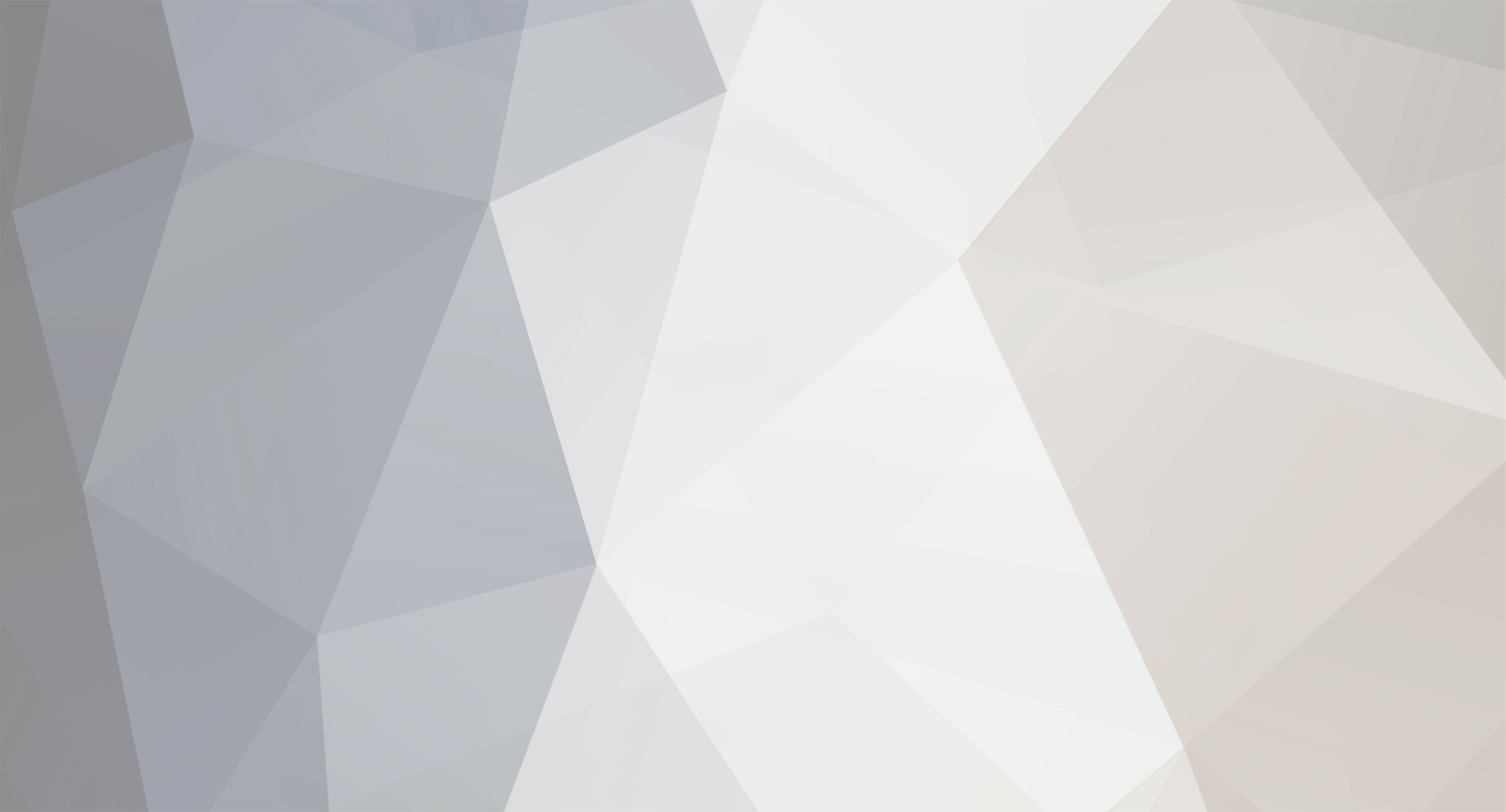
kscarbel2
Moderator-
Posts
18,744 -
Joined
-
Days Won
114
Content Type
Profiles
Forums
Gallery
Events
Blogs
BMT Wiki
Collections
Store
Everything posted by kscarbel2
-
GM prices diesel Colorado from $31,700; towing capacity set at 7,700 pounds Automotive News / July 28, 2015 The diesel-powered Chevrolet Colorado will be priced from about $31,700 to $38,700, including destination charge, when it debuts this fall. Chevy will only offer the 2.8-liter Duramax diesel in mid- and upper-trim LT and Z71 crew cab models, in both two-wheel-drive and four-wheel-drive configurations. The diesels will be offered at a $3,730 premium to those models equipped with a 3.6-liter V-6 engine. Chevy executives believe the diesel offering will give the Colorado an edge on the Toyota Tacoma, the top-selling midsize pickup, with 88,801 units sold in the first half of the year, more than double that of the Colorado (41,575). They also hope it's an answer to the Ram 1500 Eco Diesel, the only full-size half-ton pickup with a diesel. Chevy engineers have said they expect the diesel Colorado's fuel economy rating to surpass 30 mpg in highway driving, which would eclipse the diesel Ram's 29 mpg rating. The Colorado’s 2.8-liter diesel will generate 181 horsepower and 369 pounds-feet of torque. It will have a towing capacity of 7,700 pounds, up from 7,000 for the 3.6-liter V-6. Along with greater capability and efficiency, it expands the Colorado lineup to give customers more choices and the capability of exploring more possibilities on and off the road, Sandor Piszar, director of Chevrolet truck marketing, said in the statement. GM spokesman Otie McKinley said Chevy would consider offering the diesel engine on lower trim packages if consumer demand warrants it. The GMC Canyon will get the same engine. The price will range from about $33,200 on an SLE 4X2 crew cab with a 5-foot bed to about $41,900 for a top-trim SLT 4X4 with a 6-foot bed. The all-new 2.8-liter engine, which is made in Thailand, will be paired with a six-speed automatic transmission that features a vibration-absorbing system to dampen noise. The diesel Colorado will include an exhaust-braking system, which enhances control and prevents brake wear on steep downhill descents.
-
Magirus introduced the third generation of its legendary conventional cab series in 1971. Known as a Magirus-Deutz Eckhauber (meaning conventional truck), they featured air-cooled Deutz engines and became legendary in the vocational and specialty truck segments. So popular were the all-wheel-drive variants of this truck that Iveco produced it thru 2003 (You can more or less still buy a new Eckhauber today.....from SAMIL in South Africa - http://www.samiltrucks.co.za/). Photographs of older Magirus-Deutz trucks - http://www.hansreckweg.dk/truckerlinks/engelsk/magirus.htm .
-
C.D. Magirus was established in 1866 in Ulm, Germany as a fire apparatus manufacturer. The company, noted for having invented the turntable-mounted ladder, operates today as an Iveco subsidiary (http://www.magirusgroup.com/de/en/home/). In 1916, the company began producing commercial trucks. In 1936, Magirus became the truck manufacturing subsidiary of Klöckner Humboldt Deutz (KHD) AG. Klöckner Humboldt Deutz AG, a designer and producer of a diversified range of air and liquid-cooled diesel engines to this day and known as Deutz AG from 1997, was also a partner with Mack Trucks and Garrett AiResearch in the development of gas turbine engines (http://www.bigmacktrucks.com/index.php?/topic/32014-the-gt-601-gas-turbine-powered-macks/). Owing to the Deutz ownership, Magirus trucks were for years referred to as Magirus Deutz trucks and featured Deutz air-cooled engines. Iveco purchased Magirus from Klöckner Humboldt Deutz AG in 1975*, and continued producing trucks under the Magirus name thru the 1980s. * Iveco (Industrial Vehicles Corporation) on January 1, 1975 brought together five truck brands: Fiat, Lancia and OM from Italy, France’s Unic and Germany’s Magirus Deutz. In 1977, popular Mack veteran Ray Reardon* left his position as vice president of international operations at Mack Trucks under Jack Curcio to form Iveco Trucks of North America. Located in Blue Bell, Pennsylvania (northwest of Philadelphia), the new company's headquarters was conveniently near the Port of Wilmington where Mack Mid-Liners also arrived from Europe. Ray began importing Magirus trucks and sales started off well. He contacted other Mack dealers and they were thrilled with the idea of having a medium truck offering. It was common to see Magirus trucks on the road in the northeast. The North American market Magirus trucks, like the upcoming mack Mid-Liner, featured the "Club of Four" cab (officially known as the Euro Truck Development Group), which had been jointly developed by Saviem (merged into Renault), DAF, Magirus and Volvo. Owing to Fiat’s ownership of Magirus, the Italian owner switched Magirus over from its long time use of air-cooled Deutz engines (with the exception of the Eckhauber models) to its own proprietary liquid-cooled powerplants. With German engineering and assembly, a modern “European Union” cab and Italian power, the U.S. market Magirus was a solid performer in its intended market segment. The 160 horsepower model 160A11FL (17,500lb rear axle) and 16A13FL (20,300lb rear axle) rigid (straight truck), with air-over-hydraulic brakes, compared with the upcoming 175 horsepower Mack Mid-Liner model MS200P. The 200 horsepower model 200A13FL, available as rigid or tractor, with its full air brake system, compared with the upcoming 210-215 horsepower Mack Mid-Liner model MS300P and MS300T. At the time Mack dealers first began signing distribution agreements with Ray, most were unaware that Mack was exploring the possibility of selling Americanized variants of Renault’s medium truck range in the United States. By 1979 however, the Mack dealer body was in the loop on the Mid-Liner launch for 1980, and most were compelled to turn their focus to the Mid-Liner product. Iveco Trucks of North America did live on thru 1990, selling Iveco's Z-Series low-cab-forward light truck. * Mr. Raymond Reardon was a genuine Mack man, and person of the highest caliber. He passed away in 2006 and is sorely missed. .
-
Arkansas judge leaves 18-month-old baby in car, dies from heat The son of Circuit Judge Wade Naramore, who handles juvenile cases in Garland County. 18-month-old Thomas Naramore was found dead Friday afternoon after being left in a car on a day when the temperatures in that area were recorded as high as 101 degrees. Police say the child was in the car an "undetermined" amount of time, possibly up to four hours. Reports have indicated the child was with his father. The Hot Springs police for days refused to provide a copy of the incident report on the call. When they finally did so, it only contained the time of the call to a possible deceased person report. Naramore was released after questioning. Garland County prosecutor Terri Harris requested that a special prosecutor be appointed to investigate the case and that she be recused. Harris hired Naramore, who she called a friend, as a deputy prosecutor in the county before he was elected last year to succeed a retiring judge. Circuit judges in the county have also recused from hearing the case. Scott Ellington, who serves in another jurisdiction, has been appointed special prosecutor for the case. .
-
Dallas father leaves 2-year-old strapped in car, dies from heat Boston News / July 27, 2015 A Dallas man has been charged with child abandonment in the death of his two-year-old daughter who was left in a hot car. Dallas police on Monday arrested 40-year-old Hamuda Raufu in the July 17 death of his daughter, Sekinat. The girl's parents told police the family spent the day at Fair Park, drove home and went inside and took a nap. They thought all five of their children had got out of the vehicle. The father awoke and went outside to work on the car, then noticed the girl still strapped in her child safety seat in the back seat of the vehicle. Raufu estimated the girl was unattended in the car for about an hour, though the exact time is unknown, according to the affidavit. Police said the temperature was 98 degrees between 4 and 6 p.m., the time-frame police believe Sekinat was left in the car. Raufu said he took the toddler inside and his wife performed CPR for 30 minutes before they drove to Children's Medical City Hospital in Dallas. (Never called 911) They arrived shortly before 7 p.m. and the child was declared dead about 30 minutes later. Child Protective Services was then notified. In a news release, Dallas police said during their investigation into the child's death, 'additional information was developed regarding the circumstances of the child's death, the actions of both parents, and other child witnesses.' From that, a warrant was issued for Raufu's arrest and he was taken into custody Monday by officers with the U.S. Marshals Office. A judge set bond at $5,000 for Raufu. (The dead two-year-old’s life is only valued at $5,000 ?) No other charges have been made at this time. .
-
California teen murders 8-year-old girl Associated Press / July 28, 2015 A 15-year-old boy lured an 8-year-old girl into his apartment and killed her before hiding her body in a recycling bin at the housing complex for artists where they lived, authorities said Tuesday. Police say on Sunday, Adrian Jerry Gonzalez lured Madyson Middleton into his family's apartment from a courtyard at an artists' complex where they both lived. Once inside, he tied her up, sexually assaulted and killed her. Police say Gonzalez then hid the girl's body in a recycling bin. Gonzalez, who police say knew the girl as a neighborhood acquaintance, was arrested on suspicion of murder. Gonzalez was nearby when the body was discovered, and officers found evidence in the apartment that links him to the slaying, the police chief said. Prosecutors are considering bringing charges against the boy as an adult, Santa Cruz District Attorney Jeffrey Rosell said. ---------------------------------------------------------------------------------------------------------- Update: California girl, eight, died of asphyxiation, stab wounds Reuters / August 13, 2015 An 8-year-old girl whose body was discovered last month in a recycling bin at a residential complex in the seaside California city of Santa Cruz died of asphyxiation and stab wounds to the neck, officials said on Thursday. Santa Cruz County Sheriff's Office spokesman Lieutenant Kelly Kent said the coroner ruled Madyson Middleton's death a homicide. Prior to the discovery of her body, she was last seen on the evening of July 26 riding a scooter at the Tannery Arts Center housing complex. Adrian Jerry Gonzalez, 15, was charged as an adult with lying in wait before kidnapping, raping and killing Middleton. Gonzalez appeared in court last month but entered no plea, and a subsequent arraignment was scheduled for Sept. 21. Police said Middleton knew Gonzalez, who lured her to his family's apartment at the center, which offers affordable housing to artists, and killed her. Gonzalez, who acted alone, concealed her body inside a recycling bin downstairs, according to police. He was arrested while watching detectives near the bin where Middleton's body was found, police said. Police said the girl was likely killed before she was even reported missing. Local, state and FBI agents helped by law enforcement dogs searched for Middleton in Santa Cruz, a socially liberal community about 60 miles (97 km) south of San Francisco, and local residents also canvassed the area where she was last seen. .
-
Irrational exuberance – US Dentist Pays $50,000 to Slay African Lion July 28, 2015 Cecil the lion, a famous black-maned resident of Zimbabwe’s Hwange National Park, has died at the hands of a U.S. dentist. American Walter Palmer paid $50,000 to hunt and kill the endangered lion with a bow and arrow. The incident occurred around July 6, with a professional hunting outfit reportedly luring Cecil outside the boundaries of the protected reserve using a dead animal as bait. “Mr. Palmer shot Cecil with a bow and arrow but this shot didn't kill him,” Johnny Rodrigues, chairman of the Zimbabwe Conservation Task Force, said in a statement. “They tracked him down and found him 40 hours later when they shot him with a gun. Cecil, who was known all over the world, would have earned millions of dollars just from sightseeing." It wasn’t the first kill for Palmer, who has multiple photos posted on the website Trophy Hunt America showing the Minnesota resident posing with dead lions, rhinos, water buffalo, warthogs, and other animals. Palmer was the hunter listed on the permit documents, and a spokesperson for Palmer says that Palmer believes he is the one responsible for the lion’s death. “Walter believes that he might have shot that lion that has been referred to as Cecil,” the spokesperson said. “What he’ll tell you is that he had the proper legal permits and he had hired several professional guides, so he’s not denying that he may be the person who shot this lion. He is a big-game hunter; he hunts the world over.” Park rangers and regular visitors knew the 13-year-old lion as a tourist attraction, easily approached by safari guide jeeps for photo opportunities. Cecil had a propensity for lounging in the middle of roads, said Bryan Orford, a former park guide and a longtime visitor to Hwange. Hunting such an easy target only made the killing of Cecil even more wrong, he said. “I used to drive down the railway line road following Cecil and had to wait for him to get off the road,” says Orford. “This walking in front of the vehicle would go on for ages. Other times he would lie in the road, and you had to drive off the road to go around him.” The death of Cecil not only means one less endangered African lion in the world but also could mean the demise of a whole line of cubs sired by the leader of the Hwange pride. “The saddest part of all is that now that Cecil is dead, the next lion in the hierarchy Jericho will most likely kill all Cecil's cubs so that he can insert his own bloodline into the females,” Rodriques said. “This is standard procedure for lions.” http://www.dailymail.co.uk/ushome/index.html .
-
Transport Brasil / July 28, 2015 Model units 170E22 should act in SEDEX operations in Brazil Iveco has delivered 51 Tector model 170E22 medium trucks to Brazil’s post office. The completion of the sale was the final stage of a bidding process headed by the Sales to the Government, Special Vehicles and Commercial Logistics Platform of the automaker. "What we have here is a concerted effort, which culminated with a great victory for the brand," said Osmar Hirashiki, Director of Corporate Sales and Sales to the Government of Iveco. The trucks are powered by Fiat Powertrain Technolgies’ NEF 6 Euro-5 engines, which provides a 5 percent reduction in fuel consumption and strong performance. The trucks will be operated by SEDEX, the Brazilian post office’s express package delivery arm. .
-
Scania Press Release / July 27, 2015 A cable car system, a vineyard and a diamond vessel. Sometimes they need extra power to do their job. Our engine calendar profile, Johan Louw and his team make sure that Sub-Saharan Africa’s got the power. “Our job is very challenging. The things we power varies from vineyards to mines. Not any day is like the other,” says Johan Louw, sales manager for Scania Engines in Sub-Saharan Africa. Johan specifically mentions one assignment he and his team will never forget. It was a joint effort between a diamond entrepreneur, a boat builder and Scania – they constructed a marine mining solution resulting in a boat that vacuums the ocean floor for diamonds. “The project took about a year and a half and we learned a lot from it. Now we’re proud to be part of the second phase, which involves a much bigger boat.” The diamond boat is similar to a fishing vessel but completely custom made for its purpose. The Scania engine in combination with an extra large propeller powers the system that blows sediment from the bottom of the ocean and transports it like a giant “vacuum cleaner” to a sorting area that moves the gravel of correct size into the storage area on the boat. “This concept may be the only one in the world. There are similar systems, but on a smaller scale. I actually think this concept could set a new industry standard,” Johan says. To be involved in such an exciting project is part of the everyday life for Johan and his team. The Table mountain project is another example, where they needed to deliver a new standby genset on top of the 1085 meters high mountain to power a cable car system and a restaurant. The delivery was carried out in a spectacular fashion, with a helicopter lifting the genset into position. Of course not all assignments are that spectacular. Providing gensets for vineyards or tea farms is more of a daily business, however, providing power to any business is satisfying. Johan’s colleague Sonya de Carvalho joins in the conversation by saying: “My dream is to see us develop in other segments of Scania; to see where it goes. If we can’t achieve any of those, personally, I´d start baking wedding cakes.” .
-
The Morning Call (Allentown, Pennsylvania) / July 28, 2015 The federal Export-Import Bank expired June 30 when Congress failed to renew its charter. The bank is a small federal agency that helps U.S. companies sell their products overseas, by underwriting loans to foreign customers. Conservatives oppose it as corporate welfare and are pushing to keep it dead. But late Monday the Senate voted 64-29 to add legislation reviving the bank to a sweeping highway bill being considered on the floor. Five things to know about the Export-Import Bank and its future: PATH AHEAD Despite the Senate's action on a measure to revive the bank and extend it through 2019, its future is far from assured. The House announced plans Tuesday to pass a three-month highway extension that does not include an Export-Import Bank provision — and then adjourn for the summer. The Senate will likely be forced to adopt the House bill or watch transit programs lapse. That means the bank will stay shuttered at least into the fall, when Congress returns from its annual August recess. NOT DEAD YET Even though the bank's charter expired at the end of June, it remains in business to service more than $100 billion in outstanding loans and guarantees. The agency itself is funded, including employee salaries, through Sept. 30. DEBATE ABOUT THE BANK'S ROLE Conservatives say the Export-Import Bank amounts to corporate welfare, pointing out that the companies that benefit include major corporations like Boeing, Caterpillar and GE which they say can support themselves without taxpayers' help. Supporters of the bank, including groups like the Chamber of Commerce and National Association of Manufacturers, argue that most other countries have export credit agencies, in some cases more generous than the U.S. version. Supporters say it will be harder for U.S. companies to compete overseas if their competitors are supported by the government and they aren't. The bank says that last year it authorized $20 billion worth of transactions which supported $27.5 billion of U.S. exports and 164,000 U.S. jobs. And it says it has a default rate of less than 1 percent. Opponents argue that the bank mostly helps big businesses. Of the $20.5 billion in financing and insurance authorized by the bank in 2014, just over $5 billion of that was for small business exporters, according to bank officials. But if the transactions themselves are counted up, more small businesses are helped than big ones. It's just that the amounts spent on them are smaller. RIFE WITH POLITICS In past years the bank was renewed with little or no controversy and sometimes without so much as a roll-call vote. But after a tea party-infused GOP majority retook the House in 2010, conservatives began seizing on the bank as crony capitalism and a federal agency ripe for elimination, making a 2012 reauthorization vote a struggle for the first time. Outside groups like Club for Growth and Heritage Action for America made it an issue, and this year, with Republicans in control of the Senate and a presidential campaign underway, conservatives have targeted the Export-Import Bank even more assertively. Adding to the pressure, the billionaire GOP Koch Brothers took on the cause through their allied organizations Americans for Prosperity and Freedom Partners, pressuring GOP presidential candidates who are jockeying for the Kochs' coveted financial backing to toe the line. The issue provoked extraordinary GOP infighting in the Senate in recent days as presidential candidate Sen. Ted Cruz, R-Texas, accused Majority Leader Mitch McConnell, R-Ky., of lying to him about whether there was a deal to revive the bank. McConnell disputed the accusation. 81-YEAR HISTORY The bank was created by Franklin Delano Roosevelt in 1934, during the Great Depression. His aim was to help the U.S. "re-engage economically with the rest of the world," according to the State Department historian. The bank was initially established to help trade with the Soviet Union, and a second version was meant to boost trade with Cuba, but the two entities were soon merged and began extending efforts around the globe.
-
Commercial Carrier Journal / July 28, 2015 Caterpillar made the decision to bring its truck production in-house, says Cat’s Chris Chadwick, to better serve its yellow-iron oriented customer base. “There is a lot of integration throughout our construction equipment line,” he explains. “And it will be a lot easier for us to continue to fully integrate our trucks with our construction machinery if we take full control of the manufacturing process. It also better places us to serve our customers’ needs in a quicker and more satisfactory manner.” The break with Navistar is significant, Chadwick notes, but not absolute. “The majority of the truck parts used on our CT Series our outsourced from various suppliers and we will purchase and use the very same components with our truck that Navistar does today,” he says. One exception, however, is under the hood. Noting that Caterpillar has “no plans” to re-enter the on-highway engine business, Chadwick says for now, Caterpillar will continue to spec the Navistar-built CT13 13-liter diesel engine for its C-Series trucks. “The big hole for us right now is obviously the lack of a 15-liter engine,” he says. “But we have a strategy in place to add a 15-liter option before year’s end and will offer more details on that in the fall.” Chadwick says the addition of the 15-liter engine option will close out the primary phase of Cat’s C-Series product launch. “From that point, we’ll begin the process of new features and technologies to continue to build the brand.” Those efforts will see increased sales efforts in Canada and Latin America, he notes, while Caterpillar will continue to monitor truck markets around the world to seek additional overseas sales opportunities if they make sound financial sense. “Caterpillar is in a unique position to serve the construction industry,” Chadwick explains. “There isn’t another truck OEM out there that can tie one set of solutions for construction machinery to its on-highway solution the way we can. Coupled with the significant competitive advantage offered by our dealer network, we felt this move was the best way to leverage all of these assets and make sure we continue to offer the best vocational truck options available to our loyal customer base.”
-
Cat Trucks to Initially Continue as Built by Navistar Heavy Duty Trucking / July 28, 2015 Caterpillar’s go-it-alone vocational truck series will be virtually identical to current Cat Trucks for some time, using the same components as now until changes come about in the future, according to CAT executives, clarifying after the earlier announcement that the company will end the manufacturing agreement that has Navistar building the trucks at its plant in Escobedo, Mexico. “Initially they will be exactly the same as the trucks produced by Navistar today,” explained Ron Schultz, sales and product support manager. That should continue for the first 12 to 18 months after production begins sometime next year at Cat’s plant in Texas. It means continued use of the Navistar-supplied 12.4-liter CT13 diesel, as well as the cab and chassis whose designs were adapted from components shared with the International PayStar. No Cat Engines “We anticipate that an announcement on a 15-liter engine will be made soon,” said Dave Schmitz, vocational truck product manager, repeating a statement of several months ago. But “Caterpillar has no plans to get back into the truck-engine market,” so the source of that engine remains confidential. “Velocity and speed to market for changes, and better ability to respond to customer requests” for improvements comprise the reason for the shift to Cat producing the truck itself, said Chris Chadwick, director of Caterpillar’s Global On-Highway Truck Group. However, Caterpillar was not unhappy with the Navistar relationship, and the supplier agreement remains in force. "Made in America" sentiment did not enter into the decision to pull assembly into the U.S., "but it's a plus," said Chadwick. Navistar will continue building Cat Trucks until the end of 2016, and during that time Cat will begin phasing in its own truck production at a plant in Victoria, Texas, north of Corpus Christi. The plant opened in 2012 to produce hydraulic excavators, and will be equipped and 200 workers added to build the Cat on/off-road vocational product line. Cat wants to expand the Cat Truck line into more applications, particularly for versions powered by the upcoming 15-liter diesel, Chadwick said. Cat dealers who sell and service the trucks will remain vital to the endeavor. Navistar: 'Niche Product' For Navistar, the Cat Truck was “a niche product, maybe 1,000 or 1,100 a year,” said spokesman Steve Schrier. Navistar’s plans for a new “premium” line of International severe-service trucks, which the company announced today, might be revealed later this year or next year., “We were in that premium vocational market years ago, but we left it after we had no 15-liter engine,” Schrier explained, when Navistar decided not to use the Cummins ISX15 with SCR in 2010 and later dropped its own 15-liter. “Now that we have a 15-liter [from Cummins] again, we’ll go back to it. And of course we’ll still use our own N13 engine.” The collaboration with Cat gained Navistar access to design knowledge about premium details, including cab interior components, that could be used in the upcoming International model, Schrier said. He declined to add more specific details.
-
Transport Topics / July 28, 2015 Paccar Inc. reported a record profit in the second quarter as truck sales continued to rise in North America and Europe. The truck and engine maker said its net income climbed to $447.2 million, or $1.26 per share, up from $319.2 million, or 90 cents, a year ago. Revenue at Paccar’s truck segment increased 15% to $3.98 billion, while total revenue including its parts and financial services operations rose 11% to $5.08 billion. Paccar’s operating companies build Kenworth and Peterbilt trucks in North America and DAF trucks in Europe. Paccar’s worldwide truck deliveries increased over 23 percent to 41,600 units from 33,700. Sales in the United States and Canada rose 31 percent to 26,800 trucks, up from 20,500 in the same period last year. In the global market, DAF and Paccar brand sales rose 12 percent from 13,200 to 14,800 units. Paccar also raised the lower end of its projection for full-year Class 8 industry retail sales. The company said it now expects U.S. and Canadian heavy-duty truck sales to be between 270,000 and 290,000 units, up from 250,000 in 2014. Last quarter, Paccar had estimated that sales would be in the range of 260,000 to 290,000. “Our customers are benefiting from strong freight tonnage, good freight rates and the excellent operating efficiency of Kenworth and Peterbilt trucks,” Paccar Executive Vice President Dan Sobic said. “Industry truck demand is being driven by economic growth and expansion of fleet capacity.” In the first half of 2015, Paccar’s net income rose to $825.6 million, or $2.32 per share, from $593.1 million, or $1.67 per share, in the same timeframe last year. Total revenue rose 11% to $9.91 billion.
-
$34,000 to $35,000 for a mid-sized 2-wheel-drive short-bed pickup all proves that GM is clueless about the small (mid-sized) pickup truck segment. Want a plain jane work truck spec diesel Colorado or Canyon with the diesel to optimize your business overhead? Sorry, Government Motors doesn't offer it. Mary (Barra), way to go..
-
Car & Driver / July 28, 2015 General Motors made us wait a year for its Duramax four-cylinder diesel, but this fall it will join the Ram 1500 EcoDiesel as only the second compression-ignition engine offered to U.S. pickup buyers outside the heavy-duty segment. For 2016, the Chevrolet Colorado and GMC Canyon gain this third engine choice beyond their 200-hp 2.5-liter inline-four and 305-hp 3.6-liter V-6. As we’ve previously detailed, the Thai-built 2.8-liter turbo-diesel inline-four makes 181 horsepower at 3400 rpm and 369 lb-ft of torque at 2000 rpm. The $3,730 diesel engine option will be available only on crew-cab versions (and limited to LT and Z71 trims on the Colorado, SLE and SLT on the Canyon). The diesel can be spec’d with either two- or four-wheel drive. The Z82 trailering package (hitch receiver, seven-pin connector, and a diesel-only trailer-brake controller) comes standard along with a locking 3.42:1 rear differential (versus the gasoline four’s 4.10:1) and driver-switchable exhaust brake. All this, plus a required safety package (forward-collision and lane-departure alerts; $395) and convenience package (rear-window defroster with sliding glass, fog lamps, remote start, damped tailgate; $690) brings the diesel’s base price to $33,520 for the Chevy and $34,875 for the GMC. For reference, those prices are for the LT and SLE 4×2 short-bed models. Packed into the premium are powertrain features like cooled exhaust-gas recirculation (EGR), a balance shaft for smoother operation, and ceramic glow plugs. The Duramax also can run up to 20-percent biodiesel. New for all Colorados and Canyons is a centrifugal pendulum vibration damper, a set of springs and dampers attached to the six-speed automatic’s torque converter that cancels out shaking from the engine. EPA fuel-economy figures, which are expected to include 30-plus-mpg highway, haven’t been announced. But compared with the gasoline V-6, the diesel 4×2 can tow 700 pounds more (7700) and an extra 600 pounds in 4×4 trim (7600). Payload capacity is up, too, but since GM has not released curb weight figures we can only guess they’re up by close to 200 pounds. Everything else about the 2016 Colorado and Canyon, diesel or gasoline, is the same for 2016 save for a few new tech features. Apple CarPlay, the interface that mirrors the iPhone’s functionality on the MyLink infotainment system, is now available (Android Auto is on its way next year). Apple Siri Eyes Free, which integrates the iPhone’s voice controls with the vehicle, is now available along with text-message support. Plus, LT and Z71 models get a new multicolor LCD on the instrument panel. Related photographs - http://blog.caranddriver.com/2016-chevrolet-colorado-and-gmc-canyon-duramax-diesel-details-and-pricing-released/
-
There's something unsettling about seeing a Class 8 tractor flying through the air. But if it must be done, it appears that Gregg Godfrey has his front/rear weight distribution worked out. He set a new record of 166 feet. https://www.youtube.com/watch?v=tJlB5K6JXm4
-
Caterpillar to build trucks on its own Fleet Owner / July 28, 2015 It’s the beginning of the end for the nearly six-year truck-building partnership between Caterpillar and Navistar, as the heavy equipment maker expects to start building vocational trucks on its own beginning next year. The company noted that it will begin independently designing and manufacturing its CT line of vocational models at its plant in Victoria, TX; a facility that originally opened in 2012 to produce hydraulic excavators. Navistar currently manufactures those trucks at its Escobedo, Mexico, plant. “The on-highway vocational truck product family is important to our product line; customers like our trucks and want to include them in their fleets in a variety of heavy duty applications such as dump trucks, mixers, haulers or one of the other configurations we offer,” noted Chris Chadwick, director of the Caterpillar’s global on-highway truck group, said in a statement. “Our updated strategy reaffirms our commitment to grow and develop our presence in the vocational truck industry moving forward.” Caterpillar partnered with Navistar back in 2009 to build what became a three-truck product line for the North American market, starting with the CT660 in 2011 and finishing up with the CT680 back in March this year. “We appreciate the collaboration we have had with Navistar,” Chadwick said. “As we look to future launches of new truck models, this updated strategy will better position us to help provide our customers with the best products and services for this market. The company added that the “transition process” will begin immediately, with truck production at the Victoria factory expected to begin in the first half of 2016. Caterpillar added that it will continue to produce excavators at the Victoria plant, adding around 200 new jobs at the facility to handle truck manufacturing needs. Chadwick added that Caterpillar dealers will continue to sell and support Cat vocational trucks as well. The Wall Street Journal noted that sales of Caterpillar’s vocational truck have only numbered around 1,000 annually; a number Caterpillar hopes to boost significantly by bringing production of those vehicles in-house. The newspaper added that company also plans to build its own line of truck engines to power its CT models – a line of business it exited back in 2008 due to the imposition of restrictive federal exhaust emission standards. For its part, Navistar said it plans to launch a new line of “premium vocational trucks” in early 2016, leveraging “shared technology, intellectual property, supplier collaboration and licensing agreements” developed during its partnership with Caterpillar. “Navistar and Caterpillar have had a strong, collaborative working relationship through a number of projects and partnerships for many, many years,” noted Bill Kozek, president of Navistar Truck and Parts, in a statement. “This next phase provides Navistar with an exciting opportunity to introduce new technologies and product features into our new line of premium vocational trucks that we’ll launch in 2016,” he added. Kozek also stressed that Navistar will continue to manufacture trucks for Caterpillar through December 31 of next year as Caterpillar brings its Victoria, TX, plant up to full speed.
-
Navistar Press Release / July 28, 2015 Navistar today announced that it will launch a new line of premium vocational trucks for the severe service segment beginning in early-2016, leveraging shared technology and intellectual property from its venture with Caterpillar. In addition, the company announced that it will transition to Caterpillar the production and engineering of the Cat-branded severe service trucks the company has been supplying to Caterpillar since 2011. Navistar will continue to manufacture trucks for Caterpillar through December 31, 2016. While specific terms of the transition will not be disclosed, both companies will have the opportunity to leverage certain joint intellectual property, collaborate with suppliers and utilize licensing agreements moving forward. "Navistar and Caterpillar have had a strong, collaborative working relationship through a number of projects and partnerships for many, many years," said Bill Kozek, president, Navistar Truck and Parts. "This next phase provides Navistar with an exciting opportunity to introduce new technologies and product features into our new line of premium vocational trucks that we'll launch in 2016." The company expects to provide additional details on its new premium vocational trucks in the months ahead.
-
Wall Street Journal / July 28, 2015 Caterpillar said Tuesday that it plans to build its own line of dump trucks at a plant in Texas and wind down an existing arrangement it has with engine maker Navistar International Corp. to build the trucks. Caterpillar has been selling the on-road trucks built by Navistar since 2011. Beginning in the first half of 2016, Caterpillar expects to begin assembling the trucks at its plant in Victoria, Texas. The plant opened in 2012 to assemble excavators that had been built in Japan and imported to North America. Bringing the truck family into Caterpillar is expected to add roughly 200 jobs at the Texas plant, which also will continue produce hydraulic excavators, according to Caterpillar. The Navistar-built, Caterpillar-branded trucks haven't been a big hit with truck buyers. Sales of the three truck models have averaged about 1,000 total annually for the past three years. The change could help Caterpillar more effectively leverage its reputation with the construction industry for high-quality machinery, because customers will know it is making the trucks. Building the trucks itself would also add work for the Texas plant at a time of falling demand for the construction excavators it was set up to manufacture. Navistar has been building the Caterpillar trucks at plant in Mexico. Navistar plans to introduce a premium version of the PayStar next year, leveraging shared technology and intellectual property from the venture with Caterpillar, as it tries to revive its slumping market share in heavy-duty trucks by emphasizing vehicles for vocational and specialty applications. Both companies "will have the opportunity to leverage certain joint intellectual property, collaborate with suppliers and utilize licensing agreements moving forward," says Navistar. Navistar said it plans to release additional details about the planned truck line in coming months. (http://www.bigmacktrucks.com/index.php?/topic/41133-international-truck-to-introduce-new-line-of-premium-vocational-trucks-as-navistar-caterpillar-conclude-severe-service-truck-agreement/) The Caterpillar-Navistar partnership was devised in 2009 with ambitious goals to market Caterpillar-branded trucks in several overseas markets through Caterpillar dealers. Those plans were mostly scaled back when sales of the trucks were anemic in North America. Related reading - http://www.drivecat.com/blog/2015/08/truck-manufacturing-moves-to-u-s-caterpillar-facility/
-
Navistar Completes Order to Supply Quality Cos. With 9,000 Trucks Transport Topics / July 27, 2015 Navistar has finalized an agreement to supply Quality Cos. with 9,000 Class 8 tractors during the next three years. Quality Cos., a provider of truck- and trailer-leasing services, is a subsidiary of truckload carrier Celadon Inc. Navistar said the order consists primarily of International ProStar and LoneStar Class 8 tractors powered by the Cummins ISX15 engine. The manufacturer announced last week that it had received an order for the first 1,050 of the 9,000 trucks requested by the leasing company. “We look forward to serving the business needs of Quality Cos. and appreciate the confidence they have placed in our products, our people and our business,” said Bill Kozek, president of Navistar’s truck and parts business. “This order demonstrates our commitment to growth and positions us to support our customers for the next several years,” said Danny Williams, chief operating officer at Quality Cos. Indianapolis-based Celadon ranks No. 42 on the Transport Topics Top 100 list of the largest for-hire carriers in the United States and Canada.
-
Navistar Press Release / July 27, 2015 Navistar today announced that it will be first-to-market with the Eaton Procision line of dual-clutch automated manual transmissions (AMT) for its International DuraStar medium-duty trucks and IC Bus CE series school buses, available in late 2015. Based on Eaton's testing, the new 7-speed transmissions deliver a significant fuel economy advantage compared to a similarly equipped vehicle with a torque converter automatic transmission. The Eaton Procision transmission features a dual-clutch design and electronic shifting that uses grade, vehicle weight and throttle input to provide optimal fuel efficiency and smooth, continuous delivery of torque. "Through our partnership with Eaton, we're offering our customers advanced technologies that provide safe and easy operation for any driver," said Jeff Sass, Navistar senior vice president, North America Truck Sales and Marketing. "Coupled with the reliability of our medium-duty platform, the Eaton Procision transmission delivers the uptime and efficiency our customers require in many driving environments." The Eaton Procision dual-clutch technology allows for more efficient acceleration from a stopped position and optimizes shift points that will efficiently get to the highest gear. Gear changes are made by swapping the engine torque between clutches with the next gear preselected. The dual-clutch module is fully contained within the transmission, hydraulically controlled and oil cooled for extended life. The Eaton Procision includes features such as Eaton Dynamic Shifting, which allows the transmission to automatically switch between economy and performance shift schedules based on mass, grade and driver demand. Available torque, engine acceleration and grade drive dynamically modified base shift results. Economy and performance shift tables can be adjusted to tune an overall calibration to meet any customer's specific needs. Eaton Procision transmissions utilize a new synthetic transmission fluid that provides component protection while reducing maintenance costs, as part of 150,000 mile or 4-year lube and filter change intervals. The internal sump filter and electrical system do not require maintenance. Procision gives drivers more control in all situations and best-in-class low speed maneuverability thanks to features such as Hill Helper, Creep Mode and Tap Down Shifting. "Customers told us that they wanted features that made their trucks easier to drive," said Jeff Carpenter, Eaton Medium-Duty Procision engineering manager. "So, we engineered a host of features that instill confidence and maximize efficiency for operators with routes on hilly, difficult terrain, or those who navigate tight turns and traffic as part of an urban route." Eaton is a recognized leader in commercial vehicle transmissions. To prove the reliability of Procision, over 100 truck years of testing in a variety of geographies, vocations and duty cycles were performed. This confidence is expressed by a 3-year/unlimited mile warranty which covers the complete system—including the dual-clutch module—in commercial vehicle applications, and a 5-year/unlimited mile warranty in school bus applications.
-
Powered by a 563 horsepower (571 PS) 15.93-liter Mercedes-Benz OM502LA V-8, the 6x6 Buffalo offers unlimited off-road capability. PDF - http://www.rosenbauer.com/fileadmin/sharepoint/products/specialvehicles/INTERN%20Interschutz%202015/Datenblatter%20Sonderfahrzeuge_von%20DRoi_per%20Stick%20am%2020150527/12_BUFFALO%20extreme_GTLF%2033000_en.pdf
-
Transport Engineer / July 27, 2015 Flour miller and supplier Whitworth Bros has taken delivery of two Mercedes-Benz Actros and has already ordered two more for delivery later this year, thanks to fleet-topping fuel returns from its first Actros delivered in October last year. Supplied by dealer Intercounty Truck & Van, the Wellingborough-based operator's latest additions are 2545 models with StreamSpace cabs and 450bhp straight-six engines, driving through Mercedes PowerShift 3 automated transmissions. The vehicles are making nationwide bulk deliveries of bagged, palletised flour on curtainside trailers. The two Actros scheduled for delivery later this year will be 2445 StreamSpace variants. They will deliver flour in tipping powder tank trailers, so will have small-wheeled mid-lift axles which, as well as saving weight, will free up extra space on the chassis to accommodate Gardner Denver blowing equipment. Whitworth has 70 trucks, most of which are tractors, and its first Mercedes vehicle – an Axor tractor – was in service until 2013. Regional distribution manager Colin Spurrier says it was "the most reliable vehicle on the fleet". Last year's Actros, too, performed well on fuel, he adds: "At around 9 mpg, the fuel returns are as good as, if not better, than anything else on the fleet." Whitworth latest trucks are the subject of CharterWay contract hire agreements from Mercedes-Benz Financial Services, with inspections and servicing undertaken by the dealer. "All of our trucks are contract-hired because as well as offering the predictable costs that allow us to budget with confidence, this acquisition method means we get new vehicles every five years," adds Spurrier. .
-
Transport Engineer / July 28, 2015 Aberdeen-based haulier Dyce Carriers has extended its 68-strong fleet with two 44-tonne Renault Range T460 6x2 mid-lift tractors, the first Renault vehicles to join the operator’s heavy goods fleet. Supplied by dealer Alex Aiken and Son, the tractors are on a two-year contract hire through BRS, which includes tyres and road tax. The tractors are pulling oil and gas trailers to the operator's depot in Cowdenbeath. The haulier's owner Jason Moir says fuel efficiency was a major factor in his decision and the trucks are already living up to the promise. "Fuel economy is always a key factor for Dyce Carriers and we knew that the new Range T had been specifically designed to deliver fuel savings. It's early days, but initial figures are very promising," he says. The trucks have also been supplied with Renault's Fuel Eco package, which includes the Optifleet telematics system. In keeping with Dyce's policy to name its trucks, the Range Ts are called 'Blackwatch', after the Royal Highland regiment, and 'Slains Castle' after the Aberdeenshire location said to have inspired Bram Stoker's Dracula. .
BigMackTrucks.com
BigMackTrucks.com is a support forum for antique, classic and modern Mack Trucks! The forum is owned and maintained by Watt's Truck Center, Inc. an independent, full service Mack dealer. The forums are not affiliated with Mack Trucks, Inc.
Our Vendors and Advertisers
Thank you for your support!