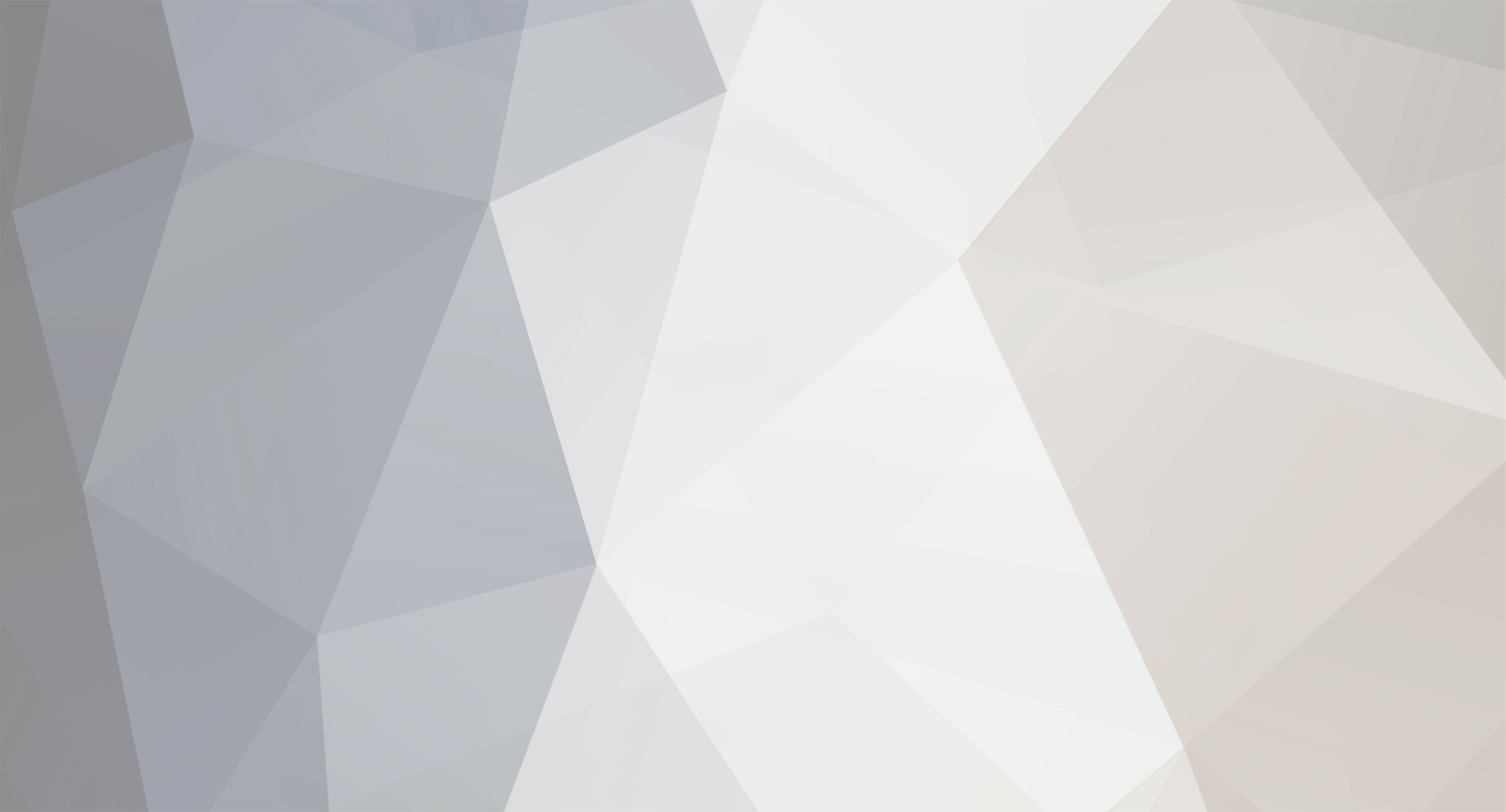
kscarbel2
Moderator-
Posts
18,767 -
Joined
-
Days Won
114
Content Type
Profiles
Forums
Gallery
Events
Blogs
BMT Wiki
Collections
Store
Everything posted by kscarbel2
-
But this is about far more that tariffs. That they are targeting countries that place VAT on U.S. goods is huge.
-
Prime Minister Narendra Modi of India is in Washington today meeting with President Trump. At a news conference with the President Trump, Modi spoke on illegal immigration saying, “We are of the opinion that anybody who enters another country illegally, they have absolutely no right to be in that country.”
-
President Trump is taking on one of the world's best known scams.......The EU's "value added tax" which makes US goods absurdly expensive and impossible to sell there. --------------------------------------------------------------------------- President Trump signed an executive order allowing for new worldwide 'reciprocal tariffs' – with plans to target foreign trade practices on a country-by-country basis that will hit within weeks. "TODAY IS THE BIG ONE: RECIPROCAL TARIFFS!!! MAKE AMERICA GREAT AGAIN!!!" The White House described the massive reach of the tariffs, which will extend far beyond the tariffs that other nations impose on the U.S to encompass 'burdensome regulatory requirements', exchange rates that lead to 'undervalued currencies,' and tax structures that may disadvantage the U.S. 'It’s patently obvious on its face that they are cheating us,' said a senior White House official. The 'reciprocal' part of the tariffs taxes imports at the same rate other nations apply to U.S. exports – although the definitions being applied by the White House give Trump plenty of leeway to hike tariffs on a nation if he sees fit. The executive order will take into account a series of 'non-tariff barriers' that hurt the U.S. But the list of factors under consideration provide a sweeping list of reasons to slap on a new tariff. They include tariffs, 'unfair, discrimination or extraterritorial taxes' including a Value Added Tax, used in Europe, China and elsewhere. Trump says he won't tolerate the European Union's VAT, which he called 'brutal.' Also considered are 'subsidies and burdensome regulatory requirements,' exchange rates which 'deviate from market value' such as 'undervalued currencies' as well as 'any other practice that [U.S. Trade Representatives] determines is an unfair limitation.' 'What we're hoping to do is have this discussion with the nations of the world about how imbalanced the trade environment is because of the existing structures. So the President is more than happy to lower tariffs if countries want to lower tariffs. But let's also recognize that tariffs, higher tariffs, are not the biggest part of the problem in many, if not most, cases,' said the White House official. .
-
USAID funded COVID gain-of-function research in Wuhan. If the Democrats had any integrity at all, we wouldn't hear a peep out of them right now. .
-
More USAID taxpayer dollar expenditure revelations. $3.3 million for being LGBTQ in the Caribbean. $37.6 million for sex workers and their clients, and transgender individuals, in South Africa .
-
https://www.yahoo.com/news/us-aircraft-carrier-collides-merchant-170845799.html
-
The Senate has confirmed Robert F. Kennedy Jr. as Health and Human Services (HHS) secretary. The vote was 52 to 48. Senator Mitch McConnell was the only Republican to vote against Kennedy's nomination.
-
"The Democrats are watching with terror as all the different sources of government money that has propped them up for the last 60 or 70 years, all of it is now being challenged by President Trump and Elon Musk. This cuts to the very base of their coalition. If they can't bribe people, act corruptly and take care of their friends, their entire coalition is going to collapse." Always a pleasure to listen to Newt Gingrich .
-
President Trump has instructed Elon Musk to recover millions the federal government paid Thomson Reuters over the course of four years for a mysterious 'social engineering defense' program. The contract was discovered by Musk's Department of Government Efficiency (DOGE) and reveals that the Department of Defense awarded Thomas Reuters Special Services (TRSS) a $9.15 million contract. The contract began in September 2018, unknown to President Trump, and concluded in November 2022. The contract was filed under the Pentagon's 'Professional, Scientific, and Technical Services' and 'Research and Development' programs. Allegedly, the Defense Advanced Research Projects Agency (DARPA) says the contract to Thomas Reuters Special Services was for cyber defense. Thomson Reuters is the company under which Thomas Reuters Special Services falls. But it is also the parent corporation for the news agency Reuters. "Looks like Radical Left Reuters was paid $9,000,000 by the Department of Defense to study 'large scale social deception.' GIVE BACK THE MONEY, NOW!" President Trump More concerning to DOGE than just the price and its connection to the Reuters news agency was the description of reasoning for the awarded contract. On the government website that tracks and publishes contracts [official contracts], the $9 million contract for Thomas Reuters Special Services is listed on the purchase order as being for 'Active Social Engineering Defense (ASED) Large Scale Social Deception (LSD).' "Reuters was paid millions of dollars by the US government for 'large scale social deception.' That is literally what it says on the purchase order! They're a total scam. Just wow." Elon Musk ASED aims to develop defenses against internet attacks such as phishing, in order to gain access to systems or information. The goal of the ASED programs is to enhance U.S. cybersecurity by creating systems that detect, analyze and mitigate the threats that exploit human psychology. Thomas Reuters Special Services was selected for the 2018 contract due to the company's expertise in risk management and fraud detections. A note on the contract award states that some funding provided in 2020 and beyond were related to COVID-19 and included Disaster Emergency Fund Codes (DEFC) 'N,' which means that money was distributed in an emergency capacity.
-
I strongly suspect McConnell and his wife Elaine Chao have dirty hands.
-
The discovery of a satellite communication module, sensors and other tech from at least five American firms underlines the failure of [Biden administration] U.S. efforts to restrict exports of technology that could have military uses to main adversary China as well as to countries such as Russia and Iran. It also raises questions over the role of private companies that sell their equipment globally in keeping control over the ultimate users of dual-use technology that can have defense applications as well as civilian uses. A Chinese patent reviewed by Newsweek describes a communications system for exactly such a balloon as the one that crossed America, based on using a satellite transceiver from a U.S. company that the balloon’s controllers in China would use to communicate with it and that would send data back, and that is easily available online. https://www.breitbart.com/pre-viral/2025/02/12/chinese-spy-balloon-featured-tech-from-american-companies/ https://www.breitbart.com/politics/2023/12/24/report-biden-administration-officials-tried-hide-chinese-spy-balloon-incident/
-
President Trump’s EPA head, Lee Zeldin, will try to recover the $20 billion in taxpayer funds lost by the Biden administration to climate projects. On Wednesday, he accused Biden of “throwing gold bars of the Titanic” in relation to the money lost on climate projects that he said was a “rush job with reduced oversight.” “The days of irresponsibly shoveling boatloads of cash to far-left activist groups in the name of environmental justice and climate equity are over. The American public deserves a more transparent and accountable government than what transpired these past four years.” “The financial agent agreement with the bank needs to be instantly terminated, and the bank must immediately return all of the gold bars that the Biden administration tossed off the Titanic.” Zeldin says the EPA will also terminate its contract with Citi bank which oversees the Greenhouse Gas Reduction Fund, a program that emerged from Biden’s 2022 climate policy. The fund seeks to leverage public and private dollars to invest in clean-energy technologies such as solar panels, heat pumps and more. Citi had an agreement with the Biden administration to oversee the release of $20 billion under the program to nonprofit groups and states. A Project Veritas video from December featured an EPA official saying that the Biden administration was “trying to get the money out as fast as possible before they come in and stop it all.” .
-
Allegedly, FEMA has clawed back over $80 million from New York City, money earmarked for illegal alien hotels. A federal judge said he wouldn’t stop FEMA from reclaiming the funds. Gone is a $59 million grant that the administration challenged earlier in the week and another award for $21.5 million, City Comptroller Brad Lander said. The money was discovered missing overnight. Lander was unaware that the federal government had access to the city's bank account. Mayor Eric Adams, a Democrat just let off the hook by President Trump, says city officials have contacted the White House about getting back the money. Good luck with that.
-
“A lot of attention has been on [the dismantling of] USAID for example. There's like the National Endowment for Democracy. But I’m like, Okay, well, how much democracy have they achieved lately? [On another note] President Trump is less interested in interfering with the affairs of other countries. There are times the United States has been kind of pushy in international affairs, which may resonate with some members of the audience. Basically, America should mind its own business, rather than push for regime change all over the place." Elon Musk
-
“I’d like the Department of Education to be closed immediately. Look, the Department of Education is a big con job. We’re ranked — so they ranked the top forty countries in the world. We’re ranked number 40th, but we’re ranked number one in one department, costs per pupil. So, we spend more per pupil than any other country in the world, but we’re ranked number 40. We’ve been between 38 and 40, the last time I looked it was 38 and then I looked two days ago … it came out at number 40. Norway, Denmark, Sweden, I hate to say it — China, as big as it is, it’s ranked in the top five. That’s a primary competitor. We’re ranked number 40 — so, if we’re ranked number 40, that means something’s really wrong, right? The United States government should send education back down to states. I say send it back to Iowa, to Idaho, to Colorado. We probably have 35, maybe 37 states that will do as well as Denmark, Norway, Finland, Sweden. They’ll be just as good. I want to let the states run schools. I believe strongly in school choice, but in addition, I want the states to run schools." President Trump
-
A federal judge on Wednesday lifted the temporary freeze on President Trump's 'buyout' offer to federal workers. Massachusetts District Judge George O’Toole ruled the unions lack standing to challenge the directive and are not directly impacted by it.
-
The Democrats, intelligent people, couldn’t possibly actually believe a word of what they’re saying. They’re paid to promote someone’s agenda. Remember all the BLM protesters that abruptly came from nowhere, and just as quickly disappeared. They were transported in and paid. Who was behind that “show”?
-
Boy, I’ve never seen a US government like this in my lifetime. https://www.dailymail.co.uk/news/article-14391325/pam-bondi-justice-department-lawsuit-new-york.html They even forced Disney to u-turn and abandon DEI. https://www.dailymail.co.uk/news/article-14390865/disney-banishes-dei-dramatic-u-turn.html
-
Cummins introduces "B6.7 Octane" Gasoline Engines
kscarbel2 replied to kscarbel2's topic in Trucking News
GAC https://en.wikipedia.org/wiki/GAC_Group
BigMackTrucks.com
BigMackTrucks.com is a support forum for antique, classic and modern Mack Trucks! The forum is owned and maintained by Watt's Truck Center, Inc. an independent, full service Mack dealer. The forums are not affiliated with Mack Trucks, Inc.
Our Vendors and Advertisers
Thank you for your support!