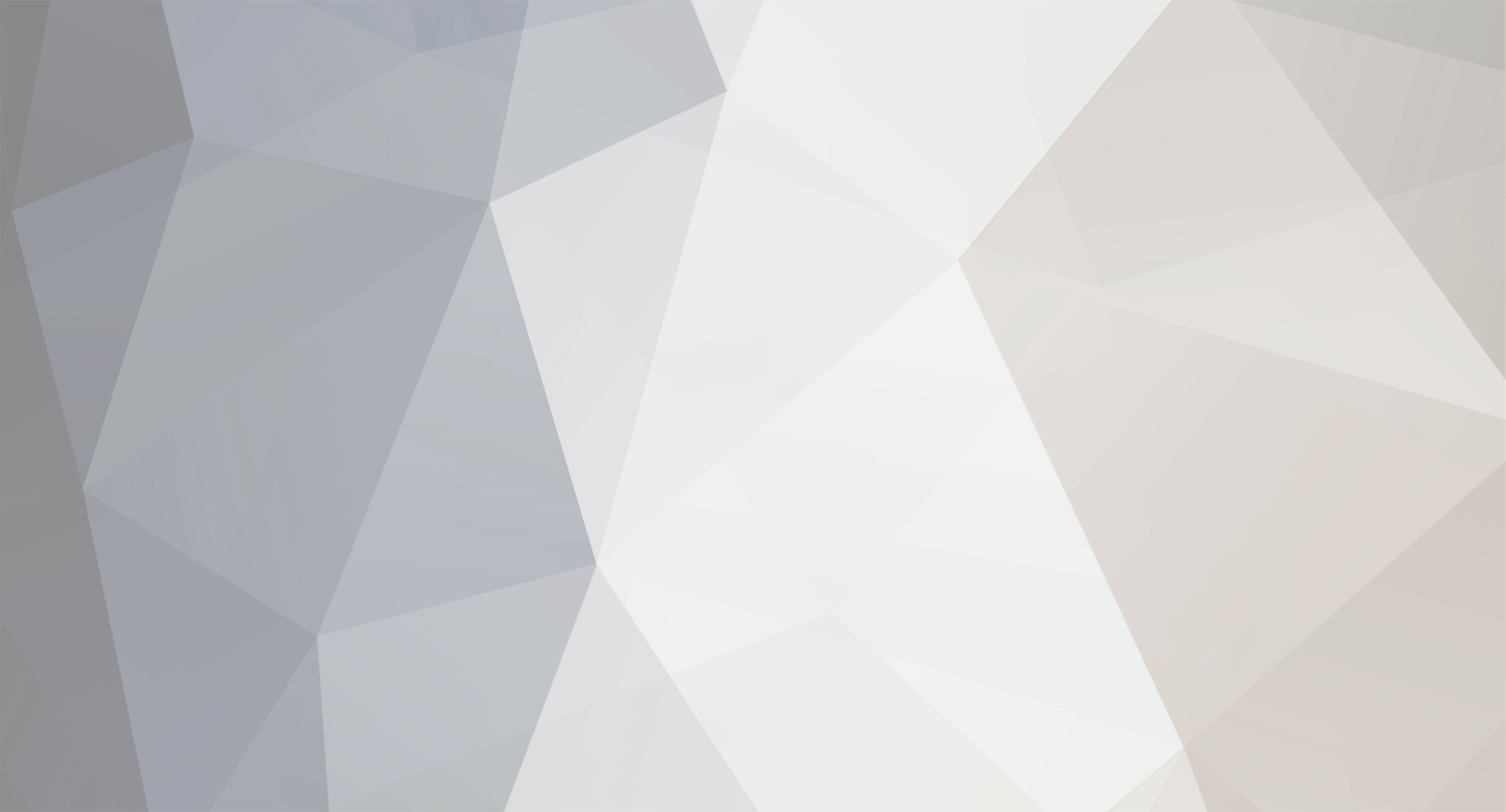
kscarbel2
Moderator-
Posts
18,776 -
Joined
-
Days Won
114
Content Type
Profiles
Forums
Gallery
Events
Blogs
BMT Wiki
Collections
Store
Everything posted by kscarbel2
-
Freightliner Trucks Press Release / May 23, 2019 . . . . . . .
-
Cummins X12 Engine Now Available for Freightliner 114SD
kscarbel2 replied to kscarbel2's topic in Trucking News
. . . . . -
. . . .
-
Autocar Trucks Press Release / April 25, 2019 This Autocar truck was THE garbage-collecting machine in the 1980s. You could see it for years, roaming the streets of Manhattan, packing and hauling that big city trash. There’s nothing out there today as good as this brute. Yet. Time to get back to work. .
-
Paul, Chamberlain appears to have been ahead of its time. Australian engineering impresses! https://www.youtube.com/watch?v=6w-ZnkeXI7c
-
The Ford Taurus Still Exists in China—and It Looks Good Joe Capparella, Car & Driver / May 22, 2019 Facelifted for 2020, the Taurus sold elsewhere makes us imagine an alternate universe where Ford's car lineup continues to thrive. Although the Ford Taurus sedan ended production for the U.S. market earlier this year, Ford continues to sell a newer version of the Taurus in China. The China-market Taurus, which looks a lot better than the outgoing U.S.-market Taurus, is getting some updates including a new top-of-the-line Vignale trim. Unfortunately we won't be getting anything like this Taurus in America, since Ford has dropped all of its passenger-car nameplates except the Mustang. Imagine an alternate universe where Ford's car lineup continues to thrive. Perhaps we in the United States would get a version of this attractive Taurus sedan, which is sold in China by the Blue Oval. Updated with fresh styling and a new luxurious Vignale trim, the China-market Taurus makes the outgoing U.S. version of the car—which ended production earlier this year—look outdated and downmarket. We first saw this new Taurus in 2015, back when we still thought it had a chance of coming to the States. Instead, Ford prolonged the sixth-generation car's life through the 2019 model year and then gave it an unceremonious sendoff, quietly ending production in March 2019. The Chinese version of the car, shown here, is essentially a longer-wheelbase version of the Fusion. It comes with a choice of three engines, including a turbocharged 1.5-liter four-cylinder, a turbocharged 2.0-liter four, and a twin-turbocharged 2.7-liter V-6. While we certainly won't see the Taurus nameplate affixed to this sedan in U.S. dealerships at any point, the nameplate might not be dead for good on our shores. Ford has said that it may apply well-established car nameplates to new crossover or SUV models in the future. For example, rumors have circulated about a Ford Fusion reincarnated as a lifted all-wheel-drive wagon to compete with the Subaru Outback. Might we see a revived Ford Taurus X crossover in the U.S. market in the near future? Only time will tell. .
-
Scania Group Press Release / May 20, 2019 Congratulations to the Scania V8, for 50 years of emotion meets logic. Here are some of the milestones and people that made the engine a true legend – the undisputed King of the Road. If there is one person to thank for the development of the engine that became one of Scania’s biggest successes, it would probably be Bengt Gadefelt. Often called “the father of the Scania V8”, the legendary Head of Design of Scania diesel engines from the 1960s to the 1980s anticipated the need for truck engines that would meet the growing demand for more power, especially for timber haulage and heavy long haulage. In the early 1960s, Scania’s inline six 8 and 11-litre engines were able to reach 250 hp, an output sufficient for the long haulage of the time. But the engineers at Scania (then called Scania-Vabis) realised that such outputs would not be sufficient in future, and decided to shake up the engines market. Gadefelt, known for his casual walk-and-talk leadership style and for his habit of leaning over the design engineers’ blueprints pointing out insightful details, was given the task of leading the development of a more powerful engine, a decision Scania took in 1962. “We realised that about 350 hp was needed to achieve good ‘driveability’. That meant approximately 100 hp more than our other engines,” said Gadefelt later, as he looked back at the project. The demands for more powerful truck engines conveniently coincided with the trend for more compact, forward-controlled trucks instead of the torpedo-built trucks that dominated post-war heavy transport. But there was a problem: how to fit a bigger, inline eight engine underneath a forward control cab? The concept that Gadefelt and his colleagues came up with involved a powerful yet very compact power unit: a 90-degree V8 featuring a 14.2-litre swept volume engine. This powertrain concept had all the characteristics that Scania’s engineers were looking for: good tractive power at low engine speeds, few gear changes, and sufficient extra power throughout the entire engine speed range. The first model to be fitted with the new engine, the LB140, quickly won acclaim from the transport industry. Customers appreciated the engine’s appearance, with its V-shaped valve covers on individual cylinder heads, and were delighted with the high 350 hp output combined with a torque curve that encouraged the use of low engine speeds. And of course, there was the distinctive sound – the rumble that would become one of the V8’s most appreciated characteristics. “Scania created a very robust engine that could last very long, even for demanding tasks,” says Ulf Wallin, a former Assistant Chief Engineer at Scania, now Performance Object Leader. “With the V8, we managed to present an engine that, due to its high output and its ability to be driven at low revs, had great fuel economy. And in contrast to other high-output inline engines, the V8 had modest wear and tear on axles, gearboxes and other components in the powertrain.” Scania manufactured more than 170,000 14-litre V8-engines in total, making it by far the best-selling engine in the high-output segment. So far, so good? Not quite. The future of the V8 engine was threatened during the late 1980s, as Scania was working on one of its largest cab redesigns to date, which would become the 4-series that was launched in 1995. Suddenly, with all the challenges of fitting a V8 engine block into the design, it was no longer an obvious choice. Scania’s engineers were split into two camps. Some favoured the idea of an inline six 11 and 14-litre ‘combi engine’ that would take full advantage of the company’s modular system. But the others emphasised the V8’s importance to the Scania brand. As one Chief Engineer put it: “Our V8 also contributes to the sales of our other products.” Luckily, the latter opinion won out. Some years later, Scania had reached another technical cross-roads: how would they fit in the new injection technology that was required for the engine to comply with the new Euro 3 emissions legislation? To solve the challenge, Scania’s engineers started the development of a completely new engine set-up: a V8 with a narrower, 72-degree angle. Around 12 prototypes were built, of which a couple still exist in less-visited corners of Scania’s R&D department. But it was at this point that a certain senior engineer stepped in: Bengt Gadefelt. “He warned that the 72-degree engine would have a very complex layout, especially the crankshaft. Finally, with another injection solution chosen, we chose to develop a totally new 90-degree 16-litre engine instead,” recalls Håkan Fransson, a retired former Scania Chief Engineer. So, even for a faithful workhorse like Scania’s original 14-litre V8, the last lap was approaching. Emissions legislation and environmental requirements were becoming tighter with the arrival of the Euro 3, 4 and 5 standards, and in the mid 1990s Scania prepared itself for a major technological step: developing an entirely new V8 engine to replace the 14-litre. With the arrival of the new millennium, the original legend was finally replaced by the substantially more powerful 16-litre V8, which had power ratings of 480 and 580 hp at 1,900 r/min and up to 2,700 Nm of torque – more than double the original V8 from 1969. Another major step Scania took with the new engine was modularisation: many components, including the cylinder, were the same as the ones used for the inline engines. The modular concept is of enormous importance for synergies in Scania’s development and production, but also beneficial for customers as it eases up service and spare parts handling. The Project Manager for the new D16 engine platform was Jonas Hofstedt, who today is a Vice-President at Scania R&D. “At a personal level it’s still the highpoint of my 35-year career at Scania,” he says. Hofstedt’s core team was a tight-knit group of just ten people, with the responsibility of integrating all kinds of demands: finding suppliers, setting up a new production line, fitting the new design into the chassis and, last but not least, developing an engine that could match its predecessor’s image of performance and reliability. “I’m very proud of the result,” Hofstedt says today. “Scania’s 16-litre V8 platform became a success that no other competitor came close to. Since the launch, it has a well-earned reputation in the high-output segment and is the foundation on which today’s improved and high-performing engine is built.” After the launch of the 16-litre V8 in 2000, work continued within Scania’s engine development. In 2005, the company launched its broadest range of engines to date, including 500, 560 and 620 hp V8s for Euro 3, Euro 4 and Euro 5 engines with up to 3,000 Nm of torque. Here, the engineers were using technologies to match the environmental requirements in the most efficient manner for all types of transport. With Euro 6 legislation rapidly approaching, Scania had put enormous resources into combining all the new engine technologies the company had developed: exhaust gas recirculation, variable turbo geometry, common-rail high-pressure fuel injection, selective catalytic reduction and particulate filtering. Add to that Scania’s own engine and exhaust management technology, which was now integrated into one system. All of these technologies would later be implemented in the V8. In 2010, all of these features came together as Scania took a major developmental step with the 16-litre engine, increasing the swept volume from 15.6 to 16.4 litre and introducing a new, lighter yet stronger cylinder block in CGI (compacted graphite iron). At the same time, Scania presented the world’s most powerful truck engine to date: a 730 hp V8 with a maximum torque of 3,500 Nm. With the R 730, a new legend was born. In the following years, engine and cab development continued to be intense. By the time Scania introduced its new Streamline trucks in 2013, the company was also presenting its second-generation Euro 6 range, including 520, 580 and 730 hp V8 engines. In line with ever-increasing environmental concerns, Scania also continued to develop engines that could run on a range of renewable fuels. Every V8 truck produced since 2015 can run on biodiesel-HVO, and the company also offers several engine alternatives for biodiesel-FAME. Coinciding with the company’s 125th anniversary in 2016, Scania introduced an entirely new truck range. This biggest-ever product launch in the company’s history was the result of ten years of development and an investment of over SEK 20 billion (EUR 2 billion). The following year, the company presented the all-new V8 engine for the new truck generation, featuring a further reinforced cylinder block to manage even higher pressure in the future. The new V8 built on many of the successful features from earlier generations, but out of approximately 650 components that make up the entire engine, 200 were completely new. The team that developed the new V8 engine focused on four key areas: increasing fuel efficiency by five to eight percent to improve customers’ profitability, improving serviceability to increase the vehicles’ uptime, improving production processes to increase quality, and a contemporary design that could signify a New Generation Scania. But what would Scania’s V8s be without the people that use them, every day, 24/7, under all conditions? The V8 customers have a special position within Scania’s R&D department. Very skilled and loyal, they are of great importance for Scania when it comes to testing new models and new functionality, not only for the V8s but also for development in general. One of the latest field test drivers for Scania is Rickard Sjöstrand, a Swede who between 2016 and 2017 was putting Scania’s new V8 generation to the test, an S 650 6×2 Euro 6. “The engine is really powerful and works well,” he said. “You would think that a bigger engine would consume more fuel, but it actually consumes three litres fewer per 100 kilometres than my previous Scania V8.” Just starting the engine was a pleasure for Sjöstrand: “This new engine rumbles even better.” Björn Westman, a manager with long experience as Head of Engine Development at Scania says that, through the years, the V8 field test customers have been among the best in giving feedback to Scania’s R&D department. “Their invaluable feedback has meant a lot not only for our V8 development, but also as a spin-off for our engine development as a whole,” says Westman. “It meant that we have been able to maintain the focus on the high-output segment and the whole King of the Road concept.” And maintaining the King of the Road concept is something Scania certainly will continue to do, with the V8 as its foundation. The legend – including its distinctive low rumble – will live on, long beyond the first “roaring fifties”, and it will probably be even more powerful than today’s 730 hp. With thanks to Scania engineers, developers, managers and technical writers past and present, such as Ulf Wallin, Håkan Fransson, Peter Wansölin, Anders Lundström, Jonas Hofstedt, Per-Erik Nordström and Anders Nordner for their insights and facts. .
-
Volvo Trucks Press Release / May 22, 2019 Brazilian truck driver Aldinan Cézar Rodrigues explains why he loves his job and why he thinks truck drivers deserve greater recognition. . .
-
Renault Trucks Press Release / May 21, 2019 . . .
-
Daimler Press Release / May 23, 2019 Logistics provider Dachser to operate the fully-electric, heavy-duty eActros in and around Stuttgart The 18-tonne truck makes deliveries to customers into the city center of Stuttgart and supplies Dachser's microhub in the city's Heslach district Daily distance of around 80 kilometres eActros is part of the Mercedes-Benz Trucks "innovation fleet" for testing the electric truck in practical operations Stuttgart / Kornwestheim – Mercedes-Benz Trucks has delivered another locally emission-free and quiet eActros to a customer. International logistics provider Dachser integrates the fully-electric 18-tonne truck into its fleet, where the truck will be tested in regular operations in and around Stuttgart. The official handover of the vehicle took place at the Dachser logistics centre in Kornwestheim near Stuttgart. The eActros is part of the so-called "innovation fleet" from Mercedes-Benz Trucks for practical testing of the heavy-duty electric truck. Martin Kehnen, Head of CharterWay Rental & Key Account Management for Germany at Mercedes-Benz Trucks explains: "The eActros has already proven itself in numerous practical operations as a clean and quiet alternative for urban distribution tasks. We are pleased to have teamed up with Dachser for practical testing of the eActros in yet another field of operations. With this, we want to gather valuable insights to help us further develop the vehicle towards series production." Clean general cargo transport for the Stuttgart area Dachser will use the eActros to deliver general cargo -- meaning palletized shipments above 32 kg, which are too large and heavy for regular parcel shipping -- to its customers in Stuttgart's city centre. Additionally, the eActros will also supply the Dachser microhub in Stuttgart's Heslach district with items for last-mile delivery. The loading area of the eActros offers space for 18 pallets. eActros as a building block for city logistics concept: DACHSER Emission-Free Delivery "The Mercedes-Benz eActros is an integral component of our city logistics concept ‘DACHSER Emission-Free Delivery’, as part of which we will deliver general cargo locally emission-free, initially within Stuttgart but later also in other inner cities. With this concept, we have won the ‘National Sustainable Urban Logistics Competition’. With a range of up to 200 km, the eActros comfortably covers the required daily distance of around 80 kilometres between our Dachser branch in Kornwestheim and the delivery area in Stuttgart. The batteries will then be charged over night at our depot," explains Stefan Hohm, Corporate Director Corporate Solutions, Research & Development at Dachser. Since March 2018 two light-duty FUSO eCanter from Daimler Trucks have been in operation with Dachser in Stuttgart and Berlin. The battery-electric 7.5-tonne truck is also a key player in the emission-free vehicle mix at Dachser. The eActros: sustainable solution for short-radius urban distribution The eActros is based on the frame of the Mercedes-Benz Actros. Beyond that, the vehicle's architecture has been entirely designed around the electric drive and thus features a high percentage of vehicle-specific components. Two electric motors near the wheel hubs of the rear axle provide for the vehicle's drive power with a respective output of 126 kW and maximum torque of 485 Nm each. Furthermore, the transmission ratio used sees this brought up to 11,000 Nm on each wheel. Performance is thus on par with a conventional truck. Lithium-ion batteries with 240 kWh capacity provide the eActros with the required energy. Depending on the available charging output, the batteries can be charged completely within as little as two hours (at 150 kW). About the eActros "innovation fleet" As part of practical testing of the eActros "innovation fleet", the 18 or 25-tonne vehicles are put through their paces by 20 customers from various sectors as part of their regular daily operations. These customers also include global logistics providers such as Dachser, who will be testing the eActros for its suitability for daily operations in Stuttgart over the course of around a year. The tests of this "innovation fleet" consist of two phases, each with ten customers. Insights from these practical tests flow directly into further development of the eActros for series production. The aim is to make clean and quiet distribution in urban areas possible with heavy-duty trucks from 2021 onward. The first eActros has already been in operation with a customer since September 2018. The development and testing of the heavy-duty electric truck for short-radius distribution operations is sponsored as part of the "Concept ELV²" project to varying degrees by the German Federal Ministry for the Environment (BMUB) and the Federal Ministry for Economic Affairs and Energy (BMWi). .
-
Mercedes-Benz Trucks / May 16, 2019 The new Mercedes-Benz Actros (2019) – intelligent driving experience. This heavy-duty vehicle stands for next level trucking. With groundbreaking new features such as Active Drive Assist, MirrorCam and multimedia cockpit, the new Actros is a gamechanger in the fields of safety, semi-automated driving and relaxed driving experience for heavy trucks. .
-
DS production ran from 1983 to 1987, when the last “Driver Cab” fitted Autocar rolled off the line in Ogden, Utah.
-
-
I always liked the lightweight DS-64 with the fiberglass hood (bonnet), predecessor to the ACL-64 and new DC-64R.
-
From what we're told, it's a fact they are doing both.
-
Chevy expands V-8 engine availability on 2020 Silverado Michael Wayland, May 22, 2019 DETROIT — Chevrolet is significantly expanding the availability of its highest-output V-8 engine for the 2020 Silverado. The 6.2-liter gasoline engine — rated at 420 hp and 460 pound-feet of torque — will be optional on five of eight trim levels, up from two high-end 2019 models. The expanded availability will lower the entry-level price of a pickup with the engine from roughly $50,000 to $43,865. Pricing includes $1,595 destination. The V-8 engine, paired with a 10-speed transmission, will be available on the Custom Trail Boss, RST (equipped with four-wheel drive), LT Trail Boss, LTZ and High Country models. It will remain unavailable on Work Truck, Custom and LT trims. The added availability of the V-8 is part of the Silverado’s launch cadence and not a reaction to higher-than-expected market demand, according to a Chevrolet spokesman. The 5.3-liter V-8 engine remains “by far” the most popular engine for the pickup, he said. The lower price threshold for the engine is one of several packaging changes or updates announced Wednesday by Chevrolet for the 2020 Silverado. Other powertrain changes include expanded availability of the 10-speed transmission as well as a 2.7-liter turbo four-cylinder engine and eight-speed automatic transmission being available on Custom models. "In today's truck market, customers continually demand more features, more technology and more capability," said Tim Herrick, executive chief engineer of GM's redesigned full-size trucks, in a statement. "For 2020, we are delivering more in each of these areas." The Silverado, like its GMC Sierra sibling, also will add new trailering technology and adaptive cruise control for the 2020 model year. The trailering includes the addition of a camera system with 15 viewpoints that enables a "transparent trailer" view that was announced for the heavy-duty models of the pickups for the 2020 model year. The camera-based adaptive cruise control will be available on Silverado LT, LTZ and High Country. The 2020 model year also will be the first to offer a new 3.0-liter inline-six turbodiesel Duramax engine. The engine was expected to be available late in the 2019 model year, but GM on Tuesday said the EPA's emissions certification process is taking longer than anticipated, causing a "slight delay" in its availability.
-
Great way to create jobs and support the human race (sarcasm on my part).
-
Ford tests package-carrying robots for driverless delivery Bloomberg / May 21, 2019 It’s a headless robot in a driverless car. Ford Motor Co. is working on a way to resolve what self-driving researchers refer to as “the last 50-foot problem.” If an autonomous delivery vehicle arrives at your house, without any humans aboard, who’s going to carry the package, grocery bags or piping-hot pizza to your doorstep? A robot, of course, could be up to the task — with no tipping necessary. In Ford’s case, the solution is Digit, an android with two stork-like legs, arms capable of carrying a 40-pound load and a camera-encrusted torso topped by a puck-shaped laser-radar sensor. It could be the headless cousin of a battle droid from the much maligned Star Wars prequels. The business case for driverless delivery is even more compelling than robotaxis — and potentially easier to execute. For one thing, there’s no need to worry about the safety of human passengers. And the rise of online shopping has turned package delivery into a huge growth area. Just ask Amazon, which spent $27 billion on delivery costs last year. Remove the human driver from the equation, and delivery costs could plunge by 60 percent or more. The benefits could be in the billions. Ford would like to deploy Digit delivery robots as early as 2021, alongside the planned introduction of its autonomous vehicle fleets to ferry people and packages around the clock. “We’re going to have an AV fleet out there, and my goal is to get robots to be able to be there and ready at the same time,” said Craig Stephens, director of controls and automation in Ford's research and advanced engineering. How real humans will react to this delivery android is a key part of Ford’s research, which is just getting underway and will include real-world tests inside Ford factories, and on the sidewalks near its headquarters in Dearborn, Mich., and in Pittsburgh. “Digit looks actually pretty friendly to me,” Stephens said. The “inoffensive” appearance is “going to be a key thing for people to be able to trust a robot.” Startup robot firm Digit was created by Agility Robotics, a startup with fewer than 30 people based in Albany, Ore. Chief Technology Office Jonathan Hurst said he hasn't seen anyone react negatively when meeting Digit or a forbearer that lacked a torso and was simply a pair of piston-like legs attached to a motorized midsection. The robots have been allowed out on the town. “I have a lot of people ask us, ‘Could this be perceived as creepy?’” Hurst said. “There is a small subset of people who stay far back,” he said, “and whip out their smartphone and starting taking video.” While the design is likely to evolve, Hurst doesn't see a need to give Ford’s delivery robot a head. In fact, he wonders if that might freak people out more. “If it looks very close to an animal or a human but is not quite there, then immediately people are revolted by it,” Hurst said. “And we didn't physically need a head up there for our current perception needs.” Other robot tests Others are tinkering with delivery robots, not all of which are humanoid. Anybotics and German auto-parts giant Continental demonstrated a robotic delivery dog concept at the Consumer Electronics Show this year. Segway has shown a rolling delivery device that looks like a mobile office copier, and FedEx is testing a boxy rolling bot that can climb stairs and carry up to 100 pounds. Starship Robots, which look like squat storm troopers with six wheels, are deployed in several cities around the world, according to the startup based in San Francisco and Estonia. And Postmates, which is researching autonomous grocery-getting with Ford, has a cute delivery robot known as Serve with googly eyes like Pixar's Wall-E, along with four oversize wheels. Ford is worried that wheeled robot couriers would be blocked by front-porch steps found outside most homes in America. Digit, by comparison, can climb steps and raise its arms to catch itself in a fall. Its tiny feet, soled in corrugated rubber, can traverse concrete, grass, wood, and gravel. Ford’s decision to go with two legs, instead of wheels, came with help from researchers at the University of Michigan. “Our world is designed for bipedals — us,” Stephens said. “So there's an inherent attractiveness to a bipedal robot.” Another advantage is Digit’s lightweight design. Rather than outfit it with a full array of sensors and processors, which would push its bulk past 100 pounds, Digit gets most of its computing power from Ford’s self-driving vehicle. The same sensors that allow an autonomous car to navigate will be used to scan the path to the door and beam the route to the robot. Transformers comparison Once Digit has left the package on the porch or handed it to the recipient, it walks back to the delivery van, folds itself into a compact square, and slides into a drawer that serves as a docking station. The process looks like something out of a Transformers movie. The suburban-porch scenario — “up the garden path to the front door,” as Stephens puts it — won’t be the only use case. Ford and Agility plan to test urban scenarios that involve gaining access to apartment buildings without help of a doorman. At first, however, there will be a role for human helpers. “We're not going to be deploying them by the thousands and replacing all people who do the job right away,” Hurst said. For Ford, which specializes in commercial vehicles, driverless delivery has huge potential. The automaker has pegged the potential value of the market for robot ride-hailing and driverless delivery at $332 billion. “The business opportunity is large,” Stephens said. “Robots are going to be necessary.” .
-
Scania to invest $344 million in Brazil after Ford exit
kscarbel2 replied to kscarbel2's topic in Trucking News
I think Ford made a huge mistake.....their decision is a huge loss of face in South America's key market of Brazil. Yes, Brazil's economy has been skidding bottom with no end in sight. As a result, all the truckmakers are hurting. Even the Chinese truckmakers largely canceled their big plans to build there. Ford's office furniture guru Hackett decided to ax commercial truck production in Brazil to cut cost (while the global truck unit Ford International is taking off nicely). https://www.bigmacktrucks.com/topic/47464-ford-market-news/?page=24&tab=comments#comment-416185 This isn't the first time Brazil's economy hit bottom and caused pain for the truckmakers. Back in the 1990s, things were so bad that Ford and Volkswagen formed a joint venture, Autolatina*, so as to consolidate production and reduce costs.....and ensure their survival. * From 1990 to 1995, Volkswagen trucks and buses were built at the Volkswagen-Ford AutoLatina* joint venture utilizing Ford truck components. Challenging economic conditions during the 1980s forced Volkswagen and Ford’s business units in both Brazil and Argentina to join forces and form a money-saving joint venture called AutoLatina in 1987 which lasted to 1995. VW and Ford trucks were produced together in Ford’s Ipiranga truck plant from 1990 to 1995. -
So maybe more appropriate people in U.S. history like Thomas Jefferson, Franklin Delano Roosevelt and Dwight Eisenhower still have a chance.
BigMackTrucks.com
BigMackTrucks.com is a support forum for antique, classic and modern Mack Trucks! The forum is owned and maintained by Watt's Truck Center, Inc. an independent, full service Mack dealer. The forums are not affiliated with Mack Trucks, Inc.
Our Vendors and Advertisers
Thank you for your support!