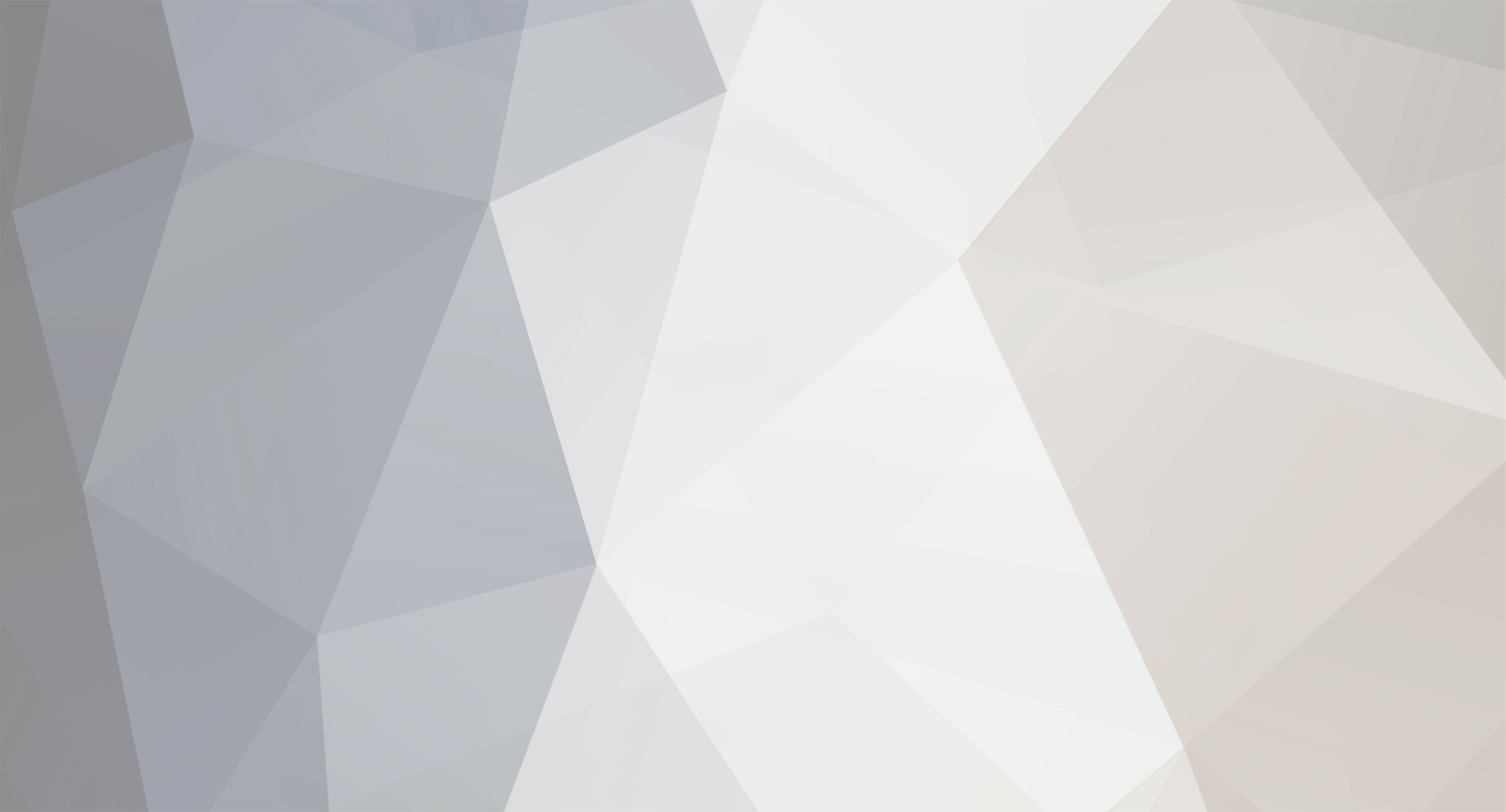
kscarbel2
Moderator-
Posts
18,780 -
Joined
-
Days Won
114
Content Type
Profiles
Forums
Gallery
Events
Blogs
BMT Wiki
Collections
Store
Everything posted by kscarbel2
-
Fleet Owner / February 17, 2016 Driver turnover and retention continue to be the top challenges for fleets across the country. Within private fleets, however, the problem doesn’t seem as bleak. Tom Moore, senior vice president of the National Private Truck Council (NPTC), told attendees at last week’s Fleet Advantage Changes in Attitudes Fleet Safety and Technology Conference that private fleets have only a 14% driver turnover rate. Compare that to the 100% annualized turnover rate at large truckload carriers – according to 2015 third quarter data from ATA. Industry-wide, not only are fleets dealing with an aging driver workforce – potentially leading to more workers’ compensation issues – Moore explained, but 70% of drivers are leaving due to disciplinary problems. “To me, that number shouldn’t even be on the table,” he said. “We’re hiring our own problem.” One of the biggest mistakes fleets make happen during the initial hiring process. According to Moore, the typical driver should be treated as a representative of the company, considering drivers see and interact with customers most frequently. During hiring, Moore suggests thoroughly analyzing how the driver looks, acts and will work with people out in the real world. Private fleets seem to be gaining ground and becoming more progressive, which could help with driver retention. According to Moore, 95% of NPTC’s members are using some sort of onboarding technology to breakdown and decipher data, and more are starting to spec safety technology to help enhance efficiency and productivity. Private fleets are also becoming more specialized in the equipment they’re using, plus they’re getting better at selling their services, he added. “If it’s not safe, it’s not going to be efficient,” Moore explained. “You’ve got to be safe. Most private fleets operate with the mentality that you’re one accident away from going out of business.” Because of that, he noted, CSA scores are three times better among private fleets. Gary Petty, CEO and president of NPTC, explained that there are 10 million CDL drivers listed in the U.S., but only an estimated 3.4 million are active drivers. Private fleets represent 46% of the trucking industry, and capacity within private fleets is growing 5-10% annually, he added. According to the federal database, there are more than 1.3 million U.S. DOT carriers – 97% of which operate with 20 or fewer trucks. Petty added that the top 10 carriers represent less than 3% of market share. Freight volume has increased for all of the trucking industry and is expected to rise 3.3% in 2015 and 4.3% in 2016, he said. Upcoming government regulations – the ELD mandate, GHG Phase II, CSA scores, and driver management practices –are meant to excise what Petty called “the bottom dwellers” out of the industry. “The trends show good news for private fleets,” Petty said. “Private fleets will continue to attract the best drivers. Professionally trained in-house management teams are essential. Along with their expertise, supplier/vendor partnerships will continue to be the keys to success for private fleets.” Moore agreed, adding that when it comes to the ELD mandate and the driver shortage, the rule will have a net gain for the best drivers and fleet operations. “I think drivers inherently want to please people,” he said. “[The ELD mandate] gives drivers and the dispatch community the intelligence and the ability to say ‘We can’t dispatch that.’ I think a driver wants to operate as legally as possible, and they don’t want people cheating them out of that.”
-
Bridgestone launches new, SmartWay-certified steer tire
kscarbel2 replied to kscarbel2's topic in Trucking News
The Bridgestone R290 remains my favorite on-road steer tire. The combination of R290s on the steer and Goodyear G367s on the drive was hard to beat. -
Transport Topics / February 17, 2016 Bridgestone has introduced a new, SmartWay-certified steer tire for long-haul and regional trucks. The R283A Ecopia model is available in two sizes and will be made available in two more in April. It is compliant with California Air Resources Board low-rolling-resistance standards. Bridgestone engineered the tire “to deliver the best combination of wear performance and fuel savings,” said Matt Loos, director of truck and bus marketing. “Sophisticated fleets today measure tire performance based on the total life cycle. The R283A Ecopia tire is an innovative solution that will help them maximize every mile.” The tire gets 21% longer life and 3% less rolling resistance than the previous model. To achieve that, Bridgestone said it made improvements in sidewall design, tread compounding and the casing. Related reading - https://commercial.bridgestone.com/en-us/truck-and-bus/product/r283a-ecopia
-
GM Powertrain becomes GM Global Propulsion Systems
kscarbel2 replied to kscarbel2's topic in Trucking News
GM renames powertrain unit to emphasize alternative technologies Automotive News / February 17, 2016 GM Powertrain is no more. General Motors said today it has renamed its powertrain unit after 24 years to GM Global Propulsion Systems. GM said the name change more accurately portrays the work the unit does as the company increasingly invests in electric vehicles, fuel cells and other technologies. “Gone are the days when a gasoline engine and a transmission designed independently meet a customer’s expectations,” Dan Nicholson, Global Propulsion Systems vice president, said in a statement. “The diversity of our propulsion systems requires a name that reflects what we are already working on and delivering to our customers.” The automaker said nearly 50 percent of its engineers in the former powertrain unit work on alternative or electrified propulsion systems. The Global Propulsion Systems unit employs about 8,600 people globally, GM said. Last month, GM said it is reorganizing certain vehicle engineering operations to speed efforts to develop autonomous and electrified vehicles. Doug Parks was named vice president for autonomous technology and vehicle execution, reporting to Mark Reuss, head of global product development for GM. The move was effective Feb. 1. . -
Green Car Congress / February 17, 2016 General Motors will rename GM Powertrain to GM Global Propulsion Systems. GM’s Global Propulsion Systems is collectively the group of more than 8,600 people that design, develop and engineer all propulsion related products and controls for GM worldwide. Nearly 50% of the Global Propulsion Systems engineering workforce is involved with alternative or electrified propulsion systems. The new name is another step on our journey to redefine transportation and mobility. Global Propulsion Systems better conveys what we are developing and offering to our customers: an incredibly broad, diverse lineup—ranging from high-tech 3-cylinder gasoline engines to fuel cells, V8 diesel engines to battery electric systems, and 6-, 7-, 8-, 9- and 10-speed to continuously variable transmissions. —Mark Reuss, executive vice president, Global Product Development Gone are the days when a gasoline engine and a transmission designed independently meet a customer’s expectations. Today’s customer is demanding unprecedented technology integration that requires unprecedented engineering and supplier partnerships. The diversity of our propulsion systems requires a name that reflects what we are already working on and delivering to our customers. I believe this will establish an industry trend. —Dan Nicholson, vice president, GM Global Propulsion Systems GM Global Propulsion Systems is responsible for all GM vehicle propulsion systems’ design, development and validation, including engines, transmissions, electrification systems, fuel cell development and all associated control systems. The Pontiac, Mich. Global Propulsion Systems Engineering Center is the flagship of GM’s eight global powertrain engineering centers, which also include Brazil, Germany, Italy, India, China, Korea and Australia, collectively representing $1.5 billion in global investments in recent years, including joint ventures.
-
One of the factors is that the younger generations of people today have never known hardship. Those in their 80s and 90s recall the depression when you were glad to have a potato, and World War 2 which brought rationing, food stamps, scrap metal drives and letters from the War Department notifying next-of-kin. While Korea was somewhat ignored by an America enjoying the roaring 50s, when most homes became equipped with TVs and refrigerators, Vietnam again brought "reality" into the minds of many Americans. But the kids born, shall we say post-1980?, have no clue or interest in how challenging life can be. These individuals, from all income levels, not only take life and our country's good fortune for granted, but many either don't want to work, or expect to start half-way up the ladder. Look at the condition of America today. It leaves me speechless.
-
You are so right about the thin armor. If the German shells didn't go all the way through, they rattled around within the Sherman like marbles in a Maxwell coffee can. It was bad. The best tanks of the war were the T34, Panther and Jagdpanther. As I mentioned before, the Shermans didn't evolve into a formidable weapon until the British modified it. They needed more tanks but recognized the Sherman's deficiencies, having suffered heavy losses with U.S. M3 "Grants" against Rommel's Afrika Korps. The most important British modification was replacement of the short 75mm cannon with a lethal long barreled 17-pounder anti-tank gun that could take on most German armor. It could penetrate more armor than the 88mm in the German Tiger. Mid-way thru the war, U.S. Army Shermans were upgraded with the heavier T23 turret and a 76mm high velocity gun, giving our guys a chance (but still unequal to the British Sherman "Firefly"). With its early weaknesses resolved, the matured M51 Super Sherman was being used successfully against significantly more modern Russian T54 and T55 tanks as late as 1973 by the Israeli Defense Force. The Israeli Super Shermans mounted a deadly French 105mm Modele F1 gun in a much modified turret, with 460 horspower Cummins VT8-460Bi V-8 engines and HVSS suspension.
-
I'd love to see Ben Stein in the White House. At age 71, he's older than I'd prefer, but even one term would be refreshing.
-
Volvo’s UD Truck unit to end production of medium trucks
kscarbel2 replied to kscarbel2's topic in Trucking News
I'm not so sure. Volvo Group has rather serious financial difficulties now, one reason being ousted CEO Olof Persson poor and costly decisions. Even Volvo Construction Equipment is on the board table for sale consideration, because it's faintly profitable. I feel, before Nissan Diesel was sold to Volvo, that Nissan for some time was failing to adequately invest in its commercial truck unit so as to keep it relevant. Did Volvo spend US$1.1 billion just to get UD's new four- and six-cylinder engines? That doesn't add up to me. I believe Volvo bought UD to embed in Asia. The problem is, Volvo doesn't understand Asia for the most part. Look at the failure of the Quester launch. -
Land Line / February 16, 2016 Seven tractor-trailers and one personal vehicle were shot while traveling along U.S. 75 Highway near Tulsa, Oklahoma, on Sunday and Monday. Six of the vehicles were Wal-Mart trucks. Three of the vehicles were shot on Sunday night and three were shot on Monday night or Tuesday morning. Most of the drivers discovered bullet holes after arriving at their destinations. A Swift truck also was hit. The Tulsa County Sheriff’s Office says two 14-year-old boys have been arrested for firing the shots at large trucks traveling on Highway 75. Both teens are facing charges on 9 counts of assault with deadly weapon and 9 counts of mishandling of a firearm. Detectives spoke with a man who said his boys were out hunting both nights. The two boys were questioned and they admitted to leaving the area and shooting at the vehicles on I-75.
-
Transport Engineer / February 16, 2016 Lombard Shipping has replaced its first Actros tractor units, acquired seven years ago, and adding five new examples of the latest Actros to its 40-strong almost entirely Mercedes-Benz truck fleet. The new tractor units are all Actros 2545s, powered by Mercedes 450bhp straight-six engines, driving through Mercedes PowerShift 3 automated transmissions. Lombard managing director Simon Fraser says that fuel efficiency is already impressive at “well over 10 mpg”, which he describes as excellent. “The Actros is a great all-round package. Our drivers like them and they’re reassuringly reliable, with downtime reduced to an absolute minimum,” states Fraser. “This is partly down to the fact that the Actros is a superb piece of engineering, but also because if we do ever have a problem, the team at [dealer] Orwell Truck & Van invariably deal with it quickly and professionally,” he continues. “They understand our business and are always willing to be flexible to help keep our trucks on the road, where they earn their keep,” he adds. For Fraser, the secret to his trucks’ fuel-efficiency is down to a combination of three factors. First, Lombard uses the FleetBoard telematics hardware, fitted as standard, to monitor driving style and highlight incidences of over-revving, harsh braking, etc, that impact fuel consumption. “It’s a highly effective educational tool,” comments Fraser. “By compiling a league table of scores we’ve fostered a real spirit of competition between our drivers, to see who can be the most economical.” Secondly, though, Lombards’ new Actros trucks have also been fitted with Mercedes-Benz PPC (Predictive Powertrain Control) system, which combines cruise control with GPS mapping – enabling the trucks to ‘see’ the road ahead and optimse gear shifts and throttle. Finally, Fraser says Lombard’s drivers took coaching from Orwell Truck & Van’s fuel-saver driver-trainer Lee Betts. Lombard’s new Actros tractors are the subject of Agility funding from Mercedes-Benz Financial Services – offering the benefits of hire purchase with a balloon payment plus additional flexibility at contract end. “The Agility payments are highly competitive and we’re able to put off deciding what to do at the end of the contract until much nearer the time,” confirms Fraser. “Orwell don’t just sit and listen. They come to us with suggestions if they think they can help us to operate more cost-effectively,” he enthuses. “For instance, they recently submitted a proposal to retrofit PPC to several 18-tonne Antos rigids, which we set on the road last year,” he explains. “We’re currently crunching the numbers to calculate what level of saving we could potentially achieve.” Mercedes’ own tests show PPC can deliver savings of 5%, although many UK operators report much higher gains. One of the new Actros is based in Ipswich, and hauls shipping containers from the dockside at Felixstowe to distribution centres in the Midlands. The remaining four work out of Liverpool, undertaking haulage and groupage duties between mainland Britain and Ireland. .
-
Transport Engineer / February 11, 2016 Readymix concrete, cement and aggregates supplier Cemex UK has added 15 new DAF CF 400 FAD 8x4 tippers to its aggregates and coated road-stone operation – six fitted with additional low-height nearside door windows to improve drivers’ visibility of vulnerable road users. The so-called Vision Doors were designed by Cheshire-based Astra Vehicle Technologies, and allow for a retractable main window, allowing drivers direct access to the nearside rear view mirrors. FORS (Fleet Operator Recognition Scheme) Gold accredited Cemex also specified DAF’s ‘Haulage’ chassis for these tippers in order to achieve the dropped cab height – six inches lower than DAF’s off-road ‘Construction’ vehicle – and hence again improved all-round driver visibility. While not mandated by legislation, further active safety features specified include DAFs AEBS (advanced emergency braking system), Lane Departure Warning and Vehicle Stability Control. The new DAF trucks have also been fitted with side under-run bars, near-side caution boards, side scan technology from Brigade Electronics and a six-camera VUE system for all-round monitoring and digital recording of incidents. It also has Continental tyres with the ContiPressureCheck TPMS tyre pressure monitoring sytem). Bodywork for all of the new tipper tucks comprises Weightlifter PPG bodies with Hyva front-end tipping-gear and Dawbarn Hydroclear sheeting systems. The new 8x4s will be joined by 40 CF 460 FTP 6x2 tractor units for the company’s cement fleet, which operatrs out of Rugby and which are now on programmed delivery. “We enjoy an excellent relationship with DAF and its dealer in Leicester, Ford & Slater,” comments Paul Clarke, logistics fleet engineering manager at Cemex. “But that doesn’t mean DAF is an automatic choice when we look at new vehicle acquisitions,” he continues. “For new fleet purchases, we go to the market with a formal tender process after which we scrutinise whole life costs to seven years. “Invariably, DAF Trucks comes up with the goods, and the DAF UK-network provides an excellent fit for our own country-wide locations.” Clarke says Cemex is “passionate” about passive and active safety for its own drivers and for other road-users. “We link-up frequently with the Met Police and the recent Exchanging Places event provides everybody concerned with road safety with an opportunity to engage,” he says. The latest of London’s Metropolitan Police’s ‘Exchanging Places’ events at Canary Wharf (29 January 2016) showcased one of Cemex’s first DAF tipper deliveries, allowing cyclists in London to see first-hand the difficulties commercial vehicle drivers face in an urban environment. These trucks were supplied and will be maintained on a seven-year DAF MultiSupport R&M package, through DAF trucks’ dealership in Leicester, Ford & Slater. .
-
Transport Engineer / February 2, 2016 Recyling and waste management operator Countrystyle has added seven 32-tonne Mercedes-Benz Arocs trucks its fleet, which has almost tripled in size in three years to 150 vehicles. Supplied by dealer Sparshatts of Kent, six of the eight-wheelers are Arocs 3242K trucks with compactor bodies by Inco-Mol, of Chesterfield, while the seventh vehicle is a 3243K mounted with Hyva hook loading equipment. The latest additions join a fleet of 8x4 Arocs refuse vehicles and hook-loaders, as well as tractor units that work with walking floor trailers. Most of the tractor units are 6x2 Actros vehicles, with a couple of double-drive Arocs versions. “Continued business growth means we needed more dustcarts for our trade waste rounds, and another hook-loader able to handle Ro-Ro bins with capacities of up to 40 cubic yards,” states Countrystyle’s commercial director Jamie Houston. “Mercedes-Benz has accounted for approximately 90% of our fleet purchases over the last 18 months, as we’ve sought not only to extend the fleet but also to reduce our carbon footprint by replacing older vehicles,” he continues. “The Arocs and Actros are both high-quality, fit-for-purpose trucks that have proved exceptionally reliable and represent excellent value for money. Our drivers speak very highly of them, too, while we receive a first-class service from Sparshatts.” The new trucks are being inspected and serviced by Sparshatts under CharterWay contract hire agreements from Mercedes-Benz Financial Services. .
-
Commercial Motor TV - sponsored by DAF Trucks / February 12, 2016
-
European Commission / February 16, 2016 The European Commission (EC) has proposed to provide Sweden with almost 1.8 million Euro (US$2 million) from the European Globalisation Adjustment Fund (EGF) to help 500 former workers of Volvo Trucks in Sweden to find new jobs. Sweden applied for support from the EGF following the dismissal of 647 workers from Volvo Trucks EMEA (Europe, Middle East and Africa), and four suppliers directly affected by the dismissals at Volvo Trucks. These job losses were the result of serious disruptions in commercial vehicles' trade in recent years. Marianne Thyssen, EU Commissioner for Employment, Social Affairs, Skills and Labour Mobility, commented: "Redundancies like these are major shocks to regional economies, especially in sparsely populated regions such as Västerbotten. EU solidarity is there to help the dismissed workers upgrade their skills and prepare for new opportunities. It is important for us to support them in this way and to help them find new job opportunities in this area or further afield. This proposal for almost 1.8 million euro from Europe's Globalisation Fund would help ease their transition to new jobs". The measures co-financed by the EGF would help the 500 most disadvantaged workers in their efforts to find jobs by providing them with: * guidance, * training, * job-search support, * advice on entrepreneurship and business creation, * job-search allowances * travel expenses. The total estimated cost of the package is almost €3 million (US$3.3 million), of which the EGF would provide just under 1.8 million euro (60 %). The proposal now goes to the European Parliament and the EU's Council of Ministers for approval. EC Press Release - http://ec.europa.eu/social/main.jsp?langId=en&catId=89&newsId=2459&furtherNews=yes
-
DAF Trucks Press Release / February 5, 2016 DAF Trucks’ market share in the heavy-duty segment (16 tonnes+) of the European truck market increased to 14.6% in 2015. "We have achieved growth in almost all major markets", says Richard Zink, member of the DAF Board of Management and responsible for Marketing & Sales. "We supply the best and most fuel efficient trucks ever, important drivers behind this growth." With a market share of 14.6%, DAF further strengthened its position in the heavy-duty segment of the European truck market in 2015 (2014: 13.8%). DAF saw its market share increase in major truck markets, such as Germany (10.8% market share), Great Britain (23.9%), Spain (11.3%), Poland (18.9%), the Netherlands (29.4%) and the Czech Republic (17.2%). In France and Italy, its market share stabilised at 12.0% and 10.2% respectively. In the heavy-duty segment, DAF is the market leader in the Netherlands, Great Britain, Poland and Hungary. In Belgium and the Czech Republic, DAF is market leader in tractors. In 2015, DAF registered around 39,400 vehicles in the European heavy-duty segment, an increase of 26% compared to the more than 31,200 trucks a year earlier. Total market for heavy-duty commercial vehicles rose by about 19% to more than 269,000 units, compared to just over 226,000 in 2014. For this year, DAF expects the European market for heavy-duty trucks to be between 260,000 and 290,000 vehicles. Light segment In the light segment - in which DAF offers the LF - the European truck market increased by more than 5% in 2015 to 49,000 units (2014: 46,500). DAF saw its market share in this 6 to 16-tonne class increase slightly from 8.9% in 2014 to 9.0% in the past year. An important contribution came from DAF's success in the UK, where it achieved a market share of over 36% in the LF segment. Further growth outside the European Union DAF has also further strengthened its market position outside the European Union. DAF made its entrance into Malaysia and Colombia. In Taiwan, a new assembly plant was opened to double production capacity for the LF, CF and XF models. With a market share of 17.8%, DAF is the largest European truck brand in Taiwan. The DAF factory in Ponta Grossa, Brazil increased production and commenced assembly of the versatile CF series and the PACCAR MX engine. DAF introduced its complete Euro 6 range in Turkey, where the new emission legislation came into effect on 1 January 2016. DAF Transport Efficiency "We are proud to have further reinforced our market position in 2015, both within and outside Europe", says Richard Zink, Director of Marketing & Sales. "Over the past year, DAF has introduced important product innovations that make our popular CF and XF models up to 5% more fuel efficient. In line with our DAF Transport Efficiency philosophy, numerous innovations were also implemented for the LF distribution truck, resulting in an even greater return per kilometre. Along with our extensive package of services and professional dealer organisation, DAF's comprehensive product range forms the basis for continuing growth toward our medium-term objective of 20% market share in Europe." .
-
Mack Trucks Inc., America’s oldest commercial vehicle manufacturer, is also the oldest rail motor car manufacturer in the United States. The company designed and produced rail cars (also referred to as rail buses), self-propelled railway passenger cars and locomotives. Always leading America forward with cutting edge technology, Mack Trucks was a pioneer in the United States of the concept now commonly known as "light rail". Facing a market contraction in 1959, Mack Trucks phased out rolling stock production in 1960. http://www.bigmacktrucks.com/index.php?/topic/33657-mack-rail-the-locomotives/?hl=rolling+stock#entry218645 http://www.bigmacktrucks.com/index.php?/topic/39989-mack-rail-the-rail-cars/?hl=rolling+stock http://www.bigmacktrucks.com/index.php?/topic/33544-mack-rail-global-sales/?hl=rolling+stock http://www.bigmacktrucks.com/index.php?/topic/33763-mack-rail-sperry-rail-service-the-oldest-operator-of-mack-rail-buses/?hl=rolling+stock http://www.bigmacktrucks.com/index.php?/topic/39495-update-sperry-rails-mack-fcd-rail-bus/?hl=rolling+stock Fast forwarding to the present, Navistar has found itself engaged in railcar production. ------------------------------------------------------------------------------------- SEDA Board alters Navistar, FreightCar incentives Times Daily / February 16, 2016 The Shoals Economic Development Authority Board (SEDA) recommended today altering an incentive package with Navistar and FreightCar America (http://www.freightcaramerica.com/) so that it is based on 1,100 workers rather than 1,350. The board also recommended extending the deadline for meeting that employment level to March 2017. The committee appropriates money from the Shoals Economic Development Fund. The fund is collected from a half-cent sales tax that was approved to assist in economic development. SEDA board members praised the companies for their dedication to the area. "I'm very confident with the FreightCar and Navistar commitment," SEDA President Forrest Wright said. "We are fortunate to have them here. It is a massive tax-paying investment with hundreds of people working every day." The initial agreement would have had the company receive $7.66 million for reaching 1,350 employees. Now they would receive $2.271 million for reaching 1,100 workers, Wright said. Navistar officials announced in 2011 it would lease the former National Alabama railcar plant at the Barton Riverfront Industrial Park [to assemble the new-for-2012 Loadstar LCF refuse chassis]. National Alabama had promised to hire at least 1,600 railcar employees, but those plans never came to fruition. In February 2013, Navistar and FreightCar America officials announced FreightCar would lease a portion of the facility. Throughout that time, employment ramped up at the plant, which reached 900 employees in June 2015, when American Intermodal Container Manufacturing Company, LLC (http://aicmusa.com/) announced it had entered into a long-term manufacturing agreement with Navistar to jointly produce high-tensile steel 53-foot domestic shipping containers at the company's Barton Riverfront Industrial Plant in Cherokee, Alabama (http://ih.constantcontact.com/fs041/1101903601555/img/243.jpg?a=1102659829328). That was the initial benchmark required to be reached and maintained to qualify for any incentive money, which was $7.67 million at that level. Navistar has received those funds, and must maintain that employment level for at least five years or the company would have to return the funds, under the incentive deal. The deal also requires a company to maintain the employment benchmark for at least 90 days in order to initially receive the money. Those requirements are standard for companies to receive money from the Shoals Economic Development Fund. The next phase, if it's approved Wednesday, will now call for $2,271,000 in incentives from the fund for reaching 1,100 employees. ------------------------------------------------------------------------------------- Times Daily / June 16, 2015 A startup company is teaming with Navistar to build intermodal containers in Colbert County in a move that will provide at least 125 local jobs. American Intermodal Container Manufacturing Co. and Navistar will jointly produce 53-foot-long, high-tensile steel domestic shipping containers at the Barton Riverfront Industrial Park. American Intermodal will use about 400,000 square feet of the mammoth plant currently occupied by Navistar and FreightCar America, said CEO Patrick Marron. “This agreement will allow our company to meet a critical need in the domestic intermodal container market by producing and delivering an American-made product that will exceed current industry standards.” Marron said the containers are the type that frequently are seen double-stacked on trains. He said the 53-foot containers are only used in America and only manufactured in China. In fact, many products used in the production of the containers are American products that are shipped to China for production. "The largest trucks allowed are 53 feet long," he said. "There are no American manufacturers that produce those at this moment in time. They are made primarily by two companies in China." American Intermodal was created in 2012 and partnered with Canadian company Centerline Limited, a Windsor, Ontario, firm that will build an advanced robotic welding and fully integrated assembly production system at the Barton plant, Marron said. He said the system will have capacity to product more than 15,000 containers per year. It includes an environmentally friendly paint system. The plant should be in full production by March, he said. "Once we're fully operational, employment will be conservatively north of 125," Marron said. "We'll start installing painting equipment in August of this year and it'll take several months. Then the robotic assembly line should be completed in late January. We hope to have the first salable containers by March." He said wages will be competitive with those in the local market. Forrest Wright, president of the Shoals Economic Development Authority, said his agency started working with American Intermodal in late 2013. "It's been a long, ongoing project," Wright said. "They're entering into a relationship with Navistar where Navistar will do the manufacturing process. It's a good project." The Barton plant already has about 1,000 workers between Navistar and FreightCar, Wright said. ------------------------------------------------------------------------------------- Ex-Navistar exec Jack Allen named chairman of American Intermodal Container Manufacturing Transport Topics / March 24, 2015 American Intermodal Container Manufacturing (AICM) has named former Navistar Inc. executive Jack Allen as its chairman, the company said March 24. AICM also appointed Patrick Marron as the group’s CEO. Allen was with Navistar from 1981 until he retired as the truck and engine maker’s chief operating officer in November. “Jack brings an enormous amount of talent and energy to the AICM team,” said John Maguire, AICM’s founder and managing board member. “His extensive experience and proven leadership in the commercial trucking industry is an immediate game changer for our company’s entrance into the domestic container market.” AICM has an “excellent leadership team and business plan that will position us as a strong U.S. manufacturing company,” Allen said. Marron joins AICM with more than 30 years of executive experience, most recently as COO at Four Seasons, a division of Latium USA, an international metal products manufacturing, distribution and installation company. AICM is a privately owned company formed to provide the North American market with 53-foot domestic shipping containers and similar transportation products. ------------------------------------------------------------------------------------- Navistar, FreightCar team up at Barton plant The Times Daily / February 20, 2013 One of the largest railcar producers in the world is sub-leasing a portion of Navistar Corp.’s Barton plant with plans to build up to 7,000 railcars annually. FreightCar America officials said Tuesday they hope to begin production in July and have 200 workers on site by the end of the year. They expect to employ 400 people at the plant by the end of 2014, said Terry Heidkamp, senior vice president of operations for FreightCar. As part of the arrangement that allows FreightCar to use two of the plant’s four assembly lines, the two companies are forming a partnership. Navistar will assist in maintenance and production of the railcars. Heidkamp said FreightCar produces about 70 percent of the coal cars manufactured in America, but the company wants a variety of railcars. “We need a new footprint, a different footprint that will help us better compete in the market,” he said. Navistar leased the nearly mile-long plant from National Alabama in September 2011. The company announced last year it would build a new truck at the facility, but plans have been put on hold, as Navistar facilities in Springfield, Ohio, and Mexico are at sufficient capacity to meet existing demand. Lauren McFarland, corporate communications manager for Navistar, said wages will be competitive with the skills needed. She said wages will range from between $12 and $14 an hour up to $20 an hour. The Shoals Economic Development Authority and Shoals Industrial Development Committee unanimously voted Tuesday to allow Navistar to count jobs related to FreightCar’s operation toward a local incentive package. Local governments will pay Navistar $7.67 million in incentives if 900 people are working at the plant. An additional $7.67 million is awarded if that number reaches 1,350. After that, $3.83 million is awarded if the number reaches 1,500 and $3.83 million more if it reaches 1,800 by 2016. David Bronner, chief executive officer of the Retirement Systems of Alabama, said officials had hoped Navistar would have a “quick and heavy” start but various issues have stood in the way. That slow start could be a blessing in disguise. “It may actually be better for the area to have two publicly listed companies,” Bronner said. “In time, this will be bigger than we had originally anticipated with just one company.” Tuscumbia Mayor Bill Shoemaker, chairman of the industrial development committee, said Tuesday’s announcement means the plant has two quality companies working together. “The products they’re building are just a perfect fit,” Shoemaker said. “This is teamwork between them, and each feels good and can’t wait to work together. Most of the plant still will be available for Navistar to produce their product. It really is the perfect match.” FreightCar has headquarters in Chicago and operates manufacturing facilities in Danville, Ill., and Roanoke, Va. FreightCar America has no debt and a good cash balance, Heidkamp said. Danville’s 250 employees received notices earlier this month of a possible layoff in April. Andress said that is not a sign of plans to shut down the plant. Instead, it is the result of a depressed coal market. He said Roanoke has a good backlog of orders, while Danville’s is not as full. Navistar said 180 people are working at the plant now, and project having over 300 at Barton by the end of 2014. That, coupled with FreightCar’s anticipated employment levels, would mean more than 700 people would be working at the plant. While FreightCar specializes in coal cars, Heidkamp hopes to produce a variety of railcars at Barton including flatcars, intermodal cars ... and other types. The plant in the Barton Riverfront Industrial Park was built in 2007 by Canadian-based National Steel Car. The concept of building a plant that can manufacture a diversity of railcars was stressed during production of the facility. The company struggled financially because of a downturn in the railcar industry, and the Retirement Systems of Alabama stepped in to take over operations at what became known as National Alabama. Heidkamp said FreightCar America will invest about $23 million into configuring the two productions lines for its purpose. That is significantly less expensive and time consuming than building a new plant or going into a plant that is not set up for railcar usage, he said. “Because of the way the facility was designed and what it was built to do, it’s perfect for us,” Heidkamp said. He said the company ultimately hopes to produce 6,000 to 7,000 railcars a year. “Our strategy for a while has been to grow our product line.” Ray Koopman, district of manufacturing and business development for Navistar, envisions the companies looking for ways to continue developing their partnership at the plant. “We’ll be looking at projects we can work on together,” Koopman said. “If all this ends up being is a customer-supplier relationship, we have failed. We’ll aggressively go after additional fabrication opportunities that utilize our equipment.” Andress said the partnership and facilities bring a lot of potential. “With us both in transportation, the usages of assets could be optimized.” ------------------------------------------------------------------------------------- Navistar’s Plans On Hold The Times Daily / December 17, 2012 BARTON, ALABAMA — The waiting continues at Barton Riverfront Industrial Park. Navistar International Corp.’s plan to produce its LoadStar refuse truck at the plant was stalled this year. The plant, which could create 2,200 jobs, would provide a major economic impact. But problems arose this year when the Environmental Protection Agency did not approve Navistar’s EGR emissions technology. Some activity is occurring at the plant, which has more than 150 full-time workers. Karen Denning, director of communications for Navistar’s truck division, said fabrication operations are going on at the Colbert County facility. Denning has not commented on how long it would take until truck production gets under way. The Retirement Systems of Alabama (RSA) is providing financing for Navistar’s operation at Barton. In March, Navistar announced it would build its International LoadStar truck at Barton. In June, company officials announced the truck’s body also would be built at the plant, meaning everything but the engine would be built at Barton. The engine would be manufactured at its Huntsville plant. The Barton facility was constructed after the July 2007 announcement that the National Alabama railcar plant would operate there and bring at least 1,600 jobs. A weak economy and other problems thwarted those plans, causing RSA, which invested more than $600 million in the project, to take over ownership of the plant. Navistar took over the nearly mile-long plant in Barton Riverfront Industrial Park on January 1. The Shoals Industrial Development Committee unanimously agreed Sept. 26 to transfer the incentives committed to National Alabama to Navistar. The action allowed Navistar to qualify for up to $23 million in incentives if the company meets specified employment thresholds. The company has about three years remaining to meet those thresholds. Navistar must reach and maintain 900 workers before qualifying for any incentive money, which would be $7.67 million at that level, according to the Shoals Economic Development Authority. The company will have until December 31, 2015, to reach 1,800 workers to qualify for the full incentive package. Company officials never confirmed the amount of workers who would be at the plant, but Gov. Robert Bentley said in September it would have 1,800 workers. Officials said the plant could produce as many as 2,200 jobs when spin-off jobs are taken into account. State officials who helped put together an incentive package for Navistar said as many as 2,200 workers could be affiliated with the plant within four years. ------------------------------------------------------------------------------------- LoadStar's Stainless Steel Cab Among Advantages to Trash Haulers, Navistar Says Heavy Duty Trucking / September 2012 The upcoming International LoadStar heavy low cab-over-engine truck will use the only stainless steel cab in the segment, and will be available as an integrated trash truck complete with an EZ Pack body installed on its frame, said Navistar executives who showed it and other trucks at a sales training event in Utah this week. The Loadstar, announced in March at the Mid-America Trucking Show, will go into production next July with only a Cummins Westport ISL-G engine at first, partly because of the fast-growing popularity of natural gas fuel among trash haulers, executives said. This also will give Navistar engineers time to adjust their own engines to use selective catalytic reduction equipment from Cummins Emissions Solutions. MaxxForce diesels with SCR will be available by the end of 2013, first the MaxxForce 10 and then the 9, said Steve Gilligan, a Navistar vice president and vocational segment manager. Left-, right- and dual-steer arrangements will initially be available, with a factory built stand-up right-hand-drive option to be offered later in 2013. LoadStar marks Navistar's return to the low COE business it left more than 30 years ago when it discontinued the old Cargostar. The stainless steel and aluminum cab will be strong and highly resistant to corrosion from trash "juices" and road salts, Gilligan said. Other LoadStar features include strong variable-depth frame rails; wide offset steps for easy entry and exit; a flat floor on both sides of the cab with suspended pedals for good foot room; ergonomically designed switches and controls; and a huge windshield and large side windows for excellent outward visibility. A LoadStar prototype was shown alongside competitor products from Autocar, Mack and Peterbilt so sales people could be aware of the strengths and weaknesses of each. Short drives of each truck underlined participants' observations. Officials said the LoadStar is the first all-new new truck product for the refuse business in many years, and Navistar's large dealer body with over 600 locations is a major selling point. Concrete pumping will be another application. The involvement with EZ Pack will culminate in February with Navistar's purchase of the company, said Jim Rogers, EZ Pack's president who briefed reporters on the deal. People from the two companies are cooperating closely on planning for the acquisition as well as production of integrated trash trucks, and it will include efficient shipping of chassis from a Navistar plant to EZ Pack's facility near Lexington, Ky., for installation of packer bodies. Navistar's Diamond Logic electrical system will make for easy joining of the chassis to the body through a single sealed and locking plug. With multiplexing, body functions can be tied into the trucks' wiring, switches and controls, and functions can be programmed to work based on what the trucks are doing, Rogers said. EZ Pack's rear-, side- and top-loading bodies will be available in the integrated program, and even after the Navistar acquisition, EZ Pack will continue to sell bodies for installation on other chassis. ------------------------------------------------------------------------------------- LoadStar to Return Navistar to Heavy LCF Market Heavy Duty Trucking / March 2012 Navistar International is returning to the severe-service, low-cab-forward truck market it left in the 1980s with the Class 8 LoadStar. It is designed with extensive customer input for the waste, concrete pumping and airplane refueling markets, among others. "It's the most exciting truck I've seen in a long time," declared Jim Hebe, senior vice president for North American sales operations, who described the truck on the eve of the Mid-America Trucking Show's opening in Louisville last night. LoadStar includes innovations and features designed for long life, productivity and driver comfort, he said. These include: * A stainless steel cab with aluminum doors to minimize corrosion and increase durability; * Vocationally oriented variable-depth frame rails for strength and light weight, low height and good ride characteristics; * Ergonomically designed cab interior with body controls integrated with Navistar's Diamond Logic multiplexed wiring system; and * MaxxForce 10, 11 or 13 diesels and Cummins ISL-G natural gas engine. "We talked to drivers to better understand their needs and what is missing from the trucks they drive," said Hebe. "To fit driver needs, we optimized the space in the cab, increased seat and steering wheel movement, and adjusted joystick placement to deliver an outstanding ergonomic and customizable work environment. "The exterior boasts the signature appearance and design of the International Truck brand." Belly room is enhanced with a standard tilt/telescoping steering column and seats with 10-inch fore-aft and 6.5-inch up-down travel. Entry and exit are eased by a wide 90-degree door opening and modest 18-inch first step height. With superior driver visibility and up to 40-degree wheel cuts, the LoadStar also delivers excellent maneuverability, Hebe said. Loadstar was a name was last used for a series of International medium-duty trucks in the early 1980s, industry observers recall. The capital S modernizes it for inclusion in the builder's line of midrange and heavy trucks. LoadStar will be available for orders in October 2012 through International dealers in the United States and Canada, he said. Production will begin late this year at a plant still to be determined. . . .
-
Keith, I didn't talk (write) about that, rather the news article did. But I think it is a generally known fact that there is an ocean of individuals with overdue student loans. Paul mentioned the figure $1.3 trillion. Like any loan, they need to be paid back. There's a generally accepted principle here......pay your debts.
-
Bloomberg / February 16, 2016 JobsOhio has executed an agreement with Navistar in Springfield to support 300 new jobs that are planned there. The state's private development arm executed an agreement with Navistar in January for a $100,000 grant to support its growth in Clark County. In return, Navistar will create 300 jobs, and plan $10.4 million in capital investment, in addition to a $12.9 million capital investment at its truck plant in Springfield. Last year, Navistar received a 60 percent, six-year tax break from the state on the project. Last fall, Navistar announced it was adding a production line in Springfield as part of a deal to make trucks for General Motors, with the first vehicles rolling off the assembly line in 2018. The company is retaining 1,100 employees at the site. Lisle, Ill.-based Navistar has nearly 16,300 employees across all of its operations, and is one of the biggest manufacturers in the Dayton region. Navistar at one time employed over 5,000 people in two plants, dropping to a low of 700 people in one facility by 2012.
-
Dodge updates off-road offerings with freshened Power Wagon
kscarbel2 replied to kscarbel2's topic in Trucking News
-
Dodge updates off-road offerings with freshened Power Wagon
kscarbel2 replied to kscarbel2's topic in Trucking News
-
FCA Press Release / February 11, 2016 Related reading - http://www.bigmacktrucks.com/index.php?/topic/43292-jay-lenos-garage-1942-dodge-power-wagon-restomod/?hl=wagon
-
Volvo’s UD Truck unit to end production of medium trucks
kscarbel2 replied to kscarbel2's topic in Trucking News
Volvo Group acquired NIssan Diesel (aka UD) in 2007 for US$1.1 billion (7.5 billion kronor), and now will sell rebadged light and medium commercial trucks. The high-end Quon heavy truck range, and decontented Quon-derivative Quester, will remain.......for now. -
But of all the Sherman variants, only the M4A4 used the Chrysler A57 multi-bank. Like the Caterpillar D200A radial (a Wright R-1820 aircraft engine converted to diesel, aka RD-1820), the Chrysler powerplant saw limited use. It was complex, and thus expensive and time-consuming to produce, whereas the Ford GAA (and Continental R975) could be produced cheaply in high volumes. One of the Sherman's biggest flaws was the Army's lean toward gasoline engines. That they were nicknamed "Ronsons" (after the lighter) tells you something. Far fewer men would have died had they been equipped with diesels like the German and Russian tanks.
-
Transport Topics / February 16, 2016 Trailer maker Wabash National Corp. will introduce a new rear impact guard option at the end of February at a major industry conference, the manufacturer said Feb. 16. The RIG-16 Rear Underride Guard System will make its debut at the Technology & Maintenance Council’s annual meeting in Nashville, Tennessee. Lafayette, Indiana-based Wabash also said truckload and dedicated carrier J.B. Hunt Transport Services has ordered 4,000 dry vans with the RIG-16 option and production on them started in January. Wabash also said the new system — patent pending — is available in limited production and is scheduled to increase over 18 months. “We have been building our rear impact guards to exceed U.S. and Canadian standards since 2007, but we haven’t stopped there,” Wabash CEO Dick Giromini said. “For the past three years, we have spent considerable time, money and facility resources [in research and development] specifically focused on enhancing rear impact guard performance.” “At J.B. Hunt, we value safety above all else,” Hunt CEO John Roberts said. “We applaud Wabash National’s leadership and advancements in rear impact protection, and we’re proud to be the first fleet to specify the new rear impact guard design.” Wabash said the new rear impact guard is made of advanced high-strength steel. The design features two additional vertical posts and a longer, reinforced bumper tube, all of which are engineered to work together to absorb energy better and deflect rear impact at any point along the bumper. In addition, the new guard is fully galvanized to resist corrosion, the company said. Underride guards hang below the rear of a trailer to prevent automobiles from sliding underneath during a crash. Such accidents can cause severe personal injuries without protection. Press release - http://news.wabashnational.com/wabash-national-to-introduce-new-rear-impact-guard/
BigMackTrucks.com
BigMackTrucks.com is a support forum for antique, classic and modern Mack Trucks! The forum is owned and maintained by Watt's Truck Center, Inc. an independent, full service Mack dealer. The forums are not affiliated with Mack Trucks, Inc.
Our Vendors and Advertisers
Thank you for your support!