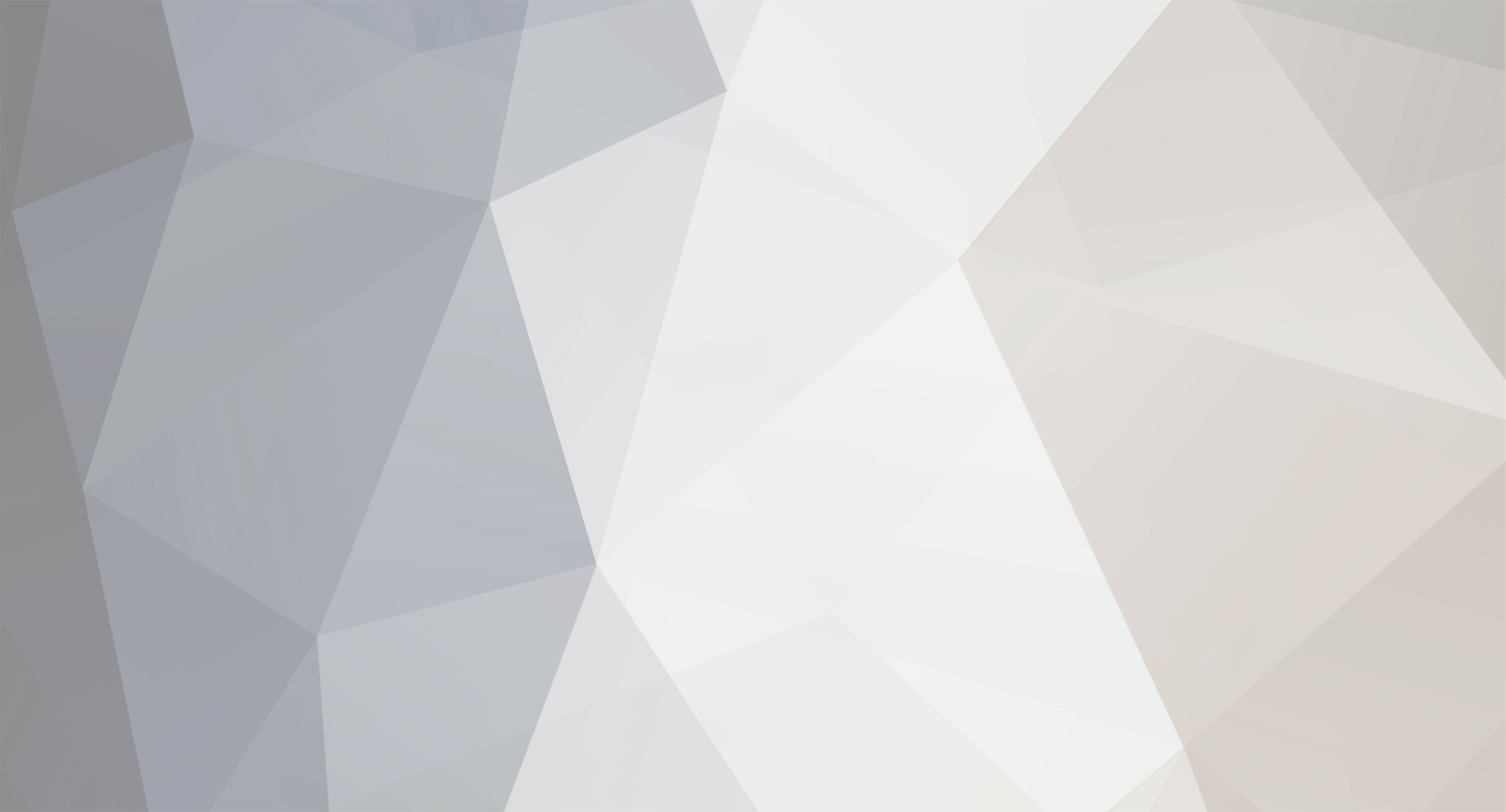
Bollweevil
-
Posts
604 -
Joined
-
Last visited
-
Days Won
4
Bollweevil replied to skip's topic in Antique and Classic Mack Trucks General Discussion
Bollweevil replied to 41chevy's topic in Antique and Classic Mack Trucks General Discussion
Bollweevil posted a gallery image in BMT Member's Gallery - Click here to view our member's albums!
From the album: Old Trucks
Images added to a gallery album owned by Bollweevil in BMT Member's Gallery - Click here to view our member's albums!
Bollweevil posted a gallery image in BMT Member's Gallery - Click here to view our member's albums!
From the album: Old Trucks
Bollweevil posted a gallery image in BMT Member's Gallery - Click here to view our member's albums!
From the album: Old Trucks
Bollweevil posted a gallery image in BMT Member's Gallery - Click here to view our member's albums!
From the album: Old Trucks
Bollweevil posted a gallery image in BMT Member's Gallery - Click here to view our member's albums!
From the album: Old Trucks
Bollweevil posted a gallery image in BMT Member's Gallery - Click here to view our member's albums!
From the album: Old Trucks
Bollweevil posted a gallery image in BMT Member's Gallery - Click here to view our member's albums!
From the album: Old Trucks
Bollweevil posted a gallery image in BMT Member's Gallery - Click here to view our member's albums!
From the album: Old Trucks
BigMackTrucks.com is a support forum for antique, classic and modern Mack Trucks! The forum is owned and maintained by Watt's Truck Center, Inc. an independent, full service Mack dealer. The forums are not affiliated with Mack Trucks, Inc.
Thank you for your support!