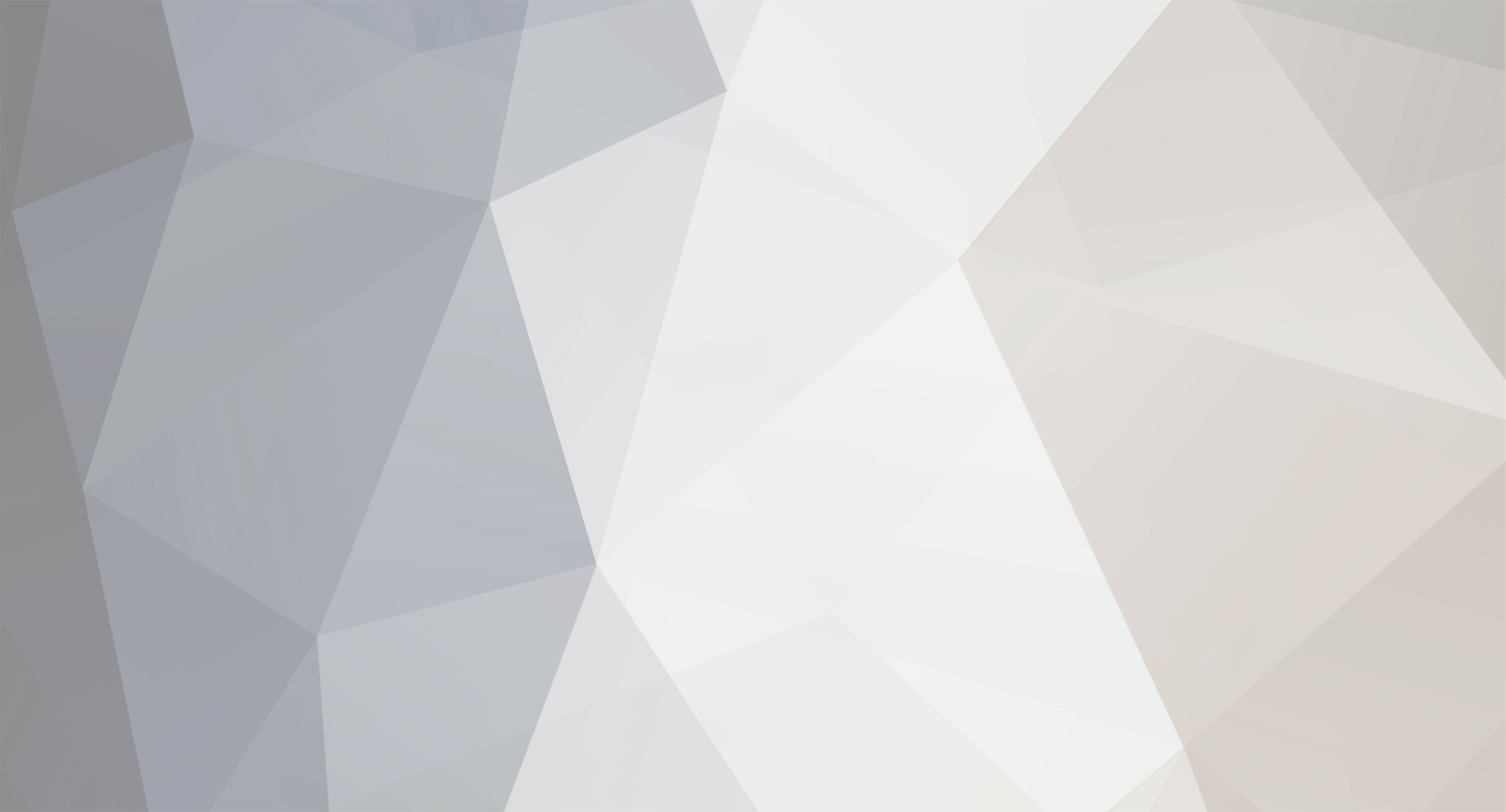
JoeH
-
Posts
2,712 -
Joined
-
Last visited
-
Days Won
18
Content Type
Profiles
Forums
Gallery
Events
Blogs
BMT Wiki
Collections
Store
Posts posted by JoeH
-
-
-
+1 on that radiator shroud looking goofy. That fan is way low and tiny compared to that massive radiator.
Also, I'm entirely unfamiliar with B's, are the X braces above the engine normal in B's? They've been cut, which is no big deal to replace.
-
1
-
-
21 hours ago, DavCut said:
Sorry to hear about the accident @JoeH . Hopefully all involved are okay. 🤞
I see from your photos that you’ve pulled the mixer off. Was there much damage to it?
Enjoyed your build thread from when you assembled this rig. I’m sure that she will rise from the ashes better than ever.
Mixer is largely fine, a little porta-power work, a little welding, and a couple small covers and the mixer should be (almost) good as new.
-
2
-
-
I had hoped to avoid Plan B on the cutoff, but seeing as we couldn't get any of the aluminum bulkhead connectors to unplug, I had to cut the big harnesses on either side.
About all that remains is the oil gauge pressure line going to the cab from the filter housing and the transmission shifter cable. Should get those done pretty quick tomorrow afternoon after concrete, then hopefully we'll have time to lift the cab off the chassis and get ready to bring it into the garage to strip down, patch a hole in the floor, and a few other things to get it ready to go on the truck.
-
1
-
-
On 1/3/2024 at 10:24 AM, Mackpro said:
On trucks where the air compressor gets it’s fresh air from the piping between the air filter housing and the turbo, we see guys running dirty air filters and the engine is sucking for fresh air so hard it pulls oil up past the rings on the air compressor which pumps it into the air drier/air tanks. Very common on the 2003.5 -2007 Aset Ac engines . Could also happen to any truck with air compressor getting its fresh air this way.
My '79 endt676 we tried a small filter they make that goes right on the compressor, so it had an intake independent of the engine. Still pumped oil.
-
1
-
-
- Popular Post
- Popular Post
"one of three" claims could mean a couple things....
One of three that he has for sale?
One of three like that that the original purchaser bought?
-
3
-
-
Chassis is sitting in the garage, not sure there's anything left to do today.
Need to pull the spare cab off the cutoff, steal whatever we need for the radiator/CAC assembly on this truck, install/gut new cab, swap guts from our cab to the new cab. Hopefully we can work in a coat of paint on the new cab before it goes onto the truck.
-
-
What's the plan for this machine?
-
That's pretty awesome. Never know what someone will find logging into this site!
I hope it runs, it looks clean, no rust in that flyer. I'd love to see that thing working on a job site, but I don't suppose that'd be good for preservation and whatnot.
Probably didn't sell more as a Scraper does the work of 2 pieces of equipment, self loads and hauls it off to dump.
-
1
-
-
- Popular Post
- Popular Post
Fair question, Joey. To elaborate on noises the air compressor can make: my '79 makes a ticking sound when the air compressor is building air pressure, and stops when the governor cuts off the air compressor. It's subtle, but maybe yours is behaving similarly?
-
3
-
24 minutes ago, terry said:
I had a 237 engine that had a loose exhaust seat, ran quite awhile that way, had the pop,pop when you let off it or coasted with it, when I pulled the head you could see where it was moving up and down in the carbon buildup. Terry
My '79 makes this kind of a pop pop on throttle let off.
Let us know what you find on valve lash.
-
Fortunately I have this gem of a 14,000 original miles ETECH 300 spare for any SNAFU's 🤠
-
Starter is relatively new, changed it 2 years ago during our frame overhaul. Batteries relatively new, but they did lay on their side for a few hours during the rollover and then sit for 2 months. Truck has a battery kill switch on the battery box, but it is underrated IMO. It gets hot from excessive cranking. Once the truck was running under its own power it was charging at 14.250 volts according to the laptop.
Restarted on its own no problems after we let it run for a few minutes. Voltage issue doesn't concern me, but it's helpful for people to know how bad voltage can affect trying to start an electronic truck.
The slight miss is going to need to be looked into, while this EUP system is good, there's nothing better than PLN for durability. We have not adjusted the valves, never even had the valve covers off.
I keep hearing the term CCRS. What is CCRS, and how's it fit in the ETECH/ASET family?
-
Considering the same year block can put out 25psi boost on the 283hp version I can't think of anything that'll get hurt at 20psi. That head you had rebuilt would make me nervous, it took a beating. Wouldn't be surprised if a valve seat worked itself loose...
The fuel pump is what limits the truck on power. The turbo will only put out enough air to match the fuel pump needs. I think. Basically the fuel exhaust drives turbo, so when you run out of fuel potential you run out of turbo potential.
-
1
-
-
Truck has about 430k miles and over 27,000 hours. No idea if the engines ever been rebuilt, so maybe injectors are squirting a little funny. Would be curious to look into injector spray pattern testing tools, no idea if there's anything affordable for occasional use.
-
Today we pulled the secondary filter housing off the replacement cab cutoff assembly we bought a few weeks ago, replaced the damaged fuel lines, installed a new secondary filter (I guess we should have done the primary filter while we were at it...), primed it up, hooked up the laptop, and turned on the key. All active codes are related to the torn ABS sensor on the passenger wheel. New sensor gets picked up in the AM on my dad's way in to work. (Hopefully we can get all the codes cleared up before we have to start gutting the cab.) Engine shutdown light was on, a bit of coolant and that went away.
Engine wouldn't start, laptop showed voltage dropping below 9.5v, which I think is about where the EECU won't fire off. Battery charger on, my dad shot a little ether in the intake, and we managed to stop cranking while it was chugging on ether, and with the voltage spike back up to normal I think the EECU was able to kick in and start firing in some diesel! It coughed through whatever air got into the injector lines and the idle steadied right out.
We pulled the bumper, pulled heater core hoses and butted them together, pulled the passenger cab latch off, rear engine heat shield, scratched our heads a few times, and called it quits. Not rushing into this too aggressively, it's a bit of a Gordian knot. I'm not Alexander the Great, so I won't be untying this one with a sword.
All looks good on the electronics side, so now we have a baseline of systems functionality before we gut the cabs and put all our wiring from this cab into the replacement cab.
The engine does have a slight miss, which it had before the rollover. @Joey Mack any tips on what to look for? Broken EUP springs? It has no codes, so whatever it is it'll likely be mechanical.
-
1
-
-
I guess I should start a new thread to document this task.
Truck got put in the ditch Nov 11th 2023, busted the cab pretty good. Most of the obvious damage to the cab was to the passenger side, but from the twist applied from impact, the driver side of the cab has some buckling and cracking in a few places.
Secondary fuel filter housing magically disappeared in the accident, ripping the ends off the fuel lines, which is a good thing because it helped starve the engine for fuel so it didn't idle too long on its side.
I pulled the crushed passenger door and unbolted the crushed step assembly the other day.
-
I'd pull valve cover. Never know what you'll see, broken rocker arm shafts, broken valve stem....
I'd also look into condition of the camshaft EUP's and H Clips, you could have broken bits there eating up the camshaft. If so, this would be a prime time to read the "old dog dead dog loggin dog" remediation thread to delete your ASET AI (guessing your truck is a granite) emissions system.
-
Keep us posted on what you find, helpful for us E7 owners down the line!
-
1
-
-
- Popular Post
- Popular Post
Dont waste your money on air compressor from Mack, it'll do the same thing. My 1979 endt676 does the same thing. We put a dryer on to try and keep the tanks clear, but it makes so much oil it was leaving stains on customers' driveways so we pulled it right back off. E7's forward actually pull the air compressor intake line off the intake manifold, so they're actually getting boost pressure off the turbo. Plumb your air compressor supply line this way and it may help with the situation. There's a whole science behind piston compression rings, they're slightly sloped so that more pressure actually helps press them against the cylinder walls harder for better sealing. Or at least an engine textbook I inherited from my deceased uncle says as much.
-
3
-
Before I pulled my engine, I disconnected the oil cooler and the radiator, plugged the lower radiator line and filled the engine with water to watch it for leaks. Had water coming out the oil pan drain bolt, so we pulled the motor, stripped it down and found the o rings that seal the piston sleeves were toast. Did a thorough visual inspection for cracks in the block due to overheating, then rolled the dice on a $2,000 rebuild kit.
Not sure about the ETECH block, but the E7 block supposedly is half dry half wet sleeves. There's a great video on YouTube from the early 90's by Mack that shows rebuilding the E7. The sleeves have a step shoulder halfway down the sleeve that gets Mack RTV silicone, I think in addition to O rings.
Think through the possible cross contamination points between the water jacket and the crank case. Cracked heads, head gasket, cracked block, sleeves corroded through, oil cooler...
-
2
-
-
- Popular Post
- Popular Post
We paint our 3 TDC marks with a bright yellow marker and which cylinders are on TDC with each mark. Saves a lot of headache.
-
3
Winter is back
in Odds and Ends
Posted
Glad you got home safe, we haven't had much of a winter here in southeastern PA in a couple years now. Some cold coming in next week, but no snow worth talking about yet.