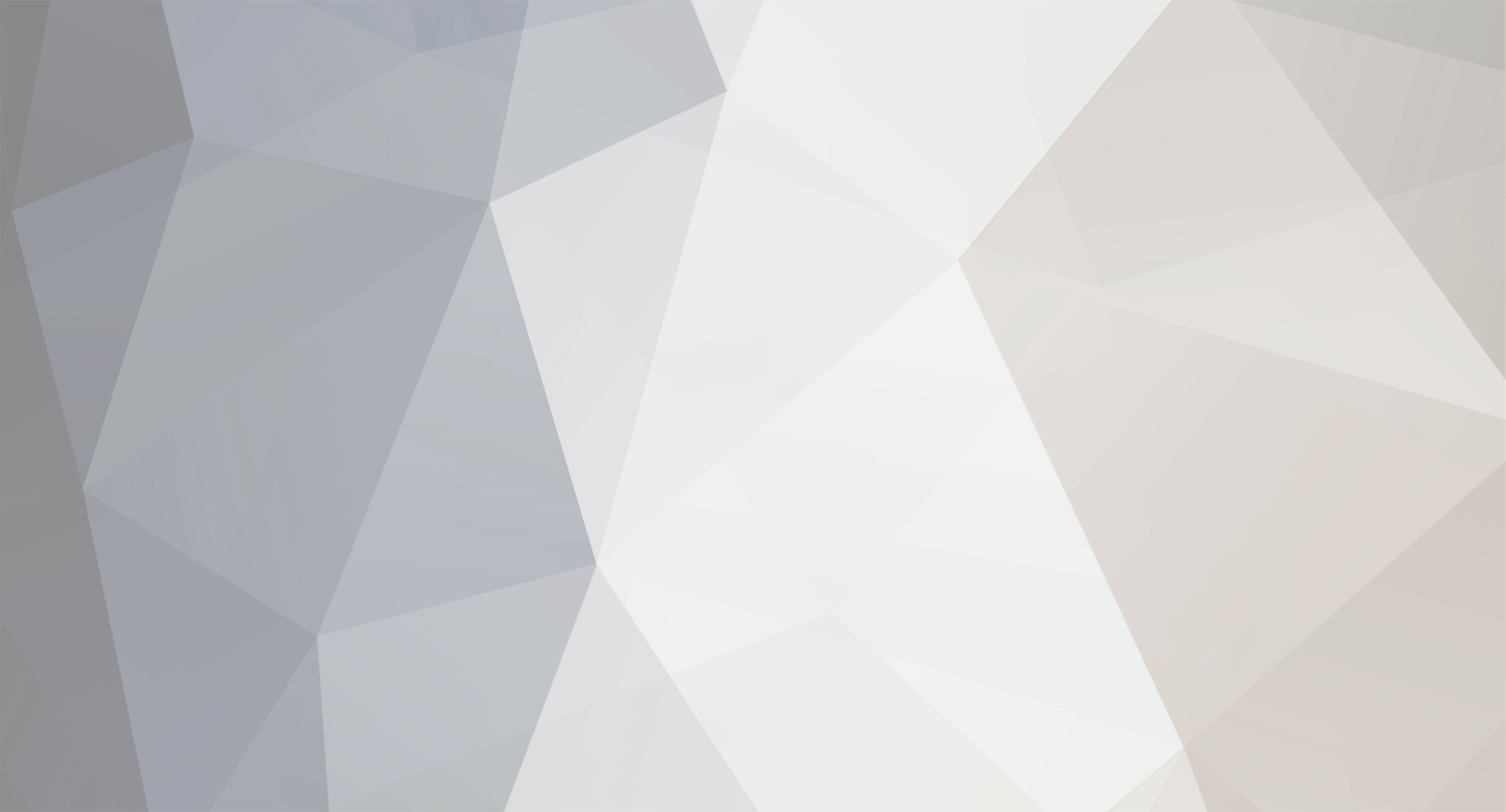
steeler
-
Posts
304 -
Joined
-
Last visited
Content Type
Profiles
Forums
Gallery
Events
Blogs
BMT Wiki
Collections
Store
Posts posted by steeler
-
-
15 minutes ago, Onyx610 said:
Jack the engine up, your engine mount could be bad.
Its hitting the engine block. Otherwise no clearance issues. Apparently this isn't an issue with the 07 emissions, only after 10 I think.
-
Yeah this one is hitting a hump in the block where an oil pan bolt threads in. Barely, but enough that the valve will not drop down far enough.
I found a service bulletin for the leu, which states to remove turbo, egr cooler, then filter head. Only other option in seeing here is to gently shave that oil pan boss on the block enough to get it out.
31 minutes ago, Joey Mack said: -
5 minutes ago, Joey Mack said:
are you trying to replace the plunger in the piston cooling tube control, under the right side of the engine? jojo
Yes, mp7, in the front of the oil filter housing.
-
2016 GU. What in the world is going on here! Piston oil thermo valve won't come out without stripping down half the engine? Or does someone have a trick?
-
Not sure if it applies to the 18s, but this was an issue with several leu's that I've worked on. There is a service bulletin about the soot level not resetting, but I can't remember what the fix was.
-
Usually when the cups start leaking, it will run fine after you get it started. I've seen engines with 3 Badly leaking cups run great, just hard to start. When it gets to the point you start noticing an engine miss under load, that's when you're running out of time with them.
Sadly there really isn't any way to get by on the cheap. Pretty much just fix it or run it.
-
1
-
-
Don't some aftermarket coolant filter come WITHOUT the additives in them? Could be wrong there but was thinking they did?
I'm a fan of the extended life coolant and forget it. If you run a filter with additives and extended life coolant, you get the sludge crap that floats at the top.
-
1
-
-
On 10/31/2021 at 9:56 AM, fjh said:
Yup ! how ever this little issue mentioned here causes a lot of grief for the dealers as well, dam nescience phone calls asking what's this code? is it important ? Bla bla , ! There is no problem making money for the dealers with New equipment of any sort! Mother Volvo IS all about the money and I guess they should be, got to impress the share holders! SELL THEM PARTS BOYS!
You are right, I never considered that being why they took the codes of of the dash. I should have though, because I get those calls all the time.
-
First step is to try to identify where the air leak is coming from.
If it's leaking into the case of the transmission, the air will be heard at the breather which is on top front left in the shift bar housing.
When you say you replaced the valve, I'm assuming you mean the slave valve on the driver's side of the transmission?
If so, and you've replaced the shifter knob, then the only thing left is going to be the o rings on the range piston. Not a big deal if you have some mechanical ability, you can remove the range cylinder and replace the o rings without removing anything else.
-
1
-
-
Nope. They took the diagnostics out other than to check the cluster. I guess they wanted to help the dealerships make money.
The ABS/ATC code is more than likely also why the other light is on.
-
1
-
-
On 10/28/2021 at 3:09 PM, Hulio said:
How do you tell which cups or injectors are bad? Once you pull the old ones out are they damaged by the removal process? Might seem Petty but at several hundred a piece why do all six when one has gone bad in less than 100k? Is it usually the injectors or just the cups? Can you replace one without the other?
Am I mistaken or is it simply extreme pressure that holds them in until the injector is installed and torqued?
No way to really tell which one /ones are bad without removing and inspecting them. Usually when I find 1 leaking, there are a couple more that are either leaking or about to.
Imo no point in doing 1 (assuming you are lucky enough that the first one you pull is the culprit) because the others will be leaking soon.
The injectors /cups once installed, mate to each other, so you can't just replace 1 without the other.
They say you can reinstall an old injector into the same cup after removal, but I don't think I've ever encountered a situation where I did that. When they come out, it's because I know they are leaking so it's all going to be replaced.
-
1
-
-
An 8908 would be an 8,000 lb transmission, where the more common 14908, or 16908 would be 14,000, and, 16,000. Can't say I've ever seen an 8908 in a tri axle though. What did it come out of?
-
Thanks guys I'll check those out. My fear is that I'm going to kill power to it which will bring it to life again for another 3 days and not be sure I've fixed the problem.
These are the jobs that I wished I still worked at a dealership. If it wasn't fixed after tossing a couple thousand bucks at it, oh well! Can't do that at this shop though.
-
I must be cursed with mystery problems!
I'm working on a GU with an MP7 that will occasionally either die and not restart, or just won't start at all.......UNTIL you unplug the engine ECU. Then it will fire right up and might run trouble free for 3 days until it happens again.
When the problem occurs, I have no communication with the engine e cu. No coolant temp, oil pressure etc. No matter what I do, it won't start until I remove power from the ecu.
I have replaced the ecu, but that didn't fix it. Sometimes when you turn the key on, the ecu will communicate fine, but as soon as you hit the starter, it will clunk and then the engine ecu goes dead. Other times, it's just dead from key on.
I've tightened and cleaned every cable on this thing. Frustrating!
Any ideas?
-
The fuse for the turbo is in the panel by your left foot.I can't remember which one (p13 maybe).
-
Problem found! Long story short is original complaint was low power and black smoke. After replacing the injector I found 4 intake manifold bolts broken and cracked manifold. That didn't help the smoking.
Went ahead and pulled dpf and found it completely melted out. O don't have any idea how this thing regened normally and didn't have a single dpf code in it. But oh well!
-
29 minutes ago, Mackpro said:
I remember having lots of issues with a certain emission year group of MP7’s. I believe it was around the 14-15 year models. Engines would have lots of injector codes and not running smoothly. The wiring harness was rubbing the top front of the air compressor. Mack sent out a bulletin it at the time. It’s worth a shot, I remember using a long pry bar to lift up the harness and a mirror to look under it for bare wires , it was hard to reach .
Yup, I've changed many harnesses for that problem. Never had one at like this, but I'll definitely be checking that.
Another thing I thought was strange was that the suspect cylinder had a different part number injector, but it crossed to the same part, except it showed as a new injector and not a reman. None of them looked like they had been replaced recently though.
-
Hopefully somebody can lead me in the right direction here. I'm working on a 2013 Mph that is black smoking and throwing codes for cylinder #4 cylinder balance, and cylinder #4 misfire.
I replaced #4 injector, that didn't help at all. I've ran compression test which all cylinders checked perfect. When I do the cylinder balance test with tech tool, #4 is way overfueling.
Cylinders 1 and 5 are near zero in the balance test, 2 and 6 are about -17, and #4 is climbing pretty fast at +56. #3 is -25.
Not sure where to go other than throwing 5 more injectors at it, but that would be a pricey strikeout!
-
That's more than likely not a head gasket problem, but rather a leaking liner. Time for an inframe.
-
I wouldn't be overly concerned with a small amount, if it's possibly been there previously and maybe you just didn't notice it? I would take an oil sample, that will tell you whether to worry or not.
-
On 7/6/2020 at 9:36 AM, fjh said:
If you have a mack logon at your location you can log on and go to this section ! Case based reasoning ! They have collected all of the field repairs and fixes and compiled them for guys to shoot for when having issues with this and other stuff Its one of the few things that they did right with the program ! as its not all theory Its fact base repairs Done by real people not dreamed up by someone whom has never turned a wrench!
Oh yeah, I'm brain dead from the heat lol.
What login does it take? Obviously not tech tool login. Something we don't have I'm sure. Impact?
-
On 6/19/2020 at 8:45 AM, fjh said:
We go to the injector first for most issues as it is the most common problem!Garden path diagnostics can really lead you to a lot of dead ends at times . The CBR setup is a better diagnostic tool if you can get to it! its a more realistic tried and true real world repair path! Believe it or not servicing the air drier more often can benefit in a lot of cases in wet climates WE have noticed the HC Doser gets ruined by water in the air sends shit down the line clogging the injector as well also the the dollar store fuel line gets rotten and can cause repeat issues in the newer units!
What is CBR?
-
I'm a die hard Mack guy, but if you aren't talking about looks of off road, or a rail truck, then Eaton is the way to go.
I can repair the common issues with Eaton (jumping out of gear/synchro) much cheaper than the common synchro repair on the T300. Not to mention I think they are easier to shift, but I'm a tech not a driver.
-
1
-
-
Has anybody cleaned out, or know where the dang A/C drain is on an LR? I can't find it anywhere under the evaporator where you would think it would be.
There is a channeled little brace directly under the cab below the evap core, but if it drains into it there is no way to unclog it.
I hate to pull the core out just to clean to mud from the drain.
Oil thermostat replacement
in Engine and Transmission
Posted
That's what I've normally seen as well. I didn't get so lucky this time. This one is actually causing the red shutdown light. I plugged in a new thermostat and the code goes away.
Had a guy at our local dealer tell me that mack says to remove the filter head, but he's been able to get them out without doing that.
If I have to do some block shaving, then shaving I will do!