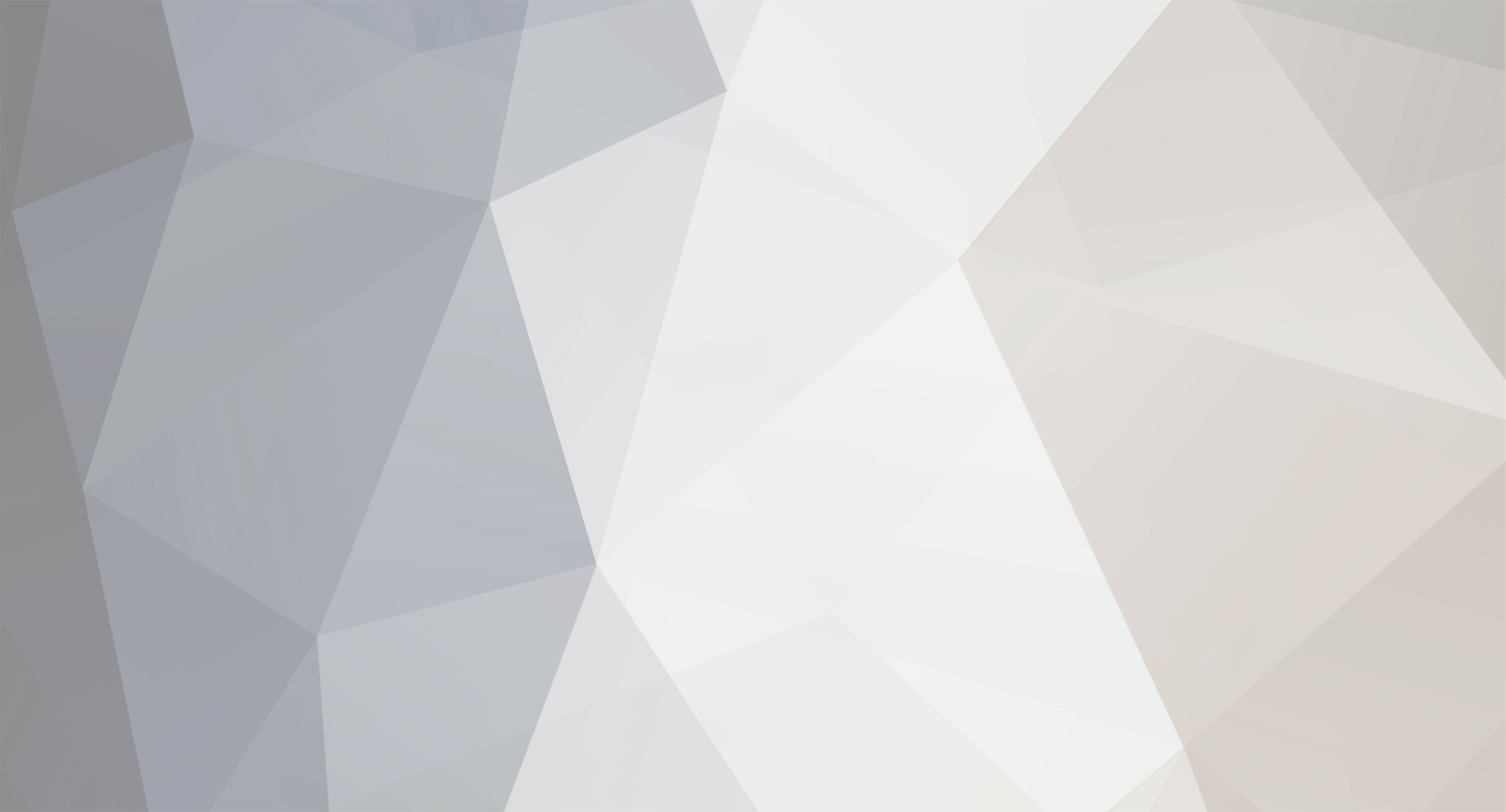
kscarbel2
Moderator-
Posts
18,730 -
Joined
-
Days Won
114
Content Type
Profiles
Forums
Gallery
Events
Blogs
BMT Wiki
Collections
Store
Everything posted by kscarbel2
-
Press Release / June 2, 2015 GAZ Group has introduced the next generation range of its legendary Ural truck brand at the 16th annual construction equipment and technologies exhibition taking place in the Crocus Expo Center from 2 to 6 June. The new Ural heavy truck series will be available for order in the second half of 2015. Offering new levels of fuel efficiency and comfort, the modern looking new “Ural Next” are available with a broad range of specifications to meet varying global requirements. While maintaining the traditional advantages of the Ural brand, a unique cross-country capability combined with high functionality, the new trucks offer improved handling and fuel efficiency. The base powertrain for the Ural Next is a new YaMZ-536 diesel engine offered in 240, 285 and 312 horsepower ratings, paired with either YaMZ or ZF transmissions. In addition to diesel power, both methane and compressed natural gas (CNG) engines are now available. The maximum front gross axle rating has been increased from 5.3 to 6.5 metric tons, while the permissible payload has increased from 12 to 13 metric tons. Allowed gross vehicle weight has increased to 22.5 metric tons, and the gross combination weight rating has risen to 38 metric tons. The redesigned transfer case has a 40 percent higher torque capacity, while a reduction in friction has reduced fuel consumption by 8 percent. Chassis strength has been reinforced on long wheelbase models. Upgraded axles result in longer service life. Redesigned propeller shafts have twice the torque capacity as previous models for significantly extended driveline life. Featuring Wabco brake components, integrated power steering, pneumatically-actuated transfer box and intra-axle differential locks, the Ural Next can easily overcome the most difficult off-road conditions. “The development of Ural Next is the result of successful cooperation between enterprises and design services of GAZ Group,” says Vadim Sorokin, GAZ Group President. “The cab for new Ural Next is based on the GAZelle Next and GAZon Next cab, and the YAMZ-536 engine was developed at our Yaroslavl Motor Plant. Ural engineers used their unique experience for developing vehicles for operation in extreme off-road conditions. The outcome of strong cooperation between GAZ Group’s business units is a new next-generation heavy truck that can exceed the varying requirements of the customers around the world.” “We have an ongoing commitment to keep our Ural series at the forefront of heavy truck development,” says Ural Plant Managing Director Victor Kadylkin. “By focusing on the demands of our customers, we have created a new generation Ural truck that will help to increase our market share worldwide in the heavy truck segment. Ural Next is characterized by its modern look and interior, comfortable cabin, easy drivability and improved performance characteristics including increased maneuverability and durability plus reduced fuel consumption. At the same time, the truck has retained the traditional high off-road capabilities that Ural is known for amongst customers in the construction, oil and gas extraction, forest industry, mining and public utilities segments.” .
-
The LE was introduced by the former Allentown-based Mack Trucks in 1994. Thus the LE was just 6 years sold when Sweden's Volvo acquired Mack in 2000. It's shocking that Volvo allowed this product to age 21 years before finally giving it an upgrade. LR product page: http://www.macktrucks.com/trucks/lr-series/ LR brochure (Volvo-like, ie. without specs): http://www.macktrucks.com/~/media/files/brochures/mack%20lr%20brochure.ashx?as=1
-
Must be some mistake on Stephen Roy's part for calling that an LR (then again, what would an ex-loan guy with Volvo Commercial Finance know about Macks). This, in no uncertain terms, is a Mack LR. .
-
Mack previews new LR refuse truck Fleet Equipment / April 29, 2014 Mack previewed the new Mack LR series of low-entry cabover refuse trucks designed with the driver, customer and demands of the rigorous job in mind. Initially available in three-axle 6×4 configurations and powered either by diesel or natural gas, the Mack LR series will be available in 2015. Mack captured customer input during the design and engineering phases of the new LR series and utilized the feedback to highlight the characteristics core to a refuse truck – outstanding driver comfort, efficient operation and exceptional visibility and safety. “The new cab will be configured to improve driver comfort and productivity, while also maintaining the excellent maneuverability identified with Mack refuse models,” said Stephen Roy, president, Mack Trucks North American Sales and Marketing. Designed with body builders in mind, the LR offers additional access points and mounting locations for wiring, controls, and joysticks. The LR series cab’s enhanced driver environment will include tilt and telescopic steering, power windows and door locks, memory mirrors, in-dash air-conditioning, standard in-cab LED lighting and an instrument cluster with color LCD display. Steering column-mounted main gauge pods for both the right-hand and left-hand driving positions will enhance driver visibility and improve ergonomics. Centrally mounted radio and HVAC controls, accessible from both driving positions, will further contribute to a comfortable, driver-focused cab environment. Initially available in three-axle 6×4 configurations and powered either by diesel or natural gas, the Mack LR series will be available in 2015. The LR series cab also will feature center storage for lunch coolers, two-liter bottles, beverage cups, mobile phones and MP3 players. A rear-wall unit offers two additional levels of storage. The large cab doors will make driver ingress and egress easier. The Mack LR model will be spec’d with a Mack MP7 11-liter diesel engine with 325 to 345 horsepower and torque ratings from 1,200 to 1,280 lb.-ft. The Cummins Westport ISL G natural gas engine will also be option. All LR models are will be equipped with an Allison RDS five-speed or six-speed automatic transmission. The LR series will be available with left-hand drive, right-hand drive, dual-drive and left-hand drive/right-hand stand-up drive configurations. “Refuse vehicle customers and their drivers want a comfortable, safe work environment, great visibility and controls where they need them,” said Curtis Dorwart, Mack refuse product marketing manager. “All of these elements were taken into consideration and incorporated into the design of the new Mack LR series.” .
-
Truck News / June 2, 2015 At WasteExpo 2015, Mack Trucks introduced the new Mack LR low-entry cabover refuse model. The new model was designed to meet the challenges of refuse customers who require enhanced maneuverability, increased driver comfort and improved visibility. Mack says the truck was built with input from customers, and is available in three-axle 6×4 configurations and can be powered by diesel or natural gas. “The Mack LR model is the latest example of our commitment to application excellence,” said Stephen Roy, president of Mack Trucks North America. “At Mack, we work hard to understand our customers’ needs and build durable, dependable trucks that get the job done. By incorporating customer feedback into the LR design, we’ve built a safer, more comfortable work environment for drivers, boosting productivity and driver retention.” The LR model was also build with body builders in mind, offering many access points and mounting locations for wiring, controls and joysticks. Inside the cab, there are tilt and telescopic steering columns, power windows and power door locks, memory mirrors, in-dash air-conditioning, standard in-cab LED lighting and an instrument cluster with color LCD display. The rear cab windows now wrap around the rear cab corners, improving driver visibility. It also offers centre storage for lunch coolers, two-liter bottles, beverage cups, cell phones and MP3 players. The 11-liter Mack MP7 diesel engine comes standard in the LR model, delivering 325 to 345 horsepower and 1,200 to 1,280 lb.-ft. of torque. The Cummins Westport ISL G natural gas engine is optional. It is also equipped with an Allison RDS five-speed or six-speed automatic transmission.
-
Heavy Duty Trucking / June 2, 2015 Mack Trucks introduced the Mack LR low-entry cabover refuse model (at WasteExpo 2015) designed for enhanced maneuverability, increased driver comfort and better visibility. The Mack LR model is available in three-axle 6x4 configurations and can be powered by diesel or natural gas. An 11-liter Mack MP7 diesel engine is standard, delivering 325-245 horsepower and 1,200 to 1,280 lb.-ft. of torque. The engine is routed through an Allison RDS five-speed or six-speed automatic transmission. A Cummins Westport ISL G natural gas engine is optional. “The Mack LR model is the latest example of our commitment to application excellence,” said Stephen Roy, president of Mack Trucks North America. “By incorporating customer feedback into the LR design, we’ve built a safer, more comfortable work environment for drivers, boosting productivity and driver retention.” The LR’s cab features a driver centric environment including tilt and telescopic steering columns, power windows and power door locks, memory mirrors, in-dash air conditioning, standard in-cab LED lighting and an instrument cluster with color LCD display. The interior also features column-mounted main gauge pods for right-hand and left-hand driving positions for better gauge visibility and ergonomics. The cab has centrally mounted radio and HVAC controls, accessible form both driving positions. For better outer visibility, the rear-cab windows wrap around the rear cab corners and for easier driver ingress and egress, the LR features large cab doors. The LR also offers center storage for lunch coolers, drinks, food and entertainment devices and an additional rear-wall unit offers two more levels of storage. Designed with body builders in mind, the Mack LR offers additional access points and mounting locations for wiring, controls and joysticks. Mack’s body builder support group is available to simplify the process and ensure better communication with body builders, dealers and customers. .
-
FBI behind mysterious surveillance aircraft over US cities
kscarbel2 posted a topic in Odds and Ends
The Associated Press / June 2, 2015 Scores of low-flying planes circling American cities are part of a civilian air force operated by the FBI and obscured behind fictitious companies, The Associated Press has learned. The AP traced at least 50 aircraft back to the FBI, and identified more than 100 flights in 11 states over a 30-day period since late April, orbiting both major cities and rural areas. At least 115 planes, including 90 Cessna aircraft, were mentioned in a federal budget document from 2009. For decades, the planes have provided support to FBI surveillance operations on the ground. But now the aircraft are equipped with high-tech cameras, and in rare circumstances, technology capable of tracking thousands of cellphones, raising questions about how these surveillance flights affect Americans' privacy. "It's important that federal law enforcement personnel have the tools they need to find and catch criminals," said Charles Grassley, chairman of the Senate Judiciary Committee. "But whenever an operation may also monitor the activities of Americans who are not the intended target, we must make darn sure that safeguards are in place to protect the civil liberties of innocent Americans." The FBI says (alleges) the planes are not equipped or used for bulk collection activities or mass surveillance. The surveillance equipment is used for ongoing investigations, the FBI says, generally without a judge's approval. The FBI confirmed for the first time the wide-scale use of the aircraft, which the AP traced to at least 13 fake companies, such as FVX Research, KQM Aviation, NBR Aviation and PXW Services. "The FBI's aviation program is not secret," spokesman Christopher Allen said in a statement. "Specific aircraft and their capabilities are protected for operational security purposes." The front companies are used to protect the safety of the pilots, the agency said. That setup also shields the identity of the aircraft so that suspects on the ground don't know they're being followed. The FBI is not the only federal law enforcement agency to take such measures. The Drug Enforcement Administration has its own planes, also registered to fake companies, according to a 2011 Justice Department inspector general report. At the time, the DEA had 92 aircraft in its fleet. And since 2007, the U.S. Marshals Service has operated an aerial surveillance program with its own fleet equipped with technology that can capture data from thousands of cellphones, the Wall Street Journal reported last year. In the FBI's case, one of its fake companies shares a post office box with the Justice Department, creating a link between the companies and the FBI through publicly available Federal Aviation Administration records. Basic aspects of the FBI's program are withheld from the public in censored versions of official reports from the Justice Department's inspector general, and the FBI also has been careful not to reveal its surveillance flights in court documents. The agency will not say how many planes are currently in its fleet. The planes are equipped with technology that can capture video of unrelated criminal activity on the ground that could be handed over to prosecutions. One of the planes, photographed in flight last week by the AP in northern Virginia, bristled with unusual antennas under its fuselage and a camera on its left side. Some of the aircraft can also be equipped with technology that can identify thousands of people below through the cellphones they carry, even if they're not making a call or in public. Officials said that practice, which mimics cell towers and gets phones to reveal basic subscriber information, is used in only limited situations. "These are not your grandparents' surveillance aircraft," said Jay Stanley, a senior policy analyst with the American Civil Liberties Union. Stanley said the flights are significant "if the federal government is maintaining a fleet of aircraft whose purpose is to circle over American cities, especially with the technology we know can be attached to those aircraft." The Justice Department recently published a privacy policy for its agencies' use of drones and unmanned aircraft systems. But that policy does not apply to piloted aircraft. An FBI spokesman said the FBI's flights comply with agency rules. Those rules, which are heavily redacted in publicly available documents, limit the types of equipment the agency can use, as well as the justifications and duration of the surveillance. Evolving technology can record higher-quality video from long distances, even at night, and can capture certain identifying information from cellphones using a device known as a "cell-site simulator" - or Stingray, to use one of the product's brand names. These can trick pinpointed cellphones into revealing identification numbers of subscribers, including those not suspected of a crime. The FBI has recently begun obtaining court orders to use this technology. Previously, the Obama administration had been directing local authorities through secret agreements not to reveal their own use of the devices, even encouraging prosecutors to drop cases rather than disclose the technology's use in open court. Officials say cellphone surveillance from FBI aircraft was rarely used. Details confirmed by the FBI about its air force track closely with published reports since at least 2003 that a government surveillance program might be behind suspicious-looking planes slowly circling neighborhoods. One such plane was spotted during the recent disturbance in Baltimore that followed the death of 25-year-old Freddie Gray, who sustained grievous injuries while in police custody. In that instance, the FBI was helping local police with aerial support, which it occasionally does when asked. Those types of requests are reviewed by senior FBI officials. During the past few weeks, the AP tracked planes from the FBI's fleet on more than 100 flights over at least 11 states plus the District of Columbia, most with Cessna 182T Skylane aircraft. These included parts of Boston, Chicago, Dallas, Houston, Minneapolis, Phoenix, Seattle and Southern California. Some flights orbited large, enclosed buildings for extended periods where aerial photography would be less effective than electronic signals collection. Those included above Ronald Reagan Washington National Airport and the Mall of America in Bloomington, Minnesota. David Gomez, a former FBI agent who oversaw parts of the aviation surveillance program over the course of his career, said the FBI surveillance aircraft are used to assist surveillance on the ground. For example, if a plane is following a suspect in a vehicle, an FBI ground surveillance team can lag behind so as not to blow their cover, Gomez said. After The Washington Post revealed flights by two planes circling over Baltimore in early May, the AP began analyzing detailed flight data and aircraft-ownership registrations that shared similar addresses and flight patterns. That review found that some FBI missions circled above at least 40,000 residents during a single flight over Anaheim, California, in late May, according to Census data and records provided by the website FlightRadar24.com. Most flight patterns occurred in counter-clockwise orbits up to several miles wide and roughly one mile above the ground at slow speeds. A 2003 newsletter from the company FLIR Systems Inc., which makes camera technology such as seen on the planes, described flying slowly in left-handed patterns. Gomez said the aircraft circle to the left because the pilot sits on the left side. He said different flight formations are used depending on circumstances on the ground, such as whether a suspect is on the move. The FBI asked the AP not to disclose the names of the fake companies it uncovered, saying that would saddle taxpayers with the expense of creating new cover companies to shield the government's involvement, and could endanger the planes and integrity of the surveillance missions. The AP declined the FBI's request because the companies' names - as well as common addresses linked to the Justice Department - are listed on public documents and in government databases. Recently, independent journalists and websites have cited companies traced to post office boxes in Virginia, including one shared with the Justice Department. Included on most aircraft registrations is a mysterious name, Robert Lindley. He is listed as chief executive and has at least three distinct signatures among the companies. Two documents include a signature for Robert Taylor, which is strikingly similar to one of Lindley's three handwriting patterns. The FBI would not say whether Lindley is a U.S. government employee. The AP unsuccessfully tried to reach Lindley at phone numbers registered to people of the same name in the Washington area. Law enforcement officials said Justice Department lawyers approved the decision to create fictitious companies and that the Federal Aviation Administration was aware of the practice. The FBI has been doing this since at least the late 1980s, according to a 1990 report by the then-General Accounting Office. -
Cut a new CarQuest and Wix in half and see what you're getting. You might never buy one again. Baldwin's premium filters will serve you well. However, do NOT assume that the filters Baldwin parent Clarcor is supplying to Carquest under contract is the same internally as any red Baldwin-branded filter. Cutting two in half will be another rude awakening. The day of the last generation technology filter (the low price CarQuest and Wix) has come and gone. If you value your truck, pay up for a quality filter. It's the cheapest insurance you can buy to protect your livelihood.
-
Mercedes-Benz - Trucks you can trust "Enjoy your ride" https://www.youtube.com/watch?v=A-uXJZbvuOQ
-
- 1
-
-
Press Release / May 26, 2015 Video: https://www.youtube.com/watch?v=t3lqxab8Afs Some need it all the time, others never and many every now and then. We are referring to all-wheel drive for construction vehicles. As a specialist among construction vehicles, the Mercedes-Benz Arocs is as individual as the requests of its customers. This applies to its numerous axle configurations, engines and cabs, but to its drive system as well: Mercedes-Benz offers the Arocs range without all-wheel drive for predominant use on the road and in mild terrain, with on-demand all-wheel drive for terrain of medium difficulty and with permanent all-wheel drive for heavy-duty off-road use. The Arocs with Hydraulic Auxiliary Drive (HAD) now rounds out the product line-up as another variant. HAD is an ingenious hydraulic auxiliary drive of the front wheels for occasional off-road use that is setting new standards in its segment: it is powerful, lighter than an all-wheel-drive model, easy to operate, maintenance-free and has a long service life. It lowers fuel consumption and consequently protects the environment as the result of low emissions. Construction vehicles: extremely broad application spectrum There are construction vehicles that rarely leave the pavement during their service life. Others plough through rough terrain day in, day out. For both specialists the question of what kind of drive system is best is quickly answered. But there is a third and especially common variant between on-road and off-road: construction vehicles that occasionally venture into terrain or that have to master a route with demanding terrain or steep ramps from time to time and therefore need an additional drive system. These are solo vehicles with tipper bodies, roll-on/roll-off tippers, tractor vehicles with trailer, tractor units with tipper semitrailer and sliding floor semitrailers, as well as tractor units with low-bed trailers for heavy-duty construction machines or construction vehicles in areas with heavy snowfall. The range of applications is very broad. There are classic construction vehicles carrying bulk materials. While payload is paramount for these vehicles, loading and unloading requires high traction. Roll-on/roll-off tippers require a traction aid when unloading on unpaved or slippery ground. Lumber transports have to navigate challenging routes in the forest, agricultural transports have to do the same in fields. Most of these trucks amass the majority of their kilometres on the road, but without outstanding traction they are unable to do their job. This is especially true when the truck is also used on the side for winter road maintenance during the cold months. And then there are the regions with heavy snowfall or areas with poor roads. For all these uses that require an all-round talent, the Mercedes-Benz Arocs HAD is the tailor-made vehicle. Hydraulic Auxiliary Drive: additional drive system at the push of a button The abbreviation HAD stands for Hydraulic Auxiliary Drive, an additional drive system. It is only used when needed and its technology is very different from a classic mechanical all-wheel-drive system with transfer case, drive shaft, differential and half shafts on a permanently or on-demand driven front axle. The advantages of the hydraulic drive are the comparatively low added weight, benefits in terms of fuel consumption and emissions, and great versatility in the configuration of the vehicle. In the case of Mercedes-Benz, these qualities are complemented by freedom from maintenance, low fuel consumption with activated hydrostatic drive and, above all, the combination with the Mercedes PowerShift 3 transmission. Hydraulic Auxiliary Drive from Mercedes-Benz is a proprietary development using components from Poclain, a globally leading manufacturer of hydraulic drive systems. The appropriate components were adapted and integrated into the vehicle. In particular the crucial control technology was created by Mercedes-Benz. Simple operation: a push of a button will do The operation of Hydraulic Auxiliary Drive is quite simple for the driver: all it takes is a push of a button in the cockpit and the auxiliary drive is active. This can be done while still on the road before entering the construction site or at any time in terrain. In this way, the driver is able to master even unforeseen situations with the Arocs HAD. The drive system offers extremely flexible use: the driver is able to engage differential locks independent of activating the Hydraulic Auxiliary Drive. This makes it possible to operate solely with the rear differential lock engaged and without auxiliary front-wheel drive as the situation allows. Wide range of variants with two and three axles Hydraulic Auxiliary Drive is available for the Arocs in a multitude of variants. First of all, for the axle configurations 4x2, 6x2 with trailing axle and 6x4, each equipped with air-sprung rear axles. Two engines, each with four closely staggered output levels, are available to choose from: the Mercedes-Benz OM 470 with a displacement of 10.7 litres and outputs from 240 kW (326 hp) to 315 kW (428 hp) and the OM 471 with a displacement of 12.8 litres and outputs from 310 kW (421 hp) to 375 kW (510 hp). The power is sent to the wheels in by fully automated Mercedes PowerShift 3 transmissions with 12 and 16 gears. With ClassicSpace cabs in three lengths, CompactSpace, StreamSpace and BigSpace cabs as well as cab widths of 2.3 and 2.5 metres, the line-up of cabs also leaves nothing to be desired. Hydraulic Auxiliary Drive is also available for the Actros and Antos in all these specifications. While there is less demand for all-wheel drive in the case of these model series, there is a call for a powerful additional drive system in certain types of operation, for example in heavy-duty distribution transport. Where an additional road sign to that effect exempts all-wheel-drive vehicles from snow chain laws, HAD eliminates the need for the time-consuming mounting of snow chains – for example, a case for distribution trucks with tyres of size 385/65 R 22.5 on demanding mountain roads. The sophisticated technology of the hydraulic drive The essential components of Hydraulic Auxiliary Drive comprise a high-pressure pump, a front axle with wheel hub motors, a side module and a valve block. The hydraulic components are interconnected by a system of hydraulic lines with different pressures. The high-pressure pump is the heart of HAD A powerful high-pressure pump is the heart of Hydraulic Auxiliary Drive. It is positioned in a central location on the engine and driven directly by its gear drive. The pump has an output of up to 112 kW and delivers a flow rate of up to 350 litres per minute at a maximum pump pressure of 450 bar. The front axle of the Arocs HAD is the familiar steel-sprung axle with disc brakes. From the outside, HAD can be identified by the modified wheel ends compared with a conventional drive system. The axle is available with two offsets, which are added automatically in dependence of the model series. For the integration of the wheel hub motor on the left and right, the stub axle and the wheel end were newly developed. Powerful radial multi-piston motors with ten cylinders The hydraulic wheel hub motors convert hydraulic pressure into mechanical work. They are radial multi-piston motors with centrally positioned power unit and ten cylinders arranged in a circle. Their pistons with rollers at the tip are alternatingly pressed outward against a cam ring by hydraulic pressure. The counterforce creates a torque that drives the front wheels. The wheel hub motors have an intake capacity of 934 cubic centimetres, a power output of 40 kW each and a peak torque of 6250 Nm per wheel. The wheel hub motors are supplied with hydraulic oil directly through the axle bolt and the axle journal. A rotary distributor in the axle stub protects the high-pressure hydraulic lines against twisting when steering. The system only has to compensate for the suspension motions and not for steering motions – a major plus in favour of a long service life. Hydraulic system generates a maximum pressure of 450 bar The hydraulic system consists of three circuits. The high-pressure system supplies the working pressure of up to 450 bar for driving the wheel hub motors in the front axle. The low-pressure system operates with a pressure of up to 30 bar and serves to control the system. It holds the pistons of the wheel hub motors in rest position when they're not needed. The low-pressure circuit is furthermore connected to a separate cooler. The third component is a non-pressurised leakage line that returns excess hydraulic fluid to the reservoir. All in all, 32 litres of oil circulate through the hydraulic system. Mercedes-Benz uses the synthetic transmission fluid familiar from its trucks. Its operating range from minus 40 to plus 90 degrees Celsius covers even extreme job conditions. When it is cold outside, a special HAD software routine automatically heats the oil to the required minimum system temperature of about 15 degrees Celsius when HAD is activated. This ensures a high level of system availability. A cooling module prevents excessively high temperatures. It is installed in a side module on the right side of the frame. The cooling module has a high cooling capacity of about 20 kW. It consists of an oil cooler and a fan in one unit mounted in an upright position, the hydraulic reservoir and an oil filter. The valve control block plays a crucial role. It is also housed in the side module below the frame and contains all valves required for controlling the hydraulic drive. It also transfers a constant amount of oil from the high-pressure circuit to the low-pressure circuit for cooling. The pressure sensors of the different circuits and a temperature sensor are also integrated into the valve control block. The cast steel design is weight-optimised. Compared with milled valve blocks, it offers weight savings of about 35 kilograms. Transmission control unit – the brain of HAD "The brain" of Hydraulic Auxiliary Drive is the control module with the transmission control unit (TCU). It controls the pump, the valve control block and the fan, ergo the entire drive system. A major advantage of the control system developed by Mercedes-Benz is that in dependence of the driving situation it only builds up as much torque on the front axle as is actually needed for traction. The basis for this control system is provided by the vehicle sensors. Among other things, the system knows how much slip there is, how heavy the vehicle is and the tilt angle of the truck. Compared with drive systems with simple on-off control, the fine control of Hydraulic Auxiliary Drive offers traction advantages because it only generates as much power as needed in every situation. At the same time, this strategy increases the service life of the drive technology and noticeably lowers fuel consumption and consequently also CO2 emissions. Driving made easy: drivetrain with Mercedes PowerShift 3 The trend towards automated transmissions has long since made it to construction transport as well: more than 90 percent of the construction vehicles from Mercedes-Benz are equipped with the fully automated Mercedes PowerShift 3 transmission (aka. Detroit DT12). It is part of the standard equipment of the current vehicle generation. Among the major advantages of Hydraulic Auxiliary Drive from Mercedes-Benz is therefore that, contrary to similar systems, the auxiliary drive is coupled with the fully automated Mercedes PowerShift 3 transmission. Especially in off-road operations this protects the major powertrain components from the engine and clutch to the transmission and the drive axles. In addition, drivers encounter their accustomed operating concept and can fully concentrate on the job of steering the truck through rough terrain. HAD also makes wear-free braking easier. Because the pump of the hydraulic system is driven by the engine PTO, vehicles with HAD can optionally be equipped with the equally powerful and lightweight secondary water retarder. The big plus is the torque-controlled drive system Contrary to comparable systems, Hydraulic Auxiliary Drive is controlled by torque. It always supplies precisely the right amount of torque that is needed. The corresponding request is controlled via the pressure on the accelerator. This makes spectacularly and pointlessly spinning wheels a thing of the past. Furthermore, HAD intervenes immediately, dependent on any potential slip of the rear wheels. In addition, the pressure in the system is increased automatically when starting. This ensures the necessary breakaway torque in rough terrain or on uphill grades. The auxiliary drive is available up to a speed of 25 km/h. At higher speeds, no additional drive system or traction boost is required. Activated Hydraulic Auxiliary Drive then goes into passive mode for this reason. Once the speed drops back below 25 km/h, HAD again automatically intervenes and ensures forward progress. This strategy also makes the driver's job easier. HAD is also active when reversing in gear one and two. Full tractive force even during gear changes To ensure maximum traction, the transmission will never skip any gears with activated HAD. Another advantage of HAD becomes apparent during gear changes: by driving HAD from the engine PTO, interruptions in tractive force are prevented during gear changes. The full tractive force is always available on the front axle. Once the truck travels faster than 60 km/h, HAD is automatically deactivated completely. This protects the major components and minimises fuel consumption and emissions. The auxiliary drive is also deactivated automatically after the ignition is switched off. This ensures that the truck isn't started unnecessarily with activated HAD the next day. The central display in the instrument panel keeps the driver always informed about the current status of the front-wheel drive: if the appropriate indicator shines white, Hydraulic Auxiliary Drive is activated but no torque is being commanded at the moment. If the indicator shines blue on the other hand, HAD is activated and boosts forward progress. The system status is also indicated by an LED in the switch. The high cooling capacity of 20 kW ensures continuous operation in terrain at speeds of up to 15 km/h. At higher speeds, only a small amount of torque is transmitted so that HAD is fully operational for about five minutes. As a result, virtually all conceivable operations of construction vehicles in mixed use are covered. Among the other strong points of the Arocs HAD is its great manoeuvrability. Contrary to a mechanical all-wheel-drive system, HAD does not limit the steering angle. It is identical to that of a truck with rear-wheel drive. The steering forces also are identical and due to the decoupled front-wheel drive no strain in the drivetrain is possible. If needed, drivers can additionally mount snow chains on the front wheels of a Mercedes-Benz truck with HAD. HAD: high traction, low fuel consumption As with all Mercedes-Benz Arocs trucks, the Arocs with Hydraulic Auxiliary Drive also benefits from its perfectly calibrated and highly efficient powertrain from a single source. And there is an added two-fold advantage: firstly, the on-demand additional drive system increases fuel consumption in standard operations only minimally. Secondly, the system developed by Mercedes-Benz offers another important specific benefit: the auxiliary drive operates in controlled mode. Contrary to comparable drive systems, the fuel consumption is only increased by the amount of power the driver requests. The sample calculation for an Arocs 1843 LS – it is popular in construction site operations pulling a tipper semitrailer – looks as follows: on the road without activated auxiliary drive, fuel consumption with Hydraulic Auxiliary Drive is only 1.5 percent higher than that of a rear-wheel-drive truck with identical transmission and hypoid axles – while offering enormous traction reserves at the same time. The basis for the calculation is a typical application profile with a large percentage of country roads and less use on the motorway and in the city. Customers opting for a heavy-duty model of the Arocs HAD with hub reduction axles and overdrive transmission will see an increase in fuel consumption of about two percent under the same conditions over a base vehicle with HAD and driven hypoid rear axle. In contrast, with a conventional on-demand all-wheel-drive system, fuel consumption increases by up to eight percent and by up to ten percent with permanent all-wheel drive over HAD and a hypoid rear axle. That not only saves money, but also results in a better CO2 balance. Added weight less than half of permanent all-wheel drive The bottom line when it comes to the weight of the Arocs with Hydraulic Auxiliary Drive also deserves special attention. It offers a much higher payload than a classic all-wheel-drive system. The added weight of HAD is just 400 kilograms. The on-demand all-wheel-drive system of the two-axle Arocs weighs twice that much (an additional 425 kg), while permanent all-wheel drive even weighs in at an additional 575 kilograms – the transfer case, differential, drive shaft, the thicker frame and other features of a conventional all-wheel-drive system are no featherweights. Sophisticated maintenance-free technology saves time and money Practical people in the construction industry keep an eye on maintenance and repair expenses as well. The Arocs with Hydraulic Auxiliary Drive impresses in this respect too: its drive system is entirely maintenance-free. There are no downtimes or costs. Hydraulic Auxiliary Drive is designed for the vehicle's service life Buyers of an Arocs HAD can rely on a solid drive technology: in typical mixed operations as a construction vehicle on the road and in terrain, Hydraulic Auxiliary Drive is designed to last for the service life of the vehicle. This statement has recently been proven realistic for construction vehicles during testing of the Arocs Hydraulic Auxiliary Drive. Mercedes-Benz has tested the technology extensively in real life on the basis of a wide range of different testing scenarios and application profiles. From trials along the Arctic Circle and customer field tests in rock quarries and underground to the tough test tracks in Wörth, the vehicle was put through its paces extensively during its development. The Arocs Hydraulic Auxiliary Drive offers crucial advantages even in extreme situations. Should the typically rough use in terrain cause damage to the high-pressure circuit of the hydraulic system, the Arocs HAD unlike others will keep going: the valve control block immediately cuts off the oil supply to the damaged line, dials the high-pressure pump back to zero flow and consequently prevents a total loss of oil. In addition, the driver is warned of the damage by a message in the instrument panel and an audible warning signal. Neither the wheel hub motors nor the high-pressure pump can run dry. As a result, the still operational conventional rear-wheel drive ensures continuing on to the nearest workshop. Related reading: http://www.bigmacktrucks.com/index.php?/topic/39998-volvo-unveils-automatic-all-wheel-drive-truck-tech/?hl=hydraulic#entry289755
-
http://translate.google.com/translate?hl=en&sl=ru&u=http://trucks.autoreview.ru/_archive/section/detail.php%3FELEMENT_ID%3D146938%26SECTION_ID%3D8087&prev=search http://trucks.autoreview.ru/_archive/section/detail.php?ELEMENT_ID=146938&SECTION_ID=8087
-
Fortune / May 26, 2015 Swift Transportation, one of the nation’s largest freight trucking companies, this month began equipping its trucks with Lytx DriveCam systems (http://www.lytx.com/) including both a front-facing and driver-facing camera. Though it’s not the first truck operator to install driver cams, Swift is by far the largest to date, and pressures on the industry point towards broader adoption. In addition to their human cost, the financial costs of crashes for carriers are substantial. In a 2012 report, the FMCSA estimated the average cost of an injury crash at $195,258, and of a fatal crash at over $3.5 million. Recent years have seen over 4,000 truck accident fatalities in the U.S. annually, and settlements to victims routinely exceed carriers’ federally-mandated $750,000 per-incident insurance coverage. 2014’s largest truck accident settlement was for over $34 million. But driver-facing cameras could help reduce the number of accidents that happen in the first place. Truck drivers, of course, are used to being alone in their cabs. However, observation—even the illusion of observation—can yield dramatic improvements in people’s behavior. A 2011 study by researchers at Newcastle University showed that just hanging posters depicting observant eyes in public spaces reduced undesirable behavior by as much as 50%. Truckers, however, have taken to industry forums to express outrage over the driver-facing cameras, saying that they represent both excessive oversight and an invasion of privacy. Swift seemed to anticipate resistance, and in April issued an internal video urging drivers to withhold judgment. Land Line reported that in the video, Swift President and COO Richard Stocking reassured drivers that “we are not watching the driver; we are watching out for the driver.” Though fatal truck crashes per mile traveled declined by 77% between 1975 and 2009, the Federal Motor Carrier Safety Administration has shown them rising again recently—by 3 percent per mile per traveled between 2011 and 2012. But the U.S. Federal Highway Administration concluded in a 2004 study that in car-truck collisions, the car driver was solely responsible for the accident 70 percent of the time. Though front-facing cameras are already common on freight trucks, evidence from driver cams may go further to limit drivers and carriers’ liability in fatal crashes. Driver resistance represents a risk for Swift. The trucking industry is experiencing a mounting labor shortage, and drivers’ responses to the new program so far indicate it may be an obstacle to hiring. But the risk of alienating drivers may be outweighed by the benefits of the cameras, which early indications show will both reduce accidents and limit carriers’ financial liability when they occur. Swift operates over 18,000 trucks, but cameras will be installed, at least at first, only in the more than 6,000 trucks owned directly by the company. Swift insists that truck feeds will not be monitored live, saying that the Lytx system will only archive footage for the ten-second window on either side of a swerve, hard brake, or other unusual event. Video will then be uploaded wirelessly to a database for analysis, first by Lytx, then, if an event is deemed significant, by Swift. But drivers remain skeptical. “Having a driver-cam recording what a driver does would be the same as installing cameras in all the Swift executives’ homes,” observed driver Nancy L. Nyman in a comment on the Land Line website. “A truck is our home, so they should treat it like one.” Most long-haul truckers sleep, eat, and even shower in their cabs, and thousands of comments on Facebook and trucking forums reflected similar privacy concerns. But the benefits of driver-facing cameras have been borne out by smaller operators with driver-cam programs. As reported by the Commercial Carrier Journal, the northeastern food distributor Bozzuto’s experienced a 22 percent drop in accidents and a dramatic improvement in safety metrics in its first two years with driver cams installed. Other large carriers have already explored the possibilities of driver-facing cameras, with CR England running a pilot program in 2013. With Swift leading the way to full-scale implementation, its competitors may not be far behind.
-
Dart Network offers Kenworth T680s in lease-to-own program
kscarbel2 posted a topic in Trucking News
Fleet Owner / June 1, 2015 Phil Marston, vice president of Highway Sales, a truck finance vendor to Dart Transit Company and the Dart Network, was expecting the Kenworth T680 to be a popular truck in Highway Sales’ lease-to-own program for Dart owner-operators. But he had no idea how popular. “I was blown away,” he said. “We have a waiting list – drivers are lining up to get the T680. I’ve been here for 21 years administering the program and I can’t remember this much demand for a truck. It’s been unbelievable.” According to Marston, Highway Sales – working with Dart and its nearly 2,000 drivers, more than 1,300 of which are owner-operators – purchased 150 Kenworth T680s through Rihm Kenworth in St. Paul, Minn. The first T680 with 76-inch sleeper went to Vincent Sykes, who has been driving a truck for 32 years, the last 11 contracted to Dart. “When I heard they were putting Kenworth T680s into the program, I told Phil that I wanted to be the first to get the truck,” Sykes said. “I’ve had several trucks through Dart and it’s been a great program for me. I can’t tell you how nice this Kenworth drives. Plus, the fuel economy I’m now getting is so much better. It’s made the decision a perfect one.” Highway Sales reviews trucks on an annual basis, then decides which to offer in the lease-to-own program. Don Oren, chairman of Dart, is directly involved in that process. “We get input from a variety of people in our organization – as well as drivers,” Oren said. “Our company is all about the driver and I was convinced that the Kenworth T680 would be a popular truck – and that’s certainly happened. The T680’s driver comfort aspect is a step above what we had before. It’s just a beautiful truck. It maintains Kenworth’s image and combines the latest in aerodynamics. That’s saying a lot – drivers want that image.” “It truly is a premium truck and with the driver shortage and difficulty in recruiting drivers, we wanted to offer up a truck that would make them take a closer look at Dart,” added Marston. “And, it certainly has – half of those who have signed up for the T680 in our program are brand new to Dart. We’re finding ourselves in a good position. Drivers want to work with Dart and they want the T680.” Equipped with the PACCAR MX-13 engine rated at 430-hp and driven through the Eaton Fuller Advantage 10-speed manual transmission, Marston said Highway Sales spec’d the T680s to be fuel-efficient and lightweight. “We want the drivers to be successful. If they’re successful, then we’re successful,” he said. “Maximizing fuel efficiency is a big way to improve their numbers. The T680 can get them the fuel economy they’re after. Dart also has a fuel program where the owner-operators can save by using Dart’s network.” “Fuel is important,” echoed Sykes. “I’m getting over 8 mpg with the T680 and that’s a big jump from the mid- to high 6s I was getting with my previous truck. I drive hard and put on more than 13,000 miles a month, so that savings really adds up.” Driver comfort has been a big upside for Sykes as well. “There is plenty of room and storage and the comfort is critical to getting a good night’s sleep,” he said. “My wife and grandkids sometimes join me on trips, but I sleep in this truck every night I’m out – and I’ll be gone for a month to six weeks before getting home,” he said. Sykes said there is a litany of improvements since the last time he drove a Kenworth. “The PACCAR MX-13 engine is very quiet and has enough power to easily handle the line-haul I work – from Texas to New Mexico. And the T680 has the new clutch (hydraulic assist) system, which makes shifting gears so effortless. The doors shut so easily – no effort at all, and the windshield is so much bigger. The visibility is just great and there’s more room between the seats, which makes it easy to get back into the sleeper. There is just so much new on this truck. I get a lot of other Dart drivers who want a tour of the truck. They like it too.” Marston said they’ll continue to gauge driver reaction to the Kenworth T680. “We couldn’t be happier with how our lease-to-own program has been going since we began operation 31 years ago. I think a testament to our success is how we work closely with drivers in this program. More than half of those drivers are on their second, third or more trucks with us. It’s a program that works.” -
Fleet Owner / June 1, 2015 From the spotless floor of its North Texas assembly facility to evaluating multiple designs for a part as seemingly routine as a hood latch, members of the Peterbilt team were emphatic: To be a premium brand—to back up the “Class Pays” tagline that accompanies the iconic red oval—means every detail counts. That’s the takeaway from a visit to Denton last week where trucking journalists were treated to an inside look at the development of a Peterbilt truck from the drawing board to prototyping to production to the customer. As Design Manager Phil Hall explained in a visit to the Engineering Lab, the four key stages in his shop are “discover, design, develop, deliver.” And the key is the “qualitative research” that goes into the product. But he’s not talking about the latest fluid-dynamics calculations; he’s talking about the truck driver. “We really want to understand our drivers, all the way down to what they do every day, how they feel about their trucks, their emotions, to what their dreams and aspirations are,” Hall said. “When we get that kind of information, we develop insights from it.” He shows a display of a dozen sketches of the early ideas for the Model 579 (sorry, photos were not allowed in the studio or in the plant) and explains that these are just a representative sample of the “wall full” of ideas—“hundreds and possibly thousands of sketches”—that the design team generates in trying to capture that feel the driver wants. Designers also make the rounds of the engineering and manufacturing departments and conduct customer reviews as the designs are narrowed and evaluated. “That’s our job as designers: It’s not just creating a product, a vehicle that goes down the road—but creating a vehicle that makes that connection with the driver,” Hall said. Indeed, Peterbilt was the only truck manufacturer with an entry in the Los Angeles Auto Show Design Challenge last fall, themed “Sensing the Future: How will vehicles interact with us in 2029?” Peterbilt’s vision is one in which vehicles will operate together in “truly symbiotic relationships,” and truck drivers will become “highway pilots” and will lead groups of vehicles, taking responsibility for passengers as well as cargo. The SymbiotUX concept explores this human-machine interface, as Hall explains. (A gallery of a mind-blowing look at the future of the road, and a detailed explanation of how the concept makes sense, is here.) “Imagine what a steering wheel will look like 20 years from now. Will it even exist?” he says. “There are no restrictions on these advanced concepts.” The point isn’t to just play around with wild ideas, however—it’s to be ready for the future, and to help set the course. Meanwhile, back in the present, Hall advances the Model 579 design from sketches and CAD images to the clay model phase, which provides a much better look at the real world shape, the vehicle’s contours and shadows. And any resulting changes in the shape are the captured by a special camera system and fed back as new 3D data. Similarly, scale models are used to test paint colors on the final design; again, providing a real-world view in various lighting conditions. Also impressive, perhaps even most impressive, is the design team’s focus on anything and everything that a driver might see or touch or hear. Hall displayed various iterations the Model 579 EPIC badge, as produced on one of the facility’s 3D printers. He then showed different versions of a simple black hood latch, to better assess whether the part should be logoed or not. Also on hand was a thick binder filled with various fabric swatches the team used to select interior options, again all part of what gives a truck a Peterbilt personality. “The truck has to be functional, but it has to be beautiful as well,” Hall said. While the Engineering Lab excites the imagination, the real work at the Denton facility was next door at the 450,000 square-foot assembly building. Surprisingly bright, quiet, and climate controlled, 81 trucks roll off the line in each of two shifts. That’s up from just 15 trucks a shift in the not too distant past, as tour host Salty Rose explained. Much of that increase in productivity comes from an increased use of robotics but, Rose said, workers aren’t replaced. Instead, they shift to duties where a human touch is essential. Indeed, on the plant walk-around, Rose routinely calls out the names of workers and their duties. He knows how many years most have worked there, and he even knows the employee numbers of a couple. Rose also emphasized the importance of the facility to North Texas, not only as a source of good jobs but as a community leader. Clearly, the assembly floor is where the workforce gives the company’s trucks their original coat of Peterbilt “pride.”
-
Owner/Driver / May 21, 2015 Video - Return of International http://www.ownerdriver.com.au/events-news/1505/bts-15-return-of-international/
-
Ford Truck targets Middle East bound long-distance fleets
kscarbel2 replied to kscarbel2's topic in Trucking News
Here is a proud looking Mk 2 Trancontinental, again with the double-skinned roof (aka. roof heat shield) for Middle Eastern travel. The revised Mk 2s had the Cummins Big Cam Formula E (NTE) engines. . -
The New York Times / May 30, 2015 Inside the National Vehicle and Fuel Emissions Laboratory (http://www.epa.gov/nvfel/) here, a mammoth contraption, with steel rollers, advanced electronics and exhaust tubes, is nearing completion. The project — an enormous “truck treadmill” — is the new centerpiece of the Environmental Protection Agency’s complex. One of the largest vehicle testing centers in the world, the truck lab will play a crucial role in shaping and enforcing a major new environmental mandate by the Obama administration that could dramatically transform America’s trucking industry. This week, the EPA is expected to propose regulations to cut greenhouse gas emissions from heavy-duty trucks, requiring that their fuel economy increase up to 40 percent by 2027, compared with levels in 2010, according to people briefed on the proposal. A tractor-trailer now averages five to six miles a gallon of diesel. The new regulations would seek to raise that average to as much as nine miles a gallon. A truck’s emissions can vary greatly, depending on how much it is carrying. The hotly debated rules, which cover almost any truck larger than a standard pickup, are the latest in a stack of sweeping climate change policy measures on which President Obama hopes to build his environmental legacy. Already, his administration has proposed rules to cut emissions from power plants and has imposed significantly higher fuel efficiency standards on passenger vehicles. The truck proposals could cut millions of tons of carbon dioxide pollution while saving millions of barrels of oil. Trucks now account for a quarter of all greenhouse gas emissions from vehicles in the United States, even though they make up only 4 percent of traffic, the E.P.A. says. But the rules will also impose significant burdens on America’s trucking industry — the beating heart of the nation’s economy, hauling food, raw goods and other freight across the country. It is expected that the new rules will add $12,000 to $14,000 to the manufacturing cost of a new tractor-trailer, although E.P.A. studies estimate that cost will be recouped after 18 months by fuel savings. Environmental advocates say that without regulation, the contribution of American trucks to global warming will soar. “Trucking is set to be a bad actor if we don’t do something now,” Jason Mathers, head of the Green Freight program at the Environmental Defense Fund. But some in the trucking industry are wary. “I’ll put it this way: We told them what we can do, but they haven’t told us what they plan to do,” said Tony Greszler, vice president for government relations for Volvo Group North America, one of the largest manufacturers of big trucks. “We have concerns with how this will play out.” The E.P.A., along with the National Highway Traffic Safety Administration, began its initial phase of big truck fuel economy regulation in 2011, and those efforts have been widely seen within the industry as successful. But meeting the initial standards, like using more efficient tires, was not especially difficult by comparison. The proposed rules will ask much more of the industry. They will require more investment and innovation, like tweaking engines and transmissions, improving aerodynamics and using lighter materials. More disruptive options, like recycling engine heat to drive a secondary turbine, or moving away from diesel itself, are also under consideration. Already, some bigger fleets like that of the United Parcel Service have started outfitting some of their trucks with natural gas. To win over industry players, regulators say they have made efforts to engage companies up and down the supply chain. They have held hundreds of meetings and have tried to shape their proposal in a way that would help truck-related businesses. “Fuel is either at the top or near the top of truck operators’ costs,” said Christopher Grundler, director of the E.P.A.’s Office of Transportation and Air Quality. Reducing those costs, he added, was good for business and the environment. Mr. Obama led the cheerleading for his truck rules. In a speech last year signaling the rules, he said, “Because they haul about 70 percent of all domestic freight — 70 percent of the stuff we use, everything from flat-screen TVs to diapers to produce to you name it — every mile that we gain in fuel efficiency is worth thousands of dollars of savings every year.” John C. Wall, chief technical officer at Cummins, a leading manufacturer of truck engines, said his company had “tried to engage proactively in the development of the regulations” and had found federal officials to be open-minded about what the company thought could be achieved. Others in the industry, though, hold a different view. John Yandell Jr., president of Yandell Truckaway in Pleasant Hill, Calif., said that fuel is the second-highest cost for his family business and that he would love to get better mileage on his fleet, which operates short-haul regional routes. But, he said, he is skeptical that can be achieved in the near future in a way that is affordable for him, if at all. “Twenty years ago, my trucks were getting five miles per gallon; today they are getting around 6.2 to 6.4,” he said, but getting up to nine or 10 seemed like a pipe dream. “Talk is cheap, but I don’t see how they get there.” Getting there, however, is a priority for Mr. Obama. The administration also hopes that ambitious government targets can help drive the innovation needed to achieve them. After the 54.5 m.p.g. requirement for cars and light trucks was announced in 2009, a wave of new research and development happened in Detroit, as automakers rushed to develop new hybrid, electric and super-efficient gasoline engines. The new truck rules are intended to spur the same rush to innovation among the companies that build the 10-ton tractor-trailers that haul things as varied as timber, steel and frozen fish. But as with any new environmental rules, the details are complicated and will take time to sort out. The public will be asked to comment on the proposed rules before the final version is put in place sometime next year. Back at the testing lab, the truck treadmill was put through its paces. A semi truck was fastened down with thick chains secured to even thicker steel anchors. A driver started the engine, which roared as the truck sat atop enormous metal rollers that allowed the wheels to spin in place. Orange tubes, intended to collect the exhaust fumes when the formal testing begins, hung from the ceiling. “This was a hole in the ground before Christmas,” said David Haugen, director of the E.P.A. lab’s testing and advanced technology division. “Now we’re ready to make history.”
-
Australasian Transport News / June 1, 2015 New Zealand trucking corporation Mainfreight (http://www.mainfreight.com/global/en/global-home.aspx) has reported a record NZ$2.05 billion ($A1.9 billion) in revenues across its global operations. That fed into an earnings before interest, tax, dividends, and amortisation (underlying earnings) result of NZ$162.2 million (A$151 million). At home, the company saw increases in revenues and profits across both its transport and logistics divisions. Group managing director Don Braid says those gains were similar to the achievements built in the previous financial year. "Our New Zealand transport operations gained a number of new customers, and increased the number of consignments transported through our network by 150,000," his report to shareholders states. "This builds on similar levels of growth in the year prior." Across the Tasman, a shaky economy and competitive market subdued Mainfreight’s ambitions in Australia for the financial year that ended on March 31. Revenues increased by seven per cent to A$490.65 million, while underlying earnings improved 5.8 per cent to A$37.2 4 million. "Whilst these improvements may seem satisfactory, when compared to New Zealand’s level of growth and the relative size of the Australian market, we would have expected more," the commentary explains. While profitable, Mainfreight’s US operations also filed below-expectation results. The smaller European business achieved strong growth off a relatively low base. Total sales for the region rose by 3.6 per cent over the year to March 31, with underlying earnings up 33.5 per cent to €11.91 million (A$17 million). "Whilst the European economy remains turbulent, our own improved performance is providing confidence for the future." In Asia, Mainfreight had underlying earnings of US$4.99 million (A$6.5 million), up 41.6 per cent from what was also a low base. Braid says the forward outlook also remains positive. "A number of large multinationals can now be counted as loyal customers, and we are underway with attracting more," he says. "Their relative logistics spend is considerably larger than we have experienced before in the smaller markets of New Zealand and Australia [and] the potential [they] bring to our global business is exciting." .
-
Owner-Driver / May 29, 2015 A growing number of the trucking industry’s customers are trying to force operators to accept 120-day payment terms, the managing director of FBT Transwest says. Cameron Dunn told a recent road safety summit that 120-day terms are now a common feature in contracts put out to tender. This comes despite efforts by the Road Safety Remuneration Tribunal (RSRT) to improve the situation. It last year mandated 30-day payments for sub-contractors and owner-drivers. "It is more common now that contracts will come out that’ll push for 120 days," Dunn, whose business is involved in dangerous goods, says. "I’ve mentioned it to some people and they are aghast. Well that’s actually quite factual and more and more, as day goes by, end companies are pushing us out." Dunn says companies are employing logistics experts during the contract tendering process and ordering them to reduce transport costs — a move that has led Dunn to refuse work to avoid agreeing to harsh terms and conditions. "I won’t be pushed to not do the right thing," he says. Dunn’s comments caught the attention of federal Labor senator Glenn Sterle, who attended the summit which was organised by the Transport Workers Union (TWU). Sterle raised concerns about payment terms and says he knows of a large food manufacturer attempting to institute 90-day payments. "This is a monster and all this will do is crush competition and it will squeeze the living daylights out of a lot of operators," he says. While small-time trucking operators with limited cashflow stand to suffer from lengthy payment terms, Dunn says large transport firms are agreeing to 120 days. "Now why do you think the larger companies are saying yes? They’re saying yes because they’ve got the ability to be able to cover that cashflow with their other contracts," he says. "They have some of their contracts at 120 [days], some at 14, some at seven. But they also then push out payments to their suppliers, so it’s ever revolving. They’ll push the tyre supplier out, possibly, to 120 days. "It’s happening. It’s more and more. It’s certainly out there and its scary, it’s very, very scary." Dunn also touched on the addition of key performance indicators (KPIs) in contracts and the effect they are having on freight rates. He says contracts generally include KPIs relating to the environment, safety and tonnage and that if a trucking company does not meet them then the customer has the ability to reduce payments. "There are some contracts when you actually read them, you can actually start off carting for $1 a tonne and and up after two years at 80 cents because you failed to meet the different KPIs. And they are out there. That’s no bullshit, it’s happening." Dunn was a feature participant at the road safety summit, which was held in conjunction with the TWU’s National Council earlier this month. The day-long event discussed road transport safety and included representatives from Victoria Police, the RSRT, the Roads and Maritime Services (RMS) and Toll.
-
Peterbilt’s Model 579 EPIQ opening doors with large fleets
kscarbel2 posted a topic in Trucking News
Truck News / May 29, 2015 Peterbilt is feeling pretty good about its position in the marketplace – especially among large fleets – thanks to the success of its Model 579. And now with the addition of the EPIQ package, the company says it has never been better positioned to sell to large fleets in the US and Canada. Three quarters of the trucks Peterbilt builds are now aerodynamic models. “It has opened a whole new customer base for us,” Robert Woodall, assistant general manager, sales and marketing with Peterbilt, said during a press briefing at the company’s Denton truck plant. Woodall said the EPIQ package improves fuel economy over a base Model 579 by 4% and contends it’s the most advanced, fuel-efficient truck on the road. It’s certainly the most fuel-efficient truck ever produced by Peterbilt. Woodall said the EPIQ package is just now entering production and already fleets are making the transition, despite an upcharge he said is quickly recovered through fuel savings. “Most of the interest in EPIQ is going to be the big fleet guys, those guys who are all about fuel economy,” Woodall said. “That’s where EPIQ is playing out.” The EPIQ package consists of: a more complete aerodynamic fairing package; the Paccar MX-13 engine integrated with the Fuller Advantage Series automated manual transmission; a single horizontal exhaust; the SmarTire tire pressure monitoring system; low rolling resistance tires; and optimized software. New additions to the package include GPS-based predictive cruise technology to ensure engine and transmission are being optimally operated and neutral coast, which disengages the transmission while travelling downhill to save fuel. Also new is a Driver Performance Assistant, which coaches drivers on fuel-efficient driving techniques. The 579 EPIQ can also be ordered with the Cummins-Eaton SmartAdvantage. However, both the SmartAdvantage and the Paccar/Eaton pairing (dubbed APEX) are limited to a GCWR of 80,000 lbs, meaning this package won’t fit all Canadian needs. For the Canadian customers, a 16-speed Eaton UltraShift Plus LSE will be available, rated at up to 110,000 lbs, but they won’t be calling that an EPIQ, even when all the other aspects of the package are spec’d. It might be EPIQ, but it’ll still be a fuel-efficient option for fleets seeking the versatility to haul heavier Canadian payloads. Fleets running north-south with US-legal loads on the other hand, may be well served by the true EPIQ, straight out of the box. The Model 579 itself is the result of an exhaustive design process. Andrew Weiblen, director of product planning with Peterbilt, said the development process began by reaching out to customers to find out what they wanted in a truck. They visited truck stops with a mobile, adjustable cab and surveyed drivers on the ideal configuration. Most preferred a 2.1-metre cab width, which was adopted for the 579. “A 2.1-metre cab is the perfect width to give drivers ample space, without making them feel like they’re driving an RV down the road,” Weiblen said. Determining the market needs was the first in a five-step design process. Next came: ideation; concept; validation; and final design. As part of the ideation process, designers studied how customers use the truck. When they noted some were placing their cell phones in the cupholder, a special phone-sized storage slot was developed. The concept stage included the building of prototypes. Clay models were built in 20%, 40% and full-sized scale. Next, as part of the validation process, full-sized functioning prototypes were built and rollover and frontal impact testing was conducted. Peterbilt wanted to ensure the truck would last a million miles or more. The 579 is the foundation from which all other models – including vocational and severe-service trucks – are built, so it had to be constructed tougher than required for the on-highway linehaul applications it was intended for. Finally, in 2012, came production. The arrival of the 579 also necessitated a redesign of the production plant. About 55,000 sq.-ft. of floor space had to be reconfigured to accommodate the new production flow. A new robotic chassis paint system was installed as well as a non-contact laser alignment system, which Peterbilt said is the only one of its kind among truck manufacturers. The company is particularly proud of this piece of equipment. It ensures trucks are delivered to dealers and customers in alignment and reduces the need for fleets to align new trucks when they’ve arrived. The Model 579 drew inspiration from the Peterbilt/Cummins SuperTruck project. The chassis fairings and predictive cruise technology are a couple of the 579’s features that were first developed as part of the SuperTruck. Peterbilt 579 EPIQ Road Test: http://www.trucknews.com/test-drive/driving-peterbilt-model-579-epiq-2/ -
Commercial Carrier Journal (CCJ) / May 31, 2015 In April 2011, on-highway diesel broke the $4-per-gallon mark for the first time since the recession, double the low of $2-per-gallon just two years earlier. Fleet managers, still reeling from the effects of the economic downturn, were scrambling for answers. By 2012, there was no bigger buzzword in trucking than natural gas. Whether it was compressed natural gas or liquefied natural gas, OEMs and engine makers were ramping up for what was expected to be a game-changer for trucking efficiency. By that time, diesel had stabilized at about $4 per gallon, and no one thought it would drop soon. A handful of carriers were quick to react, converting some or most of their fleet equipment to more expensive natural gas-powered tractors to take advantage of the fuel’s comparatively low cost. Many other carriers followed suit, dipping their toes in the water and getting positive results, just as the fueling infrastructure was unfolding. Other carriers were pressured into natural gas adoption by customers with aggressive environmental sustainability initiatives such as Owens Corning and Procter & Gamble. By December 2013, Class 8 natural gas truck sales had risen from nowhere to account for 3.2 percent of the total U.S. and Canadian Class 8 truck market, according to FTR, an industry analyst firm that tracks equipment and freight trends. Some were calling for the natural gas truck market to skyrocket at that time, with Thomas O’Brien, TravelCenters of America president and chief executive officer, suggesting that one in four heavy trucks on the road in 2020 would be powered by natural gas. The diesel dip Over the next year and a half, diesel plummeted $1.25 per gallon, hitting a low of $2.75 in April of this year, according to the U.S. Energy Information Administration’s weekly retail price index. Lower diesel costs, coupled with strides made by OEMs and engine makers to improve the fuel economy of traditional diesel-powered trucks and engines, have combined to stymie the natural gas market. “We are seeing a leveling off in activity,” said Eric Starks, FTR president. “Demand for natural gas equipment is not growing, nor is it dropping. The trucking industry has been hoping for growth in this sector, and it clearly has stalled out and is not expected to make significant strides until the price of diesel fuel rises again.” Given the inherent volatility in diesel prices, it is unlikely the low-cost fuel will remain at current levels for a long period of time. T. Boone Pickens, speaking at ACT Expo in Dallas last month, said as U.S. producers throttle back production, he expects oil prices to recover to upwards of $70 per barrel by the end of this year and approach $90 per barrel by the end of 2016. “Since 1980, I’ve seen six of these collapses of half the price of oil, and I promise you it will be back up again,” he said, adding that U.S. producers, who at their peak had more than 1,600 rigs drilling for oil, are responsible for the decline in oil prices. But rig counts have been cut by more than half as prices fell. “We’re the one who oversupplied the market and caused it to drop $50 per barrel,” said Pickens, who then compared the volatility of natural gas and diesel markets. “If natural gas doubled to $6, it would increase your fuel cost 37 cents per gallon,” he said. “$100 oil in parity with natural gas is $16, and I’ve never seen that. I’ve said that in my lifetime, I don’t think I’ll ever see $10 natural gas again, but I do think we may see $8. But I think you’re looking at $100-plus oil forever.” Navigating today’s challenges The natural gas truck market has faced other headwinds during the last year and a half in addition to lower diesel prices. The added costs of natural gas-powered vs. diesel-powered tractors – between $40,000 and $60,000 depending on tank configuration – have been slow to come down. An uncertain future in the used truck market has many fleets sitting on the fence before investing in natural gas equipment. And while many regional and dedicated carriers have had great success with natural gas operations, the fueling infrastructure still is being built out, and many over-the-road carriers remain hesitant to test the waters. The natural gas truck market took another hit last month when the journal Environmental Science & Technology published the results of a study coauthored by the Environmental Defense Fund that claims methane emissions from the natural gas manufacturing process and supply chain could lead to greater global warming than carbon dioxide emissions from diesel-powered trucks. According to EDF, methane – the main component of natural gas – has 84 times the warming power of carbon dioxide over a 20-year timeframe. “Natural gas trucks have the potential to reduce overall climate impacts compared to diesel, but only if we clean up the highly potent greenhouse gas emissions from the systems that produce and deliver the fuel,” said Jonathan Camuzeaux, EDF senior economy analyst. “Otherwise the net warming effect is actually a negative one for 50 to 90 years after the fuel is burned.” Natural Gas Vehicles for America, a developer for market acceptance of natural gas vehicles, was quick to respond. “This study clearly demonstrates that there is a role for natural gas in addressing climate change,” said Matthew Godlewski, president of NGVAmerica. “We welcome all credible insight into paths for improving emissions, yet it’s confusing that the Environmental Defense Fund has chosen to conduct and release another study, outside of the cooperative work already underway.”
-
Heavy Duty Trucking / May 28, 2015 Two decades ago, Peterbilt was primarily known for its classic truck designs that appealed to owner-operators and small fleets. But as it showed reporters during its Technology Showcase Thursday at its plant in Denton, Texas, it has reinvented itself as a company on top of the latest technology and fuel economy. About 10 years ago, the Model 386 was Peterbilt's first ground up design of an aero product, said Robert Woodall, assistant GM, sales and marketing. "In 2013 we introduced the Model 579, helping redefine our company," he said. Of course, the company still has a tried and true offering for customers who prefer that traditional look, with the Model 389. With the Model 579 Epiq, Peterbilt took the truck to an even greater level of fuel efficiency, Woodall said, noting later that it "has opened a whole new customer for us. We're the most competitive we've ever been with the big on-highway fleet business." Large fleets already buying the Epiq include Walmart, Love's, TMC, Freymiller and Celadon. On top of that, he said, "we've got a new 58-inch [sleeper] box coming out in November for regional hauls, so that's going to open up another group of customers." Many of the technologies used on that truck came through the Cummins-Peterbilt SuperTruck project, a joint effort with the EPA to demonstrate freight efficiency possibilities. Some of the aerodynamic fairings were adapted from the SuperTruck and actually tweaked to offer the same performance with easier maintainability, explained Chief Engineer Scott Newhouse. New Predictive Cruise technology, which will be available on the Model 579 and 567 this summer, also made its debut on the SuperTruck. It uses GPS data to ensure the engine and transmission are operating in the most efficient mode, working in tandem with neutral coast technology that allows trucks to coast downhills at idle. Under the hood, he said, Peterbilt's work on integrating the engine and transmission on the Super Truck taught them things they were able to apply to the new Apex package. "Also not directly related, we learned things such as driver impact, which really led into a lot of the Driver Performance Assistant technology," he said. "You have to be able to manage the impact the driver may have on fuel efficiency." Woodall noted that just as important as new high-tech products is the growth of high-tech systems and tools to support those products once vehicles are in operation. New vehicle technology such as the 579 Epiq, the Apex powertrain and the Driver Performance Assistant are complemented by back-end and diagnostic tools such as in-cab diagnostics that alerts drivers whether fault codes need immediate attention or not, as well as SmartLinq remote diagnostics. The technology extends to the plant itself, which has higher levels of automation and robotics than ever before, according to Ron Augustyn, manager of the Denton plant. The plant's undergoing an expansion that will add a new high-tech parts storage and retrieval system in addition to more docks. "The launch of the 579 and 567 was the most significant product launch in our history," he said, and the plant underwent a major transformation in order to produce the trucks, completely rearranging 55,000 square feet of floor space. Part of that transformation is an automated cab build station, a critical element in the overall build quality of the product, he said. Another significant investment was a non-contacting laser alignment system. Augustyn said this is the first truck plant in North America to use this state of the art technology, which uses a drive through laser scanning system that integrates steering wheel alignment as well. The system, he said, has improved accuracy 10-fold and efficiency by 40%. "Total truck alignment has been a challenge for the entire industry," he said, noting the accuracy of this system can provide improved fuel efficiency and reduced tire wear for customers. And looking to the future, Peterbilt is continuing to work on development of technologies that could move to autonomous vehicles. It has worked with Walmart to design a working autonomous truck that it will show to reporters Friday. "We're always looking ahead to new opportunities," said Newhouse. Autonomous technologies such as lane keeping, GPS navigation and platooning "are all technologies we continue to advance." Looking even further out, Newhouse highlighted Peterbilt's entry in the LA Auto Show design challenge last year, taking on the theme, "Sensing the Future" to look at how vehicles and people will interact in 2029. Peterbilt's concept entry, called Symbiotux, featured the concept of platooning. The interior would use nanotechnology and biomonitoring to adapt the environment to the driver's needs. For instance, a smart seat could sense a tight muscle in a driver's leg or back and adjust the ergonomics of the seat to compensate. Supporting photographs and video: http://www.truckinginfo.com/news/story/2015/05/peterbilt-highlights-technology-transformation.aspx
-
Heavy Duty Trucking / May 31, 2015 Peterbilt showed off its take on autonomous vehicle technologies to reporters Friday during a Technology Showcase at the Texas Motor Speedway. Bill Kahn, manager of advanced concepts at Peterbilt, doesn't really like to call the two demonstration vehicles "autonomous," although they would qualify as a Level 3 autonomous vehicle under National Highway Traffic Safety Administration classifications. He characterizes the technology more as the "cruise control of the future" and a "stepping stone to autonomous vehicles." Peterbilt engineers have dubbed it "advanced driver assist systems." A bumper-mounted radar system, on one of the trucks, and a lidar camera on the other, are used to determine the distance from the truck to the vehicle or obstacle ahead of it. The lidar has the added advantage of not only being able to determine an obstacle ahead, but also a wider field of "view" and the ability to provide some data on the size and shape of whatever's there. For on-highway situations, these and a windshield-mounted camera provide data to keep the truck in the lane as the truck steers itself. Kahn said this lanekeeping technology is capable of taking 85% of the active steering out of the driver's hands, leaving him much more refreshed. Kahn characterized lanekeeping as a form of advanced cruise control, and noted that just as any cruise control, you wouldn't use it in bad weather or congested traffic. The radar/lidar is also used for adaptive cruise, which can keep the truck the right distance from the vehicle in front of it and bring it to a complete stop if necessary. In addition, the concept trucks featured a GPS-based autopilot system that would allow the truck to operate autonomously in urban environments – but only if the route was preprogrammed. The GPS system is accurate up to 5 centimeters. One truck can drive the route (with a human driver) and "map" it, then transfer that data to other trucks in the fleet. The other trucks then follow that preprogrammed course; driver intervention would be needed in some situations. In the case of platooning, that information transfer between the front truck and the ones behind would happen in real time. So far, testing of the GPS system has all been done on non-public courses set up to mimic city streets. The trucks have Dedicated Short Range Communications, or DSRC, radio antennas, a vehicle-to-vehicle communication system. DRSC is similar to Wi-Fi, but is not likely to be vulnerable to interference, and is an important part of the federal government's plans for "connected vehicles." Supporting photographs: http://www.truckinginfo.com/news/story/2015/05/peterbilt-shows-off-cruise-control-of-the-future.aspx
-
Platooning is closer than you think – just like the trucks
kscarbel2 posted a topic in Trucking News
Fleet Owner / May 29, 2015 For many fleet managers, platooning seems like a dream come true - two trucks traveling in line, very close to each other, saving fuel without sacrificing safety. Platooning saves fuel because two tractor-trailers traveling closely, usually 40 to 50 feet apart, set up air flows that help to 'push' both trucks forward. In Peloton Technology, Inc. tests with CR England, platooning saved 7% at 65mph – 10% for the rear truck and 4.5% for the lead truck. So far, Peloton has logged 14,000 miles in all of its tests. At the heart of platooning is a wireless electronic communications system, also connected to the internet, that tells the second truck when the first truck driver has braked. The second truck brakes almost instantaneously without driver intervention. In essence, both trucks brake at the same time. Fleet Owner talked to Josh Switkes, Founder and CEO of Peloton Technology about the technology aspects of platooning and Randy Mullett, Vice President for Government Relations and Public Affairs at Con-way and a board member of ITS America about the policy and regulatory aspects needed to get platooning on the road. 1. How does the braking system work? Switkes: With vehicle-to-vehicle communications, the rear truck knows exactly what the front truck is doing. We know how much engine torque it's applying, we know how fast it's going, and most importantly, we know when and how much the brakes are applied. We know all this almost instantly, about ten milliseconds between when the front truck's brakes are applied and when the rear trucks knows about it. 2. Is the second driver's view of the road impaired? Switkes: Your view of your lane ahead is blocked, but your view outside of that lane is fine off to the sides. We also help the second driver know what's coming up on the road through a video link. We take a camera that's looking forward from the front truck, and send that video feed to the rear truck through the wireless communication, so the rear driver sees the road ahead. You use it like another mirror. 3. Does the second driver get bored looking at the rear of the lead truck? Switkes: Unlike some platooning tests in Europe, like the Sartre project [in Europe], we use manual steering so the second driver has complete control. He or she is engaged all the time. We're not replacing the driver. We’re taking their skills and adding an extremely fast braking reaction. 4. How do you match up trucks and decide the following distance? Switkes: This is the job of the cloud-based Network Operation Center. Trucks are connected to the internet. We don't let the drivers choose [their position], and the reason we don't let them choose is because it's how we increase safety. We order the trucks based on their braking ability. Whichever truck can stop shorter is always going to be in the back of the two-truck platoon. We only platoon when it's safe depending upon the type of road, weather and traffic conditions. 5. How do trucks find each other? Switkes: Many fleets have multiple trucks leaving a distribution center or hub at the same time or very close to the same time. Not every fleet has these trucks together, but we've found a good number of fleets that do. We plan to deploy first with these fleets. It's important to realize that trucks do not have to be going to the same destination. The can platoon for a while then split in different directions. There's still a savings in doing that. 6. How much does it cost to outfit a truck? Switkes: We're not talking about that publicly. Most fleets tell us they expect payback in about seven months. We don't do anything to the trailer, only the tractor. We charge fleets a per-mile fee while their trucks are platooning and saving fuel. 7. What's it like to ride in a truck that's part of a platoon? Mullett: I rode in platoon vehicles last summer at the ITS World Conference in Detroit. Peloton had a demonstration, and we drove around interstates in Detroit. I'm confident that the technical issues have been surmounted, and that it can be done in a safe way. 8. What are some of the non-technical or policy and regulatory issues that still need to be addressed? Mullett: You might think that technology is the problem, but it’s the policy issues that need to be worked out. For instance, we need harmony on following distance, because there are minimum following distances in some states. Also, how do we keep cars from jumping in and out of the space between trucks? There also needs to be commonality about things like where to place the video screens so you don't confuse drivers using different vehicles. There are also mundane issues like what happens when one driver in a platoon needs to go to the bathroom. 9. What about driver acceptance? Mullett: It took some drivers a while to get used to new technology like automatic transmissions. There will be a little bit of an acceptance curve on platooning. 10. What non-technical issues concern fleet managers? Mullett: If the rear truck has better fuel economy, and the trucks are from different fleets, how do you to share the fuel economy in a fair way? 11. Will car drivers call police if they see trucks following so closely? Mullett: That's another issue that needs to be worked out. Trucks need some kind of signage telling other drivers that they're platooning and driving safely. 12. What's the overall biggest challenge to platooning? Mullett: I think that our biggest challenges are having our policymakers and the public be able to keep up with and accept the technology without killing the idea. I think we're about a year away from a serious pilot program. It may take another couple of years before we get enough density to see a large difference in [national] fuel savings.
BigMackTrucks.com
BigMackTrucks.com is a support forum for antique, classic and modern Mack Trucks! The forum is owned and maintained by Watt's Truck Center, Inc. an independent, full service Mack dealer. The forums are not affiliated with Mack Trucks, Inc.
Our Vendors and Advertisers
Thank you for your support!