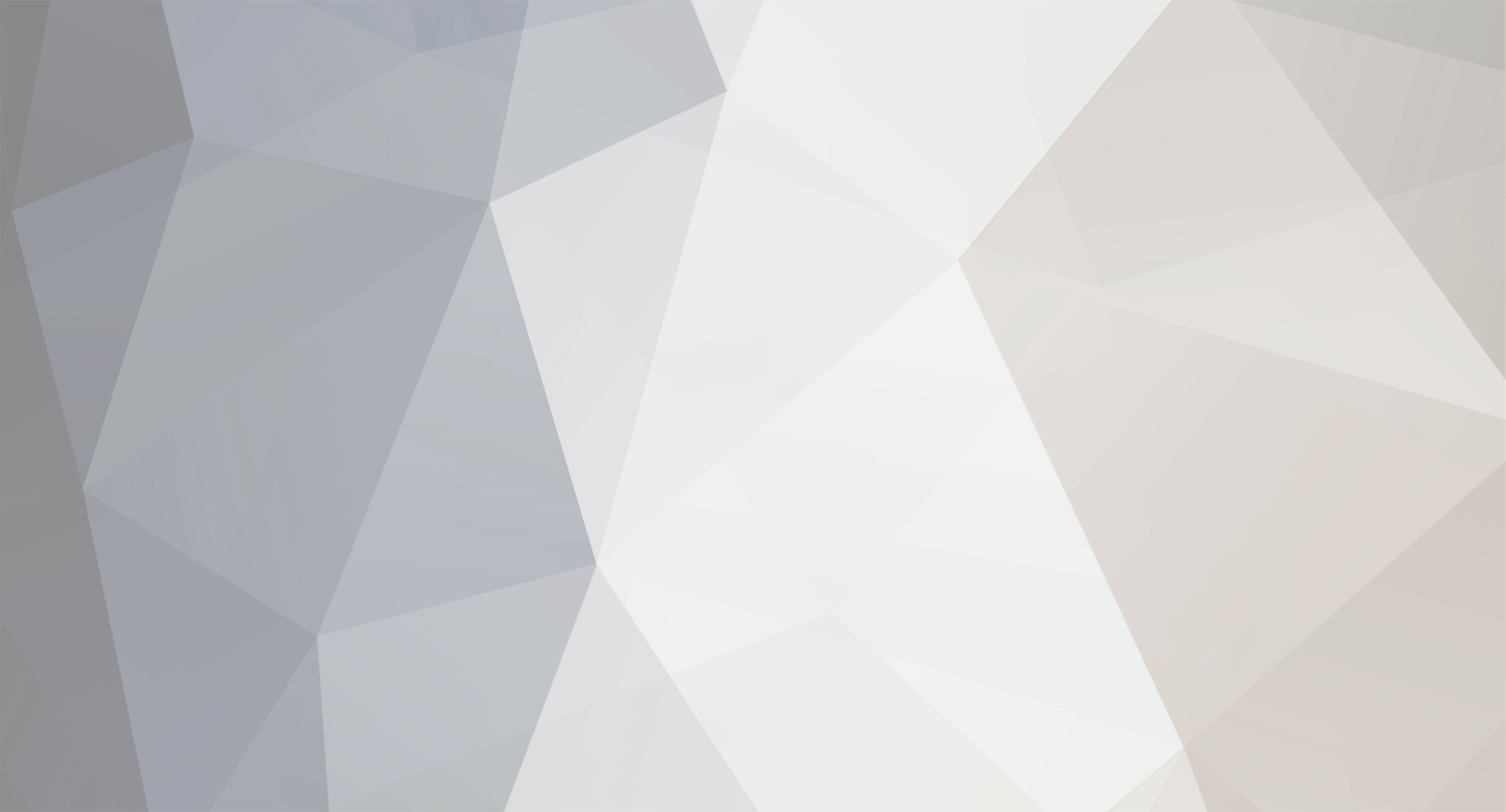
kscarbel2
Moderator-
Posts
18,774 -
Joined
-
Days Won
114
Content Type
Profiles
Forums
Gallery
Events
Blogs
BMT Wiki
Collections
Store
Everything posted by kscarbel2
-
Hyundai Trucks Press Release / September 27, 2016 .
-
ZF Innovation Truck 2016 Sees, Thinks and Acts with Intelligent Driver Assist Systems ZF Press Release / September 22, 2016 The Evasive Maneuver Assist (EMA), developed with project partner WABCO, automatically steers semi-trailer trucks around hazardous areas safely and helps to prevent rear-end collisions ZF’s Highway Driving Assist (HDA) actively keeps trucks in the lane and at an appropriately safe distance from the vehicle in front The automated maneuvering function helps to reduce accidents and downtimes while increasing efficiency at the truck terminal Friedrichshafen/Hanover. Greater safety and improved efficiency through automated driving are mobility megatrends that are increasingly relevant to the commercial vehicle sector. ZF is demonstrating its capabilities in these areas by showcasing its Innovation Truck 2016 developed for IAA in Hanover this year. With the vision of accident-free driving or “Vision Zero,” ZF is working on enhancing current assist systems for practical use on the road. Its efforts have resulted in a Highway Driving Assist (HDA) system which helps to keep the vehicle in its lane, and an Evasive Maneuver Assist (EMA) system which allows a truck to independently evade obstacles and brake. The latter was developed in cooperation with WABCO. The Innovation Truck 2016 also boasts a highly efficient solution with its autonomous maneuvering function SafeRange. Its intelligently networked systems allow the concept vehicle to autonomously maneuver to the loading bay in a precise and efficient manner, and if needed, with zero local emissions. Thanks to widely developed assist systems, modern trucks already offer a high level of safety. Now, with the ZF Innovation Truck 2016, ZF has pioneered the next level of active assist systems. Both the Evasive Maneuver Assist (EMA) and the Highway Driving Assist (HDA) systems can help prevent accidents more effectively. The SafeRange maneuvering system also boosts efficiency at the truck terminal – the key here is the linking of ZF's autonomous driving functions. Applying its competence in sensor technology, control electronics and mechatronic systems, the technology company enables the Innovation Truck 2016 to see, think and act. Avoidance instead of collision Typically, hazards occur at the tail end of a traffic jam on the freeway. If a truck driver fails to see this in time, the outcome could be fatal. In the ZF Innovation Truck, however, the unique EMA system takes control in this situation. The assistance function detects whether Advanced Emergency Braking or driver-initiated braking is sufficient to stop the vehicle before hitting an obstacle. If braking alone is insufficient to avoid a rear-end collision, the EMA directs the truck with its trailer independently (activated by the steering motion of the driver to the right or left) and safely toward the desired free lane or hard shoulder. ZF developed the system in cooperation with WABCO in early 2016. It analyzes information from cameras and laser sensors, and then activates the ReAX active electric power steering as well as the service brakes. A multi-stage warning cascade keeps the driver involved so that the system can be overridden at any time. Just like trains on a track The Highway Driving Assist (HDA) feature in the ZF Innovation Truck 2016 keeps the vehicle in its lane and effectively helps protect drivers from the often very severe consequences resulting from lack of attention, distraction or a few seconds of microsleep. The system not only warns the driver that the semi-trailer truck is unintentionally moving out of its lane, it also actively and independently keeps the truck in the lane. At the same time, it automatically maintains a safe distance from the vehicles in front at any speed, also including stop-and-go functionality. Efficient driving at the truck terminal The intense networking and automation of systems and functions help to considerably increase the efficiency and safety of workflows at truck terminals and transport hubs. Collisions while maneuvering can result in costly vehicle damage and downtimes while additionally increasing loading and unloading times. The Innovation Truck 2016 adapts a new approach. The system’s eyes and brain do not necessarily have to be located in the truck to automatically actuate its electrically powered mechatronic systems. That’s why, for the SafeRange autonomous maneuvering function, ZF has networked the truck to systems in the truck terminal. The truck to be maneuvered only needs a target on its trailer for the stationary cameras on the loading bay to be able to detect it. A computer inside the terminal calculates the trajectory and transmits the data via WiFi to the ZF Openmatics telematics system in the truck. This is where the vehicle control system takes over, using ZF's active electric power steering, ReAX, and the TraXon Hybrid automatic transmission system to steer the truck to the loading bay electrically and emission-free. A tablet doubles as an HMI control system that can be used to maneuver the truck from outside the driver’s cab. .
-
Reuters / September 28, 2016 With its recent acquisition of self-driving truck startup Otto, Uber Technologies Inc.[UBER.UL]is plotting its entry into the long-haul trucking business, aiming to establish itself as a freight hauler and a technology partner for the industry. Otto plans to expand its fleet of trucks from six to about 15 and is forging partnerships with independent truckers, Otto co-founder Lior Ron told Reuters in an interview. Starting next year, Otto-branded trucks and others equipped with Otto technology will begin hauling freight bound for warehouses and stores, he said. Uber has already started pitching services to shippers, truck fleets and independent drivers, and the services go well beyond Otto's initially stated goal of outfitting trucks with self-driving technology. It also plans to compete with the brokers who connect truck fleets and shippers. Fully autonomous trucks remain years away - some trucking industry experts estimate two decades - and the Otto vehicles are currently manned by a driver and an engineer. But the Uber-Otto efforts include a host of other technologies involving navigation, mapping and tracking, which can be deployed even as work continues on self-driving systems. An executive at one company told Reuters he had already been approached by Uber about hauling his goods, noting that Uber touted recent hires and advances in trucking technology. Uber aims to ultimately transform the competitive and fragmented $700 billion-a-year trucking industry, which is notorious for low margins. The company is challenging a host of established players, ranging from publicly traded companies, such as third-party logistics firms C.H. Robinson and XPO Logistics, to countless mom-and-pop trucking businesses. Otto has had motor carrier permits with the U.S. Department of Transportation and California Department of Motor Vehicles to move cargo since earlier this year. Eleven days after the close of the Uber acquisition last month, Otto filed for a new permit to haul freight, noting it would expand its fleet to 15 trucks. Ron told Reuters that Otto also aims to partner with the industry, and that "thousands" of owner-operator truck drivers have reached out to the company. "We are talking with everyone," he said. "We don't want to develop technology just for the sake of technology." Uber - the dominant ride-hailing firm and the world's most valuable venture-backed startup, at $68 billion - last month bought Otto in a $680 million deal. Otto, with about 100 employees, had just launched in January. While Uber's brand and financial backing could supercharge Otto's prospects, industry experts remain skeptical that a Silicon Valley startup with little experience can shake up long-haul trucking. "The transportation industry is a relationship-backed business," said Kevin Abbott, a vice president at C.H. Robinson. "There's a lot more to it than just finding a piece of equipment." Abbott noted that Uber is just the latest in a long line of companies that have tried to take the place of brokers, who typically match loads with vehicles. Uber and Otto also face competition from a growing crop of startups eyeing the industry. Companies such as Transfix, Convoy and Cargo Chief are aiming to unseat traditional brokers by matching shippers with carriers using complex algorithms, while Trucker Path has built a popular navigation app for truckers. BRAND ADVANTAGE? One indication of Otto's ambitions is its recent hiring of Bill Driegert, a logistics veteran who helped found Coyote, a leading freight broker, and served as its chief innovation officer, according to his LinkedIn profile. Uber and Otto are working to build a freight network to connect shippers and carriers, much like Uber matches passengers and drivers. The trucking push is partly a gambit to leverage the mapping and logistics expertise Uber has gained ferrying passengers and food in cities. "This is really about connecting the dots, connecting the shippers and the carriers," Ron said. "We are building that on the long-haul piece. Uber, through UberRush and UberEats, built that on the urban piece," referring to the company's on-demand delivery services. Self-driving trucks may eventually ease the driver shortage facing the trucking industry. But even absent autonomous technology, Otto says it could help decrease the cost of trucking goods by more quickly finding freight, mapping more efficient routes and reducing fuel consumption. "In Uber, you press a button and an Uber shows up after three minutes," Ron said. "In freight ... the golden standard is that it takes (the broker) five hours of phone calls to find your truck. That's how efficient the industry is today." Uber is hardly alone in tackling that problem. XPO Logistics - among the world's biggest logistics services - has invested heavily in software that maximizes the utilization of trucks and reduces fuel consumption. C.H. Robinson has developed technology that allows companies to track their shipments, as well as an app for carriers with small fleets. Moreover, the model that Uber used to disrupt the taxi industry may not translate easily to trucking, said transportation analyst Jack Atkins of investment bank Stephens Inc. Companies avoid risk when shipping goods more than consumers do when hailing rides, he said. "I don't really see it as a near-term threat, just because of how complex the industry really is," he said. "It's not as simple as, 'Hey, I want to go from point A to point B in Midtown.'" LOGGING THE MILES Ron emphasizes that Otto's autonomous driving technology is still in a "testing regimen." The trucks can drive by themselves on highways, with two copilots as backup, but maneuvering off the open interstate remains a challenge. The trucks now haul random items from the company's garage to test how the vehicles respond to hauling weight. But the company will "fairly soon" move goods for shippers - just about any type of freight, except for hazardous materials, Ron said. Otto currently has about two dozen drivers who are employees, and next year the company will have more partnerships with independent drivers. Truck fleets will also help test its technology. Otto has had talks with potential partners and is in the process of trying to cement deals with some of them, Ron said. "This is all about putting it on the road," Ron said, "collecting the miles." .
-
North West Roofing on a high with Iveco Stralis Hi-Streets
kscarbel2 posted a topic in Trucking News
Transport Engineer / September 27, 2016 North West Roofing Supplies has taken delivery of the first of two new Iveco Stralis Hi-Street rigids, ordered after positive experience with an earlier trial vehicle. Supplied by dealer Walton Summit Truck Centre, the St Helens-based operator’s new additions are 26-tonne 6x2 Hi-Street rigids, both with a plant body, an Atlas 165.2A2 crane, and a lifting and rear-steering axle, providing increased manoeuvrability for deliveries in urban areas. The first vehicle has gone into service; the second is due for delivery in December. Both are supplied on five-year Iveco Elements R&M packages. The trucks are powered by Iveco’s Cursor 9 engine, featuring Iveco’s HI-SCR technology and producing up to 310bhp between 1,675 and 2,400 rpm, and up to 1,300 Nm of torque between 1,200 and 1,675 rpm. The vehicles also feature the EuroTronic fully-automated gearbox, manufactured for Iveco by ZF. “We first decided to trial an Iveco in 2014, after speaking to another operator that recommended the Hi-Street for our line of work,” says managing director Stephen Phillips. “We took on a similar 26-tonne rigid from another manufacturer at the same time, and found the Iveco quickly surpassing its competitor in terms of on-the-job reliability. The drivers love the truck, and we’re completely satisfied – the Hi-Street is ideal.” Payload is a bonus, he adds: “The 18.8-tonne capacity is very competitive, given our body and crane combination. It means we can collect from our suppliers just once per day in the morning, and spend the rest of the day delivering what our customers ordered.” The Stralis trucks join a fleet of nine 26-tonne rigids, and will be in operation six days per week. The vehicles are expected to clock up 50,000 miles per annum and will be in operation for between five and seven years. . -
Transport Engineer / September 26, 2016 Somerset-based bulk haulier W Rolls has taken delivery of a new 32-tonne Renault Range C, joining eight more Range Cs and three Premium Landers already in its fleet. Supplied by Renault Trucks South West, the Range C460 8x4 with Aliweld bulk tipping body means the operator’s 12-strong fleet is solely Renault. Director John Bartleet says: “I’ve been buying Renault trucks for a long time and I’m always recommending them to other operators who are buying new vehicles. “The trucks are great, reliable and robust, plus we have a fantastic relationship with the team at Renault Trucks South West as well as great back-up service from Renault Trucks’ approved repairer A E George Commercials, which is only four miles away in Bruton.” The W Rolls fleet delivers all over the UK, with the trucks covering around 120,000km per year. “Our tippers are out Monday to Friday on long distance jobs up and down the UK. The fuel figures have been very impressive and on average we are achieving 9-plus mpg,” says Bartlett. Driver appeal was an important consideration, he says, adding: “Our drivers are particularly pleased with the new Range Cs. They are working on long distances so a comfortable life on board is crucial and overall they have been very happy with the bigger cab, storage spaces and interior finishes.” .
-
ZF all-electric central drive points to future city trucks
kscarbel2 posted a topic in Trucking News
Transport Engineer / September 27, 2016 ZF confirmed its position at the hub of the commercial vehicle electrification drive at the IAA exhibition, in Hanover, Germany, showing an all-electric central drive in Mercedes-Benz Urban eTruck concept vehicle. The new drive is based on ZF’s AVE 130 electric portal axle, originally designed for city buses as a close-to-wheel electric drive. It combines an electric motor with a two-stage single-speed transmission, differential and power electronics to form a compact, integrated unit. “Many commercial vehicles with limited daily mileage can already be operated using all-electric drives,” comments Fredrik Staedtler, head of commercial vehicle technology at ZF. And he adds that return-to-base operations also favour electric commercial vehicles – noting that their numbers are bound to grow as electric vehicle become mandatory in cities in Europe and Asia. Staedtler’s all-electric central drive, he says, brings electric city buses and delivery trucks one step closer to zero-emission driving – particularly since it mimics conventional driveline configurations. The fact that the central drive can be combined with both single rear drive axles and conventional low-floor axles means it can be installed in low-entry buses and all kinds of low-floor buses, he explains. The new drive is scheduled for volume production starting in 2018. At 150 kW (201.15 hp), the system can also work in light commercial vehicles. “Identifying synergies between passenger cars and commercial vehicles has always been an asset of ZF and this also holds true for our electrification strategy,” states Staedtler. . -
Efficiency Run 2016 – Product Launch: Up to 20 percent less fuel and CO2: Mercedes-Benz Trucks and Krone present highly efficient semitrailer-tractor combination Daimler AG Press Release / September 22, 2016 Integrated approach involves everyone in the haulage sector playing their part in achieving CO2 targets: commercial vehicle manufacturers, body/tyre suppliers, logistics companies and political decision-makers World première and start of sales for the "Krone Profi Liner Efficiency": economical and practical new trailer has optimised aerodynamics and A-label low rolling resistance tyres to reduce fuel consumption by over five percent IAA première: Latest generation Mercedes-Benz Actros with highly efficient OM 471 engine saves up to six percent on fuel Predictive Powertrain Control from Mercedes-Benz with fuel savings of up to five percent has been setting benchmarks for many years A-label tyres for low rolling resistance on the tractor unit enable a further two to four percent to be saved on fuel Efficiency Run 2016 tested and verified by five customers: Elflein, Grosse-Vehne, Rhenus, Seifert and Wiedmann & Winz Working together, Mercedes-Benz Trucks and the trailer manufacturer Krone have transformed the concept of an "integrated approach" to reduce CO2 into reality in less than twelve months. The integrated approach involves everyone in the haulage sector playing their part in reducing fuel consumption: commercial vehicle manufacturers, body/tyre suppliers, logistics companies and, last but not least, political decision-makers. The two companies' development efforts on the integrated approach bring customers real benefits. The specific Mercedes-Benz Actros unveiled at the IAA 2016 features the efficiency package and the latest generation of the OM 471 six-cylinder in-line engine, Predictive Powertrain Control (the anticipatory cruise control system) and A-label low rolling resistance tyres. When combined with the new Krone "Profi Liner Efficiency" trailer, it promises a reduction in fuel consumption, and therefore CO2 emissions, of up to 20 percent compared to existing combinations. A standard semitrailer-tractor combination from 2014 forms the basis of this comparison. Mercedes-Benz Trucks and its partners launched the first Efficiency Run last year and were able to save up to 14 percent on fuel as a result in comparison to a standard semitrailer-tractor combination. Dr Wolfgang Bernhard, Member of the Board of Management of Daimler AG, with responsibility for Daimler Trucks & Buses: "In 2015, The Efficiency Run proved that the integrated approach works. Now, just one year later, we are putting products that are fit for series production onto the roads. Our optimised semitrailer-tractor combination pays off for the environment and our customers: it lowers CO2 emissions and fuel consumption by up to 20 percent – and the cost can be amortised in about eighteen months." Gero Schulze Isfort, managing director of the Krone Commercial Vehicle Group, adds: "Working in partnership has moved us a decisive step forwards in terms of the integrated approach. Last year's Efficiency Run more than confirmed our expectations. We have subsequently further optimised our trailer, particularly with regard to everyday practicality. Thus, this year we were able to launch another field trial, now ended, which has resulted in a semitrailer that is fit for series production and is now going on the market – the Profi Liner Efficiency." Voluntary commitment fulfilled: 20 percent lower CO2 emissions Reducing fuel consumption, and therefore CO2, is currently one of the biggest challenges facing the haulage sector. In sectors outside the emissions trading scheme, of which haulage is one, the EU wants to reduce CO2 emissions by 30 percent by 2030. This demands enormous effort on the part of everyone involved in the haulage sector. However, the industry is convinced that it can accomplish this task – without statutory provisions – not just out of a sense of responsibility for the environment and society, but also driven by its customers. This is because lower CO2 emissions also mean lower fuel consumption, which represents a high cost factor for our customers. Back in 2008, European manufacturers formulated a vision to reduce CO2 emissions by 20 percent by 2020. It is essential, however, that this is cost-effective so that transportation by truck does not become more expensive and there is no impact on the European economy's competitiveness. The responsibility here lies not just with the manufacturers of tractor units, but rather with the entire trucking system. That extends to tractor units, semitrailers, tyres, fuel, operations, infrastructure and fleet replacement. The Efficiency Run is the best proof that this integrated approach works in real-world practice: compared to a standard semitrailer-tractor combination built in 2014, consumption could be reduced by 18 - 20 percent as a result. Thanks to the Efficiency Run, the package of measures being presented at the IAA to reduce fuel consumption and CO2 could quickly be transformed by Mercedes-Benz Trucks and Krone into specific standard products, which are already available to order. Integrated approach: enough potential to lower CO2 emissions by 20 percent Depending on the truck and trailer in use, the following increases in efficiency are evident in terms of fuel consumption and the reduction in CO2 emissions: Krone Profi Liner Efficiency: over five percent Mercedes-Benz Actros tractor unit: up to six percent Predictive Powertrain Control (PPC): up to five percent Low rolling resistance tyres for tractor unit: two to four percent This increase in efficiency of up to 20 percent in total pays off for customers. Depending on the application and the vehicle service life distance, the extra cost of the trailer can be amortised in one to two years. Efficiency Run 2016 with new Krone semitrailer tested by five customers, now available to purchase This year, Mercedes-Benz Trucks and Krone organised a further three-month endurance test. As part of the Efficiency Run, five transport businesses tested the new optimised semitrailers in everyday operation: Grosse-Vehne, Elflein, Rhenus, Seifert and Wiedmann & Winz. In the course of this, the transport companies involved deployed their own Actros tractor units dating from 2013 to early 2015 from their fleets. These included two Actros 1845, two Actros 1842 and one Actros 1843. None of the five vehicles were specially configured for the three-month test run and no efficiency packages were implemented. The only on-board equipment was the FleetBoard telematics system into which Krone Telematics had been integrated including tyre pressure loss detection system, and Predictive Powertrain Control (PPC). Instead, the main focus of the field trial was on the completely new semitrailer attached to the five Actros models: the Krone Profi Liner Efficiency. It celebrates its world première at the 2016 IAA Commercial Vehicles show in Hanover, Germany, and is now available to order. This solution differs from the familiar Krone Profi Liner in three main ways: New self-engineered Krone side panels made of impact-resistant plastic cover all the sides, including those of the three trailer axles, and improve the Cd value by 5.2 percent. A four-part rear wing, also made of robust plastic, improves the Cd value by a further 6.3 percent. A-label low-resistance tyres reduce rolling resistance. Profi Liner Efficiency: ready for tough day-to-day operation In comparison with last year's Efficiency Run, this test run did not look solely at fuel savings. Assessing the new trailer's everyday usability was a specific priority. This involves examining handling, noise emission, robustness, loading options and access. During the three months of testing, the five semitrailer-tractor combinations covered more than 150 000 km on German roads. They transported car engines, steel, paper, timber products and building materials – in short- and long-distance haulage. According to the drivers, the new trailer really proved its worth in tough day-to-day operation. Loading is possible from all sides and even from the top, and presents no problems at all. Using a forklift to load from the side works just as smoothly as with a conventional trailer, despite the side panels. No damage to the side panels was noticed at any time during the test phase. Reverse docking onto a loading ramp was also completed without difficulties. All that is necessary is to fold in the four-part rear wing before opening the rear-end doors. Based on feedback from drivers, this takes just a few seconds. They also made positive comments about the familiar operability of the lifting and lowering unit. The structural system for the side panels was singled out for high praise. It comprises five individual elements. These can be removed easily by hand at the height of the trailer axles – an important consideration when a wheel needs to be changed, for example. Even so, the lightweight plastic side panels (a proprietary Krone design) are so stable that they do not cause any wind noise. The side panelling is, of course, certified by the German Technical Inspection Authority (TÜV) and complies with legal requirements relating to the side underride guard. Low rolling resistance tyres and the trailer's improved Cd value reduce consumption by over five percent The side panels improve the Cd value of the Krone Profi Liner Efficiency by 5.2 percent. What's more, the rear wing improves the Cd value by a further 6.3 percent. These two benefits, in conjunction with low rolling resistance tyres, have an extremely positive effect on the Actros tractor unit's fuel consumption. An analysis of FleetBoard and Krone Telematics data showed that the optimised aerodynamics and use of A-label tyres reduced consumption by over five percent on their own. Krone's new efficiency specification will also be available for the Mega Liner, Cool Liner and Dry Liner in future. New heavy-duty engines from Mercedes-Benz Trucks at the IAA: Actros with standard efficiency package and OM 471 engine saves up to six percent on fuel The new Krone trailer is not the only form of the integrated approach that will be presented in Hanover at the 2016 IAA Commercial Vehicles show. At the Mercedes-Benz Trucks stand, the latest generation of the Mercedes-Benz Actros featuring optimised aerodynamics due to a new spoiler lip, an optimised drivetrain and economical heavy-duty engines will also be on view for the first time. Of the new generation comprising three six-cylinder in-line engines, the most economical is the OM 471 with a displacement of 12.8 litres. The standard optimised Mercedes-Benz Actros with this engine variant consumes up to six percent less fuel. PPC lowers fuel consumption with further refined shift strategy In addition to the new engine and transmission technology, the driving strategy also makes a noticeable contribution to lowering fuel consumption. Mercedes-Benz has been setting benchmarks for many years now with Predictive Powertrain Control, GPS data and topographic maps in conjunction with the Mercedes PowerShift 3 automated transmission, and with fuel savings of up to five percent. Now driving with PPC is even more efficient. The shift points of the anticipatory cruise control have undergone further optimisation. Internal tests by Mercedes-Benz confirm that journey times change only negligibly with the new strategy – in reality, the difference is of no significance. In contrast, the saving effect of the new driving strategy is quite tangible. About Krone Commercial Vehicle Group Innovative, competent and responsible – for many years these quality criteria have informed the philosophy of the family-owned Krone business which was established in Spelle, Germany, in 1906. The right mix of knowledge, entrepreneurial spirit and strong customer proximity has been the defining factor in the Krone Group's successful development. As one of the fastest growing companies in both the commercial trailer and agricultural machinery sectors, Krone is a benchmark setter. The reason for this is a high level of innovational strength, as demonstrated by a number of unique selling points. Worldwide, Krone's agricultural machinery and commercial vehicles are known to meet exceptional quality standards. The Krone portfolio of commercial vehicles includes platform and box semitrailers, container chassis, swap systems, trailers, truck bodies and vehicles designed specifically for courier, express and parcel services. Krone now has production facilities in four locations in Germany: Werlte, Herzlake, Dinklage (all in Lower Saxony), Lübtheen (Mecklenburg-Western Pomerania), as well as in Tire in Turkey. Annual output is currently around 40 000 vehicle units. All the time Krone is developing new solutions which can help transport businesses to operate successfully, even in a difficult economic environment. In the process, the focus is on two aspects: efficiency and load securing. The Group has succeeded in considerably boosting the efficiency of vehicles by means of numerous innovative solutions such as new vehicle concepts (Smarter Trailer). At the same time, vehicle safety is being continually optimised by new certified load-securing variants. Back in 2008, for example, Krone unveiled a particularly aerodynamic trailer – the Profi Liner Eco. The new Profi Liner Efficiency, which is available now, sees Krone once again underlining its expertise as a sustainable and environmentally aware commercial vehicle manufacturer. Krone is one of the biggest employers in the Emsland district of Lower Saxony; approx. 1700 people are currently employed in the agricultural machinery sector. Following the merger of the Brüggen vehicle production plants and service companies into the Krone Commercial Vehicle Group at the start of 2016, around a further 2800 employees now work for Krone across the five commercial vehicle production sites. The company has been family-owned for four generations without interruption; the Krone Group is now led by Bernard Krone who is managing partner of Bernard Krone Holding SE & Co. KG. . . .
-
Scania Group Press Release / September 27, 2016 BUMA, one of Indonesia’s leading mining operators, has decided to invest in 266 Scania trucks over the next five years, at a value of approximately USD 30 million. The order includes parts and maintenance contracts and will be delivered by Scania’s partner United Tractors. In the face of tough competition from other manufacturers, Scania was chosen as the supplier of transport solutions to Indonesian mining operator BUMA. The order comprises 266 trucks, plus parts and services on site over the next five years and is worth approximately USD 30 million. “This is a perfect fit for our ‘tailor-made for application’ approach,” says Björn Winblad, Head of Scania Mining. “By utilising our experience from lean production and continuous improvement, we intend to help BUMA to improve its mining operations across Indonesia.” Scania has worked with continuous improvements in its own business for decades, and is now drawing on that experience to offer its know-how to customers within application areas such as mining and forestry. The order includes Scania P 410 8×4 and R 580 6×4 models. The vehicles and services will be delivered by United Tractors, Scania’s partner in Indonesia. In August 2016, the first 14 vehicles were delivered, and another 86 vehicles will be delivered in 2016. BUMA (PT Bukit Makmur Mandiri Utama) was established in 1998 and provides services to Indonesian coal producers across all production stages, including geology and planning, overburden removal, coal mining, coal hauling and reclamation and rehabilitation. The company has some 11,000 employees and operates more than 3,000 heavy vehicles. United Tractors is the leading and the largest distributor of heavy equipment in Indonesia, providing products from world-renowned brands, including Scania. United Tractors’ distribution network includes 19 branch offices, 22 site support offices and 11 representative offices in 22 provinces across the country. The company has played an active role in the Indonesian mining industry for many years by delivering top-tier products and services to its customers. .
-
Mercedes-Benz Citan: compact on the outside yet roomy on the inside, with new packages of equipment for the exterior and interior, dual clutch transmission for diesel Daimler AG Press Release / September 21, 2016 Compact and flexible: the Citan's many variants Citan with Exterior Off-Road Styling package Citan with Exterior Dynamic package by Hartmann Citan with new packages of equipment for the interior Diesel engine: Euro 6 attained without SCR technology Transmission: dual clutch transmission now available for the diesel version Small wonder: the Mercedes-Benz Citan urban delivery van fits the bill when a combination of compact dimensions with plenty of payload and a surprisingly large volume is called for. The Citan has long since established itself as an integral part of the Mercedes-Benz Vans model range. With a choice of three lengths, the panel van, Mixto and Tourer variants, several weights and many equipment variants – the Citan is a real pro among its peers. Featuring new equipment packages, and now a dual clutch transmission for the diesel engine too, further attractive variants of the Citan will be available from summer 2017. Compact and flexible: the Citan's many variants The Citan offers maximum flexibility when it comes to adapting to the requirements of its customers. The variety begins with its three lengths: the compact Citan (3.94 m), the long Citan (4.32 m) and the extra-long Citan (4.71 m). No-one offers greater choice in this class. It is available ex factory as a panel van, Mixto and Tourer – covering all requirements from goods to passenger transport and combinations of the two. There is also the Citan WORKER panel van and the Citan CREW for particularly price-sensitive customers. The Citan's permissible gross vehicle weight ranges between 1.8 t and 2.2 t. The long variant of the Citan is particularly versatile, offering a choice of three weight variants. The Citan offers a diverse scope of particularly useful options ex factory. These include different door and window variants, panel vans with a folding load retention grille on the co-driver's side or a roof flap at the rear, a load retention grille for the Mixto or a luggage net for occupant protection on board the Tourer. Lashing eyelets are similarly available ex factory in the sidewalls, wood flooring and interior panelling of the cargo space. Last but not least, accessories such as cargo baskets with loading roller, basic roof carriers or ladder racks are available from Mercedes-Benz partners. The Citan panel van with double co-driver's seat is particularly flexible. Both seats have three-point seat belts and height-adjustable head restraints. If no-one is using these seats the backrests can be folded forward, with the centre backrest then acting as a writing surface if needed. There is a stowage compartment underneath the double seat, accessible from above by folding forward the single-piece seat cushion. A navigation system developed specially for the Citan points the way to the destination. The device has a 1-DIN form factor and is operated via a touch-sensitive 3.5-inch screen. The optional reversing camera makes manoeuvres at low speed easier, thereby boosting safety. The camera is hidden behind the licence plate holder on the tailgate or rear door and is activated when the reverse gear is engaged. The camera picture is shown in the inside rearview mirror, which dims automatically in bright light conditions. Guidelines help the driver to assess distances. Citan with Exterior Off-Road Styling package Although it already has a distinctive and attractive look, the Citan can now be enhanced further with new equipment packages. The Exterior Off-Road Styling package (Offroad-Optik Paket Exterieur) underlines the Citan's robust suitability for a range of application profiles and makes for an even more striking and individual appearance. It consists of dark grey wheel arch liners and sill panels and a front and rear spoiler in the same colour shade. The Exterior Off-Road Styling package is available for the long Citan. It is additionally on offer with raised ground clearance, steel underbody protection and reinforced tyres of size 195/65 R 15 for use on uneven surfaces such as construction sites. Citan with Exterior Dynamic package by Hartmann The Exterior Dynamic package by Hartmann (Dynamik Paket Exterieur by Hartmann) enhances the Citan's looks in a particularly emotional and exclusive way. This package is made for the German market by partner firm Hartmann as part of VanSolution, the programme for body and conversion solutions ex factory. It consists of a new front and rear apron as well as sill panels. Optional 16-inch light-alloy wheels can also be added. Citan with new packages of equipment for the interior Another new feature for all markets is the Colour Interior Design package (Design-Paket Interieur Color). This freshened look stands out with red highlights around the air vents and loudspeaker grilles. Red topstitching gives the seating fabrics and head restraints, the centre armrest as well as the shift lever gaiter a dash of emotion. The red topstitching is on offer in addition to the already available Chrome package (Chrom-Paket), upgrading it to the Chrome Interior Design package (Design-Paket Interieur Chrom). Furthermore, Mercedes-Benz is adding another practical item of equipment to the Citan portfolio: a radio with navigation system and LINGUATRONIC voice control. Mercedes-Benz Vans also supplies the Citan with driving aids ex factory for drivers with restricted mobility. Diesel engine: Euro 6 attained without SCR technology With four engines to choose from, customers are guaranteed to find the right one for them. The Citan's compact turbodiesel engine with a displacement of 1.5 l is available in three output categories, all of which comply with the Euro 6 emissions level as standard: 55 kW (75 hp), 66 kW (90 hp) and 81 kW (110 hp). Progressing to Euro 6 has actually increased maximum torque by 20 Nm for each diesel engine, to figures ranging between 200 Nm and 260 Nm. This translates into a noticeable rise in pulling power of around 10 percent. In the process of moving to Euro 6, the BlueEFFICIENCY package has become part of the standard specification of all vans with manual transmission. Among other features, this includes an ECO start/stop function and lowers fuel consumption for the diesel variants to just 4.3 l/100 km according to NEDC. The Citan achieves this outstanding consumption figure without compromising performance. The new emissions standard has certainly made the Citan clean for the future: all variants of the Citan with diesel engine achieve Euro 6 simply through internal engine measures and a storage-type NOx catalytic converter. No complex SCR technology is necessary, so drivers of the Citan no longer have to worry about using the extra service fluid AdBlue. Buyers can also choose a sprightly petrol variant as an alternative to the diesel engine. This engine has a displacement of 1.2 l and is rated at 84 kW (114 hp). In action, the compact engine is surprisingly powerful: at kickdown the engine mobilises 205 Nm of torque for a short time rather than 190 Nm. The extra torque is provided in second, third and fourth gears for a maximum of 20 seconds and helps in situations such as overtaking, thus making it a further safety factor. Transmission: dual clutch transmission now available for the diesel version Depending on the specified engine variant, the Mercedes-Benz Citan comes with a five-speed or six-speed manual transmission. It is also optionally available with the 6G-DCT six-speed dual clutch transmission. Previously available exclusively for the petrol-engined Citan 112, it will also be possible to get this for the Citan 111 CDI from 2017. This six-speed unit combines the economy of a manual transmission with the convenience of an automatic. The transmission features two separate clutches; one for the even-numbered gears and one for the odd-numbered ones. While driving the next gear is already pre-selected, and it only takes fractions of a second for one clutch to open and the other to close. The gear changes occur at lightning speed and virtually without interruption to tractive power, thus making them almost imperceptible to the driver. The driver's work is also made easier by a crawl function and a start-off assist system. The performance of the vehicle with dual clutch transmission remains the same as with the conventional six-speed manual transmission. .
-
Mercedes-Benz Vito: versatile all-rounder with three drive system variants and new items of interior equipment Daimler AG Press Release / September 21, 2016 One van, three drive systems The Vito's broad model range Wide choice of length and weight variants Safety first: numerous assistance systems Engines complying with the Euro 6 emissions level, SCR technology for exhaust gas cleaning Interior now comes with additional equipment items One van, two engines, three lengths and three drive systems – the Vito is the versatile all-rounder among mid-size vans with a permissible gross vehicle weight of around 3.0 t. Particularly outstanding it the powertrain engineering: the Vito is the only van in its class to be available with a choice of front-wheel, rear-wheel and all-wheel drive. At the IAA Commercial Vehicles 2016 the Vito is appearing with numerous new equipment variants. One van, three drive systems The Vito is the first and only vehicle in its class to be available with a choice of front-wheel, rear-wheel and all-wheel drive. As such, the Mercedes-Benz among mid-size vans perfectly accommodates a whole range of different requirements. The selection criteria are logical: the front-wheel drive is very light, and when the vehicle is unladen or carrying only a low load, it offers better traction. It has a very high payload of around 1300 kg, but its procurement price and maintenance costs are low. Rear-wheel drive is the right solution for all applications involving heavy weights, high towing capacities and, if required, exceptional driving dynamics. All-wheel drive is the answer to the request for maximum traction. The Vito's broad model range From skilled crafts and trades to retail, service providers, shuttle services and taxis – the Vito is truly one vehicle for all. For example, the Vito panel van is available in a choice of three lengths. There is also the particularly favourably priced WORKER panel van for cost-conscious buyers. The Vito Mixto combines the advantages of a panel van and crewbus. The Vito Tourer is available as the functional Vito Tourer BASE, the versatile Vito Tourer PRO and the premium Vito Tourer SELECT. By virtue of this complete model family, the Tourer can accommodate all types of passenger transport. Wide choice of length and weight variants With three lengths spanning the compact (4.90 m), long (5.14 m) and extra-long (5.37 m) variants, the Vito offers plenty of choice. The Vito is also available in various weight variants up to a gross vehicle weight of 3.2 t. The optional equipment for the Vito covers an unusually diverse range offering broad scope for commercial applications. There are, for example, numerous door and window variants or roof rails with a rack. A highly functional range of optional equipment is also available for the cargo space, comprising wood flooring, a rail system for securing loads and also tie-down rails on the side wall and the interior panelling. Roof attachments and carrier systems as well as luggage compartment tubs are available either ex factory or as accessories. Customers opting for a Vito Tourer are spoilt for choice when it comes to fitting out the passenger compartment and installing seating: two and three-passenger bench seats, bunk and table packages are available, for example. The seats can be installed on wood or plastic flooring, or on a floor with fine carpeting for use as an exclusive shuttle. Whether as a panel van, Mixto or Tourer, different heating and climate control systems make the time spent on board a pleasant one. Safety first: numerous assistance systems The Vito panel van was the first van to provide airbags and a seat belt reminder for both the driver and passengers as standard. The Vito Tourer PRO and Vito Tourer SELECT models also impress with windowbags and thorax/pelvis sidebags in the front. It is possible to get windowbags in the rear for the Vito Tourer. With up to eight airbags in total, it is the benchmark. ATTENTION ASSIST and Crosswind Assist are part of the standard equipment. Crosswind Assist virtually eliminates the effects of wind gusts acting on the vehicle. Tyre pressure monitoring is another item of standard equipment on the Vito Tourer. In addition, the Vito may be equipped with numerous other assistance systems to suit individual needs. Examples include the only Active Parking Assist system for vans, COLLISION PREVENTION ASSIST, Blind Spot Assist and Lane Keeping Assist. An optional Intelligent Light System (ILS) provides an alternative in the Vito to the powerful halogen headlamps. This technology consists of LED indicators, LED daytime running lamps, as well as LED low-beam headlamps and main beam with cornering light function. Depending on the road speed, the headlamps adapt for driving on motorways or country roads by varying the light distribution. Engines complying with the Euro 6 emissions level, SCR technology for exhaust gas cleaning Ever since it was presented in 2014 the Vito has been available in Europe with diesel engines that comply with Euro 6. Now Mercedes-Benz has switched the entire Vito range in Europe over to the most stringent emissions level. This means that all models feature an effective form of exhaust gas cleaning with SCR technology and AdBlue injection. Furthermore, the additional CDI designation has replaced the previous BlueTEC designation. The standard version of the AdBlue tank has a capacity of 11.5 l. A larger 25 l version is available as an option. Switching to Euro 6 has involved no change to the basic engine data. For the Vito with front-wheel drive there is a horizontally installed compact four-cylinder engine with a displacement of 1.6 l available in two output categories: the Vito 109 CDI rated at 65 kW (88 hp) and the Vito 111 CDI at 84 kW (114 hp). In the Vito with rear-wheel drive, a four-cylinder model with a displacement of 2.15 l works at three output levels: the Vito 114 CDI rated at 100 kW (136 hp), the Vito 116 CDI at 120 kW (163 hp) and the Vito 119 CDI at 140 kW (190 hp). Power transmission in the Vito is taken care of by a six-speed manual transmission and the 7G-TRONIC PLUS automatic transmission – the world's only automatic transmission with torque converter offering seven levels for vans. It forms part of the standard equipment for the Vito 4x4. Interior now comes with additional equipment items New equipment items for the interior are unveiled at the IAA Commercial Vehicles 2016. These include the new combination of a comfort driver's seat with folding armrests and a double co-driver's seat. Drivers working for courier, express and parcel services now in turn benefit from a new seat with modified contours: the less strongly shaped sitting surface makes it easier for the driver when getting in and out of the vehicle frequently. It is now possible to obtain the particularly versatile Vito Mixto and Tourer models with sliding windows in the centre. As an option, Mercedes-Benz now supplies the Tourer with a 2-2-3 seating arrangement in the passenger compartment, i.e. with three seat rows for the rear passengers. The long variant of the Tourer is also optionally available with an attractive panoramic roof. For the Vito Tourer categorised as an M1 passenger car, the permissible gross vehicle weight rises from 3.05 t to 3.1 t, which means it can carry an additional 50 kg as part of its passenger and luggage load. As for the exterior, a Mercedes-Benz can also look particularly stylish from the outside – also when it is a commercial vehicle. Therefore, all models are now available with an optional chrome-plated radiator grille. Last but not least, the Vito can now be equipped with numerous driving aids ex factory for drivers and passengers with restricted mobility. .
-
Mercedes-Benz Sprinter: the benchmark in its vehicle class, now with new weight variant and more powerful engines Daimler AG Press Release / September 21, 2016 Vans for the world: six locations on three continents The Sprinter's variety is unrivalled Comfortable cockpit, high level of safety The Sprinter crewbus now has more seats An extra variant with a gross vehicle weight of 5.5 t Euro 6/VI emissions level for all models, modified designations More power and torque for the four-cylinder CDI It is the benchmark in its vehicle class: large vans with a gross vehicle weight of around 3.5 t are widely called Sprinter. This flagship model from Mercedes-Benz Vans has given its name to an entire vehicle class. The first generation was unveiled 21 years ago, and today more than three million Sprinter are on the road in over 130 countries of the world. Now a variant with a permissible gross vehicle weight of 5.5 t has been added to the already varied product portfolio of the successful Sprinter. At the same time, Mercedes-Benz has revised the diesel engines for the Sprinter and in Europe all variants now comply with the Euro 6/VI emissions standard. The performance of the two engines at the lower end of the range has been considerably increased too. Vans for the world: six locations on three continents The Sprinter is not only sold all over the world, it is also produced all over the world. The lead plant is Düsseldorf, where the closed panel van and crewbus versions of the Sprinter leave the production lines in six-figure numbers each year. Mercedes-Benz produces the chassis in Ludwigsfelde near Berlin. The other Sprinter production locations are in Buenos Aires/Argentina, Charleston in South Carolina/USA, Fuzhou/China and Nizhny Novgorod/Russia. The same, high Mercedes-Benz quality standards are applied throughout. After Germany the USA is now the second-largest sales market for the Sprinter. Because the successful European concept also impresses American customers, the number of outlets selling and servicing the vehicle has grown to 280 nationwide. The plan is to build on this success: to service the North American market even better, a full production plant is presently being constructed for the Sprinter in Charleston, South Carolina. Construction began this summer. The Sprinter's variety is unrivalled Key factors in the success of the Sprinter include its tailor-made concept and continuous further development – the Sprinter never stands still. Panel van, crewbus, pickup, chassis – this roughly sums up the range of Sprinter models. The closely tiered line-up meets practically all requirements and is unrivalled in this segment: there are three wheelbase, four length and three height variants, rear axles with single, twin or super-single tyres, gross weights now ranging from 3.0 t to 5.5 t plus numerous body, equipment and drive system variants ex factory. The portfolio is rounded out by an effective management of external body and conversion solutions. These are produced by certified body specialists and converters. The Sprinter is also perfect for special-purpose bodies. The chassis is available with a cab, with a crewcab and as a chassis with cowl, i.e. without a cab. There is also the low frame chassis, unique for vans with rear-wheel drive: in this case the frame is lowered by 205 mm behind the cab. Comfortable cockpit, high level of safety Another of the Sprinter's outstanding attributes is its spacious, comfortably appointed cab. Mercedes-Benz has continuously improved and refined the cab over the years, and also constantly upgraded the standard equipment. The Sprinter is not only comfortable, its driver and passengers also feel safe when on board. Safety is priority number one for the Mercedes-Benz Sprinter. This encompasses the whole range from driver-fitness safety thanks to outstanding ergonomics to car-like handling characteristics and passive safety features. Avoiding accidents is paramount: the first generation already set standards for active safety back in 1995. Since then the Sprinter has been the uninterrupted trailblazer in this discipline – most recently with five new assistance systems in the new Sprinter launched in 2013. With the Sprinter, safety technology has also become a sales argument in the van sector. Solutions range from Crosswind Assist to COLLISION PREVENTION ASSIST, Blind Spot Assist and Lane Keeping Assist through to High Beam Assist. The Sprinter crewbus now has more seats For share taxis, school transport, sports clubs and regular rural bus services, the number of seats in the classic Sprinter crewbus sometimes proved to be inadequate. A Sprinter crewbus with extra seats now closes the gap. At 7.3 m in length and with a high roof, it is based on the extra-long version of the panel van. There is a model available with 16 passenger seats (Sprinter Tourer 16+1, 4.6 t permissible gross vehicle weight) and another with 19 passenger seats (Sprinter Tourer 19+1, 5.0 t permissible gross vehicle weight). From the interior trim and ceiling to the seat covers, the interior corresponds to that of the familiar Sprinter crewbus. Passengers enter the Sprinter through the sliding door, which is supplemented by an electrically-powered step. Depending on the field of application, the Sprinter can be supplied either with seats only or with a separate luggage compartment as an option. The seats have adjustable backrests as standard. They are optionally available with a rugged artificial leather cover instead of fabric. What is more, the Sprinter can be equipped with air conditioning in the passenger compartment as well as luggage racks including air ducts, ventilation nozzles and reading lamps. The Sprinter is suitably powered by the four-cylinder CDI engine rated at 120 kW (163 hp). As an alternative to the standard six-speed manual transmission, there is an automatic transmission with torque converter. Sales and service are provided through the Mercedes-Benz Vans network. An extra variant with a gross vehicle weight of 5.5 t Sometimes a little more is needed. Courier, express and parcel services, logistics, the trades, service providers, construction companies, local authorities, fire and rescue services or bus companies – they all require maximum payload in order to master their given tasks as effectively as possible. The previous maximum permissible gross vehicle weight of 5.0 t for the Sprinter could therefore prove a little tight in these and other sectors. Till recently the solution was load uprating. Following individual examination of the body solution by Mercedes-Benz Vans, an increase in the permissible gross vehicle weight from 5.0 t to a maximum of 5.3 t was possible with a certificate of non-objection. The new solution for maximum payload is the Sprinter with a permissible gross vehicle weight of 5.5 t. This new weight variant from Mercedes-Benz Vans closes the gap between the brand's vans and its light-duty trucks. The Sprinter with a gross vehicle weight of 5.5 t offers the payload of a light-duty truck. At the same time, it benefits from the convenient entrance, seat positioning and driving dynamics of a van. As such, the new version of the Sprinter is ideal for small and medium-sized companies in the trades and for industrial use, for fleet customers in the areas of parcel services, car rental, trade and commerce, and for the emergency services. 5.5 t variant: the Sprinter with a gross vehicle weight of 5.0 t provides the technical basis The Sprinter with a gross vehicle weight of 5.5 t is based on the components employed to date for the 5.0 t variant. In view of the Sprinter's robust basic design, there was no need for the engineers to develop a new chassis or a new frame. Rather, they exploited the potential offered by the existing self-supporting integral frame. Modifications to the bodyshell are restricted to the front end. These primarily concern stiffening, new consoles bolted onto the damper struts, reinforcements and additional welding spots on the strike plates of the longitudinal frame members. In adapting the chassis and suspension to the higher permissible gross vehicle weight, the Mercedes-Benz engineers had recourse to an excellent stock of Sprinter components, comprising springs, shock absorbers and stabilisers for high weights and loads. The higher permissible gross vehicle weight is accompanied by a rise in permissible axle loads. The maximum permissible front axle load on the Sprinter rises from 2000 kg for the previous reinforced variant to a level of 2100 kg. The maximum rear axle load increases from 3500 kg to 3600 kg. This provides the Sprinter with adequate axle load reserves, even in the event of uneven weight distribution. 5.5 t variant: payload rises by around 450 kg The increase in permissible gross vehicle weight from 5.0 t to 5.5 t benefits the vehicle's payload which rises by around 450 kg on all variants, thereby attaining a record level in certain vehicle configurations. The Sprinter as a chassis with cab achieves a very substantial load-bearing capacity of around 3460 kg. As a panel van with standard wheelbase, the Sprinter with four-cylinder diesel engine attains a payload of up to 3150 kg – no other panel van in this weight class is able to carry a higher load. With a permissible gross vehicle weight of 5.5 t, the Sprinter as a chassis is more than ever the prime choice for bodybuilders who place great emphasis on payload. As a chassis with cab and a long wheelbase of 4325 mm, for example, the Sprinter is able to carry conversion solutions of up to 5023 mm in length and 2488 mm in width when making full use of the permissible overhang of 2200 mm. 5.5 t variant: low cargo space sill, convenient entrance, high comfort In contrast to light-duty trucks, the Sprinter with a gross vehicle weight of 5.5 t is also available from Mercedes-Benz as a panel van in numerous lengths and heights. In unladen state, the panel van's cargo space is only around 700 mm above road level, making it easily accessible for loading and unloading. The same applies to the pickup which is available ex factory. The pickup's load area in empty state is only 1012 mm above the road. Bodybuilders benefit from a favourable level for the top edge of the frame, approximately 780 mm above road level. This firmly sets the Sprinter apart from light-duty trucks as well as other vans with a conventional frame design. The Sprinter additionally benefits from its design as a short-nosed vehicle. This results in a convenient, low entrance behind the front axle and a comfortable cab with a passenger-car feel and unhindered through-cab access. Additional merits are dynamic handling akin to a passenger car and high ride comfort thanks to the seat positioning behind the front axle. With a body width of only 1933 mm, the Sprinter panel van as a 5.5 t variant is as agile as its lighter counterparts and slips effortlessly through narrow spots. There is also news on the Sprinter's core segment: the variants with a permissible gross vehicle weight of 3.5 t are now optionally available with springs made of glass-fibre-reinforced plastic on the rear axle in place of steel springs. This choice reduces the weight by up to 12 kg and increases the payload accordingly, depending on the chosen equipment. A glass-fibre-reinforced plastic transverse leaf spring has been deployed on the front axle of the Sprinter since the first generation. Euro 6/VI emissions level for all models, modified designations As a world first in the van segment, the Mercedes-Benz Sprinter has optionally been available with diesel engines complying with the Euro VI emissions level from the summer of 2013, the V6 even featuring this Euro VI technology as standard. Mercedes-Benz has now switched the entire Sprinter range in Europe to Euro 6/VI. This means to minimise emissions all diesel engines now feature SCR technology with AdBlue injection. This is an effective form of exhaust gas cleaning. To coincide with this change, Mercedes-Benz has modified the model designations. The previously employed BlueTEC designation for the Sprinter with diesel engines complying with emissions level Euro 6/VI has been replaced by the familiar CDI designation. More power and torque for the four-cylinder CDI At the same time, Mercedes-Benz Vans has adapted the Sprinter's power variants to its customers' changing requirements. The changes concern the two lowest engine variants of the four-cylinder OM 651 with a displacement of 2.15 l. The new entry-level engine variant now has an output rating of 84 kW (114 hp). This represents a substantial 20 percent increase in output and torque compared with the previous entry-level engine. At 300 Nm, the pulling power, which is important in daily traffic, approaches the level attained by the previously next-highest rated engine variant. This mid-range variant of the four-cylinder CDI engines has also undergone a marked upgrade, with output and torque both rising by around 10 percent to 105 kW (143 hp) and 330 Nm. As a result, the Sprinter boasts high torque in these two newly defined power levels. Peak torque is on tap from both engines at an engine speed of 1200 rpm, providing for high flexibility and tractive power even at very low revs. In combination with an unchanged rated speed of 3800 rpm, the Sprinter offers exceptionally good driveability and an unusually large usable engine speed range in both engine variants. These features also characterise the most powerful four-cylinder engine rated at 120 kW (163 hp). This engine remains on offer unchanged, as does the V6 CDI, which is without parallel in the van segment. The broad engine range results in a clear and logical constellation of four CDI engine variants complying with the Euro 6/VI emissions level. As previously, all of the engine variants are paired with the ECO Gear six-speed manual transmission as standard. The 7G-TRONIC PLUS automatic transmission with torque converter is available as an option. As an alternative to the high-traction rear-wheel drive, Mercedes-Benz offers the Sprinter 4x4 with manually selectable all-wheel drive and optionally with gear reduction in the permissible gross vehicle weight range from 3.5 t to 5.0 t. Mercedes-Benz Sprinter: diesel engines Vehicle model Cylinders/ displacement Output Torque 211/311/511 CDI 4 in-line/2143 cc 84 kW (114 hp) at 3800 rpm 300 Nm at 1200–2200 rpm 214/314/414/514 CDI 4 in-line/2143 cc 105 kW (143 hp) at 3800 rpm 330 Nm at 1200–2400 rpm 216/316/416/516 CDI 4 in-line/2143 cc 120 kW (163 hp) at 3800 rpm 360 Nm at 1400–2400 rpm 219/319/519 CDI V6/2987 cc 140 kW (190 hp) at 3800 rpm 440 Nm at 1400–2400 rpm Mercedes-Benz Sprinter: petrol and natural gas engines The Sprinter also remains optionally available in one petrol and one natural gas variant (choice of monovalent/bivalent). These are both based on a four-cylinder engine with a displacement of 1.8 l. Output (115 kW/156 hp) and torque (240 Nm) are identical. Vehicle model Cylinders/ displacement Output Torque 216/316/516 4 in-line/1796 cc 115 kW (156 hp) at 5000 rpm 240 Nm at 3000–4000 rpm 316/516 NGT 4 in-line/1796 cc 115 kW (156 hp) at 5000 rpm 240 Nm at 3000–4000 rpm No matter which transmission customers choose, the advantages are a wide ratio spread and dynamic starting with a high ratio in top gear for fuel-efficient, quiet, low-emission driving at high speeds. Maximum economy also means extremely long, wear-dependent service intervals of up to 60 000 km. Whether it is the engine, transmission, driven rear axle or the all-wheel drive, all components of the Mercedes-Benz Sprinter bear the Mercedes star – they are provided from a single source and are perfectly co-ordinated with one another. .
-
International Trucks Press Release / September 27, 2016 .
-
Truck-less freight system prototype introduced by Texas A&M
kscarbel2 replied to kscarbel2's topic in Trucking News
You're right of course, but this would......in theory, allow a trailer to "immediately" head alone on to its destination. It could/would be a faster door-to-door experience. -
Heavy Duty Trucking / September 23, 2016 Hankook has expanded its e-cube Blue trailer tire line with special steering and drive-axle threads designed for efficiency and fuel savings, the company announced at the IAA Commercial Vehicle Show in Hannover, Germany. The tire line is being released in Europe but the company has plans to bring it to the U.S. market in the future. The new tire product line is a long-haul system solution and with the new steering and drive axle versions, Hankook is presenting a complete lineup of low-rolling resistance tires. The e-cube Blue line enables fleets to gain and additional 8% of tire-related fuel efficiency and up to 55% more durability. The tread design, which is tailored for each particular axle position, also helps to further reduce fuel consumption and increase mileage without affecting dynamic characteristics such as braking and traction performance. Both central rib tread blocks of the e-cube Blue AL20 steering axle tires support each other through their interlocking design, which increases tread block rigidity and helps to reduce rolling resistance. The stepped main tread groove design gives extra support for each tread block side. Moreover, they provide straight stability and improved steering response. The largely closed tread design in the shoulder rib area ensures particularly uniform tire wear. The tread appearance of the e-cube Blue DL20 steering axle tires is characterized by a central 4-block design of the massive central rib. The offset arrangement of the individual tread blocks guarantees interlocking action on both sides and results in mutual support for very good traction performance while reducing rolling resistance at the same time. In addition, the horizontally arranged semi-deep extra sipes in combination with tie bars in the open shoulder block area further promote traction. The extra-wide contour of the e-cube Blue TL20 trailer tires supports a very high driving stability and optimizes wear resistance. The multi-sipes added in the central rib area prevent uneven wear without affecting tread rib stability. The closed 4-groove tread design provides lateral stability and also a very low rolling noise. All three e-cube Blue products feature a tread compound with highly structured carbon black molecules for high fuel efficiency. In addition, the complete e-cube Blue tire family also features all basic technologies of the Hankook e-cube product group, which uses Hankook's mixture process IMS (Innovative Mixing System). This results in an even distribution of carbon black and rubber molecules within the mixture. Together with longer mixing times at lower temperatures, this significantly increases the bonding rate between the carbon black and rubber molecules. As a result, e-cube tires produce less heat during driving. The patented Hankook Stiffness Control Contour Theory (SCCT) design technology provides an even distribution of pressure inside the tire and thus promotes more stability and less movement in the tire. This results in high carcass durability and offers customers very good retreadability and economy. .
-
I like the 10QK388 urethane lower pads for vocational applications, but felt the softer rubber 10QK36B was better for most on-highway.
-
Commercial Carrier Journal (CCJ) / September 26, 2016 Texas A&M University earlier this month unveiled a plan 18 years in the works for a truck-less freight movement system. University officials and Texas Gov. Greg Abbott introduced the Freight Shuttle System, an electric, elevated railway network that transports loaded trailers without the tractors from one distribution point to another, according to a report from Dallas ABC affiliate WFAA. The transporter can move 70,000 pounds of freight at 60 miles per hour up to a distance of 500 miles using two-thirds less energy than a conventional diesel truck, according to the university. The WFAA report adds that the Port of Houston Authority has said it is in the process of building a five-mile system, which can be extended up to 20 miles, linking two container terminals. Freight Shuttle International, a private corporation founded in 2005, has been funding the truck-free project and shares 17 patents with Texas A&M, the WFAA report states. . .
-
Commercial Carrier Journal (CCJ) / September 27, 2016 Daimler Trucks has issued two separate recalls that affect approximately 1,160 Freightliner and Western Star trucks. One recall affects 1,007 model year 2013-2017 Freightliner Cascadia trucks manufactured between Sept. 24, 2012, and May 27, 2015, equipped with compressed natural gas engines. The recall pertains to the location of the power distribution module on the trucks. Daimler says the module is mounted near the CNG fuel tank and may be sprayed with water and other contaminants from the road, causing it to short out. If it was to short out, Daimler says there would be an increased risk of fire, especially since it is located near the CNG fuel tanks. The company says it will begin notifying affected truck owners Nov. 7, and will relocate the module free of charge. The other recall affects approximately 156 trucks equipped with Conmet aluminum non-high capacity front axle hubs manufactured between March 15, 2013, and July 29, 2016. Daimler says the following trucks specify a front axle weight limit that could be higher than the hub capacity, causing the hub to fail and the wheel separating from the axle: 2014-2017 Freightliner 108SD 2014-2017 Freightliner 114SD 2014-2017 Freightliner Business Class M2 2014-2017 Freightliner Cascadia 2014-2017 Freightliner Coronado 2014-2017 Western Star 4700 2014-2017 Western star 4800 2014-2017 Western Star 5700 Daimler says it will begin notifying owners of this recall Oct. 27 and will replace the front axle hubs free of charge.
-
This is the North American market variant of the Knorr-Bremse model ST7 trailer disc brake (Germany's Knorr-Bremse acquired Bendix in 2002).
-
Fleet Owner / September 26, 2016 The new Bendix ADB22X-LT – the first Bendix air disc brake engineered specifically for trailers – is now available to the North American commercial vehicle market, the company announced. Bendix unveiled the ADB22X-LT in conjunction with Utility Trailer Manufacturing Company. The new brake “advances the design” of the Bendix ADB22X. Like the ADB22X model for tractors and trailers, the ADB22X-LT – exclusively for trailers – is produced by Bendix Spicer Foundation Brake (BSFB). “In the decade since Bendix introduced the first air disc brake to the North American commercial vehicle market, we’ve had many customers equip their trailers with ADBs; their positive feedback and effective on-road experience played a big part in developing the ADB22X-LT,” said Keith McComsey, director, marketing and customer solutions, Bendix Spicer Foundation Brake. “We put Bendix’s wide-ranging braking expertise to work to help meet the challenges presented in trailer applications, and the end result is an air disc brake that offers the advantages of lighter weight and more convenient servicing – while still performing at the high levels demanded in today’s trucking environment.” The Bendix ADB22X-LT – with a 23,000-lb. brake rating – weighs in at 40 lb. per tandem axle lighter than its companion Bendix ADB22X air disc brake. “Lighter wheel-ends deliver increased payload capacity and value for trailers – such as refrigerated units – particularly sensitive to brake weight. Lighter weight wheel-ends can also help a fleet significantly improve its overall fuel efficiency,” according to Bendix. “Though the ADB22X-LT has been specifically designed for trailer use, it’s built on the same proven, successful platform as the ADB22X brake,” McComsey said. “In terms of uptime, that means the two brakes share replacement wear items, which helps to streamline maintenance and training plus reduce inventory requirements. In addition, the same skill sets fleet technicians use for installing and maintaining the ADB22X are equally applicable to the ADB22X-LT, making it a great candidate for installation by trailer builders. That’s a real cost-saver when compared to axles with preinstalled brakes.” The Bendix ADB22X-LT offers the same 5-year warranty as the ADB22X air disc brake. “Our ongoing dialogue with fleets reinforces the growing interest in air disc brakes as more operators understand their impact as a strong contributor to help drive lower total cost of ownership,” Bendix Spicer Foundation Brake president Eddie Wilkinson said. “That’s true of trailers as well, where increasing numbers of carriers are choosing this superior technology. We’re proud to bring the industry a second high-performing air disc brake, with unique advantages for trailers. And we’re honored that Utility – which shares our commitment to safety, performance, and value – is the first to make it available.” For more information about the Bendix ADB22X-LT trailer air disc brake, call 1-800-AIR-BRAKE. .
-
Fleet Owner / September 27, 2016 Every other year, global truck manufacturers gather in Hannover, Germany for a celebration of commercial vehicles now known only by its initials IAA. Spanning over a dozen buildings, the displays range from the smallest components to the heaviest haulers. Current products in bright graphics mix with flashy hi-tech concept vehicles during two days of press conferences for a global media audience followed by crowds of truck buyers and tire kickers. Here are just a sampling of IAA 2016's highlights. Slide Show - http://fleetowner.com/equipment/walking-iaa-2016-worlds-largest-truck-show#slide-0-field_images-201751
-
In the days of Mack Trucks, we sourced our trunnion pads (and all rubber insulators) from a quality supplier called Lord. http://www.lord.com/industries/commercial-vehicles/truck/cab-suspension However, I suspect Volvo long ago shifted to a cheaper supplier.
-
When you called Watt's Mack (provider of the BMT website) at 888-304-6225 and asked for a 222GB119C oil fill cap assembly, what did they say?
-
US [officially] spends $8.1 billion a year on fossil fuel subsidies
kscarbel2 replied to kscarbel2's topic in Odds and Ends
US and China release fossil fuel subsidy peer reviews The Guardian / September 20, 2016 The world’s biggest polluters have released their fossil fuel subsidy peer reviews and the obstacles to reform are clear: the US will wait on Congress, while China will wait on China. The documents, released on Monday by China’s G20 presidency, reveal the long road ahead. The G20 has commited to eliminate “inefficient” subsidies for coal, oil and gas in the medium term and the G7, of which the US is a member, has tightened the timeline to 2025. Of 16 policies marked for elimination by the US, all but three concluded with the sentence: “The United States Congress must pass enabling legislation for this proposal to become law”. Since 2010, the Obama administration has put forward 11 proposals to eliminate fossil-fuel subsidies. None have yet passed the house. In a pointed observation about the drawbacks of the US political structure, a review panel of officials from China, Germany, Mexico, and the Organization for Economic Cooperation and Development (OECD) noted: “A result of this system is that political processes can only happen if a sufficient number of citizens are informed about the case for reform and are motivated enough to express their views to their representatives in Congress.” The reviewers called upon the administration to deliver an “effective communication strategy” to convince constituents of the need for subsidy reform. The US subsidies identified for culling included a $52 million excise exemption for tar sands, the most carbon intensive source of oil. Like many of the subsidies, the exemption is earmarked for a cut, but waits on the approval of the Republican-controlled Congress. The review process worked from a definition for subsidies similar to the OECD’s. The argument over how subsidies are defined is vexed. For example, the IMF believes they should account for the extra burden on public health systems caused by pollution. This leads them to estimate the total public spend on fossil fuels to be around $5.3tn each year. The OECD’s narrower definition estimates it to be $160-200bn. -
US [officially] spends $8.1 billion a year on fossil fuel subsidies
kscarbel2 replied to kscarbel2's topic in Odds and Ends
U.S., China peer-reviewed reports lay out huge subsidies for fossil fuels Green Car Reports / September 22, 2016 Critics of the renewable-energy industry argue that it's unfair that energy sources such as wind and solar often benefit from government subsidies. But the volumes and amounts of subsidies received by the fossil-fuel industry are substantial, as new analysis shows. In December 2013, the U.S. and China announced plans to undertake a reciprocal peer review of their countries' fossil-fuel subsidies. The results of those studies, released this month at a meeting of the G20 nations, show that the U.S. and China provide around $20 billion in subsidies to the fossil-fuel industry each year. The U.S. report (pdf) identified 16 "inefficient" fossil-fuel subsidies for exploration, development, and extraction of fossil-fuel sources that could be phased out or reformed. The Chinese report found nine subsidies for similar activities, but also included subsidies that benefited specific groups of users, such as fishermen and taxi drivers. All told, subsidies were estimated at $8.1 billion annually for the U.S., and $14.5 billion for China. In addition to the listed subsidies, the U.S. report also took note of related government spending that benefits the fossil-fuel industry. It noted that while subsidies for the bulk transportation of fossil fuels by rail or barge were not specifically identified, much of the infrastructure that supports these activities receives at least some taxpayer funding. It also noted that the cost of maintaining the U.S. Strategic Petroleum Reserve—the world's largest emergency supply of crude oil—is borne entirely by the government, not by the oil industry itself as in other countries. Only one fossil-fuel subsidy—the Low Income Home Energy Assistance Program (LIHEAP)—was not marked "inefficient" by reviewers, and thus escaped a recommendation for elimination or alteration. The U.S. has an incentive to cut the subsidies deemed "inefficient," at least in theory. In 2009, the G20 nations agreed in principle to phase out "inefficient fossil-fuel subsidies," and the smaller G7 group set a deadline of 2025 at a meeting in Japan back in May. But cutting most U.S. subsidies will require Congressional legislation, something that seems unlikely to happen any time soon given the current heated political climate in Washington. -
Autoblog / September 27, 2016 That $7,500 that the US federal government provides in subsidies for each new electric vehicle? That may be small potatoes compared to the perks two of the world's largest governments are giving to Big Oil. Of course, estimates depend on who's doing the counting. The US and China in late 2013 both agreed to conduct reciprocal peer review reports of how much each government was funding the fossil-fuels industry, and not surprisingly, those numbers are pretty huge. Specifically, China funds fossil fuels to the tune of $14.5 billion a year, while the US provides $8.1 billion a year in Big Oil perks, Green Car Reports says. The numbers were released in a report that was recently presented at the G20 nations conference in Hangzhou, China. More tellingly, many of such funding activities were classified as "inefficient" examples of upstream activities such as exploration, development, and extraction of fossil fuels. The 50-page report can be found here. The US subsidy estimate dwarfed an estimate released by the New York Times last month. Citing the Council on Foreign Relations, the Times said the US spends about $4 billion on oil subsidies a year. But those numbers are downright conservative compared to a 2013 study from the Earth Policy Institute, which is obviously going to take a pro-green approach to things. According to that report, global governments provided $620 million worth of fossil-fuel subsidies in 2011. About 85 percent of that total was geared towards consumption by providing artificially low prices for the end user. To put those statistics into further context, a Los Angeles Times report estimated last year that Elon Musk's Tesla Motors and SpaceX, and SolarCity (where Musk is chairman) had taken $4.9 billion in subsidies since they'd been in business.
BigMackTrucks.com
BigMackTrucks.com is a support forum for antique, classic and modern Mack Trucks! The forum is owned and maintained by Watt's Truck Center, Inc. an independent, full service Mack dealer. The forums are not affiliated with Mack Trucks, Inc.
Our Vendors and Advertisers
Thank you for your support!