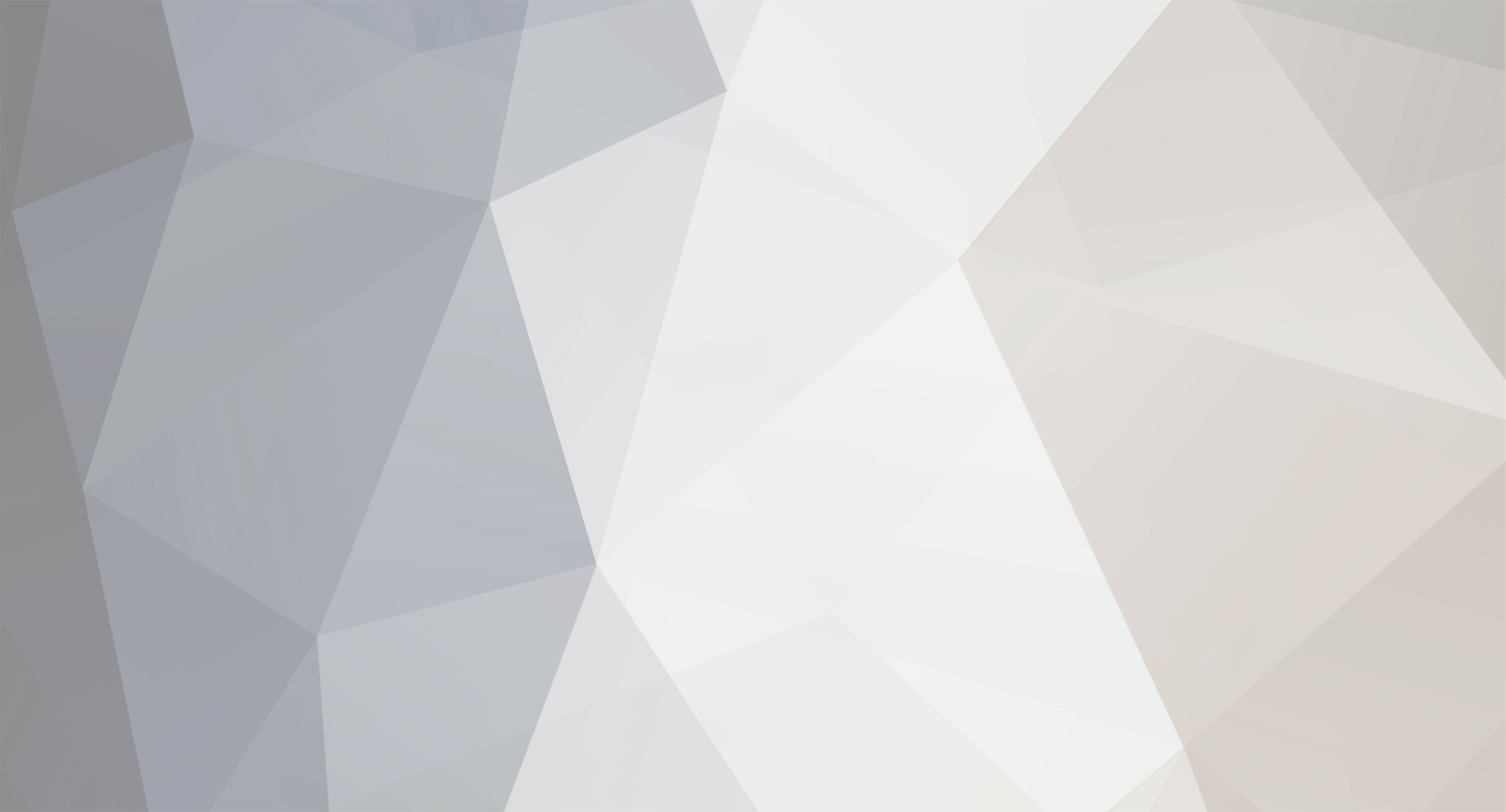
theakerstwo
-
Posts
3,816 -
Joined
-
Last visited
-
Days Won
7
Content Type
Profiles
Forums
Gallery
Events
Blogs
BMT Wiki
Collections
Store
Posts posted by theakerstwo
-
-
Did you try the mack dealership? I got the same thing about 1 year ago.I am in need of door locks w/ keys and the retainer clips for the driver and pass. doors on my 85 R model anyone know where I might aquire these? -
I have seen that done many years ago when the engines had a ring break in problem even seen fine dust off of top of stove used. glennWhat is the sea foam that you use. When we used to have this problem from excess idling in a paddock loading bags of potatoes. we used to drop the oil out and do about a thousand miles with Castrol hydraulic oil in the motor. This used to bed the rings in again. The other way to cut the glaze was to put a couple of teaspoons of Bon Ami cleanser into the inlet manifold while the engine is running. You cant do this too often as it will wear the rings out. The old Caterpillar books used to describe this in detail. If your rings are totally gummed up, some of the newer additives would be better. Heavy work is the best cure.Michael.
-
hi hello does anybody know what year did mack stop using wedge brakes
I dont know when they went away but all i can say good deal We are all better off now.
But for real the shoes on them wil last for ever.I dont think you can wear them out because the shoes hardly ever though the drums. The adjuster are froze up before the shoes are wore out. glenn
-
Realy it is not a crush sleeve but a soild tube about 10 inches long that goes between the 2 brgs. and it sets the load from the factory and you set that nut up to about 450 and that is it .The pupose of it was so no bad adjustments can be made and the front axle had then to.I was concerned to whether some one had left them out.I have not been updated in any schools in about 4 tears so i did not know the late stuff .Yes they were on the otr trucks and started around 1998 i think.I have seen them left out but if you tighten the nut like the factory calls for then you burn a brg. glennOther than the self locking adjusting nut, everything is the same as a conventional wheel bearing setup.Run the nut up tight, spin the hub a few times, back it off, run it up tight again, spin the hub and back off the nut til you have the proper bearing adjustment, then make sure the lock nut has clicked into the lock position.
I've never run across one with a crush sleeve yet, but all the stuff where I work is 46,000 lb axles.
Is that crush sleeve used on the lighter OTR type axles?
-
That is what we did at freightliner and the tone wheel will set the clearance itself. Many times some one fogets to shove the sensor in when they get thru with it and the abs light come on and it will say too much air gap so you take a screwdriver and push it in all the way.In the past when ABS sensors gave problems we would push the problem sensor all the way into the tone ring while on a jack with someone turning the wheel. That often cleaned the sensor and ring solving the ABS code problem.Chuck
-
No Glenn, there is no spacer. The nut just goes right up against the outer bearing.
The inner part of the nut has a notch to engage into the spindle to prevent it from turning, and the tabs on the sides of the nut are connected to prongs that pop out and lock the threaded part of the nut to the inner part of the nut, keeping it in proper adjustment and preventing the nut from coming loose.
That's why it's necessary to use the right size socket and depress the tabs properly to remove the nut without damage.
On a freightliner with that axle there is a crush sleeve to set the brg. load and i would have though that would have been in the same set up you had.
-
Yesterday I happened to be doing a brake job and wheel seal replacement on a truck with 46k Meritor rears.
Here are some photos of the things described in my previous post:
Meritor wheel bearing adjusting / retaining nut. The tabs on each side are pushed in when the socket is placed on the nut, thereby unlocking the nut from the spindle and allowing it to turn.
On top of the spindle is the ABS wheel speed sensor. Sometimes when reassembling the hub onto the spindle, the sensor gets pushed back slightly. Once the hub is on and the wheel bearings are adjusted, place a .005 feeler gauge between the sensor and the notched ring on the hub, and put your finger behind the sensor and push the sensor against the feeler gauge.
Notice that there is an ABS sensor on the rearmost drive axle only. When reinstalling the hubs, make sure you put the correct hub (the one with the notched ring) on the axle with the ABS sensor.
This hub has the notched ring which allows the ABS sensor to detect wheel speed.
Is there a inter spacer between the brgs ? i didnt see the spacer in the photo should be a spacer with that set up.
That makes the brg. adjustment simple.
-
I have seen lines groww together inside from too much fuel additive use and it is the same as not having large enough lines.Well I got it figured out. feel kinda stupid but I guees thats the way it goes. I apparently forgot one fuel line when I was changing them, so I changed it today before work and it feels like a brand new truck. don't know what I am going to do with all that power now. It had to be the last line I changed but at least it's fixed. I want to thank all of you for your replies and suggestions very much. Thanks again, John -
It may be derating so you should have the codes read.
there should be a check engine light coming on if it is a active code in it.
-
Maxville, years ago Diamond Reo built tri-drives used for cement mixer chassis. I used to have sales brochures but thats a long time ago. I also have seen some of these trucks in a truck junkyard in eastern Pa. I know where they are (if still there). Could call and ask and if over that way I could possibly take pictures. Tandem B
I dont think they could raise 1 axle like he wants to do . I dont know how that is going to be done. glenn
-
If the axle nut is the single nut with two locking tabs then it is easy to do because that is the set up that has the spacer sleeve between the brgs. like a crush sleeve and you just tighten the nut up against the brg. and torque i think about 450lbs .Mack sure the lugs will lock because i have seen them broke and would not lock because some one did not know how to release the locks when taking off nut because they did not have the size socket that was needed.The first thing you need to do is get the proper size socket to remove the bearing adjusting/ retaining nut.Meritor uses a nut with 2 lock tabs that are depressed & released when the proper size socket is applied to the nut.
Trying to loosen the nut any other way will not work and will damage the locking mechanism causing possible wheel end separation in the future.
Once you get past that little difference, the procedure to change a meritor wheel seal is the same as any other make of axle.
Also, if the truck is 1998 or newer and has ABS, after you reinstall the hub, use a .005 feeler gauge to set the clearance between the ABS sensor and the hub.
Frequently these get pushed away from the hub when reassembling, resulting in too large of a gap, which causes the sensor to not provide a signal to the ABS, resulting in inoperative ABS, and the ABS warning light on the dash will be on if you do not re set the sensor clearance..
-
Adrian: Although it will be just a little bit louder, it will not be a ticket magnet due to noise. In the USA a muffler/spark arrester is required, (I believe) but most any turbocharged diesel engine is very quiet in operation through the exhaust compared to a natural aspirated model.
Rob
[/quote I can remember when the F models did not have a muffler from the factory and on the turbo hot side was printed muffling device, this was cast in the hot side. They were 4 inche and maybe 12 ft tall and i dont remember them as loud that was a endt673b but same almost as the 675. glenn
-
Yes, definitely!
The following story has nothing to do with sleeve removal, but points out that the ground should always be as close as possible to the weld area.
A company up the road from here found out the hard way about proper ground clamp placement when welding.
Evidently somebody put the ground clamp in a place where it allowed current to flow thru the main bearings. This caused burning and pitting of the bearings and when they started the truck, several of the main bearings spun.
Talk about expensive f--- ups!
Sure glad it wasn't mine!!!!!!
I have seen that same thing happen more than once.
-
Ok I was just reading an old Mack construction brochure from 1990 and it really bought a tear to my eye but it also peaked my curiosity. My questions are:
When and why did mack stop offering AWD trucks?
Did Mack also make their own front drive axle or was it 3rd party? Did it use bevel gears or U-joints for power transfer?
Also I never knew they made a rear PTO that bolted between the engine and tranny. Its called a "self contained, gear driven flywheel PTO". Anyone ever see one? Sounds pretty cool.
I saw a pto like that back in the 60s that had a adapter between the flywheel and crank and it had a flat cog belt around it and it cam out of the side of the adater to a pulley on the out side that whent to a cement mixer.
-
Wrap the journal of the crank with wet rags, then wrap the rags with several layers of aluminum foil before welding on the sleeve.
When the sleeve is out, remove the rags and wipe any moisture off the crank.
When welding a bead around the liner dont forget to put the ground clamp on the block becuase i have seen a deal done where the man grounded to the frame and now you can burn up other things and if if has a ECM then it should be unhooked.
-
My RD822 has power steering and a massive single steering box. The power steering pump is gear driven and the reservoir is full. When I try to make a sharp turn to the left, loaded or unloaded, the last two turns of the wheel prior to the stops are very difficult. Steering to the stops on the right turns is a breeze. I'm afraid I will get dizzy if I have to make all right turns on every trip!
What should I be looking for to fix this issue? The king pins took grease without problems, the truck only has 91k on it, I did not see any damage to any of the components on a visual inspection. I'm thinking it must be the hydraulics because it only happens when turning to the left and the engine speed does not make a difference to the effort required to get it to turn.
My Superliner was like this sometimes but I always thought that was because I took up the slack in the steering box. I've not made any adjustments to the steering on the RD yet. If I can get the left turns as easy as the right turns, I'll be happy.
Another thing that will cause the box to turn hard to one side is if a punp is weak and will not build enough pressure any time then when loaded one side of the turn could be harder.The reason is because in a steer box there is more squar inches of piston on the bottom side than there is on the top side and that is ok when you pump can build enough pressure when needed but if you are loaded and the punp will not put out more than say 600 or 800 psi then that will be something you will feel different from one side to the other. That is the reason you need a flowmeter to monitor the flow and pressure as you go thru the turn both way.If a piston ring is leaking you can monitor the flow sa it looses power.I lik to put a block of wood between the tire and wheel and block the movement as you monitor the flow and about 1000 rpm and if a piston ring is leaking you will notice the flow go up and the pressure go down .
Most pumps are about 6 gpm flow. If you are monitoring the flow meter and the flow goes down and the pressure goes down from one side read to the other side turn reading then you may say that the control valve is wore out and the on that box there it is not much you can do.
-
The name that is cast into the steering box is R.H. Sheppard Co. from PA. I did not see a tag or number on the unit at this time. According to the build notes from the Mack Museum, it is a 245-2204 steering unit 592s Shep-pwr(integral).
Where can I find service literature for this? I can likely do any repairs myself. I've done quite a bit with hydraulic systems but pictures and exploded views really help. I'm sure there is a specific set-up sequence to follow as well in order to get everything adjusted evenly.
The problem with trying to do any major repairs on the steer box is if it is not a adjustment then it is worn parts and you may not be able to buy those parts.I know i can buy the out put shaft or some call it the cross shaft and bushing or if it uses brgs. for a kw but freightliner do not sell ant thing much more than a seal kit but dont know about mack but the last mack rebuilt box i got was around 450.00. alot of the time the slck is in the control valve and that is the heart of it. But the was i set the stops and poppet valves is jack up front and backoff botl poppets and i am talking about adjustable poppets some a automatic set when you install but back to setting poppets. Set you axle stops both at max to where the turn is about the same both ways and lock them and leve them along.you need a flowmeter to install inline on the supply line to the steer gear and then let the weight back down and then with engine running about 1000 rpm turn the steer wheel slow to one side and just as the axle stop comes in contact with the axle then you want see a pressure reduction and a flow to decress to about 25 to 50 psi on the pressure and i have used a 2500 psi pressure gauge only with out a flow meter and you will maybe be reading 500 psi on the gauge as the wheel is turned and the stop contacts the axle and you pressure should drop to about 25 to 50 psi. If it does not the screw in the stop till it reduces the pressure. If the pressure is reduced before the axle stop is contacted then back out the poppet screw. that will adjust the poppets. You sure have that engine painted good. glenn
-
As far as I know there is no way to way to get rid of the free play in those old boxes other than to replace the worn parts, most likley the worm gear, your best bet would be to try and find a good used one or have yours rebuilt, also check all the u joints,if there worn it will add a lot of free play.
If you are checking the free play with the engine not running then there will be some there. But with the engine runing there should only be little slack in there. The screw is to take out the slack between the input gear and the side gear.The best way to adjust is to break the drag link off of the pitman arm and then lossen the jam nut and turn the srew in a little and then turn the steering wheel from one stop to the other and turn screw in untill u fell a little drag which will be in the middle of the turning range and then just take that drag out to where you dont feel it much any more then hook up drag link and start the engine and if you still have too much slack then replace with a rebuilt. You cant take the slack out of the control valve in the box because it is wear in the sector control or worn bushing or brgs. on the cross shaft or out put shaft. These box should not be messed wih much any way because i have seen people pull then apart and loose something and then it ant no good no more. glenn
-
1
-
-
Dont know about that but i do know that you will get more power and run cooler on the exhaust with a air/air than a akter cooler. glennI have a 79 R-600 with a tip turbine engine that i would like to change over to air to air. I know i will need a different radiator and change the intake over. I have heard the hood don't fit after doing this , i was wondering if thats true and what will have to be done to make it work ? -
I finally got the E9 all back together and cozy with the frame. The test driving bobtail was fine except that it was slipping the clutch a little due to the torque and maybe some errant grease or oil on the flywheel. The clutch was re-adjusted and I took it out to pick up some equipment with my lowboy. While the trailer was empty, I had no problems but after I loaded up with about 25k lbs of equipment, the ride home went real bad, really fast. I'm pretty sure a couple of head gaskets let loose as I lost a lot of power and it started running very rough. I made it home, but it was a slow ride.
The only thing that I think may have gone wrong on my reassembly would have been the run-in and retorque procedure. I am a meticulous mechanic. I don't think that I missed anything on reassembly. The book was very vague regarding initial run-in procedures.
My questions:
1) What is the correct run-in procedure before retorque of the heads?
2) Should the engine be hot or cold during retorque?
I was so pissed with the whole deal that I parked the truck over the holiday week and left town. Now I have to face reality and get busy with it and determine if the head gaskets did go. If a simple retorque procedure can't fix the problem then I guess I will be yanking the motor out of the cradle, again
I am not happy with the machine shop that did the valve job as they banged the heads around and left scratches that cross over the fire rings. I think this led to the problem.
The block measured flat enough with the feeler gauges, as did the heads but both surfaces looked less than perfect. I think the motor had a bad gasket or two on it for a long time before I adopted it. Any suggestion besides finding another heart for the patient would be appreciated.
If you had i guess you are talking about head gaskets leaking or blowing you would hear them making a leaking copression noise like leaking compression to the out side. But if they blowed that soon your engine has a problem other than a torque procedure. I know old boys that dont take time to retorqe and dont have that much trouble. i guess you check the liner protrueion and the top of the liner were not damage.You probley would have compression in the coolant if you had a head gasket leaking bad enough to loose power.It i were you i would find the clyinder that are missing and that is easy and then pull the valve covers on that cylinder and then see if a push tube did not jump off. I my self let the engine get 5 to 10,000 miles on it then let it cool and retorqe by backing off one head bolt at a time 1 turn and retorque it and go to the next bolt and the reset valves. I have not worked on the E9 very much but the 864 865 was my days and the thing you dont what to do is start tear it down llok for the miss. find it firsr and go on it may be a missing injector ,i mean they may have been ok before you pulled it down but any thing can happen when you are around a little dirt that is on all trucks and who knows why a push tube kicks off but some time they do. I dont know what you did to it but you will find it when you start checking for a miss.
-
Most new trailers have gone to grease packed brgs. because they dont loose as many axles due to leaks and drivers not finding them in time. If you think about it there is not much more than maybe 2 pints of oil in a wheel so it cant leak too long or you may need a axle. The snythectic grease is so much better than the old grease but i can tell you that i was working on trucks when the oiler seals just started and it was noting to repack the front wheels on seem like ever truck that came in the shop and they tryed to do that ever 50000 miles and you would find many bad brgs if not all because that is something that is esay to overlook on mileage. I also remember when the drive axle had two wheel seal in each wheel and that was in the mid 60s.There was a grease packed inter seal which the brg was packed in grease and the outer brg run in oil from the rear end and there was a grease seal on the end of the axle shaft and sealing to the axle housing so the outer brg ran in oil.The old trucks used grease. Some were converted to oil which often performed better than the grease that was availible in that time period. Now many new trucks have returned to grease and even beyond that to non-sevicable front wheel bearings. I prefer to use grease on my older trucks. Less chance of leaks and the modern grease is many times better than what these trucks were designed to use.Chuck
-
Your right. glennI assume the benefit to the gear oil is that it is easier to service, (pull the plug, drain and refill) Versus taking the assembly apart, and repacking the bearings with grease?Dave
-
Most B's had greased bearings, but a lot of people changed them over to oil filled just for convenience...I'm not sure what set up is better though.
Stay with ythe oil which nis realy 85/90 grease but do keep a close watch on the oil level like every trip check the level before the flight. glenn
-
is the timeing off? i believe the maxidynes had diffrent timeing than the econdynes?
as far as not walking off the line easy, it could be a few diffrent things... low speed idle set to low, wrong timeing(low power) problem in the gov box... Maxidynes made more TQ down low so this was lost when you switched parts around to a 350 set up. the 350s make there power around 1450RPM and up they tend to fall on there face around 1350RPM.
if you say you have power loss up top and down low than i susspect timeing issues... that is if all your 350 parts are correct and your fuel and filters are fresh.
Mack sure that the stop cable is not pulled alittle bit when runing
Carrier Bearing
in Driveline and Suspension
Posted