- Popular Post
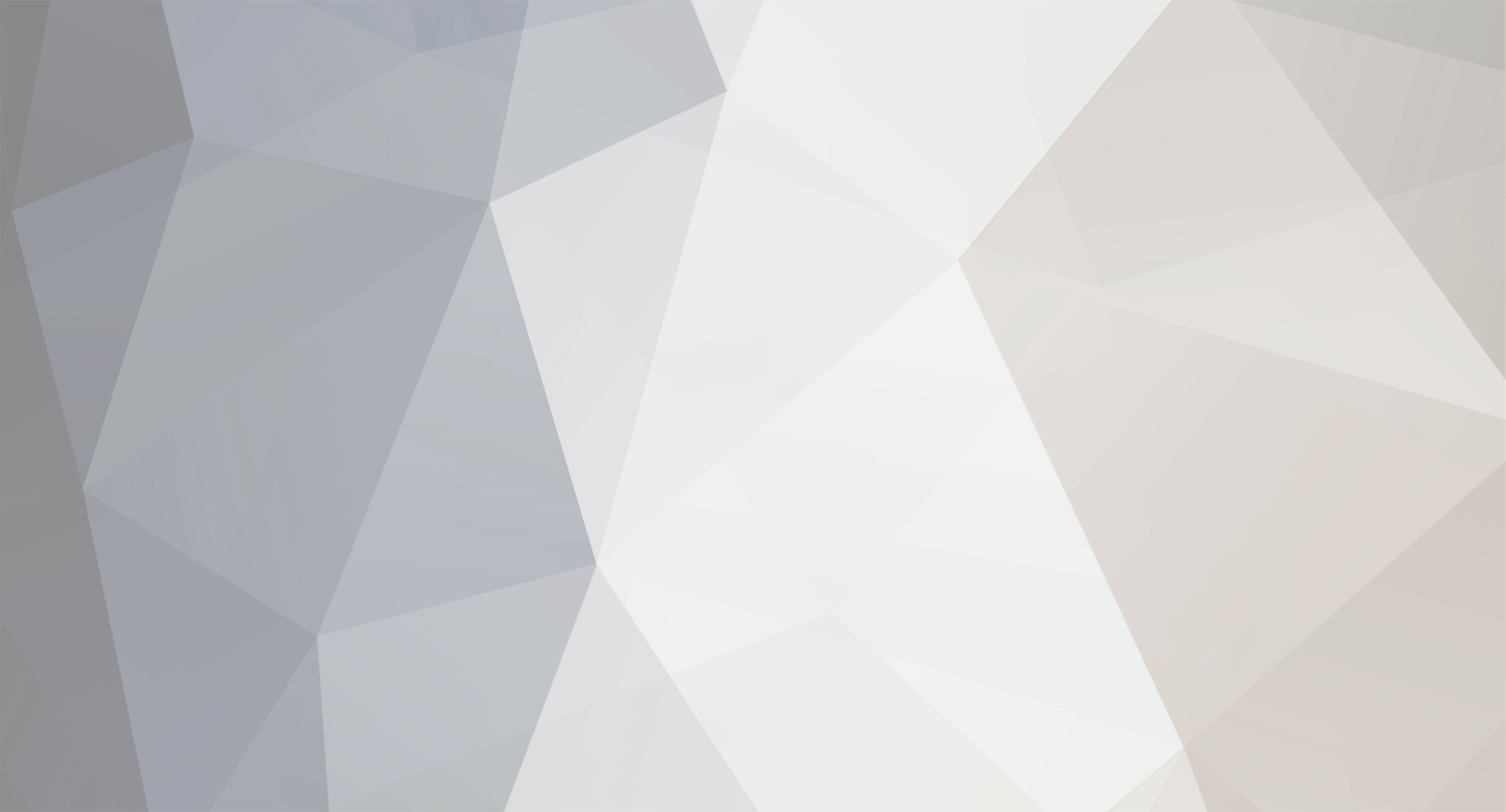
kscarbel
-
Posts
1,114 -
Joined
-
Last visited
-
Days Won
8
Content Type
Profiles
Forums
Gallery
Events
Blogs
BMT Wiki
Collections
Store
Posts posted by kscarbel
-
-
Bloomberg / July 16, 2013
Navistar International rose the most in more than two months after agreeing to let shareholders Carl Icahn and Mark Rachesky nominate two directors each to the truckmaker’s board.
Navistar shares rose 9.7% to $31.99 at the close in New York, the biggest one-day gain since May 3.
Icahn and Rachesky also agreed they won’t run a proxy contest at the company’s annual shareholders meeting in 2014, according to a statement. Navistar last year agreed to add three directors designated by Icahn Partners and Rachesky’s MHR Fund Management LLC. To make room for the fourth board representative, John Pope is retiring as a director immediately, Navistar said in the statement.
The change “likely puts greater control in the hands of these activist investors,” said David Leiker, an analyst with Robert W. Baird & Company.
"Icahn and Rachesky probably will increase their Navistar stakes to almost 20 percent each", said Leiker.
Rachesky and Icahn are among Navistar’s largest shareholders and Rachesky is a director. Each investor owns almost 15 percent of Navistar. Chief Executive Officer Troy Clarke, who has led the company since April, is trying to end losses and wants Navistar to concentrate on its main truckmaking business.
Navistar has surged 47% this year, compared with an 18% increase for the Russell 1000 Index.
-
Trailer/Body Buliders / July 16, 2013
Navistar Inc. has launched its heavy-duty International "WorkStar" vocational trucks powered by the company’s 13-liter engine with Selective Catalytic Reduction (SCR) emissions technology.
The WorkStar is the fourth heavy-duty International truck model to transition to SCR technology since December 2012.
“With the launch of the WorkStar with our 13-liter SCR engine, we continue to make great progress in our engine transition strategy and customers are benefitting from our expanded product line-up,” said (former Paccar executive) Bill Kozek, president North America Truck and Parts, Navistar. “We’re well positioned to continue our positive momentum and we are on schedule to complete the SCR transition in our remaining heavy-duty truck offerings by early August.”
The company’s portfolio of SCR-based heavy-duty trucks also includes the International ProStar, International PayStar 5900 Set-Back Axle and International 9900i—all available with the Cummins ISX15 engine. In addition, Navistar’s proprietary 13-liter engine with SCR was launched in the ProStar in April and is now available in the WorkStar. The remaining line-up of International heavy-duty truck models will transition to SCR emissions technology in a phased launch in the coming weeks based on volume and customer demand.
The WorkStar is designed to take on the heaviest loads and the most rugged jobs. The heavy-duty WorkStar model includes two variations, 7600 SBA (46” set-back axle) and 7600 SFA (30” set-forward axle). Both models feature a 113” BBC (bumper to back-of-cab).
Features include:
- Available high-visibility hood where front-end power take-off (FEPTO) is not required
- Available 4x2, 6x4 and 8x6 axle configurations
- Available from 365 hp 1,250 lb-ft torque up to 475 hp 1,700 lb-ft torque
- Huck-bolted frame and crossmember system with a number of frame-rail options for maximum durability
- Diamond Logic electrical system for greater reliability, improved productivity and lower maintenance costs
- Double-sided, galvanized steel cab for maximum durability
- Dual-powered steering gears and large front axle for excellent maneuverability
- Wrap-around panoramic windshield for best-in-class visibility where FEPTO is not required
- Optional Eagle interior with premium rosewood dashboard and easy-to-read ivory gauges or chrome bezel black gauges on instrument panel
- Easy-to-clean vocational floor mats and vinyl interior panels throughout the cab to improve durability
“With the launch of the WorkStar with our own SCR-based 13-liter engine, we continue to focus on meeting the needs of vocational customers by delivering innovative, best-in-class products for a wide range of severe applications,” added Kozek. “With great products, an extensive dealer network, and superior after-sales support, our International Truck severe service lineup continues to deliver for our customers.”
-
In 1976, Allison began development of a generator powered by the GT-404 gas turbine to supply power to the radar set and engagement control station of the U.S. Army Patriot Missile System. The program’s goal included placement of two 150 kW generator sets providing 100 percent backup in a single container to be carried on an Army 5-ton truck. Other goals included minimizing fuel consumption by the use of twin, rotating ceramic-disk regenerators and developing a reliable, multi-fuel capability without adjustment.
In 1978, Allison began the design, development and construction of five military specification gas turbine-powered generator sets. The completed generator sets were tested at the Aberdeen, Belvoir, Elgin and White Sands facilities with these results:
- Fuel consumption was reduced from 48 to 16 gallons per hour as compared with previous generators.
- A 0.1 percent frequency stability at rated load was obtained.
- Free-shaft starting to minus 50 F was accomplished without heaters.
- Multi-fuel capability was demonstrated on diesel, JP and gasoline.
- All reliability requirements were met.
- Sound level standards of less than 90 dBA were met.
In December 1981, Allison delivered an initial order of 200 generator sets to the U.S. Army. Thru 1997, over 2,000 GT-404 powered generator sets were delivered to-date for the Patriot system, which was employed during the Gulf War.
These generators have logged over 1 million hours of operation without any major problems.
-
1
-
Ford Motor Company also experimented with gas turbine powered inter-city coaches in cooperation with Continental Trailways. In Detroit, Ford installed a gas turbine in a 1969 Model 05 Eagle operated by American Bus Lines (unit 29511). In 1970, it went into regular service running from New York City to Los Angeles via St. Louis.
Unlike the Greyhound gas turbine buses where were paid for under grants from the US Dept. of Energy (Greyhound just supplied the MCI buses), the Trailways gas turbine Eagle was entirely privately funded by Continental and Ford.
The Continental-Ford project went better than expected. The initial engine actually proved too powerful, and a smaller gas turbine was subsequently installed.
How often do you see the signage "Turbine Power By Ford" on the rear of a Trailways bus?
-
1
-
-
Dept. of Energy/Dept. of Transportation
Gas Turbine Transit Bus
Demonstration Program
Program Plan
April 1978
One of the most promising advanced propulsion systems is the gas turbine engine. The gas turbine not only offers potential for reductions in noxious emissions and fuel consumption, but also could provide operators with improvements.
Development of the gas turbine engine as a potential power source for automotive vehicles began in the early 1950's. In1976, only three manufacturers in the United States, Chrysler Corporation, the Detroit Diesel Allison (DDA) Division of General Motors Corporation, and Industrial Turbines International (Garrett, Mack Trucks and KHD) were actively engaged in the development of small (150 HP to 650 HP) gas turbines that could realistically be considered engines for automobile, truck and bus use.
The Chrysler engine evolved as a passenger car engine. In 1962 this engine was extensively field-tested in 50 prototype automobiles. The development of this engine is continuing with U.S. Government financial aid, in areas that can best be described as "advanced technology."
The ITI consortium (Garrett, Mack Trucks and KHD) engine is in the 450 HP to 650hp range and is being designed as an eventual replacement for truck diesel engines. It is in the initial, unproven stages of development and prototype engines will not be available for 2 to 3 years. Production engines could not be available for several years after the prototypes.
Activities Involved in Developing Improved Gas Turbine Engines
Chrysler Corporation - ERDA Baseline Engine (150 HP) and Upgraded Engine (123 HP) under active development, 2-shaft regenerative
Detroit Diesel Allison - 300 HP, 400 HP and 500 HP, 2-shaft regenerative engine under active development for bus, truck, industrial application
ITI (Garrett/Mack/KHD) - Comprehensive program for truck and industrial applications 450-650hp range
The DDA gas turbine engine has been designed as an alternative for the diesel engines manufactured by that firm, and is currently developed to a state where volume production can be seriously considered. In addition to research and development engines, nearly 100 DDA gas turbines have been field-tested in trucks, transit coaches, intercity coaches, marine craft, and industrial electrical generator sets and air compressors.
Since 1972, test engines in 24 trucks of ten different brands have operated in widely divergent service in all parts of the country. In addition, eight Greyhound inter-city coaches powered by GT-404 gas turbines have operated throughout the country. In the most recent of these applications, the turbine engine has demonstrated greatly improved reliability and fuel consumption rates compared with earlier turbines. In fact, the fuel consumption in the inter-city coaches was nearly competitive with that of the diesel engine.
In the early 1970's, under the Urban Mass Transportation Administration (UMTA) Transbus Engineering Test Program, three DDA gas turbine engines were installed in the Transbus prototype coaches manufactured by the Truck and Coach Division of General Motors. This engine was selected for testing in Transbus because of the gas turbine's apparent advantages and demonstrated potential in heavy trucks. During this program the turbine engine demonstrated its potential as a viable transit coach powerplant by exhibiting the following advantages over the conventional diesel engine in transit coach application:
- Reduction of installed weight and volume
- Elimination of cooling radiator, fan, and
- attendant piping
- Cleaner exhaust emissions
- Lower noise level
- Reduced or low vibration operation
- Reduced lubricating oil consumption
- Good reliability
- Improved vehicle performance for power rating
- Greater engine braking capability
- Superior cold weather starting
Fuel consumption demonstrated in the program was higher than contemporary diesel engines. The extended periods of idle and extensive part-load operations, both inherent to transit coach service, accounted for a measure of the high fuel consumption.
However, improvements have been made since these coaches were evaluated and further improvements are scheduled for reducing brake specific fuel consumption (BSFC) in the transit coach duty cycle.
Because of the gas turbine's apparent advantages and demonstrated success in heavy trucks, an in-depth survey of gas turbine engine manufacturers was conducted to determine the suitability of the turbine engine for transit coach application.
The following sections trace the development of the only gas turbine engine found to be sufficiently developed to be considered for near-term volume production and subsequent application to transit coach service.
Gas Turbine Engine Development at Detroit Diesel Allison
For over 20 years, Detroit Diesel Allison both independently and with government assistance has been energetically developing gas turbine engines to compete in many commercial applications with piston diesel engines. Specifically, they have concentrated on applications in large trucks and buses, although field evaluation has included construction equipment, marine equipment, and electrical power generation units.
DDA's goals were to develop a practical, cost-effective turbine engine to meet the requirements of heavy vehicles. This program has resulted in a family of three engines covering the power range from 300 HP to 500 HP (SAE rating): The smallest of these engines is designated GT-404, and engines incorporating the latest design changes with improved performance have the -4 suffix.
The GT-404 gas turbine is a two-shaft, regenerative gas engine featuring a power transfer system. A rigid block assembly, constructed of cast iron, serves as the main structural support member for the engine. It houses, in a modular fashion, the burner, gasifier section, power section, regenerators, and the reduction and accessory drive gearing. The modular design allows easy service and unit replacement of the various sections. The engine controls are electronic and are remotely mounted from the engine block itself. The engine is available with a rated maximum output shaft speed of 2880 rpm.
The GT-404 engine's normal dry weight of 1750 pounds is approximately 650 pounds lighter than a comparable diesel engine, the DDA 8V-71, and its basic size is very similar. On an average vehicle-installed basis, this weight savings advantage is about 1,000 pounds, and the GT-404 can be installed in virtually any vehicle accommodating the 8V-71.
The GT-404-4 will have similar performance but with improved fuel economy and durability. Maximum torque is produced at power turbine (output shaft) stall (0 rpm) condition. With the high torque rise characteristic, fewer number of transmission gear ranges are required-generally five or less in trucks, and four or less in buses. With an automatic transmission, a torque converter is not required and a fluid-coupling can be used. The dynamic braking capability of the engine is equal to the rated power at maximum output shaft speed and is effective in each transmission gear range.
The GT-404 engine displays a considerable cost savings, consuming just one quart of lubricating oil per 20,000 to 30,000 miles compared with about 1 quart per 800 miles for a diesel engine in transit coach service . In addition, the turbine engine oil requires changing every 250,000 miles compared with 9,000 miles for the transit coach diesel engine.
The GT-404 engine emits less noise than a comparable diesel engine. Results of an exterior noise test on trucks, conducted to the SAE test standards, demonstrated that the noise level of the GT-404 engine is 11 dBA lower than a standard diesel powered truck. This 11 dBA lower reading represents nearly a 75 percent reduction in sound pressure over a diesel engine. Development effort is continuing toward a still further reduction of the noise level to meet future noise attenuation requirements.
Major pollution elements in transit coaches would be minimized with the GT-404 engine through highly efficient, low-pressure, continuous burning with large amounts of excess air resulting in almost 100 percent combustion.
The gas turbine’s exhaust odor is virtually undetectable, exhibiting only as light kerosene odor a t engine idle, and exhaust smoke is virtually undetectable. And it’s ability to start quickly at low temperature is superior to any conventional diesel powerplant. The GT-404 has demonstrated its ability to start, without aids, in temperatures well below 0º F. However, batteries must be reasonably well-charged and #1 diesel fuel must be used (since #2 diesel fuel begins to gel around +20º F).
The GT-404 does not require a water-based cooling system because it is internally cooled by the excess air passing through the engine and by the lubricating oil which is cooled through a small oil-to-air heat exchanger. The elimination of a water-based cooling system greatly decreases engine maintenance and downtime, thereby reducing a major maintenance cost area in transit coaches.
The gas turbine engine, in general, requires less maintenance than a diesel engine because of fewer wearing parts and almost vibration-free operation. All moving elements in the basic turbine engine are rotary in motion, compared with reciprocating components in diesel engines.
No water hoses or pipes, drive belts or other elements that tend to be unreliable are used. Use of self-cleaning inertial air filters, absence of a liquid cooling system and manifold exhaust system, extended brake life, and expected extended life of components will contribute to reduced maintenance costs and significantly increase vehicle availability.
The fuel system of the GT-404 engine can operate on a wide range of petroleum-based fuels including: #1 diesel, #2 diesel, heating oil, JP fuels, kerosene and gasoline. The diesel fuels are most commonly used because of their higher energy content and current ready availability. Gasoline is the least preferred fuel because the lead additive tends to deposit and foul the turbine, nozzles, and regenerators, thereby reducing engine performance. When synthetic or other fuels become available in quantity, the fuel handling and control system of the GT-404 can be modified to accommodate these fuels.
Detroit Diesel Allison Field Tests
DDA has manufactured approximately 100 GT series gas turbines for field evaluation in trucks, buses, boats, electrical power generation units and other applications. These engines include the GT-404 and GT-505 in both the -2 and -3 versions. Pilot models of the engine began going into service in 1972 for extensive field evaluation. The engines have been tested in 24 trucks from ten manufacturers, eight motor coaches from MCI-Greyhound, coaches from GMC Truck and Coach Division, Transbus prototypes, various watercraft and industrial applications.
Consignment engines were operational with Greyhound on the East Coast and West Coast, Binswanger Trucking in Los Angeles, Freightliner Corporation and Consolidated Freightways in Portland, Acadian Marine Rentals in New Orleans, Terminal Transport in Atlanta, Gardner-Denver in Quincy, Illinois, a Hatteras yacht operating in the waters of New Jersey, GMC Truck and Coach Division of General-Motors in Pontiac, Michigan, and Detroit Diesel Allison in its Indianapolis-based field-test vehicles.
The major effort at DDA in the development of the GT-404 engine has been directed toward heavy trucks. The field experience with turbine engines in transit coaches has been the Transbus prototypes, and several transit coach engineering models assembled by the Truck and Coach Division of General Motors. The most extensive coach experience with turbine engines is in the Greyhound fleet. However, it must be recognized that the duty cycle and service requirements for intercity coaches, such as those operated by Greyhound, are substantially different from transit coaches.
The eight GT-404 turbine powered Greyhound coaches, four MC-7s and four MC-8s, have logged well over one million miles since mid-1975 and several have been refitted with -3 engines. These particular -3 engines were capable of operating at 0.51 BSFC as compared with 0.54 BSFC of the -2 engines used in the Transbus prototypes. The last of the -3 engines with the latest burner improvements, and other developments, lowered the BSFC to 0.45. Even without the latest engine modifications, the fuel penalty sustained by Greyhound has averaged slightly over 1 mpg for the turbine engine compared with the diesel. The gas turbine engine also virtually eliminated engine overheating and other cooling system-related problems, which account for 50 percent of Greyhound's road failures with diesel engines. Brake life on the turbine powered Greyhound coaches was extended by more than 50 percent due to the engine's regenerative braking system. Elimination of engine vibration-induced cracks in refrigerant lines and fittings improved air conditioning system reliability in turbine powered coaches, and elimination of engine vibrations and reduction of the powerplant weight improved coach structural integrity. The largest number of engine problems Greyhound experienced with the turbine engines were with the various electrical controls.
Eleven Allison GT 404-4 gas turbine engines, and five HT740CT and six V730CT Allison automatic transmissions, were supplied to Greyhound for testing in 1981.
The turbine engine in the early years of production is projected to cost 20 to 25 percent more than the 8V-71 diesel engine. The projected production cost of a turbine engined transit coach, however, is projected to be $70,000 in 1976 dollars, or only 2.9 percent more than $68,224 for the typical diesel-powered coach currently in production.
DDA Engine Survey Conclusions
The operational cost impact analysis indicates that transit coaches equipped with the production improvement 'gas turbine engines (GT-404-4 PI) will be essentially equal in total operating cost to current diesel-powered transit coaches, without including any added value for:
- BSFC performance gain potential beyond 1983
- Multi-fuel capability
- Ability to accommodate future synthetic or
- alternative fuels
- Improved operational performance
- Conformance with environmental standards
- Perceived environmental improvement
- Reduced noise
- Reduced gaseous emissions
- Elimination of exhaust odor and smoke.
The tangible and intangible value/benefit of these attributes can, based on currently proposed regulations, lower the operating cost of a turbine-powered transit bus by well over 1 cent/mile.
If the current government regulatory trends continue into the 1980's, the above factors will become increasingly important and realistic monetary value could be assigned to these benefits offered by the gas turbine engine. The current higher fuel consumption of the gas turbine could continue to be a disadvantage of 'the engine, particularly if the cost of fuel continues to escalate at a faster rate than other costs. The multi-fuel capability and the ability to burn less expensive lower grade middle-distillate fuels may offset this disadvantage, especially if non-petroleum based fuels become readily available.
Beyond 1983, the fuel consumption of the gas turbine engine will continue to improve relative to the diesel engine. Increasing emission controls for diesel engines will result in a more complex engine, with escalating cost and declining fuel economy, while development of improved technologies in all gas turbine component areas indicate that gas turbine fuel economy will continue to improve. In fact, by the mid-1980's gas turbine fuel economy should equal that of the diesel engine at most speed/load ranges (with the exception of idle).
The major factors indicated by the cost impact analysis are the improved reliability and reduced maintenance costs of the gas turbine engine, offsetting the increased fuel consumption. The turbine engine used in the analysis was the DDA GT-404-4 PI model. This improved engine, with a rated MTBO of 10,000 hours, is tentatively scheduled for
volume production in 1983, which is the earliest reasonable date to expect widespread use of turbine engines in transit coaches.
The procurement cost of the turbine engine, as stated previously, will initially be about 20 percent higher than the contemporary diesel engine. As the production volume of the engine is increased, the cost of the engine should be reduced and may be comparable with the diesel engine. Cost of the diesel, moreover, may be adversely affected by additional equipment required as a result of environmental regulations. The anticipated fuel consumption improvements will be attained by increasing the TIT and possibly variable inlet geometry. The higher TIT will necessitate incorporating improved materials in the nozzles and turbine blades and may also require blade cooling. These changes and the additional complexity of the variable inlet mechanism will increase the cost of the engine somewhat, but it must be presumed that the competitive nature of the engine market will maintain the selling price of the gas turbine within a range commensurate with the advantages it has to offer for vehicular power.
-
1
-
The future for gas turbines appeared bright in the 1970s, particularly with the introduction of the Detroit Diesel Allison GT-404-4.
Information on these trucks is extremely limited, a but I’d like to share what I know.
The Astro 95 gas-turbine was powered by the General Motors developed GT-309 gas turbine.
It was equipped with GM’s 34,000 pound "Astro-Aire" rear air suspension, available from 1971 and offering up to 1,000 pounds in weight savings.
Throughout its 18-year production run, the Astro’s grille opening was never enlarged, and the gas-turbine Astro was no exception. GMC made the grille appear larger by using a painted section that matched the pattern of the truck's custom grille.
The truck's chassis equipment, including battery boxes, steps, fuel tanks, suspension, and even wheels, were all painted white, complimented by a chrome front bumper.The truck’s enlarged dual exhaust stacks were painted white to draw attention to the clean-burning nature of the truck’s gas-turbine powerplant.
Like many GM concept trucks such as the Turbo Titan III, the Astro gas-turbine had its own trailer for display and load testing.The U.S. Department of Energy (DOE) initiated a program in the mid-1970s at the Detroit Diesel Allison Division of General Motors to design ceramic components into the GT- 404-4 gas turbine truck engine. Testing included powering a truck on highways, city roads and the GM proving grounds, where the engine was exposed to extreme vibrational and shock loading on the Belgian-block and truck-durability road courses. Testing clearly demonstrated that properly designed ceramic components could survive under the most severe conditions for a typical vehicle.
GM said the emergence of low-cost, high-temperature ceramic components could allow the potential of gas turbines to be realized. Operating with ceramic components at turbine inlet temperatures up to 2350 F to 2500 F, GM said the GT-404 engine had the potential to offer fuel economy equal or superior to current diesel engines.
From 1974 to late 1977, Detroit Diesel Allison installed nearly one hundred GT-404 and GT-505 series gas turbines in trucks, inter-city coaches (Greyhound), municipal buses (Baltimore – RTS-II), fire apparatus (American LaFrance), marine and industrial applications to conduct field evaluation. Consolidated Freightways, Greyhound, Ruan Transportation, Terminal Transport, GM Truck and Coach and Freightliner participated.
Later in 1979, an “Astro SS” was built equipped with a General Motors GT-404-4 split-shaft regenerative gas turbine incorporating newly developed high temperature resistant ceramic materials. At 1,750 pounds, the GT-404 was approximately 650 pounds lighter than a comparable Detroit Diesel 8V-71. On a vehicle-installed basis, a 1,000 pound weight savings was realized, once reason being the lack of an engine cooling system.
- GT-404 300/310/325 horsepower
- GT-505 390/400 horsepower
- GT-606 475 horsepower
-
1
-
Diesel News / July 10, 2013
Less than two months after the overwhelming success of the Brisbane Truck Show, Cat Trucks has made it known it will not attend the International Truck, Trailer & Equipment Show, commonly known as the Melbourne Truck Show, next year.
In a recent press release Cat shared its strategic vision for product plans and future trade events: “Given the success of Brisbane Truck Show and the upcoming Perth Truck Show, Cat Trucks does not plan to participate in the Melbourne Truck Show as the investment would exceed the value of participating in three major trucks shows in nine month’s time. Instead, Cat Trucks plans to shift marketing resources into a broad range of more focused marketing initiatives, including a major launch for the CT630S scheduled to occur in the first part of 2014,” said the release.
“The Brisbane Truck Show sets the pace for the industry, and we were extremely pleased to be part of an event that broke previous records and where we were able to unveil our full 2013 product range,” said Bill Fulton, Cat Trucks managing director for Australia and New Zealand.
“We will be back in Brisbane in 2015 and we will be excited to showcase an interactive display that will feature new additions to Cat Truck model line up,” he stated.
“In conjunction with our dealer network, we have made the decision to not to proceed with Melbourne for the 2014 event,” said Kevin Dennis, General Manager, Sales and Marketing, for Cat Trucks Australia and New Zealand.
Cat Trucks who picked up two prestigious awards at the 2013 Brisbane Truck Show, which included the hotly contested “Outstanding Truck Manufacturers Display”, is electing to invest in a wider scope of marketing projects.
“When we promote our brand to the trucking audience, we always aim to make an impact, and we did in Brisbane, we will in Perth for the Perth Truck and Trailer Show later this month” Mr Dennis said.
“This decision to not partake in the 2014 Melbourne Truck Show will allow Cat to shift the focus onto a wide array of marketing initiatives, including launching the CT630S.”
According to the company the Cat CT630S is a light tare weight vehicle and one of the lightest in its class, and one of the shortest conventional cab trucks in the market to use a 15-litre engine.
Its shorter bonnet enables the Cat CT630S to operate comfortably in B-double / 34-pallet operations aimed at the line haul consumers for fleets and interstate trucking.
The CT630S is planned to be released in the 1st quarter of 2014 through the Cat dealer network.
____________________________________
CAT Trucks Australia displayed the CT630S short-nose tractor last year at the Melbourne Truck Show.
"The Australian market has been calling for a short bonnet conventional truck, and Caterpillar has listened to its customers," said Bill Fulton, managing director of Cat trucks in Australia and New Zealand.
"We are now offering a powerful, practical vehicle, the Cat CT630S, which has been developed for the Australian market and designed to meet the demands of the Australian road environment."
The Cat CT630S is a lightweight vehicle and one of the shortest conventional cab trucks in the market to use a 15 liter engine. Its shorter bonnet enables the Cat CT630S to operate comfortably in B-double/34 pallet operations, with superb visibility and dynamic handling. The aerodynamics of its integrated cab also provides linehaul and road train consumers with improved fuel efficiency, making the CT630S ideal for fleets and interstate trucking.
Like other Cat trucks, the CT630S represents the only brand of truck on the market featuring the world renowned Cat engine. Its Cat C15 engine delivers up to 550 horsepower and 1850 lb/ft torque. The engine is offered in an ADR 80/03 compliant option (Euro-5 / roughly EPA2007), which uses dual horizontal DPFs to eliminate the need for EGR or SCR for emissions compliance. As a result, fuel efficiency remains essentially the same, as it would be in an equivalent ADR 80/02 compliant vehicle. The CT630S will come with a standard four year, 800,000 km driveline coverage.
The CT630S is available in two versions: a sleeper cab with BBC measurement of 138" (3515 mm), and a day cab with BBC measurement of 112" (2855 mm). Both versions utilize a conventional hood design for improved fuel efficiency and ease of access. The high mount cab also provides increased under-cab airflow. Cab strength is compliant with ECE R-29, with three point cab mount and rear air cab suspension providing improved stability and comfort.
The sleeper cab version of the CT630S features an aerodynamic, integrated sleeper cabin, with a comfortable mattress (1850 mm x 660 mm) for sleeping and resting. The cabin also features an under-bunk storage allowance and side vent windows give added ventilation and comfort. The fully integrated and factory engineered sleeper cabin, through its structural integrity, not only offers the driver greater levels of comfort, but also offers the operator a truck which will stand up to the tough task of transport in Australia.
Both versions feature a robust 260mm x 92mm x 9.5mm frame, with an insert over the tandem axle and an upper frame tie for the high mounted cabin. The vehicle has a GCW of up to 198.000 pounds (90,000kg).
The CT630S comes equipped with:
- Updated Meritor RT46-160 rear axles, fitted with traction control. A differential lock is standard on the RR axle, as are alloy hubs, while differential locks on both axles are offered as an option.
- An Eaton RTLO20918B manual transmission comes standard, with an optional Eaton UltraShift Plus Transmission.
- LED headlights come standard and provide improved vision and longer life.
- Parabolic front spring suspension.
-
The GT-309 gas-turbine was designed to be a series of four engines with power ratings up to 2,000 horsepower.
Two significant technological advancements that distinguished GM's GT-309 gas turbine engine design were the regenerative system and “power transfer”.
The regenerator recovered energy from hot exhaust gases. Instead of being exhausted directly into the atmosphere, the gases passed through the rotating regenerators, discs which recover more than 90 percent of the exhaust heat. As they rotate, the discs transfer heat to the relatively cool air flowing to the burner.
Regeneration pays three principal dividends. First, it cuts fuel usage. A regenerative engine will use only 50% of the fuel of a non-regenerative engine in a comparable application. Second, it cools the exhaust gases. The exhaust is in the 200° to 500°F range, depending on load. Third, thanks to the regenerator, a muffler isn’t necessary.
While some earlier gas-turbine engines used regenerators, the GT-309's claim to uniqueness was “power transfer”, a patented GM development of the GM Research Laboratories and Allison Division.
Power transfer transmits a scheduled amount of power from the gasifier turbine to the output shaft, thus stabilizing the turbine inlet temperature over much of the engine operating range. A direct result is improved fuel economy at partial throttle, where the engine operates most of the time.
When the vehicle decelerates, power transfer couples the driving wheels to the compressor, providing engine braking power two to three times greater than that of a conventional diesel-powered truck.
The power transfer system of the 280 horsepower GT-309 gas-turbine engine provided over 1000 lb. ft. of torque at stalled output rpm. Power transfer allowed trucks to make faster and safer descents, controlling downhill speeds while extending service brake and wheel-end life.
Another function of Power transfer was to prevent turbine overspeed if the load suddenly is disconnected from the engine.
-
2
-
-
Leading up to the GT-304 gas-turbine powered Turbo-Titan III, the Chevrolet Division of General Motors built the 200 horsepower GT-304 powered Turbo-Titan I of 1956, and 225 horsepower GT-305 powered Turbo-Titan II in 1959. Despite the dramatic names, both of these gas-turbine testbeds externally resembled stock Chevrolet COEs (I suspect the test chassis were respectively a GMC F-series and DF-series “Crackerbox”).
However the Turbo-Titan III (XP809) introduced by Chevrolet in 1965 was altogether different. GM put the truck concept on display in 1966 at the 1964-1966 New York World’s Fair and said the truck was five to ten years away from commercial production.
Developed by the General Motors Research Laboratories, the GT-309 gas-turbine delivered 280hp at 4,000rpm (an upper shaft speed of 4,000 rpm, reduction geared downward from 35,000 rpm). Because turbine engines deliver their highest torque levels at stall (0 rpm), the turbine developed a maximum torque rating of 875 ft-lb (1,152 N.m) at idle.
An operational prototype, three of the advanced Turbo-Titan IIIs were built on modified GMC COE truck chassis (I assume DF-Series “Crackerbox”) and paired with a specially built aerodynamic side skirt-equipped 40-foot Fruehauf stainless steel trailer.
The tractor-trailer combination had a 50-foot overall length and GCW of 76,800 pounds.
The General Motors GT-309 was a conventional turbine including a compressor, gasifier, power turbine and regenerator. The gasifier was mounted on the same shaft as the compressor. The power turbine gear was connected to the output shaft.
A 6-speed Allison MT-40 automatic transmission with the torque converter and hydraulic retarder omitted was coupled to the turbine with a special aluminum adapter.
Chevrolet claimed the Turbo-Titan III’s turbine engine to be lighter, quieter and longer-lasting than conventional diesels (350,000 miles versus 250,000 miles), however fuel costs were higher.
Engine: General Motors GT-309
Horsepower: 280 @ 4,000
Torque: 875 ft-lb (1152 Nm) @ stall (0 rpm)
Engine Weight 1,425 lb
Specific Fuel Consumption 0.45 lbs per horsepower·hour
Transmission: Allison MT-40 less torque converter and hydraulic retarder
Front axle: 15,000 lb
Front Springs: 2 x 7,500 lb
Rear Bogie: Hendrickson 34,000 lb
Rear Axles: Eaton 2-speed (7.17/9.77) spiral bevel drive axles
Rear Springs: 2 x 17,000 lb
Frame: Ladder type, channel section side rails, 10-1/16 x 3-1/2 x 5/16”
Brakes: Full air, Rockwell 17-1/4 x 3-1/2 (front), Rockwell Stopmaster 15 x 7 (rear)
Wheels: Budd heavy-duty
Tires: 10.00-20 (front), low-profile 18-19.5 16-ply (rear)
The cab consisted of fiberglass-reinforced polyester exterior panels with a steel framework. Molded side chassis air fairings followed the cab’s futuristic styling theme and enhanced aerodynamics.
Left and right side sections of the side chassis air fairings, just behind the cab, tilted upward to provide access to dual batteries and other components.
An electro-hydraulic cab tilt system provided quick and easy access to the GT-309 gas-turbine engine.
Top-hinged power-operated swing-up door windows provided driver entry when the key was inserted into the door lock.
Triple rectangular headlamp assemblies in the left and right side engine air intake scoops, retracting into the sidewalls when not in use for an optimized aerodynamic profile.
The front turn signals were retractable, emerging from the front fenders only when actuated.
The rear 3-bulb turn signals operated in an inboard-out sequence, indicating motion in the direction you were turning.
A flat exhaust stack exited through the roof.
Inside the cab, "Astronaut Seats" with full headrests were mounted on each side of a center console.A T-handle controlling the 6-speed Allison transmission was mounted on a pedestal that pivoted forward and back along with the panel to provide drivers of all sized with an optimized driving position.
Full interior carpeting was included along with retractable seatbelts, air-operated windshield wipers, full tinted glass and air conditioning.
A 4-speaker AM/FM stereo radio and a 2-way telephone were featured for the first time in a heavy truck.
Mounted on a pedestal in front of the driver, the GM designed and engineered dual steering system replaced the conventional steering column and wheel. Twin dials mounted on a padded vinyl panel operated the platforms power steering. An auxiliary pump driven from the propeller shaft provided emergency usage if the main pump failed for any reason when the truck was in motion.One of the Chevrolet engineers who designed and drove the Turbo-Titan III had these comments:
"At the time Chevrolet was getting very serious about turbine engines. Although the Turbo-Titan III was highly experimental, the key advantages were power, fuel economy and cheap fuel (kerosene). The driveability was outstanding. However, the driver had to be extremely careful about monitoring turbine temperatures. The engine could not be used for braking as in internal combustion engines. I have no idea what happened to the vehicle. Since it was one of a kind, I assume they kept it in storage or scrapped it. As an added thought, the disc steering wheels (the truck did not have a steering wheel--it had two small discs in front of the driver), I had them installed on a passenger car for evaluation in normal driving situations. This type of steering system was very novel at the time and required a lot of attention to normal driving. I kind of liked it but I do not think anybody else did!"
When driving the Turbo-Titan III through Pennsylvania on the way to the New York World’s Fair, he encountered a large hill that other trucks had trouble climbing. The Turbo-Titan went over it "like nobody's business."After appearing in various auto shows, the three working prototypes entered service with GM’s own truck fleet. I don’t know what became of these trucks, an important piece of trucking history.
-
1
-
-
-
Of all the concept trucks of the 1960s, certainly the General Motors Bison III was the most futuristic of them all.
The Bison began life as Bison I (XP757) in 1959.
Bison II (XP795) incorporated an aerodynamic design resulting from extensive wind tunnel work, and featured a patented design for standardized containers.
A “see-thru” version of the Bison II (XP794) showed the regenerative gas-turbine system and other features.
General Motors put the Bison III (XP?) on display for the first time in 1964 at the 1964-66 New York World’s Fair, an aerodynamic gas-turbine concept truck designed to carry containerized cargo with utmost efficiency.
GM’s design goals were centered around the idea that freight loaded into globally standardized cargo containers could be automatically loaded, unloaded, sorted and stored by electronically-controlled equipment. At modern freight terminals, the containers would be transferred by automatic equipment to local delivery trucks.
The Bison concept had two General Motors developed GT309 gas-turbine engines rated at 280 and 720 horsepower located above the cab.
Part of GM’s “Futurama” exhibit, the Bison’s low cab forward design had seating for two ahead of the engine and wheels. Drivers entered the aerodynamic cab through a forward-tilting canopy. A cab entry step folded out as the canopy opened.
Drivers steered the Bison using two coupled hand grips on a console extending over the driver’s lap.
The Bison had a trailer locking device and a four-option steering arrangement that resulted in exceptional maneuverability in tight, urban environments.General Motors said the Bison was capable of pulling conventional semi-trailers with an adapter.
Combination integral jack and sand dispensers were located between the axles on each side of the truck to facilitate tire replacement.
The GM division logos on the trailer remind one of just how broad a presence General Motors once had.
Frigidaire home appliances were a technology and sales leader. Even today, it’s not uncommon to visit an older home and see an oven with the logo “Frigidaire – Product of General Motors”. GM founder William Durant invested his personal money in 1918 to buy Fort Wayne-based Guardian Frigerator Company, who’d invented the first refrigerator in 1916, and renamed the company Frigidaire.
AC was named after Albert Champion. He’d worked with the Stanhan bothers who’d founded Champion Spark Plug before being hired by William Durant to produce plugs for Buick.
United Delco (Dayton Electrical Laboratory), previously United Motors, was also formed by GM legend William Durant.
The fourth logo on the trailer is that of General Motors' Central Foundry Division. The division included 3 plants: Saginaw Malleable Iron, Danville (which was purchased from the Federal Government), and a foundry operated by the Harrison Radiator Division in Lockport, New York. This plant was closed in 1948 when a new Grey Iron Foundry in Defiance, Ohio was added. In 1949, an addition was added to the existing foundry in Danville, Illinois. In 1967, the Central Foundry Division celebrated its Golden Anniversary and was recognized as the largest foundry organization in the world, employing approximately 11,000 people.
.
-
1
-
-
Transport Topics / July 10, 2013
Engine maker Cummins Inc. said it is boosting its quarterly dividend 25%, reflecting its “confidence in the long-term prospects for the company.”
The dividend will be raised to 62.5 cents per share, from 50 cents, on September 3 to shareholders of record on August 22.
Cummins has “raised its dividend by a total of 257% over the last four years, while continuing to invest in products and our global footprint that will drive future profitable growth,” Chairman and CEO Tom Linebarger said.
-
Not to keep hijacking this tread but John Deere, AGCO, and CaseIH do the same thing with old and obsolete parts. Likely other companies do the same.
Yes they do. However I'm primarily talking about current production truck parts.
-
- Popular Post
- Popular Post
-
T100 number 4 (1959) was a 6x4 oilfield COE version called the “Tulsa” because it was shipped to the U.S. and exhibited at the 1959 Oil Industry Show in Tulsa, Oklahoma. It no longer exists.
The Tulsa’s Cummins engine was removed in 1962, and a 1000 horsepower Turbomeca Turmo IIIC gas turbine helicopter engine was experimentally fitted. Always the case with turbines, fuel consumption proved excessive and the Cummins engine was refitted.
-
2
-
-
- Popular Post
- Popular Post
-
- Popular Post
- Popular Post
-
Designed to run in Algiers and Chad (then French North Africa) to oil production sites in the Sahara desert, the massive Berliet T100 was the largest truck in the world when introduced in 1957.
Paul Berliet had been on a business trip and heard people complaining they didn’t have trucks strong and large enough to run deep into the desert for oil exploration. Upon returning to France, Berliet had a design for the first T100 on paper in eight days, and produced it in just nine months.
Cummins VT-12-BI 29.6-liter V-12 engines available in 600 and 700 horsepower ratings fed power to a Clark R1400 FS 4-speed semi-automatic transmission.
Four units were built, in both 6x4 and 6x6 configurations. It rode on Michelin XR 37.5x33 tires.
The T100 lost the oilfield market in North Africa when those countries began declaring their independence from France.
Paul Berliet, son of company founder Marius Berliet, was a sharp heavy truck man that increased his company’s sales tenfold from 1950 to 1974 when he sold out to Renault. In 1978 Berliet and Saviem were merged under Renault, forming Renault Vehicle Industries (RVI). The Berliet and Saviem brands were phased out two years later in 1980.
-
2
-
-
Who owns International trucks and what country?
To answer your question, Navistar International Corporation is an American truckmaker, incorporated in the United States and headquartered in Lisle, Illinois.
Paccar and International are America's last remaining heavy truck manufacturers.
-
I would love to buy a new 55 Chevy or a real Jeep CJ but times change and I don't care how much you complain about Volvo your never going to buy a new R model or Superliner. If Paccar or International would have bought Mack it would have been their truck with Mack on the hood like it is now. Like everyone said be glad there is still a Mack out there.
Today's truck customers in year 2013 wouldn't want a new 1987 spec R-model or RW-613/713 Super-Liner and I woudn't sell it to them. Today's trucking needs have evolved, and thus so has truck design.
Had Mack Trucks remained American owned and operated, the company's truck designs and technology would inherently have evolved to offer customers around the world a cutting edge trucking solution.
-
At the GM Heritage center lies proof that GMC pondered the production of an "Aero Brigadier".
GM Design proposed the first truly all-new GMC Brigadier, which would have debuted in 1988.
GM planned to use the then-new GMT 400 (C/K) light and medium truck cab.
However, once the decision was made to sell GM’s heavy truck unit to Volvo, GM focused on its GMT 530 medium duty program (Topkick/Kodiak) then under development by GM’s UK truck unit Bedford for introduction in late 1989.
Clearly, the Aero Brigadier influenced the GMC TopKick/Chevrolet Kodiak.
Note: 1987 was the last year of the GMC-badged Brigadier (the Series 60 was an option that year). Volvo GM Heavy Truck Corporation, the successor to Volvo White Truck Corporation. began operations in January 1988. For year 1988, the Brigadier was manufactured by GM but marketed by Volvo GM, and carried the WHITEGMC nameplate. In 1989, the Brigadier was replaced by the WG model.
Brigadiers were manufactured in Orrville, Ohio; Ogden, Utah (the former Autocar plant); and New River Valley, Virginia (the former White plant). Volvo GM developed and assembled several Brigadier engineering prototypes at their Greensboro, North Carolina headquarters, but nothing came of it.
.
-
The overall parts situation is an important topic that we don't speak anough about, and certainly one of the issues I have with Volvo.
Since acquiring Mack Trucks, Volvo have adopted a strategy/policy of marking up spare parts prices to "just below" the point where most customers will walk away.
Let's take a simple example. An AC belt used to be $3.00 to $4.50. Mack's cost as around $1.00. Mack covered their overhead and made a solid profit, and yet the customer received a fair price. But Volvo came in and decided that most customers would be willing to pay $9.00 to $15.00 for that AC belt. Anyone that has been purchasing Mack parts for many years knows exactly what I am speaking about.
The other day I needed a low air pressure sender. The Volvo/Mack dealer demanded an absurd $105, while the exact same Cole Hersee switch was available for just $7 at NAPA. This is a typical example of Volvo intentionally raping the American customer so as to improve their global margins. Mack Trucks didn't do business this way.
Mack Trucks wasn't selling the parts too cheap, rather they gave the customer a sound reason to shop at Mack's dealers rather than the will-fit parts house. But now Volvo has pushed customers out of the Mack dealers. No customers shop at Mack (Volvo) dealers for anything other than proprietary items they can't buy elsewhere.
Volvo's stick-the-customer strategy has been a poison pill to the service departments at the Mack dealers as well. Up to 80 percent of the service work performed is warranty now, because they are unable to be price competitive with customer and local shops. In the days of Mack Trucks, warranty repairs never accounted for more than 10 percent of shop work.
And Volvo's termination of Mack part numbers, replacing them with meaningless "Volvo global part numbers", has destroyed the once superior Mack parts system. The Mack part numbering system combined shear brilliance with simplicity. Easy-to-remember part numbers that told you exactly what that part was. This is why Mack parts people were the best in the world.
Volvo's randomly chosen impossible-to-remember global numbers represent nothing. It amounts to much more than a huge step backwards. Relating to Mack, the part number change to Volvo global part numbers is just plain stupid.
The Mack part numbering system was VASTLY superior to the dysfunctional Volvo system. The Mack veterans in parts operations told Volvo the change was a huge mistake, and most of them were shown the door for not willingly going along with the "new way".
-
I didn't see this posted already under "Trucking News".
-
Transport Topics / July 9, 2013
Volvo Trucks North America has begun a recall to of 23,003 units to deal with a potential clutch problem, the manufacturer advised the National Highway Traffic Safety Administration.
The recall covers 2007-2014 models of Volvo’s VAH, VHD, VNL, VNM and VT tractors. The recall was outlined in a letter from Volvo, whose U.S. headquarters is in Greensboro, N.C.
At issue is the potential risk of a crash because of a longer stopping distance if the clutch doesn’t disengage when the brakes are applied. No crashes or injuries have been reported in connection with the condition.
“Volvo considers this [recall] as a proactive measure to protect the public and Volvo’s customers from the risk of a vehicle crash,” said the letter from Tim LaFon, director of regulatory affairs. “Volvo has received 183 warranty reports and 155 field reports that may be associated” with the condition.
Volvo spokesman Brandon Borgna said the company declined to comment, referring Transport Topics to the NHTSA report.
Volvo identified the problem as the possible removal of a “micro switch” that “provided a redundant clutch disengagement signal.”
The micro switch is designed to instruct the (Volvo I-Shift) automated manual transmission to disengage the clutch in the event that the primary brake switch doesn’t do so.
The recall began July 2 with a message to dealers, and tractor owners will be notified of the recall by Aug. 25. Volvo said in its letter that the defect doesn’t affect the braking system.
According to Volvo, the company is evaluating potential solutions and will advise NHTSA when a decision is made about the specific repairs.
The company statement said the number of units with the micro switch issue isn’t known. Volvo first notified NHTSA of the potential issue in February.
The American “Chinese Six”
in Other Truck Makes
Posted
Yes America, we have built Chinese Sixes. A term coined in the UK during the 1960s, a Chinese Six is a twin-steer 6x2 tractor configuration.
Cole's Express of Bangor, Maine thought to create a tank/van, combining a tanker with a conventional 45-foot box trailer that was still within maximum length restrictions. The result resembled the dromedaries operated by Pacific Intermountain Express (PIE).
This 1964 GMC “Crackerbox” began life as a model DFX7009 spec’d with a 230 horsepower Detroit Diesel 6V-71 (naturally) and a 10-speed Fuller Roadranger transmission.
Introduced in 1959 and produced thru 1968, the DF series "Crackerbox" replaced the GMC "Cannonball" line.
Cole's new GMC was shipped to Hendrickson in Chicago (then known as the Hendrickson Motor Truck Company) which had patented the tandem-axle truck suspension in 1929. Hendrickson had developed a 22,000 pound twin-steer tandem steer axle design and begun sales in 1958 to International Harvester for their 8x4 VCO model COEs, and also to Diamond T.
After the first truck had been successfully modified, Cole's Express ordered three more.
The four trucks were shipped to Techweld of Burlington, Massachusetts for the installation of an 11-foot long, 3,300-gallon aluminum fuel tank. Initially a square tank was planned, but a rounded tank was finally chosen for greater strength.
The idea for the 3,300 gallon fuel tank was aimed at solving Cole’s northbound deadheading problem in Maine. With the tanks, Coles could deliver fuel oil and gasoline to customers on their way to northern Maine where the trucks would pick up potatoes for delivery in the south.
Although the Cole family also owned the Diamond T and Freightliner dealerships in Maine, they chose the GMC “Crackerbox” because its V-6 engine block was short, allowing for the longest possible fuel tank.
Typically, the trucks ran a 300 mile route from Portland through Bangor to Caribou.
Unfortunately, Maine revised the length regulation, stating that a dromedary-type tank had to be factored into the truck's overall length. This made the truck-trailer combination over length and illegal.
One of these innovative GMC 6x2s remains in existence and is on display at the Cole Museum of Land Transportation in Bangor (www.colemuseum.com). The museum also has a 1955 Mack D-42, formerly operated by St. Johnsbury Trucking in Vermont.