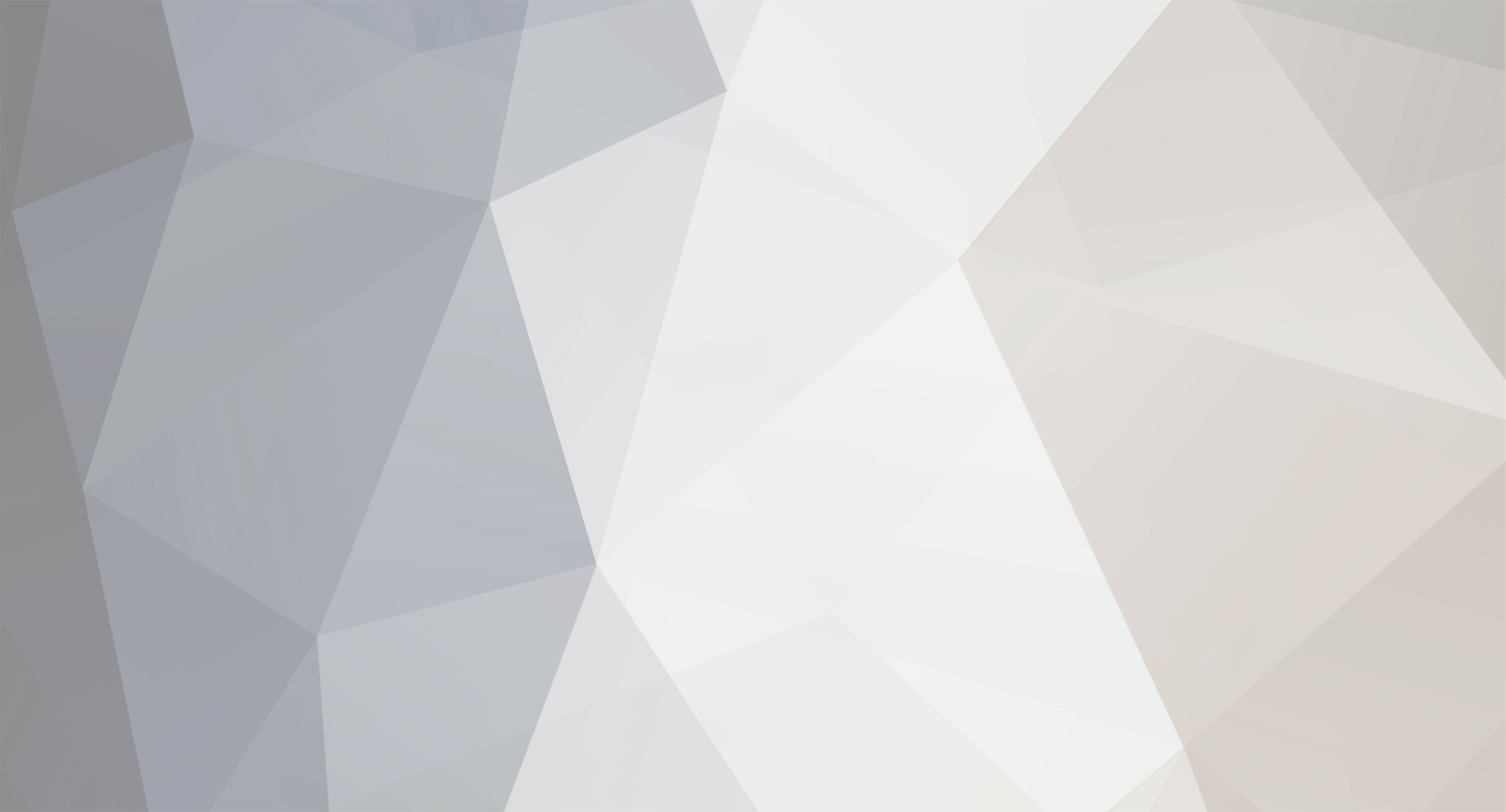
kscarbel
-
Posts
1,114 -
Joined
-
Last visited
-
Days Won
8
Content Type
Profiles
Forums
Gallery
Events
Blogs
BMT Wiki
Collections
Store
Posts posted by kscarbel
-
-
If your shift knob is the old style knob (the black cylindrical air shift knob), you can repair it with a Mack part-no. 14RC1131 repair kit.
-
Transport Topics / July 23, 2013
Paccar said Tuesday its second-quarter profit dipped from a year ago but cited “gradually improving truck sales and strong aftermarket parts.”
Net income slipped to $291.6 million, or 82 cents a share, from $297.2 million, or 83 cents, a year ago.
Sales and financial services revenue declined to $4.3 billion from $4.5 billion, Bellevue, Wash.-based Paccar said in a statement.
Paccar is the parent company of Kenworth, Peterbilt and Europe-based DAF trucks.
“Class 8 industry retail sales for the U.S. and Canada in 2013 are expected to be in the range of 210,000 to 230,000 vehicles,” said Executive Vice President Dan Sobic.
“Truck demand is being driven primarily by the ongoing replacement of the aging truck population and an improving housing sector. The truck market should benefit from projected economic expansion in the remainder of the year, particularly growth in auto production and construction activity,” Sobic said.
-
Let me toss a question in the ring.
I have my R688ST with 3 leaves front springs and Neway airride.
What shock absorber part number I should keep with?
To my big sorry Mack museum hasn't recognized my truck so I probaly have no chances about production record.
Or is it more question to Barry?
Your front shock is a 14QK366P1. Ask Barry what your rear shock is for that Neway.
-
Thanks.
And, by the way, the local Mack dealer shows the 14QK2100 in stock at a warehouse. He looked up the 14QK2100P1, and it was "superceded by" the 14QK2100. That would tend to support the "they are the same" theory, as an older number would typically not supercede a later number...unless they were the same part.
I hear you what you're saying. And I already said, a 14QK2100 and 14QK2100P1 are indeed the same thing. But in the days of Mack Trucks, only engineering might not use the P1 (the way the blueprints were typically written, and your truck's line sheet), whereas parts operations would always use the "P1".
But I have never seen a P1 suffix dropped even if the other P variations had been discontinued. If that's what Volvo has done, then no wonder the parts system is a convoluted mess now.
And Volvo wants $68 a piece for that shock? This is a great example of the Volvo stick-the-customer pricing I spoke of the other day. I could easily accept the $38 price, but not $68.
Since acquiring Mack Trucks, Volvo have adopted a strategy/policy of marking up spare parts prices to "just below" the point where most customers will walk away.
For example, an AC belt used to be $3.00 to $4.50. Mack's cost as around $1.00. Mack covered their overhead and made a solid profit, and yet the customer received a fair price. But Volvo came in and decided that most customers would be willing to pay $9.00 to $15.00 for that AC belt. Anyone that has been purchasing Mack parts for many years knows exactly what I am speaking about.
The other day I needed a low air pressure sender. The Volvo/Mack dealer demanded an absurd $105, while the exact same Cole Hersee switch was available for just $7 at NAPA. This is a typical example of Volvo intentionally raping the American customer so as to improve their global margins. Mack Trucks didn't do business this way.
Mack Trucks wasn't selling the parts too cheap, rather they gave the customer a sound reason to shop at Mack's dealers rather than the will-fit parts house. But now Volvo has pushed customers out of the Mack dealers. No customers shop at Mack (Volvo) dealers for anything other than proprietary items they can't buy elsewhere.
Volvo's stick-the-customer strategy has been a poison pill to the service departments at the Mack dealers as well. Up to 80 percent of the service work performed is warranty now, because they are unable to be price competitive with customer and local shops. In the days of Mack Trucks, warranty repairs never accounted for more than 10 percent of shop work.
And Volvo's termination of Mack part numbers, replacing them with meaningless "Volvo global part numbers", has destroyed the once superior Mack parts system. The Mack part numbering system combined shear brilliance with simplicity. Easy-to-remember part numbers that told you exactly what that part was. This is why Mack parts people were the best in the world.
The randomly chosen and impossible-to-remember "Volvo global part numbers" represent.......nothing. It amounts to much more than a huge step backwards. Relating to Mack, the part number change to Volvo global part numbers is just plain stupid.
The Mack part numbering system was VASTLY superior to the dysfunctional Volvo system. The Mack parts computer software was vastly superior to Volvos.
Mack veterans in parts operations stood up at meetings and told Volvo the changes were huge mistakes, and most of those experienced Mack veterans were shown the door.
-
1
-
-
So, if I understand you perfectly...
A 14QK2100 shock would have been the "original" version of that part. It would have no "P" on it. But, as soon as there was a different version, the new part would become a 14QK2100P2, and the "no P" part would become the 14QK2100P1. Is that the gist of it?
The reason I ask is that I can get a 14QK2100 for $68 apiece, and a 14QK2100P1 for $38 apiece. Pretty significant difference! So, as long as it truly is the same part... Ya' see?
On a side note, and in defense of some of the guys who have used non-Mack parts, I have had the Mack parts folks (on occasion) give me the vendor (TRW, Moog, etc...) part number for the Mack part. Remember, Mack doesn't make EVERYTHING they use. They make some. They have some made to spec. And, on occasion, they buy an already-existing part.
That's right, after additional variations are introduced, the plain number becomes a P1.
And often, engineering (responsible for the line sheets) would leave off the P1 even though there were more variations (because some blueprints were written this way), but in parts operations they always used the P1.
Something like a Cruise-Liner and MR rear cab latch (produced by Power Packer), 184QS39301A, had the "A" to denote an engineering improvement, but no P variation because there was only one version. And note the 5 digit Mack Western style part number, which carried on to the MR because the part was originally designed for the Hayward-production first generation Cruise-Liner.
Anyway, buy the $38 14QK2100P1s and you'll be all set to go.
No, Mack doesn't make everything they use. But the specifications handed down to the vendors are typically different than the will-fit vendor branded items. Mack used to have a Monroe all-makes shock absorber program, and the shocks were NOT the same as what Monroe supplied under the Mack part number, which was supplied exactly to the blueprint specs.
-
The GT-601 gas turbine was produced by Industrial Turbines International (ITI), a joint venture between Garrett AiResearch, Mack Trucks and KHD (Klöckner Humboldt Deutz AG) established in 1972 to produce purpose-designed gas turbines for heavy trucks.
Klöckner Humboldt Deutz had been producing gas turbines from 1956. In 1980, the KHD gas turbine unit was renamed KHD Luftfahrttechnik GmbH and sold to BMW Rolls Royce in 1990, now known as Rolls Royce LLC and a major producer of jet engines.
The GT 601 was a free-turbine all-metal engine with a fixed boundary recuperator. More than 7,000 hours of operation were accumulated, including more than 2,000 hours in highway trucks. These engines demonstrated the feasibility of fixed boundary recuperators along with superior torque compared to diesels of similar rated power, easy cold starting, and the ability to survive limited foreign object ingestion.
While the initial chose power range was 450-638 horsepower (335-476 kW) for heavy trucks, ITI later created a 550-750 horsepower (410-559 kW) engine range to better target the tracked military vehicle segment.
Installed in the experimental XM723 mechanized infantry combat vehicle (the forerunner of the Bradley fighting vehicle), the GT-601 was mated to a Detroit Diesel Allison X-300 four-speed automatic transmission with the torque converter omitted.
GT-601 Development History
1974 – Initial design work begins
1976 – Final design completed.
1978 – Production of early prototypes. Results proved the GT-601 to be highly reliable.
1979 – The first GT-601 underwent endurance testing in a Mack R-795S 6x4 tractor.
The U.S. Army Tank Automotive Research Development and Engineering Center (TARDEC) and ITI sign a one million dollar contract to identify gas turbine power as a viable powerplant for tracked military vehicles. Specific test programs were created for the U.S. Army’s XM2 infantry fighting vehicle and XM3 cavalry (scout reconnaissance) fighting vehicle, requiring a power increase to 750 horsepower.
1980 – Gas turbine truck testing (Mack Trucks) at the U.S. Army Yuma Proving Ground in southwestern Arizona.
1981 – A 638 horsepower GT-601 installed in a 45,000 pound XM723 mechanized infantry combat vehicle (MICV) underwent TACOM Phase II demonstration testing at the General Motors proving grounds in Milford, Michigan from August 17 thru November 5. to demonstrate the characteristics of a Garrett GT601 gas turbine engine mated with a Detroit Diesel Allison X-300 transmission without a torque converter installed. Virtually no engine-related problems were observed.
Combined with additional U.S. Army testing of the GT-601 in M2 infantry fighting vehicles, Mack 6x4 tractors, and M-48 main battle tanks, over 6,200 miles of feasibility study was done.
1982 – The GT-601 completed 1,000 hour qualification testing, and testing using multiple types of fuels.
1983 – The GT-601 powered XM723 underwent TACOM Phase III demonstration testing at the General Motors proving grounds in Milford, Michigan from January 4 through 18, March 24 through 30, and completed June 7 through June 9, 1983.
Conclusions:
- Vane Braking - The U.S. Army concluded that the distinct advantages of gas turbine “vane braking”, a feature unique to the GT-601, provides enhanced drivability as well as the ability to maintain low speeds on downgrades without vehicle brake application.
- Inlet Blockage - The engine showed no adverse affects from a 55 in-H 20 inlet depression other than reduced power output
- Maximum Braking - Power turbine inertia does not have any adverse affects on the gear train during vehicle braking.
- Forward-Reverse-Forward Maneuvers - This maneuver did not adversely affect engine or transmission integrity.
- Gradeability - The GT601-powered vehicle demonstrated the ability to maintain a balance speed approximating computer predictions on a 60-percent grade.
The positive experience prompted the U.S. Army to arrange for additional testing at their Yuma, Arizona proving grounds to evaluate various inlet filter systems and demonstrate the GT-601’s ability to operate in extreme sand and dust conditions.
The GT-601 was installed in additional vehicles for testing including the General Dynamics Land Systems Division Electric Vehicle Test Bed (EVTB), a “Chieftain” main battle tank from the UK’s Royal Armament Research and Development Establishment, French AMX-30 main battle tank, Israeli Russian T-55 main battle tank, M-109 self-propelled howitzer (at Yuma and Fort Sill Proving Grounds), and a Weasel air-transportable armored fighting vehicle and M-48 main battle tank from the Federal Republic of Germany.
1987 – Sixteen prototypes had been completing logging over 60,000 miles. Development costs reached US$90 million. The GT-601 gas turbine has been extensively tested by the United States, Britain, France, Israel and Germany. ITI hoped for orders to refit M-47, M-48, M-109, AMX-30, and German main battle tanks, as well as orders related to power generation, industrial and marine power.
ITI estimated the military spec GT-601 in mass production would cost US$250,000 per unit.
Reference: The XM723
From 1958, The U.S. Army was imagining an infantry fighting vehicle that, with substantial armament and greater protection than the M113 armored personnel carrier, would allow the armored infantry squad to fight from the vehicle. In 1964, the Army initiated a development effort for a mechanized infantry combat vehicles (MICV) to include an interim vehicle, the MICV-65 (XM765), and an objective vehicle, the MICV-70.
After rejecting the XM765 AIFV derived from the M113, the Army gave FMC a contract to develop a superior version. In 1972, the Army awarded FMC $29.3 million to design, develop and fabricate three prototype MICV-70 vehicles, a ballistic vehicle, 12 pilot vehicles, and associated systems engineering, product assurance, and test support.
The MICV–70 project led to a purpose-built vehicle, the XM723 MICV, armed with light cannon and a machine gun in a one-man turret, and provided with vision devices and firing ports for the mechanized infantry squad it carried.
Prototype to the Bradley Fighting Vehicle, the XM723 operated with a crew of 3 and carried 9 Infantrymen. The turret was armed with a 20mm cannon and 7.62mm coaxial machine gun. The design had a novel laminated steel / aluminium armor which was relatively light but gave improved protection against small arms fire up to 14.5mm.
The XM723 prototypes were completed in 1975 and owed some design heritage to the US Marine Corps Amtrac series of vehicles, rather than the M113. Although the Infantry (XM2) and Scout (XM3) variants of the MICV were still mechanically identical, they were envisioned as having different weapons stations. The infantry version was to continue with the one-man turret as planned. A dual turret version was planned as well.
The scout version with its reconnaissance mission placed a premium on observation for the commander. The original MICV arrangement, with the commander stationed in the hull behind the driver and beside the turret, was unacceptable. Thus the Scout version was to have a two-man turret so the commander could be stationed at the highest point in the vehicle with a 360-degree field of view. And in addition to the cannon and coaxial machine gun, the Scout version included an optically-tracked wire-guided (TOW) heavy antitank missile launcher.
In 1975, the Army rejected two prototype designs for the Scout version and began developing the prototype XM723 as a cavalry vehicle. The Army combined both cavalry and infantry fighting vehicle requirements under the Mechanized Infantry Combat Vehicle program in 1976. At the same time, an army task force new program called the Fighting Vehicle System consisting of two vehicles: the XM2 Infantry Fighting Vehicle and XM3 Cavalry Fighting Vehicle.
The XM723 was designated the XM2 for the Infantry Fighting Vehicle requirement and the XM3 for the Cavalry Fighting Vehicle requirement. FMC was awarded a contract to produce the modified vehicles. Based on recommended changes to the XM723, the M2 Bradley Fighting Vehicles was manufactured and fielded in the early 1980's.
-
NOx Emission Controls for Heavy-Duty Vehicles: Toward Meeting a 1986 Standard
Motor Vehicle Nitrogen Oxides Standard Committee
Assembly of Engineering
National Research Council
1981
Another promising alternative engine for heavy-duty applications is the GT-601 gas turbine being developed by a consortium of the Garrett Turbine Engine Company, the Mack Truck Company, and German engine manufacturer KHD (Klöckner Humboldt Deutz AG). This a very large engine rated at 550 horsepower in commercial applications.
It’s emissions of hydrocarbons, carbon monoxide and nitrogen NOx have been measured at 0.05, 1.89 and 3.13 g/bhp-h respectively, on the steady-state test cycle.
At its most efficient operating point, it has a brake-specific fuel consumption of 0.393 lb/bhp-h.
Its particulate emissions have been reported as 0.33 grams per kilogram of fuel.
Using the best fuel economy figure of 0.393 lb/bhp-h gives a minimum brake-specific particulate emission rate of 0.38 g/bhp-h. (Of course, the actual emission rate over the test cycle would be greater than this, and no direct comparison with the 1986 particulate standard of 0.25 g/bhp-h, on the transient test procedure, is possible.)
The developers of this engine are optimistic about its introduction in the latter half of the 1980s, but they recognize that this high-powered engine’s uses will be limited. Initial applications are expected to be in on-and-off-road applications such as logging and mining. The first application in trucks would be in a Class 8 trucks operating on rugged terrain.
This particular engine is cited here because it is currently undergoing on-road evaluations in a truck. Future use of this engine will obviously depend on its ability to meet NOx and particulate standards, as well as on its fuel economy as compared to that of the diesel engine it would replace.
-
Debut for Gas-Turbine Macks
Commercial Motor / May 1, 1982
Two gas-turbine powered Mack trucks made an appearance at last week's Gas Turbine Conference at Wembley
The GT 601 turbine is produced by Industrial Turbines International, a consortium comprising Garrett and Mack of the USA, and Klockner Humboldt Deutz of West Germany.
The gas turbine is particularly sensitive to ambient air temperature, hence the qualification that it develops 410 kW (550 hp) at 29°C (85° F).
At sea level, with an ambient temperature of 15° C (59° F), the GT601 is rated at 475 kW (638 hp).
The turbine-powered Macks are both 6x4 tractors, a forward-control Cruise-Liner and a bonneted Super-Liner.
They have been brought to Europe to demonstrate the potential of the turbine to military authorities as it is also produced in 520 kW (700 bhp) form for use in a light tank.
To be compatible with automotive transmissions, the output drive speed of the GT 601 is 2,600 rpm compared with its generator and power turbine speeds of 37,000 and 26,000 rpm respectively.
The highest temperature recorded in the engine is the 1,040° C (1,900° F) at the turbine inlet.
According to engine load, the temperature prior to the stainless steel heat exchanger (or "recuperator" in Garrett terminology) is 650° C (1200° F) and 315°C. (600°F) after it.
One of the advantages claimed for the gas turbine concept is that it is far lighter than equivalent high horsepower diesel engines. At the Wembley exhibition, Garrett was quoting a weight of 998 kg (2,200 lb) for the GT 601 compared with 1,360 kg (3,000 lb) for a 600-plus horsepower diesel engine.
The GT 601 has been designed specifically for heavy trucks (30 tons plus) where it is claimed to achieve 10,000 hours between major overhauls.
At a gross weight of 80,000 lb (approx 36 tons) in U.S. tests, the Super-Liner achieved 56.5 lit/100 km (5 mpg) compared to 62.7 lit/100km (4.5 mpg) at 100,000 lb (45 tons) and 70:6 lit/100 km (4 mpg) at 120,000 lb (54 tons).
The Gas Turbine Conference was organized by the American Society of Mechanical Engineers and the Institution of Mechanical Engineers.
-
2
-
-
A NEW GAS TURBINE FOR TRUCKS
Owner Operator / Sept-Oct 1978
A new gas turbine engine for trucks, the GT601, is being developed by Industrial Turbines International (ITI), a consortium of Mack Trucks, Inc. and Garrett Corp., American firms, and one German company, Klockner-Humboldt-Deutz AG. All have extensive backgrounds in worldwide truck engine manufacturing.
The GT601 is an all-metric design that ITI refers to as a recuperated cycle free power turbine engine in the 300 kW to 560 kW (402 hp to 750 hp) shaft power class.
The engine weighs 988 kg (2178 Ib) and measures 1492-mm (58 3/4-in) long, 1038-mm (41 -in) wide, and 1119-mm (44-in) high.
All engine accessories are gear driven, and include the starter, lubrication pumps, fuel pump, governor, and an air pump which is used for starting only. Likewise, all vehicle accessories (brake air compressor, air-conditioning compressor, alternator, and power steering pump) are gear driven.
Aeromechanically, the engine consists of a gas compressor section, a recuperator section, a combustor section, and a power turbine section.
An electronic computer oversees engine operation for minimum fuel consumption.
At its commercial rating of 410 kW (550 hp), the GT601 should have an overhaul life of 10,000 hr in over-the-road truck use.
The lack of belt-drive accessories and water-cooling system contribute to low maintenance, and there is easy access to engine components.
The variable stator, free power turbine design makes transmission requirements relatively simple. Though laboratory test-cell and in-vehicle evaluations of the GT601 have just begun, results to date look very good.
In combustion tests, the GT601 produced 3.7 g/bhp-hr nitrogen oxides and hydrocarbon; the carbon monoxide content of the exhaust was 0.076 g/bhp-hr.
Installed in an 80,000-lb tractor-trailer combination (Mack R-795S), the engine accelerated the loaded rig from a dead stop to road speed using only top gear of a 5-speed manual transmission. Initial fuel consumption results are in the area of 238 g/kW-hr (0.39 Ib/hp-hr), which is within the diesel engine range.
If all goes well, production of the GT601 could begin as early as 1981.
-
1
-
-
Mack Turbine Truck
Commercial Motor / June 27, 1969
Another American vehicle manufacturer has entered the gas-turbine league. Mack Trucks unveiled a prototype turbine-powered truck to its executive earlier this month. The truck uses an industrial gas turbine engine made by The Garrett Corporation, a Mack associate; both Garrett and Mack are part of The Signal Companies Inc.
In announcing the development, Mack states that the prototype is intended to provide the firm's engineers with data needed before the introduction of pre-production test models. Data to be obtained includes acceleration rate, intake and exhaust silencing requirements and general performance information. No information is given on the turbine, such as output and type, but the unit is coupled to a modified Allison semi-automatic transmission in a standard Mack forward control chassis (F-model).
There is added interest in the Mack development given the agreement signed at the end of last year by Garrett and Cummins. This covers a joint program between these two companies to explore the feasibility of gas turbines for trucks and construction equipment. It was stated at the time that Cummins would handle marketing of such units.
-
1
-
-
The GT-601
Developing a gas turbine for vehicular use posed unique challenges, as vehicular operation encompasses a wider operating envelope than aircraft or stationary gas turbine operation over a limited altitude range.
The GT-601 vehicular gas turbine incorporates variable turbine nozzles for engine braking and gear shifting, as well as its conventional use as a temperature trim device.
The GT-601 was designed to work with a manual clutch and transmission, or with automatic transmissions (with torque converters omitted).
To meet the challenges of vehicular operation, the GT-601 incorporates features not found in previously designed gas turbine engines.
- 2-Stage Compressor - To meet the high specific power requirement not obtainable with a single stage compressor.
- Radial Inflow Gas-Generator Turbine – Minimum cost solution for equivalent performance/life trade-off. Cooled radial stators considerably cheaper to fabricate offered possibility of later transition to ceramic stators
- Two-Stage Power Turbine with Two Stages of Variable Stators – Higher Efficiency – Reduced diffuser loss-turbine /recuperator. Requirement to match with manual transmission dictated need to decelerate turbine during gear shifts in 2 seconds. Only two stages of variable stators will suffice.
- Multi-Module Recuperator – High specific power dictated the pressure ratio. Pressure ratio mitigated against rotary regenerator – leakage incompatible.
-
1
-
- Popular Post
The Mack gas turbine was the most powerful and promising of them all. And Mack chose two superb partners to work with.
The GT-601 gas turbine tested by Mack Trucks was designed and produced by Industrial Turbines International (ITI), a partnership between Garrett AiResearch, Mack Trucks and KHD (Klöckner Humboldt Deutz AG).
The joint venture began a program in 1972 to develop a 450-638 horsepower (335-476 kW) power range of gas turbine engines specifically designed for heavy trucks. This effort resulted in the GT-601, a free-turbine all-metal engine with a fixed boundary recuperator.
The GT-601 gas turbine eliminates winterizing requirements, operates without vibration, with less noise and favorable torque characteristics, and is air cooled. For density, weight and reliability, the GT-601 was far ahead of the diesel engine. However in typical on-road applications, U.S. truck weight (80,000lb/36.3 metric tons) and size regulations don’t allow the efficient use of the 550 horsepower GT-601. Only the use of larger trucks (97,000 pounds/44 metric tons) will allow the GT-601 to yield economic savings.
Several engines were built during the program and tested extensively.
More than 7,000 hours of operation were accumulated, including more than 2,000 hours in highway trucks.
These engines demonstrated the feasibility of fixed boundary recuperators along with superior torque compared to diesels of similar rated power, easy cold starting, and the ability to survive limited foreign object ingestion.'"
In 1979, a GT601 was experimentally fitted in a Mack R-795S tractor, and tested thru 1980.
In 1980, GT-601s were installed in a 1979 Hayward-production Cruise-Liner (WS-760LST) and Super-Liner (RWS-760LST).
Mack installed the engines in Allentown, and in Phoenix, Arizona on the property of the local Mack distributor where the IMI joint venture rented a building. Phoenix was the home of Garrett AiResearch.
The two trucks made an appearance at the 1982 Gas Turbine Conference in Wembley, UK and operated thru 1986.
I don’t know how many Mack gas turbine test beds were built. I heard there was an F-model, but I never saw it. And while I’ve never heard people speak of a RL/RS Value-Liner testbed, I did witness one being retrofitted with a GT-601 gas turbine.
I regret more photographs of this exciting chapter of Mack history are not available.
-
7
-
I was able to get a print of the front shock used on my MH. The print listed the Monroe part number so I ordered it from a parts warehouse at a lower price than Mack wanted for the same part.
Your front shock is a 14QK373, right? Typically, in return for the Mack contract, the vendors aren't allowed to sell the "Mack spec" shock themselves. But these are older parts so the vendor might not still be obligated. And I don't know how the Swedes handle it now.
How's your shift tower shock absorber?
-
Fleet Owner / July 19, 2013
Bosch has released a new line of starters it said are designed to outperform and outlast OE counterparts on most heavy duty commercial vehicles. The Long Haul 12-volt series includes all the features necessary for the widest range of large displacement commercial diesel engine applications.
“High compression diesel engines require greater amounts of torque and power to turn over in all temperature ranges,” said Fred Padgett, group product manager, rotating electrical. “Bosch Long Haul starters use a shock absorbing planetary gear system originally designed by Bosch. Mounted on rubber shock absorbers and located in a steel drive-end housing, the planetary gear carrier resists ‘kick back’ and eliminates drive-end breakage common in many competitive designs.”
Features of the line include:
- Easy-to-use universal mounting flange reduces SKU count which, in turn, simplifies inventory
- Over crank protection prevents damage and ensures a longer life
- Internal magnetic switch (IMS) ensures optimal voltage for starting in all weather conditions
- Fixed over running clutch with 50% less moving mass protects internal components in case of ‘blind start’ or ‘click no crank’
- Meshing spring for positive gear engagement during cranking. This eliminates ‘click no crank’ and prevents costly damage to the engine ring gear.
- Isolated external ground circuit promotes optimal grounding and maximum starting power
- Open nose design resists moisture, dust and dirt, preventing damage to internal electrical and mechanical components
- Dual composite long life brushes create better surface contact, less heat and lower current draw resulting in longer life and quicker starts
- Double chamfered pinion gear increases first time engagement and positive starts
- Protective cover shields the solenoid and critical electrical connections, ensuring positive connections and maximum starting power.
“The innovative technical features of Bosch Long Haul Starters contribute to their long-lasting service life, outstanding performance, and comprehensive SKU coverage,” said Padgett. “Our starters are designed to keep trucks operating worry-free for miles and miles and ensure continued profitability for heavy duty business owners and operators.”
-
Information about revisions and such very much appreciated. Yet, you mention the "P1" part. The build sheet calls for "no P" (see original post).
Sorry for not being more clear. The base part number without the P variation shown (14QK2100) is the same as the P1 variation (14QK2100P1). When Mack people saw 14QK2100 on a line sheet, we instinctively knew that's a 14QK2100P1.
-
Wonder if the P1 or P3 is a revision, or an actual different part. They don't necessarily cross over exactly the same, depending on whose chart you use.
A letter suffix after the base part number, typically A, B or C, denotes an engineering improvement, but the parts are interchangeable.
For example, 14QK2100P1, 14QK2100AP1, 14QK2100BP1. These would all be interchangeable.
However, "P" variations are distinctly different parts. You can not interchange a 14QK2100P1 with a 14QK2100P3.
Why not contact a Volvo-Mack dealer and buy the correct part? The will-fit shock absorbers will NOT give you the same fit and performance as the "made for Mack" version.
The reason multiple Mack P variations sometimes all cross to one "will-fit" part number is because the will-fit parts are often a compromise solution. Do you want to install a compromise part on your truck?
You've got an older R-model with multi-leaf front springs, right? So you need a pair of 14QK2100P1 front shocks. Why don't you give Barry and the good folks at Watts Mack a call?
-
Bloomberg / July 19, 2013
Scania, the Swedish truckmaker controlled by Volkswagen, plans to increase production rates to ensure short delivery times after second-quarter orders rose 15 percent.
Sales contracts increased to 22,564 trucks and buses from 19,586 vehicles a year earlier, while deliveries jumped 33 percent, Soedertaelje, Sweden-based Scania said today in a statement. Net income fell 6 percent to 1.37 billion kronor ($210 million) as a strengthening Swedish currency and truck-price pressure weighed on earnings. Revenue gained 19 percent to 22.8 billion kronor.
“The economic climate remains uncertain, but there is a replacement need,” Chief Executive Officer Martin Lundstedt said in the statement. “Scania is continuing its efforts to expand annual technical production capacity toward 120,000 vehicles.”
The manufacturer is rolling out new vehicles that meet tighter emissions standards to drive sales in a bid to counter recessions across Europe. New registrations of heavy commercial vehicles weighing more than 16 metric tons in the region, excluding buses and coaches, fell 13 percent in the first five months of 2013, with double-digit declines in all major markets, industry association ACEA said on June 28.
Scania fell as much as 5.1 percent to 140.3 kronor, the steepest intraday drop since April 2012, and was trading down 2.7 percent at 10:30 a.m. in Stockholm, valuing the manufacturer at 113.8 billion kronor.
Margin Declines
Operating profit in the quarter rose 5 percent to 2.04 billion kronor. The operating margin narrowed to 8.9 percent of sales from 10.1 percent a year earlier.
JPMorgan Chase & Co. reduced its recommendation on Scania stock to neutral from overweight earlier this month, with a share-price estimate of 140 kronor, saying risks to growth in the European truck industry next year are increasing.
“We continue to view Scania as the best executor amongst our truck coverage but, with no upside to our price target, we prefer a neutral positioning until the risks in Europe and Brazil are understood or reflected in the stock,” Alexander Whight, a London-based analyst at JPMorgan, said in a note to clients on July 9.
Volkswagen, Europe’s biggest automaker, is forging a truck alliance between Scania and its Munich-based MAN SE truck division to reap cost savings and take on global market leader Daimler AG.
A domination and profit and loss agreement giving VW full control of MAN is now in effect after being entered in the corporate register, the truckmaker said on July 17. VW promoted former Scania CEO Leif Oestling to run its group trucks operation last year to lead cooperation efforts.
-
1
-
-
Caterpillar tested a few gas turbine powered on-highway trucks.
My understanding is the CAT gas turbines were for off-highway dump trucks and construction machinery.
Noel Penny Turbines (NPT) of Coventry, UK designed, developed and built 350 horsepower gas turbine engines for Caterpillar, for off-highway applications.
CAT built an experimental model 621 turbine scraper in 1968, a model 992 turbine rubber tired loader in 1973, and I heard they also built a gas turbine grader.
Penny had been managing director of Leyland Gas Turbines, which had developed two-shaft gas turbine engines with regenerative heat exchangers from 1968 to 1974 for experimental Leyland gas turbine trucks.
Leyland Gas Turbines was the successor to Rover Gas Turbines, a small UK company that had worked with Sir Frank Whittle during World War II on England’s first jet engines. Rover was the earliest company to consider gas turbines for vehicles and built the world’s first gas turbine car in 1950.
-
1
-
-
-
- Popular Post
- Popular Post
Freightliner completed the first “Turboliner” (serial 18-727) in September, 1965. The tractor was powered by a Boeing 553 aviation gas turbine. Boeing was a major gas turbine manufacturer during the 1950s and 1960s for applications such as minesweepers, power generation and propulsion, aircraft compressed-air starters, tanks and other armored fighting vehicles, and anti-submarine drone helicopters. The 553 gas turbine was paired to a modified Allison automatic transmission. The Turboliner was run for four years before being disposed of after the engine finally failed.
(In January 1966, Boeing decided in phase out gas turbine production and focus those resources on the 747 jumbo jet program, completing its last turbine orders in 1968)
In 1968, Pacific Intermountain Express joined Consolidated Freightways in operating a first generation Turboliner in regular service.
In May of 1971, Freightliner began building several White/Freightliner cabover tractors with gas turbine engines purpose-designed for heavy trucks. These trucks, with their distinctive 10-inch diameter exhaust stacks, were given the name “Turboliner II”.
The first tractor was powered by a Detroit Diesel Allison GT-404.
The second unit was powered by a Ford gas turbine, for Ford to test at their Arizona proving grounds.
A third yellow and black tractor, powered by a Detroit Diesel Allison GT-404, was assigned to Freightliner's own test fleet and used to transport parts between Portland and Pomona.
These trucks were followed by six more GT-404 units in November 1973, five for Consolidated Freightways and one for Goldston Transfer.Roger Sackett, who headed the development team on the first Turboliner and was chief engineer for the last six Turboliner IIs, said the 2,400 pound weight savings (refers to the first generation Turboliner) provided by the gas turbine was not enough to offset fuel consumption of 2 miles per gallon.
From 1974 to late 1977, Detroit Diesel Allison conducted a field evaluation of the 300/310/325hp GT-404 and 390/400hp GT-505, placing trucks in the fleets of Consolidated Freightways, Greyhound, Ruan Transportation, Terminal Transport, GM Truck and Coach and Freightliner.
-
4
-
-
- Popular Post
- Popular Post
Bridgewater - Though now but a memory, the mere utterance of the word still causes Mack parts veterans to skip a heartbeat.
How many Mack parts people are left that remember the white “punched” pull tags?
The massive 422,000 sq.ft. Bridgewater parts distribution center (PDC) was constructed in Bridgewater, New Jersey in 1951.
As America entered more deeply into the cold war, the PDC’s chosen location had much to do with our country’s civil defense strategies. To minimize the vulnerability of critical industries in the event of an enemy air attack, Washington was encouraging American companies to locate new facilities away from established industrial centers. Mack Trucks followed the policy and was subsequently praised by the U.S. government’s Industrial Dispersion Task Force for choosing the Bridgewater location, as well as for its convenient proximity to major highways and not being dependent on rail transportation.
While Bridgewater was revolutionary for the Mack organization in 1951, its shear size and unyielding union atmosphere made it an ungainly juggernaut by 1980. Having solidly established itself in the western United States and Canada, Mack shifted into high gear to establish strategically located distribution centers across North America.
- Baltimore (Severn)
- Atlanta
- Chicago (Bridgeview)
- Dallas
- Hayward (adjacent to Oakland, California)
- Toronto
Joining the Hayward and Toronto PDCs that went online in 1966, the Atlanta, Chicago and Dallas PDCs opened in 1973.
The massive and superb Baltimore (Severn) PDC came online in 1980, taking over the regular duties of the Bridgewater PDC. Bridgewater for the next four years became the home for slow moving inventory while remaining the headquarters for Mack Parts Operations.
Bridgewater closed at the end of 1984, transferring its parts responsibilities to the vast Baltimore PDC. Mack Parts Operations relocated to nearby Somerset, New Jersey, and finally to Mack Trucks’ Allentown world headquarters in 1991.
Responsible for Europe, the Middle East and Western Asia where Jack Curcio as executive vice president of international operations had supercharged Mack Truck’s international sales, the company’s massive PDC in Antwerp, Belgium processed 22 percent of Mack Trucks’ global parts sales.
The Antwerp PDC was supplied first via Mack Trucks’ Bridgewater PDC, later the Odenton, Maryland export PDC and finally from 1986 the Baltimore (Severn) PDC.
Staffing the eight Mack PDCs were the highest caliber people in America’s truck industry. No other truckmaker in our country’s history had a finer group of dedicated men and women. They were a key pillar in making Mack Trucks’ parts operations the benchmark for the entire truck industry.
.
-
3
-
-
While the Brits called them a Chinese Six because there was a time in the UK when anything the opposite of normal was termed Chinese, I call them a Chinese six because China is the most popular market for them today (tractors and straight trucks). Pulling a clutch is no issue today, with tilt cabs and typically twin-steer axle spacing of 1900mm to 2100mm (6.23 to 6.89 feet).
In on-road operation, a 6x2 twin-steer tractor provides you with 90 percent of the abiity of a 6x4, with lower purchase and operating costs, and reduced curb weight for greater payloads.
True, you can't lift that second steer (auxiliary) axle, but most people run loaded all the time anyway (the exception being the petroleum haulers who might lift a conventional 6x2 tractor's tag axle when running empty back to the oil terminal, but the 6x2 twin-steer would still save them money).
-
2
-
Ford’s Futuristic Gas-Turbine - “Big Red”
in Other Truck Makes
Posted · Edited by kscarbel
Designed for the super highways of tomorrow, Ford's advanced experimental “Big Red” gas turbine truck represented a massive and deeply invested R&D effort by Ford Motor Company. And unknown to Americans, a major catalyst for the project was the potential for lucrative military gas turbine engine contracts unrelated to heavy trucks.
“Big Red” made its public debut at the 1964-65 New York World’s Fair powered by Ford’s 600 horsepower model 705 gas turbine engine.
After the fair, “Big Red” toured the United States and Canada with stops in Boston, Buffalo, Chicago, Denver, Dallas, Los Angeles, Newark, Philadelphia, Oklahoma City, Toronto and Washington DC.
Later, the truck made several cross-country test runs at costs comparable to diesel operation.
Specifications: Ford “Big Red” Gas-Turbine Tractor
Wheelbase: 119”
Length: 237”
Height: 156”
Width: 96”
Axle Track (Front): 82”
(Rear): 78”
Turning Radius: 21’
Ground Clearance: 7.75”
Top Speed (at full load) 70 mph
(at reduced load) 78 mph
Fuel Capacity: 280 gallons
Operating Range: 600 miles
GCW rating: 170,000 pounds (double-trailer combination)