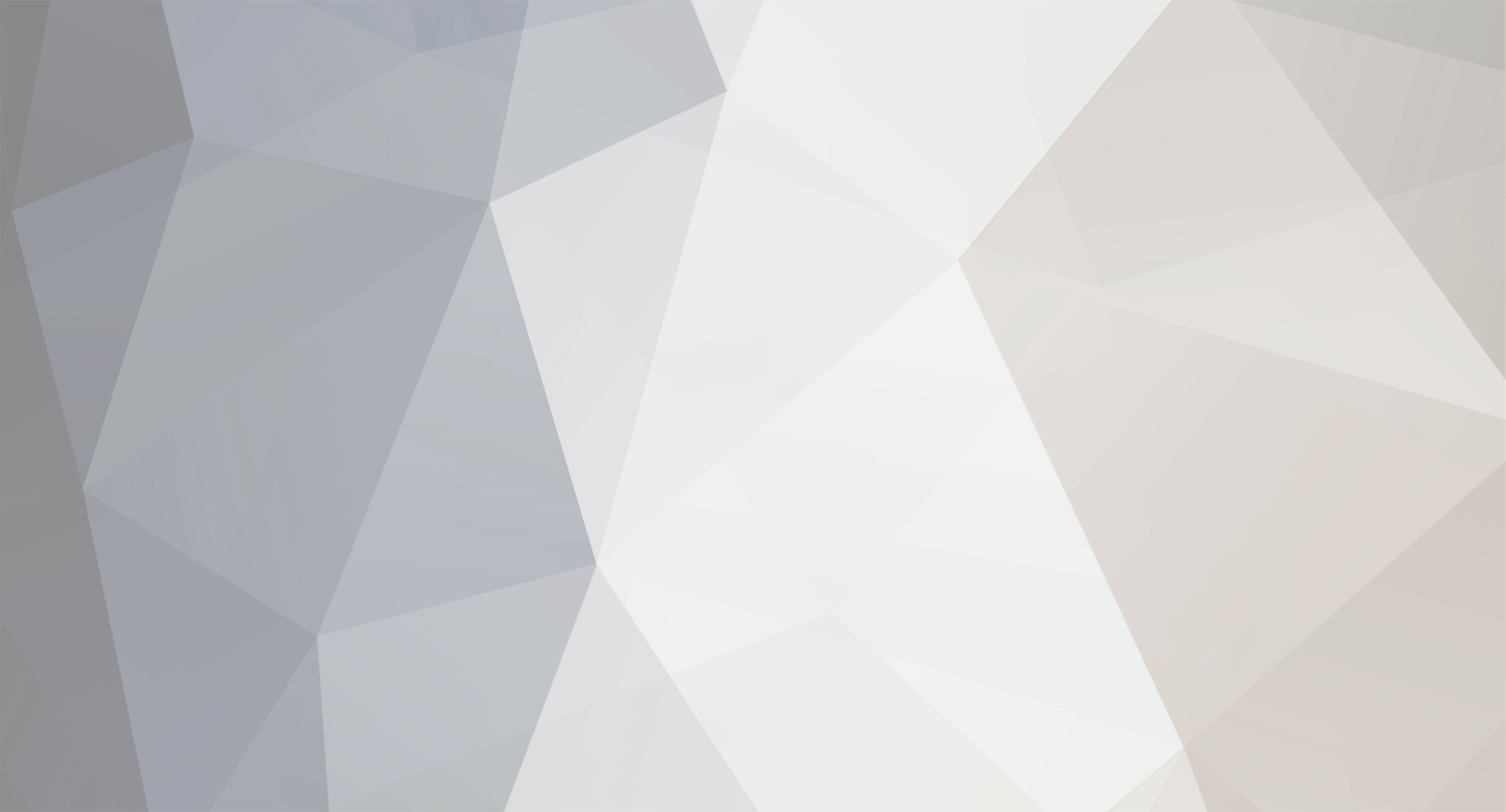
Mandrewoid
-
Posts
43 -
Joined
-
Last visited
-
Days Won
1
Content Type
Profiles
Forums
Gallery
Events
Blogs
BMT Wiki
Collections
Store
Posts posted by Mandrewoid
-
-
4 minutes ago, JoeH said:
We have a pump like that on one of our trucks, it's a piece of sh*t in our application, but the swash plate adjusts very fast on ours.
Our system requires multiple hydraulic valves to need to be synchronized, and the type of control valves don't allow for it well.
What kind of application is that? Mine has a second pump on the front for running aux functions but I have it just pumping oil through the filter and back to tank.
-
The pump is an Eaton hydrostatic pump. 5.4 cubic inches. 40gpm@1800. But it's a variable displacement pump. The response time would be because the pump has to swing the s wash plate before it starts pumping. Although maybe if I put an air cylinder on it it would move faster than the current 1/8" hydraulic cylinder that activates the control lever.
I could put a button on the shifter that would be kinda cool.
-
Another fun experiment that I'm not sure anyone has ever tried before. You could link up your throttle pedal and a boost sensor to a 1-in airline going to your exhaust manifold on the pre-turbo side. Then when you stomp on the throttle at 900 RPM and have no boost yet. Dump compressed air from your air tanks into the exhaust manifold to light up the turbo faster. If you want to get real fancy you can also stick a fuel injector in the exhaust manifold so when you dump this cold air in then you light it on fire. And you have a jet powered turbocharger for a quarter of a second every time you step on the throttle until boost builds.
-
I have also toyed with the idea of using my massive live PTO as a hydraulic retarder. All I have to do for that is install a check valve and a 4000 PSI relief valve. It would dump a lot of heat into the oil but at maximum rpm it would give me 150 horsepower of braking force. I never thought of using it as a shift assist though because the delay from hydraulic valve activation to pressure actually building is probably about half of the amount that you'd need to make a good shift anyway. Unless I had the oil always pumping and just threw a directional valve in order to activate the breaking then it would be immediate but if I screw it up I'd end up with 300 gallons of manure on the road.
My tanker unloads 6,000 US gallons in one minute and 30 seconds
-
A guy might be able to get away with 30 PSI of exhaust back pressure. Because that's about the same pressure as your turbine drive pressure under hard loading conditions would be. I have looked for these butterflies before and I've seen them for RV purposes but I've never really seen one that I thought was big enough to use on an e6 Mack?
-
1 minute ago, JoeH said:
One more spitball idea, throw a butterfly engine brake in the exhaust pipe for upshifting. It'll make the truck a whole different animal. It'll cut your engine speed down much faster so you'll be getting into gear closer to 1100 or 1200 rpms. We had a jake brake on one of our Maxidynes for decades, and it made the truck faaast.
I like this idea. But I'm also afraid of valve float from exhaust back pressure. I never really thought of it before, but two valves have much more surface areas and fewer valve springs to hold them shut. I'm pretty sure my engine is a 2 valve, I have had the covers off in the past.
-
It is an EM6-275L for sure. I believe the other one is an EM6-350 but I will definitely check. It only has a 9 speed so my assumption is that it has the same large power band. Especially when I talk to the old owner of that truck and he describes driving it.
The 350 had a massive air to air in front of the radiator, and my 275 is a tip-turbine with water to air.
I saw on here somewhere that they did make a tip-turbine 350 with water to air. Would that be the same motor internally as mine, or did Mack do crazy things like put different valve springs and pistons in depending on the horsepower designation of the engine?
It would make sense to me to keep all that stuff common for ease of manufacture and parts supply... But I know other engine manufacturers did not do that.
-
I realize this is several years ago, but this is exactly the issue I have with our EM6-275L. The puff limiter is disabled and the fuel plate is adjusted and ground down a little, but still when you hit 1700Rpm, those governor weights pull your fuel rack back because the springs cannot hold it in anymore. In my case I do have an "L" rated engine, which I know was designed for fuel economy, but now in the second life performance matters a lot more. I can't shift gears going uphill because you lose so much speed, by the time you get into gear it's dropped to 900rpm,and the sky turns black.
-
52 minutes ago, JoeH said:
So all Mandrewoid needs to do is turn that screw a turn or two one way or the other to get to 2100 rpm I figure.
No this is incorrect. You can set the high idle screw to 2300 rpm all you want, but if you have 1800rpm governor springs, you will only make idle power at 2300rpm.
What you can do is put 3000rpm governor springs in and then turn the high idle screw down so you don't exceed 2200 rpm. At that point it will likely behave a little bit like a farm tractor. As soon as the engine rpm drops to 2100, all the horsepower will be available. You won't have to wait to drop down to 1700rpm.
-
1
-
-
4 hours ago, mechohaulic said:
my thoughts exactly. slight adjustment to max RPM screw can be done. with fuel peddle check max RPM. remove pin from fuel pump disconnecting linkage manually run up RPMs . check any difference. cab mount set up while driving may be cutting full fuel . I wouldn't be changing internal springs. check all fuel linkage pins . have seen a Mack engine run away (title usually held buy DD). scared the heck out me. fuel shut off cable has been know to keep an engine from full fuel as stated.
In neutral I've got 1990RPM. Under significant load I've got 1800. My understanding is that the e6-285 has different governor springs than the e6-275L but otherwise should contain identical internals. The low rpm version was designed for fuel savings, which is no longer an important issue for this vehicle. Time savings and performance is worth it for us.
The people that do extreme truck pulls with these, are there any of those guys here?
On 12/11/2023 at 2:10 PM, JoeH said: -
2 hours ago, MACKS said:
What transmission do u have,sounds like u have the wrong gearing for that engine?
Maxitorque 8 speed. Everything on the truck is factory. It used to be a cement mixer. Just made for local city driving. Now I'm taking it all sorts of off-road up very steep slopes trying to keep my speed and engine rpm up in order to unload my load.
Overall GVW is pretty similar to the mixer configuration, because the tank has a very heavy subframe and I've got 5990 USG of manure
-
1
-
-
You can still adjust the high idle stop. I don't want my engine to actually turn 2800, I just want full fuel all the way to 2200. The notice on the sun visor says it's good for 2300rpm. I'm sure people have pushed that a bit and gotten away with it too.
I have found that on an incline of any sort, I can't get above 1700rpm, then when I try to shift I'm down to 900 by the time it gets in gear. Then I'm turning the sky black for 3 minutes before we get some boost and some RPM going.
If I could shift at 2000 or 2100 it would be much better for everyone especially the guys behind me. And if I can maintain 2000rpm in field in second gear that would be nice too. The governor springs from my spare motor would be guaranteed not to hurt it, but not sure how much of an improvement it would actually be.
-
Following on a thought I had in a previous thread. I know a few people with Cummins pickups( same fuel pump as my E6-275L. ) Who have replaced their governor springs with higher RPM springs, and they say it really awakened the truck quite a bit. I know these trucks were made with the L destination for low rpm in order to be more fuel efficient. Fortunately for me in my off-road application the fuel economy is pretty much irrelevant, what matters to me is having the widest possible power band.
There are times where I can definitely tell that the pump is de-fueling due to high RPM, but I'm not talking 2000rpm, I'm talking about anything above 1550rpm the engine starts to work less hard. It is my understanding that higher RPM governor springs will help to solve this problem. Obviously I'm not going to go 4000rpm like the truck guys do. But I am thinking perhaps a stock spring from a Cummins would work in the Mack application. Or possibly the spring out of an E6-350, or maybe even just a 285 non-L
Does anyone have experience with this? In the Cummins, the fuel pump is mounted with the governor springs on the outside so it is a 10 minute job. On the Mack, it seems to be on the inside, so the fuel pump may have to come off...
Looks like the stock Cummins is set to 2800rpm. That should do nicely, as long as I don't actually allow the engine to over-rev
-
4 hours ago, JoeH said:
Obviously you'll have to have a new driveshaft made up as the trans will likely be a different length than your current one.
Do you think the mounts will be in different spots too? Drilling new holes in the frame normally wouldn't be a big deal, but my fenders etc are in the way. Perhaps this is why people don't do it.
I already have an E6-350 spare engine for parts from a truck I dismantled 😅 but it has a 9 speed unfortunately.
I have wondered about stealing the injectors and fuel pump to give me more power. I have already ground my fuel plate in the e6-275 that this truck has. The problem is that it's a 275L so with the low speed governor springs I'm still losing all my power about 1600 rpm on the top side. I'm sure if I had full fuel all the way up to 2100rpm it would be a different beast.
-
Thanks for the comments everyone.
I do not require overdrive, technically I'm not supposed to exceed about 30Mph since this is technically a farm tractor. My farthest haul is 14 miles, but up and down several steep hills on the way there. Still beats hauling a tanker behind an AG tractor. Much more efficient hauling. Probably for most of the close hauls and especially on the steep hill, I could put the Tcase in low, which is about a 2:1 reduction. That would let the auto get out of low gear and do some real work. Or that's my thinking at least.
To those who wondered, yes the transfer case is divorced. It sits about 2 feet behind the cab. I could slide the tanker off the back to do a big job like this, it's only held on by 8 big bolts. But what I'd never want to do is put a cab back on after taking it off 😂.
Also, the retarder that autos often have would be really nice. This engine unfortunately is not equipped with Jakes.
Or should I just get the engine+transmission combo out of a fire truck and swap them both in?
-
1
-
-
Hi everyone, I have a DMM690EX with a em6275L and a maxitorque 8 speed. It's a 6 wheel drive and the transfer case has a 2 speed air shift. I have another thread on here about the building of it. She's quite a beast and hauls 6000 USG of liquid dairy manure, on top of the weight of the truck of course.
Unfortunately, as time goes on it is nearly impossible to find people who can drive. And even I am getting annoyed by the shifting at times. On some routes to the field we have a stop sign, 30 feet of level road and then Half a mile of 12% grade. It's impossible to get into 3rd gear before you start climbing the hill, so you gotta roar up the whole thing in 2nd. Annoying all the neighbors as you go. ( Rusted out exhaust system)
I am wondering if people on here have any prior experience with these engines coupled to an auto transmission? I was thinking an automatic mack garbage truck likely would be a similar mechanical configuration.
How much work would it take to switch? Do you put the transmission on underneath or do you have to pull the cab off?
-
Here are some progress photos. Centering and squaring the plate for welding was easier than I thought, and no additional wobble was incurred. I am cutting some additional pieces for reinforcing the inside, as I agree it will put excessive stress on the edge of the center rim if too much weight is borne by the outside wheel.
I also have to make a few small blocks on the surface of the flat adapter to "hub pilot" the outside wheel, as I don't think that I want to get into the complications of special lug nuts. In this photo, the third wheel is secured by 1" bolts. I am considering the possibility of purchasing knurled studs, does anyone know where I could get 40 26mm knurled studs?
-
1
-
-
On 5/8/2022 at 4:39 AM, Vladislav said:
Ughh... I can't imagine a few things. First, how are you going to acces the middle (2nd) wheel nuts to remove it when needed?
Second, you definitely should weld reinforcing ribs to the inside of that new plate to increase its bending stiffness. I'd put them off the center hole to the rim circle. The way the sun rays used to be painted by a kid. Six ribs at least, and with their outer ends welded to the wheel rim. And you definitely need to do that BEFORE you apply any welds attaching the adapter plate to the wheel.
Ok, my second thought - if I was going to make such the design my way would (probably) be cutting a center off another Budd wheel and weld IT into the 2nd wheel instead of your custom adapter plate. Actually making a wheel with two centers. It definitely would be much tougher than flat adapter you're going to use. But any way the original center of the 2nd wheel gets much higher stress with the 3rd wheel added in relation to its normal operation carrying load applied to the 2nd wheel only.
Your actual idea gives me a guess you are a "practice man" and prefere checking things made of metal. Would be interesting to learn how your custom setup work on a real truck. Anyway good luck on the project!
As always thank you for replying. The matieral the adapter plate is made of, is 1/2" (12.7mm) I think you are forgetting my original wheels do not have any centers at all("Dayton style"), so there is no risk of tearing the center out of the second wheel. the six cutouts around the outside are how I will access the nuts and wedges to remove the other two wheels. I may have enough space to weld reinforcement to the inside of the center adapter, but according to my figuring it should be fine. Biggest concern is being able to fixate and weld it accurately in the center. Also the third wheel will be running at half pressure, so the tire will deform if I drive over an obstacle.
-
We're getting there. Here's the fabricated adapter plate, cold off the waterjet table. I have not yet welded it onto the hub but you can clearly see what the plan is now. I also have spacer discs, 1/2" plate with the 10 bolt holes in them. I will machine one of the spacer plates to provide the hub piloting required, and then weld them all together. It will be quite a challenging weldment to get everything lined up right.
-
2
-
-
4 hours ago, Vladislav said:
I don't like your idea of using those flat rings to fit Budd wheels onto Dayton hubs. My guess is they will crack really soon. You may use something like that when the distance between two points of the force applied (in your case between the spoke stud and Budd mounting stud) is short. Otherwise you've got really large banding torque in the part. I would go another way and find hubs to fit Budd wheels. Mack axles made a way they used both Dayton and Budd hub on a similar spindle so doesn't seem difficult to convert (from where I'm sitting). My DMM had stud piloted Budd hubs from the factory and I located 4 13.50 (or so) steel wheels to mount 445/65R22.5 super singles on and fit to the rears.
Speaking the differentials the cam type in the axles was an option and by my observations a seldom used one in that era. Usually interwheel diffs are of a common gear style. The interaxle unit is always (if Mack axles) of a cam style and distributes torque. It may be equipped with air operated complete lock down and wouldn't distribute anything when locked just forcing both axles spinning together. It was an option for the most of models but I doubt many DMM's left the factory without it.
Thanks for the info Vladislav. But have you ever seen Budd style wheels with triples on the rear? What I'm looking for isn't a way to add a bolted wheel to a spoke hub, but actually a way to add a 3rd wheel on my rear axles. 445/65r22.5 singles on the back is not sufficient, I need more like 810/30r22.5 to have enough traction and flotation. I don't see how a mounting plate inside a open center rim would be any different than the mounting face inside the budd rim itself, but it definitely would have to be at least the same thickness. I'll try and build a CAD model so you can see what I mean.
-
-
3 hours ago, Bullheaded said:
I've often wondered why they never caught on as self loader logging trucks.
I wonder if it is turning radius related? Or payload related. My DMM is incredibly heavy. 10" inner frame & 13" outer frame. With a mixer you'd want a stout truck because even when empty, you're carrying quite a load.
Also I'm not a concrete guy but I have my suspicion that they may sometimes be a little over legal gross, but.... There ain't many scales in town if you know what I'm saying.
Log truck is pretty light when empty and at least where I'm from, you may have quite a drive to the mill.
-
New rubber is on. 650$ per tire 😬
I have gotten stuck once with the new tires but it was my fault not theirs. I got too close to a wet spot and couldn't turn sharp enough to avoid it.
Question about the Mack rear ends. Do they all have the "cam type" differential that is supposed to automagically torque bias? I think mine may be worn, because with my lockers engaged I can have only one wheel on each axle spinning if the traction is bad enough.
-
On 11/19/2021 at 6:47 PM, BGarofalo said:On 11/20/2021 at 3:49 AM, Swishy said:
I need all these rear ends in my life. Especially the 9 foot wide one. What's the axle ratio? Is it a Mack double reduction?
High RPM governor springs.
in Engine and Transmission
Posted
Ohhh yes I know that equipment. Live less than a mile from Quinte Mobile concrete. They've got tons of volumetric mixers. The older ones run a big crank mounted gear pump like a garbage truck, and then use pressure/flow compensating valves, and the newer ones are Allison autos with REPTO.
.... Kinda jealous of those new trucks 😂. They have a few international and a few Mack.